BMW develops next-level digital manufacturing at Landshut and Regensburg plants
BMW’s Landshut and Regensburg plants showcase how AI, automation, and smart logistics are transforming component production into digitally driven, future-ready operations.
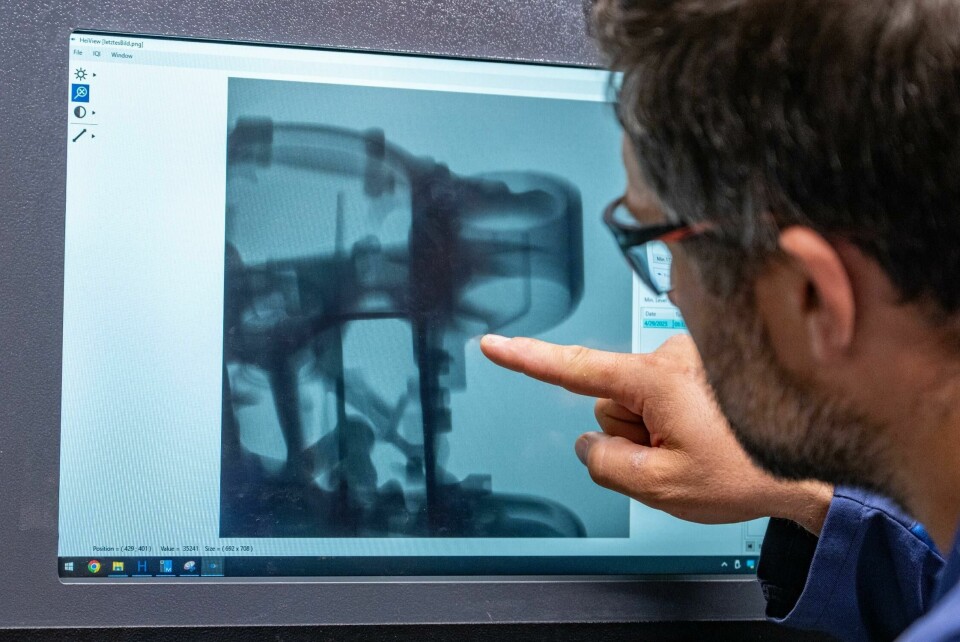
The Landshut plant is accelerating its transformation into a digital manufacturing hub, unveiling cutting-edge technologies and AI-driven processes that are reshaping how automotive components are made and redefining efficiency, quality, and resilience across BMW’s global production network.
“We view complexity as an opportunity and use the data we gain to continuously improve our processes”
Franz Heigl, BMW Head of Digitalisation of Component Manufacturing
As the company’s largest component manufacturing site, the Landshut plant is playing an important role in BMW’s broader digitalisation strategy. “We not only implement technical progress, but also actively shape it in order to secure our competitiveness in the long term,” says Thomas Thym, Head of Plant Landshut. “Behind every digital car there must also be a digital factory.”
Central to this transformation is the “Shopfloor.Digital” program – a global initiative to harmonise production processes across BMW’s 30 manufacturing locations. At Landshut, this means deploying cloud-based IT infrastructure, process automation, and AI for everything from production management to quality assurance.
“We view complexity as an opportunity and use the data we gain to continuously improve our processes,” says Franz Heigl, Head of Digitalisation of Component Manufacturing. Heigl emphasises the importance of Lean Management integration, where digital disruption handling and value stream mapping enable teams to focus on value-added activities. “Our goal is to focus on the essentials in our day-to-day business and prioritise value-creating activities,” he added.
Smart logistics and connected supply chains are also key. AI-powered systems optimise material flows and pre-empt bottlenecks. In the production of the BMW Energy Master – the core control unit of Neue Klasse vehicle batteries – inline AI monitoring and cleanroom testing ensure global supply with zero defects.
Even in areas like aluminium casting, BMW says it is setting new standards. Each electric motor housing undergoes a 42-second AI-driven CT scan that produces a 3D model from 2,400 images, enabling precise, automated quality control.
An AI Lab has also been unveiled at the plant. This is an internal innovation space where employees experiment with PowerApps, build no-code digital tools, and explore AI use cases through the Technology Trend Radar and AIQX quality system.
“We are using AI for quality control in vehicle assembly. In this way, we are optimising our production processes and creating added value for our products and, ultimately, for our customers”
Armin Ebner, Head of Plant Regensburg
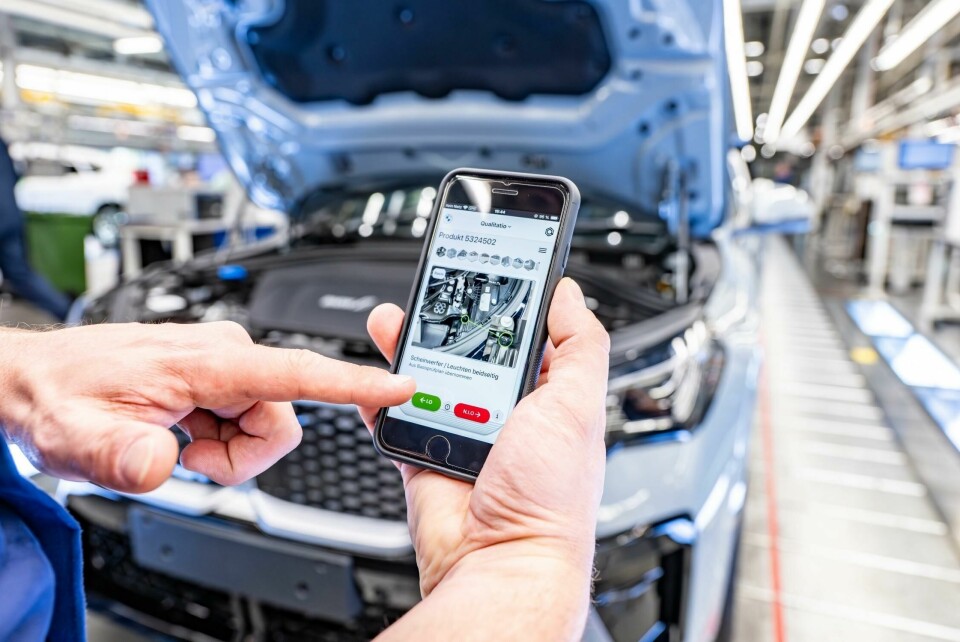
The inspections are carried out using a mobile app interface that provides an intuitive checklist for operators.
AI vehicle quality control at Regensburg
Another example of BMW’s digitalisation progress comes from Group’s Regensburg plant. The OEM says this facility is taking vehicle quality assurance to the next level with an AI-powered system developed through the “GenAI4Q” pilot project. This software is transforming how inspections are conducted on the approximately 1,400 vehicles produced daily, offering faster, smarter, and more precise quality control tailored to each individual car.
At the heart of the project is a learning-based analysis tool that delivers customised inspection recommendations for every vehicle that rolls off the line. “The use of artificial intelligence supports the digital transformation of BMW Group production towards an intelligently connected factory,” said Armin Ebner, head of Plant Regensburg. “We are using AI for quality control in vehicle assembly. In this way, we are optimising our production processes and creating added value for our products and, ultimately, for our customers.”
The challenge lies in the sheer variety of vehicles produced. Regensburg builds a new car every 57 seconds, each configured uniquely to meet specific customer preferences across global markets. The plant produces ICE models, plug-in hybrids and fully electric vehicles – all on a single, flexible assembly line.
“Our AI tool generates an individual inspection catalogue for each specific customer vehicle,” explained Rüdiger Römich, who oversees the Test Floor and Finish in Regensburg’s vehicle assembly. This AI doesn’t just look at standard vehicle data – it crunches real-time production data and identifies patterns to determine what checks are necessary and in what sequence.
The inspections are carried out using a mobile app interface that provides an intuitive checklist for operators. “Intuitive usability makes it easy to record findings,” Römich noted. “Employees can also access additional functions when needed – for example, a microphone icon in the app activates voice recording.” The AI manages both speech recognition and transcription, using standardised codes to maintain consistent reporting.
This innovation was developed in partnership with Munich-based startup Datagon AI and is now actively enhancing operational efficiency and quality assurance in Regensburg.
By customising inspections to each vehicle, the GenAI4Q system is reducing unnecessary checks, improving speed and reliability. It’s also easing the workload on quality control specialists, allowing them to focus more on value-added tasks and decision-making.
As Ebner notes: “This is not just about making inspections faster – it’s about building smarter systems that understand and adapt to complexity, just like our vehicles do.”