The use of collaborative robots in automotive assembly operations is gaining pace. AMS reports on the applications, technology and why this is a growing trend
A new robot went into operation just a year ago at the BMW plant in Dingolfing, Germany. But this machine is not a massive, powerful piece of equipment for an application such as vehicle painting or welding. Instead it represents the very first example at the plant of a trend that is steadily gathering pace in the automotive industry, that of human robot collaboration (HRC) also known as collaborative robotics.
The machine in this instance is an LBR iiwa lightweight robot from Kuka, which has been slotted into place in an area previously occupied by a human operator alone to support them in the same arduous, repetitive task of first lifting and then installing differential cases for front axle transmissions. The cases involved can weigh as much as 5.5kg and quite apart from the strain of lifting them their installation is by necessity a task that requires both precision to ensure accurate fitting and delicacy to avoid damage to any of the system elements involved.
Getting the innovative robotic application at the plant up and running was the result of a joint effort by both car maker and robot supplier, which involved development work at the BMW plant in Augsburg before the concept was finalised and implemented at Dingolfing. An interesting aspect of the set-up in this instance is that the robot is mounted in an inverted position above the work area from a slim steel framework – an approach facilitated by the robot’s own lightweight construction. It weighs just 30kg.
Henning Borkeloh, vice president for advanced technology solutions for Kuka, confirms those core details. Not the least of them are the restricted confines of the total space occupied by the robot and its support structure. The footprint of the supporting structure, he reports, is 200x200mm and its height 1,400mm.
Heavy parts, light touchBut, as Borkeloh further explains, the project required some clever thinking to cope with the challenges involved. “Fitting the heavy differential case in place is an incredibly delicate task,” he notes. “The sensitive tooth flanks must not be damaged by impacts when meshing the gears. One of the challenges was the variation of the weight of the different parts that had to be assembled. Basically, we had to find the right parameters to adjust the torque sensitivity of the robot to the various requirements.”
Nevertheless Borkeloh makes the point that the most visually striking aspect of the application – the inversion of the robot – is actually quite unexceptional from Kuka’s point of view. “It’s not unusual for us,” he states. “We’ve implemented ceiling mounted solutions for several clients already.” The construction of the robot itself is also an enabling factor. “The LBR iiwa has joint torque sensors in each of its seven axes, meaning it does not require external sensors,” he explains. “Combined with the robot’s lightweight construction this enables it to work from any position.”
A third handIn fact, Borkeloh continues, the sensor system incorporated into the robot is absolutely crucial to its suitability for this particular application. “Assembling a differential gear is a highly sensitive application because the cogwheels have to be carefully meshed with another tooth part,” he notes. As such the fact that the machine has integrated joint torque sensors in all of its axes ensures that it has the necessary contact detection capabilities and programmable compliance. “This means that accompanying humans can control the sequence of a robot application without control equipment simply through gestures – for example by touching the robot,” he adds. “The sensors also enable the robot to master force-controlled joining operations, process monitoring and continuous-path processes for which the position of the objects must be sensed.”
In a sense it becomes, he observes, “the third hand of the human operator”. In operation the components are fed to the system automatically along a conveyor and prepared by the operator, who places all of the small and lightweight parts, such as spacers and ball bearings, into the cast aluminium transmission case and the cover. The operator then presses a button to activate the robot, which comes into operation to fit the differential case carefully in place.
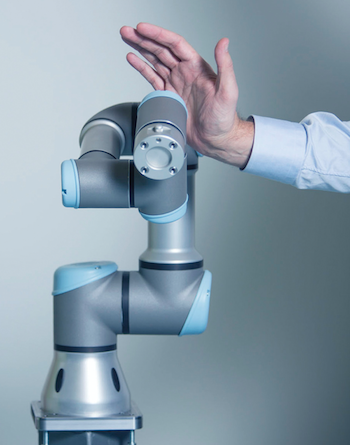
Meanwhile another feature of the robot illustrates how such machines can now incorporate technology that facilitates an HRC approach directly in themselves – in this case the absolutely essential capability of ensuring the safety of the people who will work in proximity to it. Borkeloh explains that the integrated torque sensors respond to the slightest of external forces to enable safe collision protection. “In the case of unexpected contact – human or technical – the robot reduces its velocity instantaneously thereby reducing its kinetic energy to a level that precludes injuries,” he confirms.
But the overall design of the robot also plays a part. According to Borkeloh the housing of the machine is made entirely of aluminium, which in conjunction a streamlined external geometry without sharp edges further acts to eliminate crushing and shearing hazards. Specifically the machines fulfil the requirements of functional safety according to the relevant international standards - DIN EN 62061 up to SIL 2 and EN ISO 13849 up to Performance Level d performed in Category 3.
A qualitative approachIn this instance Borkeloh is certain that a collaborative robot was the only viable solution to automating the monotonous and physically demanding task within one station. Nevertheless he cautions that when implementing HRC applications, it is not enough just to assess the robot. Instead the specific application in its entirety has to be designed according to HRC guidelines. “Cell layout, sensors, workpieces, the process and grippers all have to fit an HRC production concept,” he states. But Borkeloh also stresses that the benefits of an HRC approach may well be qualitative rather than quantitative.
“When implementing HRC applications, improving cycle time is not always the primary goal,” he states. Indeed on that count all that was required at BMW Dingolfing was to meet the same cycle time as the previous manual system, which is less than 30 seconds – there was no necessity to run it faster. However, he says, “the robot dramatically improved the workers’ ability to place parts softly without damaging the teeth of the gearwheels.”
Meanwhile a company that has based its business entirely on the provision of collaborative robots is Danish outfit Universal Robots (UR). According to chief technology officer for UR Esben Ostergaard the company has racked up sales of around 15,000 of its UR3, 5 and 10 machines over the last eight years and is currently continuing to grow rapidly. All three of its robots are six-axis machines with the largest – the UR10 – having a reach of 1.7m and a maximum payload capacity of 10kg.
"Automata’s EVA machine weighs just 8kg including its controller and can be programmed over the internet, requiring only a laptop computer set up within “the same Wifi area as the robot" - Suryansh Chandra, Automata
Ostergaard says that irrespective of the particular industry concerned the ‘driver’ for adoption of the technology is almost always the same – “to combine the benefits of flexibility with those of automation.” Surprisingly, though, he also says that thinking only in terms of cooperative working between robots such as those UR provides and people is overly restrictive. Indeed, he says, installations involving direct interaction between people and robots are actually “quite rare”.
Instead the right approach is to think of the machines as “tools that can be used by people rather than just by experts.” As such key attributes of the machines include their ease of installation, programming and reconfiguration, as well as compactness, lightweight and integral safety capability. Ostergaard adds that another key attribute is the way they can be easily retrofitted to existing operations.
Automotive manufacturing certainly figures amongst the company’s customer base though Ostergaard does not hazard a guess at how many such users there are. In OEM environments, he reports, the machines are generally used in assembly operations rather than bodyshops for simple but repetitive operations such as tightening screws, though quality control applications are increasing.
Interestingly he observes that a distinct characteristic of automotive users, which presumably stems from their previous experience of expensive ‘high-end’ robotic applications, is a reluctance to devolve programming responsibility to shopfloor staff even though the procedures for collaborative machines – physical manipulation of the robot arm through required movements – are very straightforward. Instead the responsibility continues to be that of more specialist staff.
Supporting an ageing workforceOne automotive company that has adopted UR’s robots as a solution to several issues is Nissan Motor Company at its plant in Yokohama, Japan. Apart from streamlining production processes it was also seeking to cope with the problems caused by an ageing workforce and loss of vital skills. The plant employs 3,200 people in the manufacture of engines and parts for electric and hybrid cars. One issue that was proving problematical was the persistent overrun in levels of ‘takt time’ – the cycle time of a specific process – in assembly areas. This was making the company use relief workers with concomitant increases in both labour costs.
So two lines of Universal Robots’ UR10 robot arms were deployed at the plant to offer more time to human workers for obtaining line experience elsewhere, as well as eliminating takt time overruns. The robots were initially deployed to loosen bolts on cylinder head cam brackets. This posed some highly specific demands for robot capabilities including that the main body of robot should be light and easy to move, compatible with a 100V outlet and usable without a safety fence.
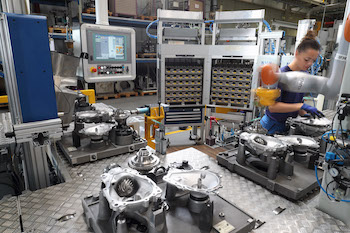
Subsequently the UR10 machines were employed as part of the process for installing engine block intake manifolds, which meant they would need to work in collaboration with human workers. This would mean movement across conveyor belts without safety fences, as well as carrying intake manifold components that constituted loads of 4-6kg when including the robot hands. Nissan therefore made a comparison with various companies’ robots, but reports that the UR10 was selected because of its advantages in cost for a single robot, as well as its weight capacity. It states that only the UR10 had the payload capacity of 10kg.
The robots were installed and programmed with operatives trained and basic operations underway in about a week. Programs were slightly adjusted after the installation and have been operating steadily since, thereby both solving the company’s takt overrun problem and reducing the amount of heavy lifting required for staff. Moreover Nissan now says that being able to move the UR robot to any place it sees takt time overruns means it can think about creating production equipment capable of flexibly responding to the situation.
New lightweight cobotMeanwhile a small start-up UK company is on the verge of introducing its very first product – a lightweight, six-axis collaborative robot that it claims will set new benchmarks for both ease-of-use and affordability. The company, called Automata, which now employs 13 people at its base in London, has some rather unusual origins for an outfit that aims to sell into manufacturing industry as well as other sectors. Its co-founders are two architects Suryansh Chandra and Mostafa ElSayed, who both formerly worked with the practice of the now late Zaha Hadid. According to Suryansh Chandra their interest in the area was spurred by their experience of working with a small robot in the apparently simple task of panel bending, which led both of them to decide that programming techniques in particular were overly complex and intimidating for people without in-depth experience of the technology.
Nevertheless the first thing about the machine that a user is likely to notice is simply its weight of just 8kg including its integral controller, which Chandra says means it requires no special sort of mounting but can instead be simply clamped to almost any available commonplace surface. Other performance parameters for the machine – which is called EVA – are a 600mm reach and a maximum 1.25kg payload.
"In the case of unexpected contact – human or technical – the robot reduces its velocity instantaneously thereby reducing its kinetic energy to a level that precludes injuries" - Henning Borkeloh, Kuka
A number of factors facilitate that low weight, which as Chandra further points out means that the machine can be picked up and moved around by just a single individual. One is the use of lightweight metal and plastic componentry achieved by some use at least of additively manufactured parts. Another is the use of modern – and again intrinsically lightweight – electronics in the controller, which is housed in the base of the machine. Yet another is the consequential diminished weight of the electric motor needed to power the machine. The fundamental enabling factor, though, is that all the elements of the machine are designed from scratch to achieve those objectives. “We don’t use off-the-shelf componentry,” confirms Chandra.
Moreover programming can be effected over the internet. Chandra says that all that is necessary is to access a dedicated website via a laptop computer that needs to be set up “within the same wifi area as the robot”. Then a visual representation of the robot that constitutes the necessary interface will appear on-screen with the actual programming implemented via conventional keyboarding and mouse routines. Essentially, explains Chandra, a “back-end” to the control software that resides on the robot itself is located on a remote server.
As such the machine, in effect, makes use of Industry 4.0 principles for its programming. “It is a connected robot,” he confirms. Alternatively programming can also be carried out by the established procedure of physically moving the robot arm though desired manoeuvres and recording them at the machine.
Chandra says that the formal launch of the EVA device is scheduled for late July or early August. But he also confirms that one of the companies already showing interest in the machine is a UK-based automotive component supplier, which is considering using it for applications including barcode label attachment and machine tending, specifically the retrieval of small components as they are delivered to the production line and then loading them into manufacturing equipment.