JLR and Daimler Truck are building resilience through flexible manufacturing, agile supply chains and modular production systems
JLR and Daimler Truck are adapting their global production systems to meet rising demand for vehicle personalisation, electrification and supply resilience. From simulation to system design, flexibility is now built in from the start.
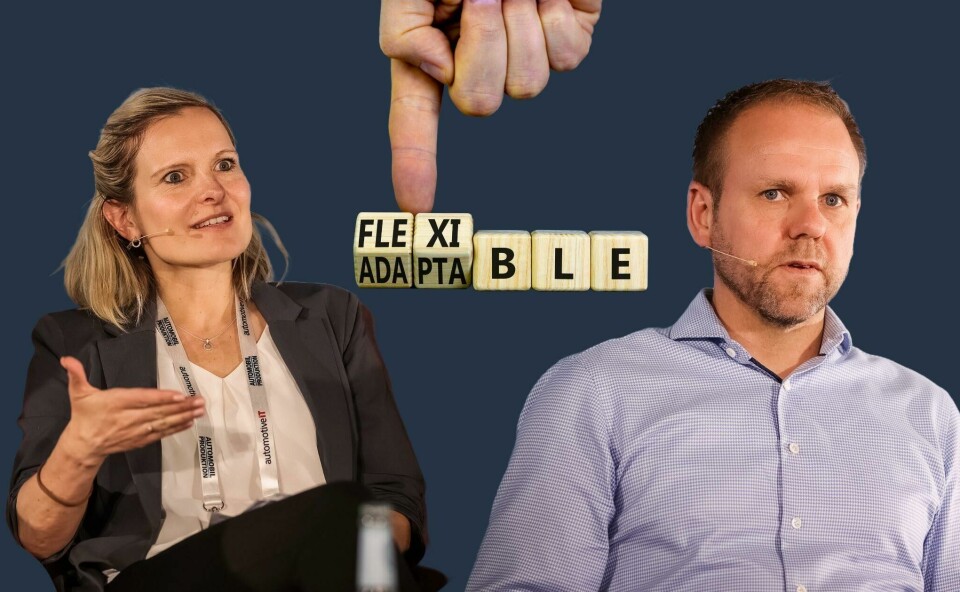
Automotive factories once prized rigidity. Efficiency meant repetition. Any hint of variation in parts or product was discouraged, and logistics systems were often fixed in place like conveyor belts. But that logic is being upended. Today, production must absorb both the volatility of electrification and the deepening of customer demands. At the Automobil Produktion Kongress (APK) in Munich, senior manufacturing leaders from JLR and Daimler Truck offered a revealing glimpse of how this shift is transforming their plants; and the mindset behind them.
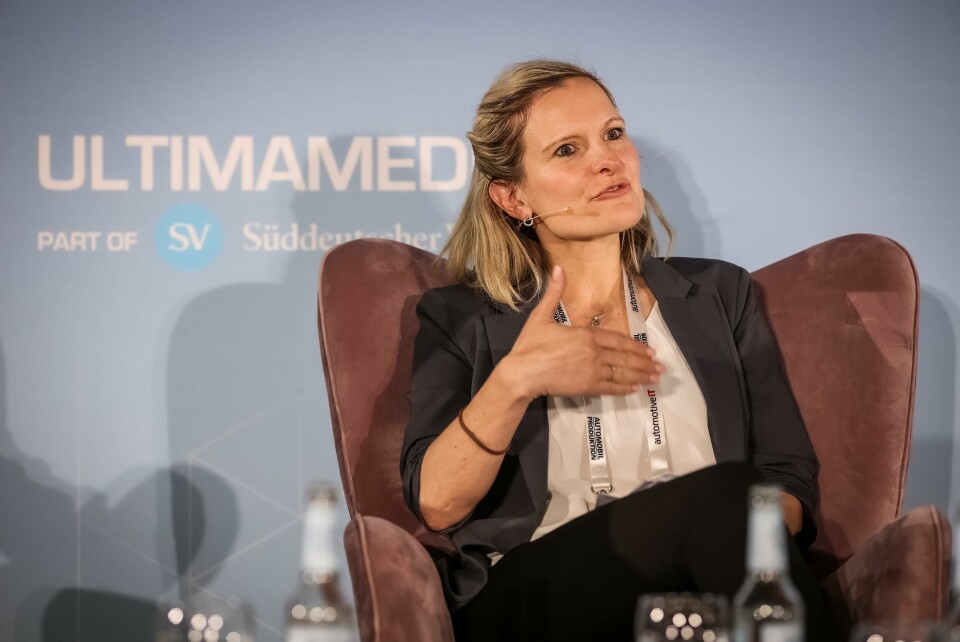
“For us, it’s the ability to adapt our production processes, resources and supply chain to changing customer requirements and product diversity,” said Loretta Dittrich, Global Manufacturing Engineering Logistics Manager at JLR. The transformation she describes is not simply a matter of accommodating more vehicle variants. It is about integrating new platforms into existing flows, balancing product complexity against limited physical space, and embedding agility into both workforce and systems.
JLR’s strategy involves simulating material flow for new models, such as the next-generation Jaguar and various Range Rover derivatives. A surge in painted body variants is pushing the company to reassess storage, sequencing and delivery from the ground up.
The use of control tower systems in procurement enables predictive mitigation of risks before they escalate into disruptions. “We’ve got a material procurement team working with a control tower tool, which helps us to predict issues and resolve them quickly,” she explained.
“We use a product delivery framework where all our logistics and manufacturing requirements must be ticked off before programme kickoff […] this way, we influence design much earlier.
Loretta Dittrich, Global Manufacturing Engineering Logistics Manager at JLR
Daimler Truck, where production is based on build-to-order logic, faces similar pressures. “Flexibility for us is essential because we work with build-to-order systems and face natural volatility in customer needs across different markets,” said Jürgen Distl, Head of Mercedes-Benz Trucks Operations. At Daimler, diesel and battery-electric vehicles roll off the same lines, often in the same shift. The result is not efficiency in the traditional sense, but responsiveness in the face of extreme product diversity.
Systems thinking as the groundwork for flexible manufacturing
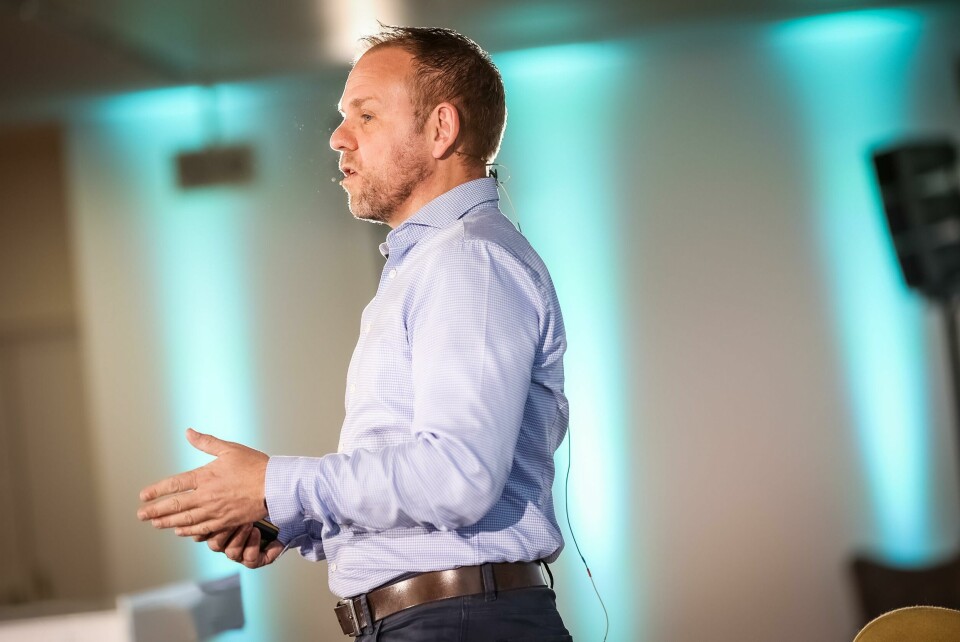
The production lines themselves are not the only thing being reconfigured. Both firms are remapping their organisational structures to allow logistics, engineering and manufacturing to operate more collaboratively. Dittrich noted that JLR’s relatively new Industrial Operations division, formed just two and a half years ago, is already helping to break down legacy silos.
“We use a product delivery framework where all our logistics and manufacturing requirements must be ticked off before programme kickoff,” she said. “This way, we influence design much earlier.”
Daimler Truck is pursuing a similar shift by requiring engineers to engage with plant operations from the outset. “Before engineers make their first drawings, we want them to talk with operations,” said Distl. “We don’t call them red lines, we call them green lines – to understand the implications of their design choices.” This early-stage collaboration extends to aftersales and even retail teams, creating a feedback loop that links the production line to the end user.
Managing the electric transition with flexibility
One of the most testing aspects of this new flexibility is the integration of electrified drivetrains alongside combustion-engine platforms. The transition is not uniform or linear, and uncertainty remains over the speed of adoption across global markets. “We knew early on that we’d need to build both types simultaneously,” said Distl, referring to the diesel and electric trucks now coexisting in Daimler’s plants.
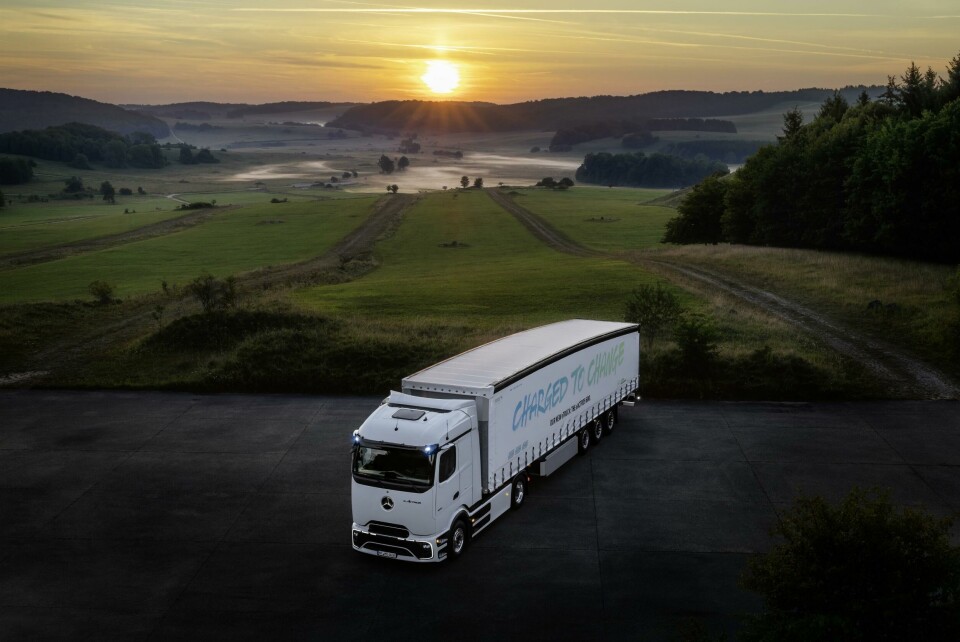
The company’s experience with the early production of the eActros 300 informed a more seamless line integration for the larger-scale eActros 600. Critical to this was the training of thousands of workers in the handling of high-voltage components. “HV training is no small task – it takes time and planning. But it’s crucial for safety and efficiency,” he said.
JLR is going through a similar evolution, bringing battery production and new EV platforms in-house, following an initial partnership with Magna. “We now design product and production flows more effectively,” said Dittrich. This includes integrating kitting zones directly within the line, which reduces both walking time and error rates. Design-for-logistics principles are giving way to a broader ambition: design for automation.
Space, storage and software: the digital component of flexible production
Flexible systems do not come cheap. Increasing variants drive up demands for space, kitting and sequencing. In response, both firms are deploying automation strategically. At JLR’s Solihull plant, automated systems like goods-to-person and pick-to-go are being deployed alongside narrow-aisle racking solutions. ASRS systems are being reassessed based on efficiency rather than novelty. “As Jürgen said, automation must make sense,” said Dittrich. “We’re always looking for technologies that fit our needs.”
Read More Flexible Production Stories
- Honda looks to master flexibility to futureproof production operations
- BMW plants prepare for a new era with Neue Klasse production
- Mercedes-Benz develops flexible van architecture for EV and ICE powertrains
- VW Chattanooga: a masterclass in flexible manufacturing
Daimler is equally selective, particularly in final assembly. In contrast to its highly automated body and paint shops, the firm prefers reliability and maintainability in assembly areas. “We don’t believe in automating everything just for the sake of it – it needs a solid reason and a clear benefit,” said Distl. That pragmatism extends to new technologies like cobots. Both speakers agreed their promise remains largely unrealised. Cobots often require redesigning entire workflows, including safety systems and software integration.
“If automation wasn’t designed in from the beginning, it’s difficult,” said Dittrich.
Building talent for transformation
All of these changes depend on a workforce capable of adapting. For both companies, training and strategic workforce planning are critical. Daimler Truck offers a structured onboarding process for contract workers, while also investing in upskilling to retain long-term talent. “Salary alone doesn’t retain people – you need good training,” said Distl.
”As product complexity rises and production becomes more variable, collaboration between OEMs and suppliers is no longer optional”
At JLR, transformation training is being extended to senior leadership. “Our last session focused on leading through complexity and ambiguity,” said Dittrich. The company is also engaged in workforce planning to map future needs, identify gaps and design career pathways that support its strategic direction. Its National Innovation Centre is a hub for experimentation and training in future technologies.
The collaborative frontier
As product complexity rises and production becomes more variable, collaboration between OEMs and suppliers is no longer optional. “We must be aware of their workforce and supply chain constraints too. It’s too easy to blame suppliers. We’re in the same boat,” said Distl. Synchronising development timelines, especially in just-in-sequence processes, is a delicate task. The tyre supply chain was cited as one example where customisation requires intense coordination.
JLR and Daimler Truck are not merely reacting to change. They are reengineering their systems to anticipate it. Whether in their design frameworks, automation strategies or organisational culture, they are laying down the architecture of a more flexible, more adaptive automotive industry. Flexibility, it seems, is no longer the exception. It is fast becoming the rule.