Augmented reality, AI, cobots and digital twins are transforming automotive production by enhancing worker training, planning, inspection and collaboration
Human-machine interfaces are becoming central to car production. With AR, cobots, AI inspection and digital twins, OEMs like Ford, Volvo, GM and Mercedes are reshaping the way people and machines interact.
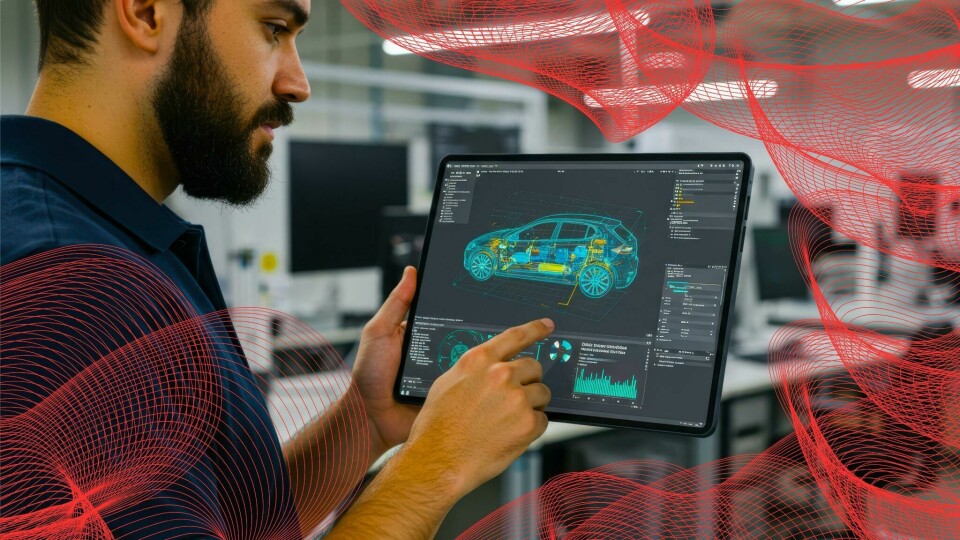
For more than a century, manufacturing lines have run on a delicate choreography of human dexterity and mechanical repetition. But in today’s automotive factories, the rhythm is changing. Across production halls from Cologne to Chattanooga, the interface between man and machine is being rewritten - not in steel, but in code, sensors and holograms.
Augmented reality headsets hover instructions in mid-air, allowing new workers to learn by doing without touching a spanner. AI-powered vision systems scan weld seams with a scrutiny no inspector could match. Digital twins - entire factories rendered in photorealistic simulation - let planners walk through production lines years before they exist. And cobots, once caged off for safety, now work side by side with operators, responding to gestures and voice commands.
”The result is a factory that is “digital by default,” where workers collaborate with machines through intuitive, data-rich interfaces”
What links these technologies is not just the novelty of smart tools, but a deeper industrial shift. As automakers pursue more flexible, electrified and low-volume production, traditional control systems are giving way to adaptable, data-rich human-machine interfaces (HMIs). These do not remove people from the process; they embed their judgment, extend their reach and reduce their fatigue.
The result is a hybrid model of production - not quite robotic, though not wholly manual - that promises greater efficiency, resilience and inclusivity. For automotive manufacturers, the future of labour lies not in replacing the worker, but in reshaping how the worker and the machine think and move together.
Mixed reality for assembly and training
Ford has long been known for innovation in automotive production. Today, it is not assembly lines or automation that define its edge, but mixed-reality headsets. At plants in Michigan and beyond, new operators don Microsoft HoloLens 2 devices and follow holographic guides that float in their field of view.
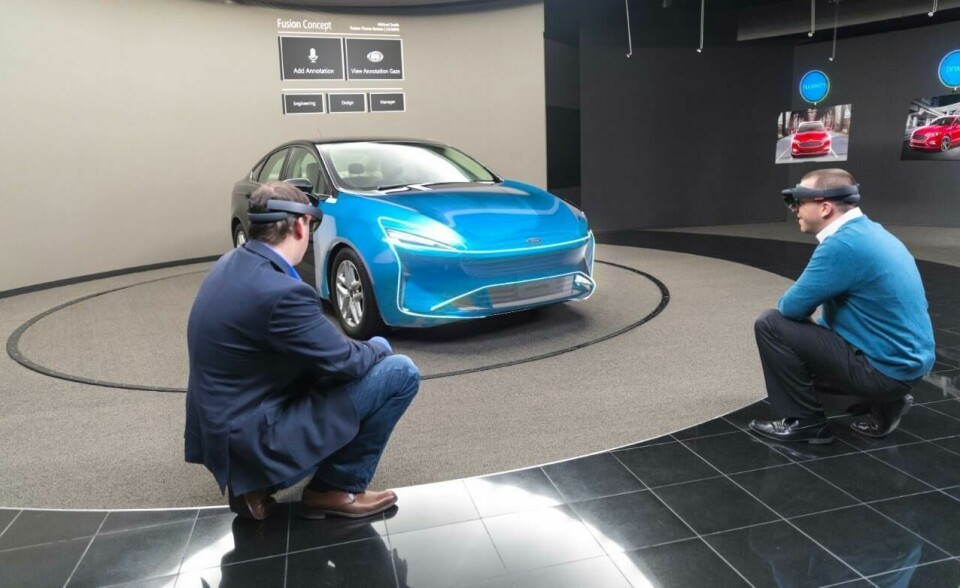
These augmented overlays help them learn complex engine assembly tasks, speeding training and reducing errors. “The technology has accelerated the learning curve,” says Ford. At Rawsonville Components Plant, training time has been cut from days to hours, with new hires building “muscle memory” before ever touching the line.
In one quality audit, a HoloLens guide highlights each connector in a wiring harness, enabling trainees to follow a glowing indicator and spot miswirings that would prevent an engine from starting. By 2024, Ford had expanded HoloLens use to multiple plants including Dearborn, Louisville and Rawsonville. The gains have included faster onboarding, improved accuracy and more confident (and connected) operators.
”This virtual assembly approach feeds into BMW’s broader iFactory programme, which unifies planning, data analysis and AI diagnostics across its plants”
Volvo also has AR tools deeply embedded into its workflows. On the production line, workers using AR glasses see visual step-by-step instructions overlaid on real components, minimising errors and improving efficiency. In QA processes, Volvo uses PTC’s Vuforia AR platform to guide inspectors through 40 checks with 200 possible variants per engine, and has done for several years now, but the technology is beginning to embark on its maturation journey.
Previously at Volvo, five weeks of training were needed on average for this type of quality control work. With AR, training time has already fallen 60% and inspection time by 90%. Another ongoing example is Volvo’s system which integrates with PTC ThingWorx to create a digital thread that links real-time AR inspections with upstream data in engineering systems. Any defect flagged visually becomes part of a continuous improvement loop, resulting in tangible savings across its global manufacturing footprint.
Read more Smart Factory stories
- Making vehicle manufacturing more flexible at JLR and Daimler
- When machines talk back: How HMIs are rewiring the factory floor
- GAME Theory: Is Tesla’s “Unboxed” process a new production paradigm?
- Digital threads weave together connected car factories
Factory planning with augmented reality
Volkswagen also uses HoloLens for production planning. At its Chattanooga plant in the US, engineers use AR goggles to visualise full-scale models of future machinery and walk through them virtually. This helps identify risks early (as in the case of collision points between robots and conveyors) before anything is physically installed.
This visual alignment tool has proven crucial in launching lines for EVs like the ID.4, allowing cross-functional teams to review layouts collaboratively. VW also links this to its Industrial Cloud, developed with AWS and Siemens, to connect sites globally and apply AR insights at scale.
BMW has pursued a dual track of AR deployment. On active lines, the company uses AR glasses to provide step-by-step guidance for complex assemblies. But the deeper transformation is in planning: at Regensburg, BMW created immersive digital twins of future EV lines, complete with virtual human avatars performing tasks. Workers experience new workflows years ahead of production start.
Ergonomic design improves as planners catch awkward tasks in simulation. This virtual assembly approach feeds into BMW’s broader iFactory programme, which unifies planning, data analysis and AI diagnostics across its plants.
Digital Twins and virtual factories
Digital twins are now central to strategic factory planning. Mercedes-Benz has gone furthest with this concept. Using NVIDIA’s Omniverse and the OpenUSD format, the carmaker built high-precision twins of its Rastatt, Kecskemét and Beijing plants. These include every station, robot and aisle - even break rooms.
Engineers use these twins to walk through entire factories in VR, adjust layouts, simulate retooling, and anticipate bottlenecks. Mercedes reports that these tools have doubled the speed of line configuration and halved ramp-up time for new EV lines based on the MMA architecture. The virtual ramp-up ensures stability before physical changes occur.
The twins are part of the MO360 ecosystem, which links dozens of global plants via real-time production data, allowing Mercedes to optimise and benchmark across sites. Suppliers can also participate in virtual planning, streamlining tooling delivery and collaboration.

Toyota has applied a similar philosophy at Toyota Motor Manufacturing Turkey. Here, digital twins supported the launch of a new SUV line by enabling remote collaboration. Global teams reviewed line balance and equipment changes without needing to travel. Engineers used the model to simulate failure scenarios and optimise ergonomics in advance.
The digital twin halved preparation time, supporting Toyota’s lean philosophy with digital foresight. It also provided a platform to simulate new physical innovations, like giga-casting and autonomous material transport, before implementation.
AI-Enhanced Quality Inspection
On quality control, AI now plays the role of tireless inspector. Ford’s MAIVS (Mobile AI Vision System) uses standard smartphone cameras and AI to compare photos of assemblies against reference models. When deviations occur - such as a missing fastener - the system halts the line and notifies the operator.
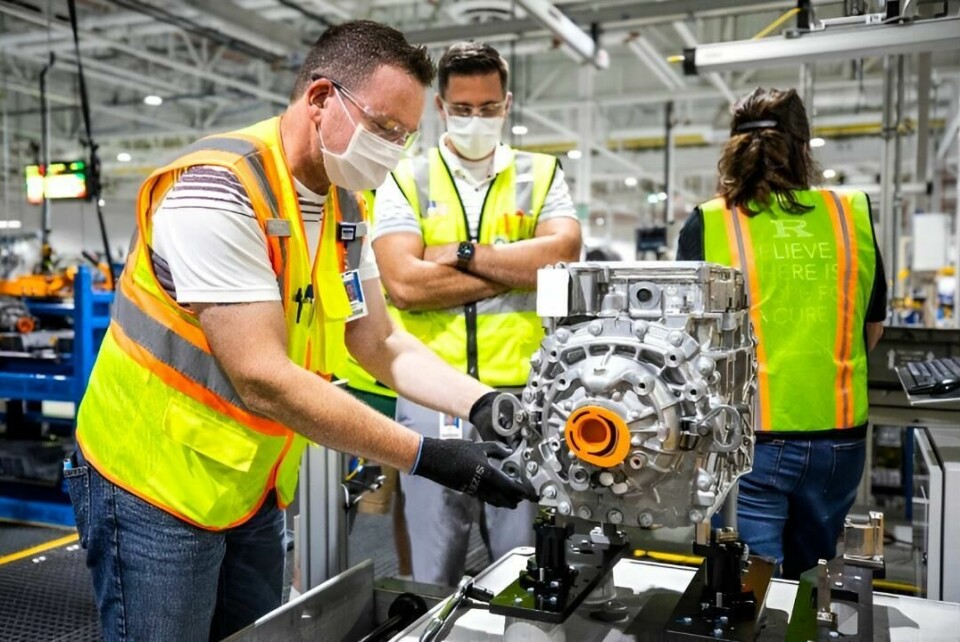
Ford has deployed MAIVS at over 300 stations across 20 plants, performing 60 million inspections annually. At Van Dyke Electric Powertrain Center, the system eliminated recurring defects in electric oil pumps by catching misaligned rubber inserts. Visual feedback is delivered on station monitors, empowering workers to act instantly.
GM has taken a robotics-led approach. AI-powered vision tools inspect laser welds on door panels and paint finishes for imperfections. These systems use cameras and heatmaps to show anomalies on user dashboards, and highlight poor coverage or pores invisible to the human eye.
AI also helps in battery production: GM uses machine learning to analyse pressure tests and sensor data, pinpointing potential leaks early. According to CEO Mary Barra, “AI in manufacturing helps us build smarter vehicles while empowering our workforce.”
Škoda Auto employs a network of over 70 high-res cameras, provided by VDS Vivaldi, to scan aluminium housings for electric motors. This AI vision cell detects flaws as small as 0.2mm. Operators only intervene when the AI flags a suspect part - enhancing speed, consistency and workforce efficiency.
”In one example, Ford’s Cologne plant used six cobots to polish Fiesta paintwork. Workers taught the cobots the required movement by guiding their arms - a method known as lead-through programming”
Cobots on the line
Cobots - collaborative robots - represent another evolution in human-machine interface. At Ford’s Cologne plant, a cobot nicknamed Robbie assists operator Dietmar Brauner, who has reduced mobility. Dietmar positions engine covers, then signals Robbie to press them into place. The cobot only moves when triggered and stops instantly if hands are detected nearby.
The project, supported by academic researchers and disability funding, has shown how cobots can extend careers and open manufacturing to a broader workforce. No safety cage is needed, and interaction is intuitive.
Elsewhere, Ford’s Craiova plant in Romania uses UR10 cobots to apply grease, fill oil, and conduct camera-based inspections. Operators were trained using UR’s touchscreen interface and online tutorials. The cobots offer precision and consistency, easing the physical burden on staff.
Other carmakers have used cobots to hold windows and dashboards during installation, apply sealants, and polish car bodies. In one example, Ford’s Cologne plant used six cobots to polish Fiesta paintwork. Workers taught the cobots the required movement by guiding their arms - a method known as lead-through programming.
The International Federation of Robotics expects cobot use in automotive to rise tenfold by 2030, but many carmakers feel that this promise of increased flexible production is more likely to be fulfilled by humanoid robots as opposed to cobots. However, as things stand flexible interfaces like tablets, drag-and-drop software and voice triggers are making integration faster and more accessible, than compared to formerly more manual processes.
Smart tools and interfaces ignite automotive production efficiencies
Beyond robots, many factories now deploy wearable and light-guided tools. Smart gloves vibrate if the wrong bolt is picked. Light projectors show where to place components. Exoskeletons support workers’ arms during overhead tasks. These assistive HMIs reduce errors, injuries and fatigue.
ABB’s RobotStudio AR app allows engineers to position virtual robots on the shop floor using tablets or smartphones. This ensures correct reach and placement before physical installation. Volvo has deployed over 1,000 robots for EV production using such tools to minimise commissioning time.
A newer frontier is AI-generated programming: cameras observe a human perform a task, and software builds a robot routine from the demonstration. Such low-code HMI tools may eventually allow anyone to configure automation.
A digital factory by default
Underpinning these advancements are industrial platforms from Rockwell, Siemens and PTC. FactoryTalk, SIMATIC WinCC and ThingWorx are common tools enabling real-time data dashboards, predictive analytics, and unified control systems. These platforms give maintenance teams early warnings - such as vibration anomalies predicting a bearing failure - via tablet or control room interfaces.
BMW’s Landshut plant uses AI not just for quality but also for cybersecurity alerts. Predictive maintenance via anomaly detection is becoming standard. Toyota’s twins also simulate downtime scenarios, allowing contingency planning.
The result is a factory that is “digital by default,” where workers collaborate with machines through intuitive, data-rich interfaces.