Mercedes-Benz blends AI, humanoid robots and craftspeople at its Digital Factory Campus to redefine the boundaries of human-machine collaboration in vehicle production
At its Digital Factory Campus in Berlin, Mercedes-Benz is pioneering new forms of human-machine interaction, from generative AI agents to humanoid robots, blending physical and digital intelligence in its production system.
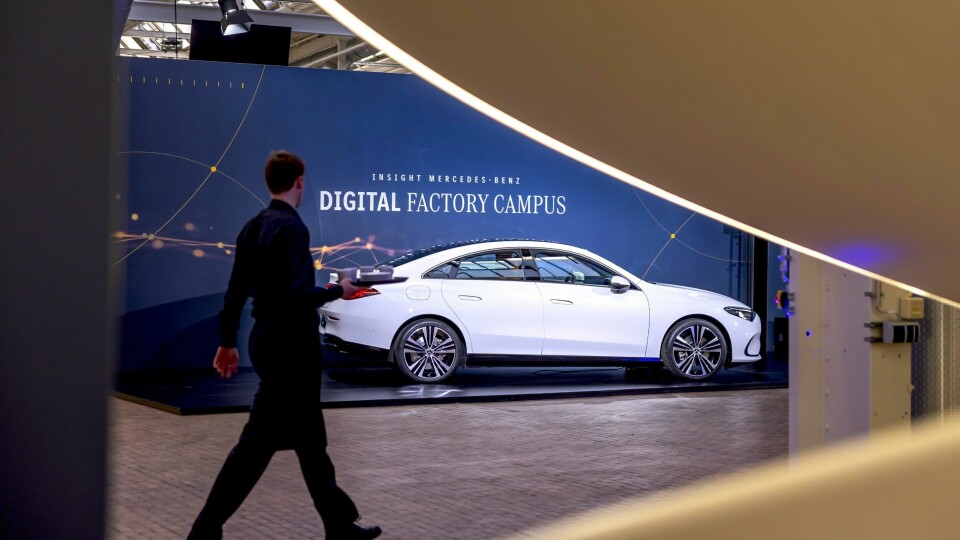
When AMS visited the Mercedes-Benz Digital Factory Campus in Berlin earlier this year, what stood out was not what was missing - commercial assembly lines, the sounds of production - but what was taking shape. This is where Mercedes-Benz prototypes the future of its manufacturing architecture: a controlled environment where engineers, software architects and robots work in sync to test, refine and deploy the digital systems that power its global plants.
Artificial intelligence, data analytics, and human-machine collaboration are not abstract concepts here - they are trialled, iterated and made operational. The campus functions as a technological proving ground, where ideas are stress-tested before scaling. It is less a factory, more a blueprint in motion.
”We are convinced that skills and competence combined with digitalisation is key to the future of production”
Jörg Burzer, Member of the Board of Management, Mercedes-Benz
For decades, the automotive industry has deployed robotics and software as separate pillars of efficiency. Now, Mercedes-Benz aims to weave them into a coherent whole through advanced Human-Machine Interfaces (HMIs).
These interfaces span everything from humanoid robots assisting in production and logistics, to AI chatbots advising production engineers, to self-adjusting tools guided by digital twins. The company’s guiding premise is disarmingly simple: technology should serve those who use it, not displace them.
Craftsmanship meets code at Mercedes-Benz where humans and machines interface in production
“We are convinced that skills and competence combined with digitalisation is key to the future of production,” said Jörg Burzer, Member of the Board of Management at Mercedes-Benz Group AG. His emphasis on continuity is not nostalgic, but strategic. The Berlin-Marienfelde plant, in operation since 1902, is among the oldest in the automaker’s network. But it is also home to the MO360 digital ecosystem and now a testbed for one of the industry’s most ambitious deployments of AI and robotics in a live manufacturing setting.
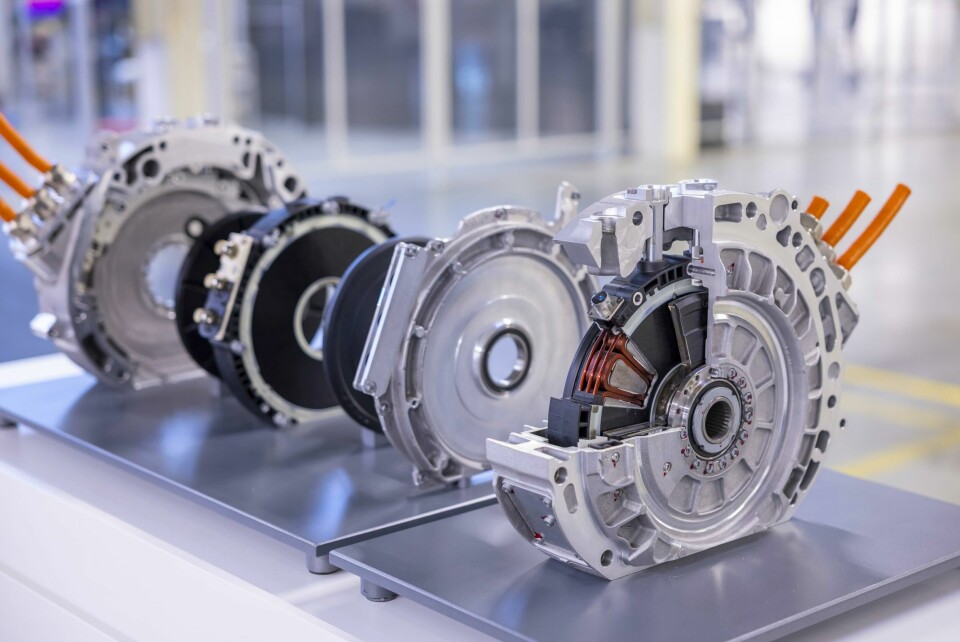
This continuity matters. At Mercedes-Benz, digital transformation is not treated as an exogenous shock but as an evolution of practice. For example, the axial flux motor, which is due to be used in the OEM’s upcoming models, is now being produced and tested in Berlin, exemplifying this union.
Lighter, smaller, and delivering three times the power density of conventional electric motors, the motor is manufactured using over 100 distinct steps and 65 new processes.
Many of these have been co-developed with shopfloor teams who bring experiential insight to the design of production tools and interfaces. Here, humans are not retrofitted into automated systems. Rather, the systems are built to learn from and respond to human expertise.
Apollo rising: the teachable humanoid as technical co-worker in production
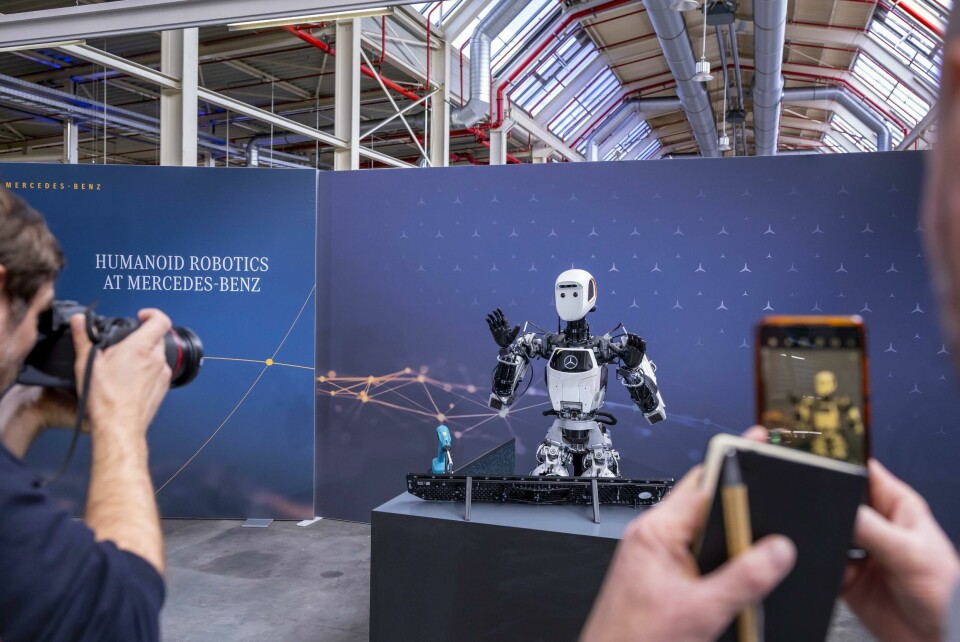
Among the most striking demonstrations of this philosophy is Apollo, a humanoid robot built by Texas-based Apptronik. Apollo is not the kind of single-task automaton that has populated factories since the 1970s.
It is designed for flexibility, intended to perform a range of physically dynamic tasks, from moving parts in intralogistics to inspecting quality on the shopfloor.
“The future lies with robots that can perform many different tasks as opposed to just one,” explained Apptronik’s CEO Jeff Cardenas. “We’re at an inflection point in robotics - similar to the personal computing revolution.”
Apollo is trained not through programming alone, but through teleoperation; a process by which human actions are mirrored by the robot, which then learns through pattern recognition and generalisation. As Cardenas put it, “robots will be able to learn from us, training them, without ever having to hand-program.” This changes the nature of interface; humans do not simply command machines, they demonstrate and collaborate. Training becomes not a software upload, but a physical apprenticeship.
Yet such robots do not arrive ready-made for integration. “Step one is training away from humans,” said Cardenas, reflecting Apptronik’s roots in NASA’s Human-Centred Robotics Lab. Safety remains paramount. Apollo has been deployed first in scenarios such as moving boxes or performing visual checks - tasks that require mobility and dexterity, but pose minimal risk.
Over time, as AI models improve, the robot’s scope of application, and closer integration with human workers will grow.
”Instead of flipping through manuals or asking around, imagine receiving an instant, accurate answer to your vehicle manufacturing questions”
Katrin Lehmann, Chief Information Officer, Mercedes-Benz
Burzer sees Apollo as emblematic of what he calls “Physical AI”. “You have a combination of physical and data innovation,” he noted. “This is, indeed, the symbol of Physical AI. We are proud of our Apptronik collaboration - it is tele-operation on the one hand; AI on the other.”
From chatbots to colleagues Mercedes-Benz evolves production thorugh HMI
If Apollo represents the physical manifestation of AI, then MO360’s AI Factory represents its cerebral dimension. Under the leadership of CIO Katrin Lehmann, Mercedes-Benz has developed a constellation of virtual agents that assist production teams in real time. These range from single-task chatbots that retrieve technical documentation, to multi-agent systems that simulate the input of cross-functional teams.
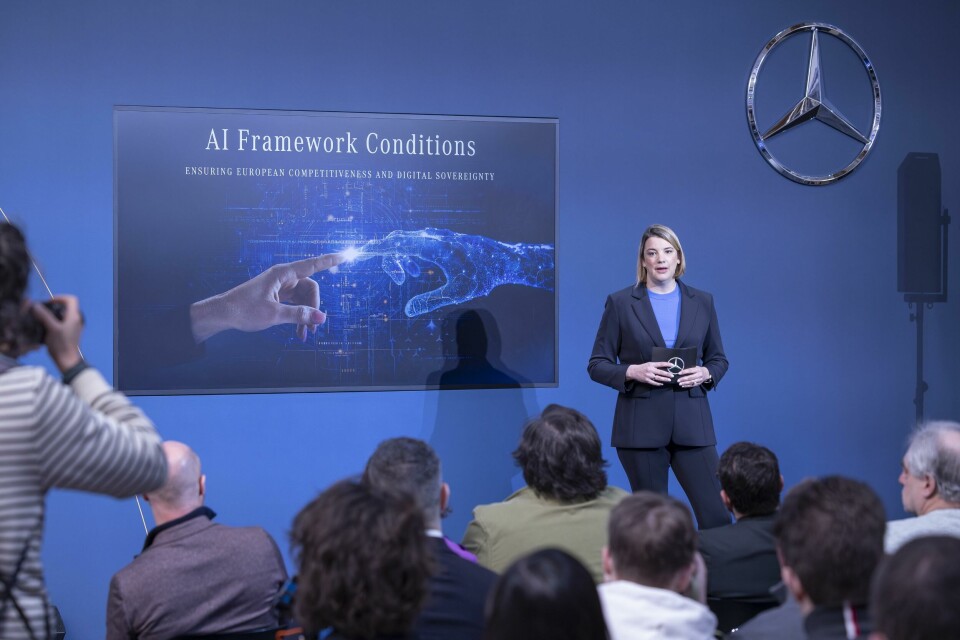
“Instead of flipping through manuals or asking around, imagine receiving an instant, accurate answer to your vehicle manufacturing questions,” Lehmann explained. One such system is the MO360 Digital Factory Chatbot Ecosystem, which has been designed to understand and respond to production-specific queries. Crucially, the system provides not only answers, but references: every piece of advice links back to digitally documented internal sources.
“We built an LLM Suite like a web search feature, but specifically for our departments,” said Nicolai Gruber, Senior Consultant for AI & Ideation. He demonstrated how the system can answer detailed queries such as the height at which RFID tags must be placed on load carriers, with citations and multilingual support. This is more than natural language processing; it is knowledge curation shaped by domain expertise.
“We are entering a new era of digital craftsmanship.”
Stephanie Knizkov, Head of the MO360 AI Factory, Mercedes-Benz
Multi-Agent AI systems: digital teams for physical workers
Even more ambitious is the use of multi-agent AI systems. These act like virtual teams: an engineer facing an issue submits it digitally, and agents representing logistics, assembly, coding, and data begin a simulated collaboration. The entire process is transparent. Every message, decision, and citation is recorded. It is, in effect, a digitised meeting, minus the scheduling.
“What excites me most about this work is the fusion of cutting-edge AI engineering with the decades of craftsmanship and production expertise at Mercedes-Benz,” said Stephanie Knizkov, Head of the MO360 AI Factory. “We are entering a new era of digital craftsmanship.”
Data democratisation as the digital backbone of vehicle production
Much of this is made possible by MO360, Mercedes-Benz’s digital operations platform. Described by Head of Digital Planning Wolf Poppe as an ecosystem akin to a smartphone OS, it integrates over 30,000 users across 30 global plants. The system covers quality, logistics, maintenance, and production management.
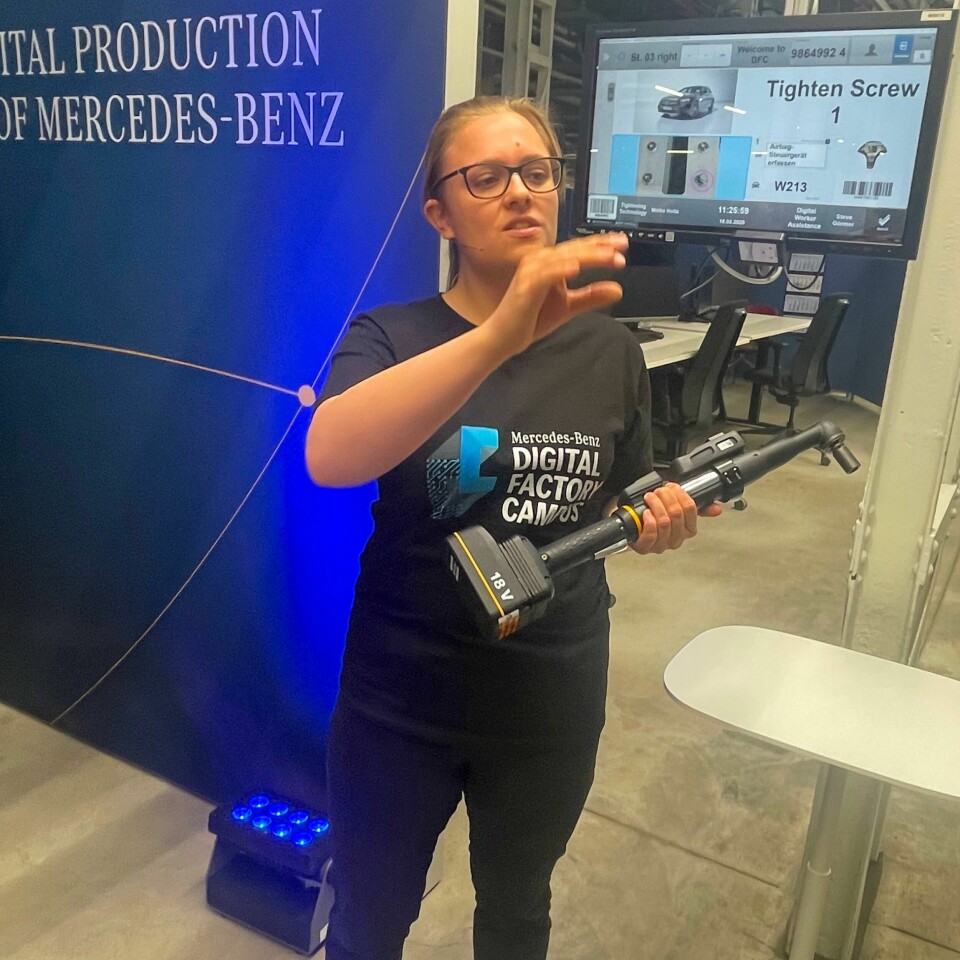
Tools like the smart tightening tool exemplify how real-time data can guide physical processes. As Screw Technology Specialist Maike Holtz demonstrated, the tool syncs with the vehicle’s position, adjusts torque and angle parameters, and confirms successful tightening through visual cues.
The data is logged in the cloud instantly. This enables real-time quality control and traceability across facilities. The platform also includes a Self-Service Data Interface, which allows non-technical staff to perform complex data analysis using natural language prompts.
Employees can access data on vehicle builds, paint shop performance, or supply chain metrics without needing SQL expertise. This “data democratisation” is a strategic goal, enabling faster decision-making and reducing dependency on specialised analysts.
Implications of human-machine interfaces for the automotive industry
What makes Mercedes-Benz’s approach noteworthy is not the technology per se, but its integration. Humanoid robots have long been theorised. AI chatbots are becoming ubiquitous. What is rare is the careful way in which these systems are embedded into the organisation. The goal is not to disrupt workflows but to enhance them through human-machine interaction. This is evident in the OEM’s ideation funnel, which captures suggestions from shopfloor workers and develops them into usable applications.
Read more Human-Machine Interface stroies
- When machines talk back: How HMIs are rewiring the factory floor
- Human-Machine Interfaces at Mercedes, Volvo, Ford, and GM
- BMW develops next-level digital manufacturing at Landshut and Regensburg plants
- Making vehicle manufacturing more flexible at JLR and Daimler
But Mercedes-Benz’s efforts raise broader questions. What does it mean to work alongside a robot that learns from your gestures? How does a production line adapt when knowledge is no longer stored in binders, but in chat interfaces? And what happens to the traditional hierarchies of expertise when AI agents can outperform junior engineers in diagnostic tasks?
Some answers lie in the company’s ethos of empowerment. As Knizkov noted, “AI is not something we build in isolation - it is created with our colleagues, from the initial idea through to deployment.” The systems are not intended to replace the skill and expertise of workers, but to extend their reach.
”The Digital Factory Campus does not herald the end of vehicle manufacturing, but its very redesign”
And with the technological developments quickly accelerating, this ecosystem is not mere utopianism. Lehmann herself noted the need for regulatory frameworks and AI governance, citing her participation in the EU AI Summit in Paris. The risks of over-reliance, bias, and opacity are real. But so too is the opportunity to rethink the very idea (and reality) of automotive manufacturing.
An industrial and vehicle production renaissance on the horizon?
There is a quiet radicalism in what Mercedes-Benz is doing in Berlin. In an environment often distracted by headlines about AI superintelligence or dystopian automation, the carmaker offers a more grounded narrative: one in which machines learn from humans, assist them, and operate alongside them. This is not a return to the artisanal past, but a reinterpretation of craftsmanship for the age of data and dexterity.
The Digital Factory Campus does not herald the end of vehicle manufacturing, but its very redesign. It suggests that the most advanced production environments of the future will be those where humans and machines are both interoperable, and intelligible to each other. And that may prove to be the most powerful interface of all.