Inside Tesla’s ‘radical’ manufacturing shift: How the “Unboxed” process could slash EV production costs and impact the automotive industry
As Tesla gears up to launch its $25,000 electric car, its “Unboxed” manufacturing process draws both praise and scepticism. AMS explores its potential to transform automotive production and its implications for the industry.
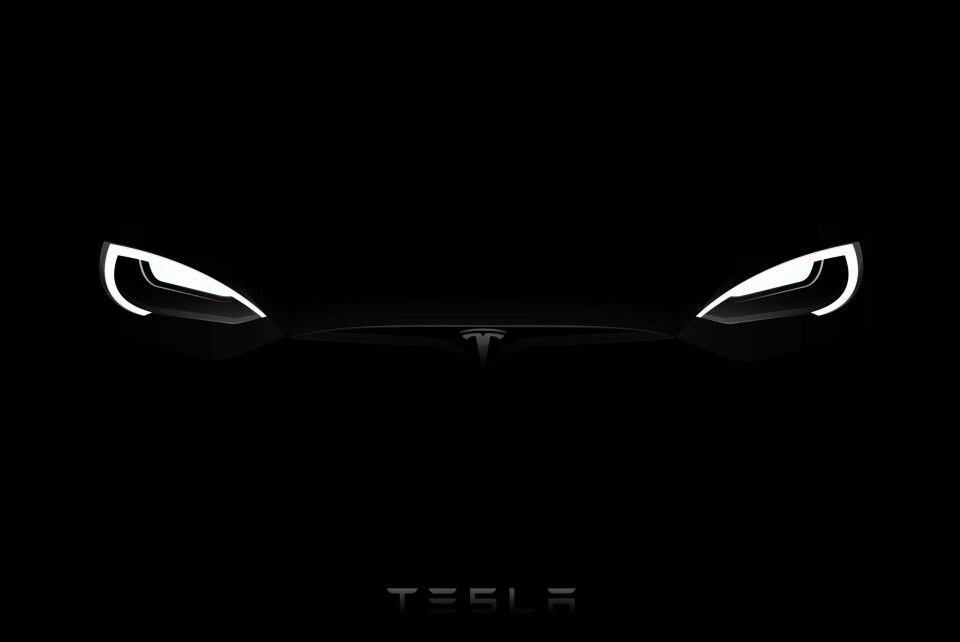
The automotive industry is no stranger to transformation, but Tesla’s Unboxed Manufacturing Process, unveiled in March 2023, has ignited a fierce, protracted debate about the future of car production. Promising to slash production costs by up to 50% and reduce factory footprints by 40%, this modular approach could make electric vehicles (EVs) more affordable, particularly Tesla’s much-anticipated (and imminent) $25,000 model. As competition from low-cost Chinese manufacturers intensifies, Tesla’s innovation could set a new standard - or falter under the weight of its own ambitions.
Decoding Tesla’s “Unboxed” production process
Traditional car manufacturing relies on a linear assembly line, a century-old model pioneered by Henry Ford, where vehicles move through stations, gradually taking shape. Tesla’s Unboxed Process, also known as Global Automotive Modular Evolution (GAME), upends this by building cars in separate modules-front, rear, battery, and floor sections-before a final assembly stage. “It’s radical, crazy, and no one has pulled this off,” said Lars Moravy, Tesla’s VP of Vehicle Engineering, likening the process to assembling Legos.
”Tesla claims cars can be built 25% faster, requiring 40% fewer workers, which could reshape factory operations at a fundamental level”
This modularity allows simultaneous work on multiple sections, reducing production time and factory space. Tesla, is in many ways a master of unmatched automotive production optimisations. Giga-casting, a process which uses massive presses to mould large parts like the Model Y’s underbody in a single piece, eliminates hundreds of components and welds, making vehicles lighter and assembly simpler.
The OEMs early development of advanced robotics, including Tesla’s Optimus Bot, further streamline tasks at the carmaker’s plants, with Tesla recently announcing forward-looking plans for thousands of units to be implemented in North American factories by this year; and a million annually by 2030.
The promise of affordability and efficiency
Tesla’s primary goals with GAME, are efficiency and affordability. With the OEMs cheapest model currently priced above $40,000, a $25,000 EV is critical to compete with Chinese rivals. What it will mean, on the factory floor and how it will translate into production, is still being weighed by vehicle production experts, but the reality will soon be clear. According to Bloomberg, the “Unboxed” process could halve production costs and reduce factory footprints by 40%, enabling smaller, cheaper plants.
Tesla is all-in on optimisations from inceptions. For instance, Tesla’s newly planned factory in Monterrey, Mexico, is expected to cost $5 billion, with construction savings of up to 30% once it kicks off production, following a pause in construction due to uncertainties caused by unpredictable North American tariffs.
Industry debate: is “Unboxed” a production game-changer or overhyped?
Beyond cost, the “Unboxed” production process, if successful, will enhance sustainable production. The increased modularity of design and assembly will minimise waste, with real-time data analytics used to optimise resource use, aligning with the industry’s environmental goals.
Tesla claims cars can be built 25% faster, requiring 40% fewer workers, which could reshape factory operations at a fundamental level.
The “Unboxed” process has divided experts. Martin French, manufacturing consultant and managing director at consulting firm Berylls, sees it as a seismic shift. “I got the feeling when I watched the Tesla presentation that the Toyota Production System handbook has just been thrown up in the air and machine-gunned down,” he told Reuters. Meanwhile, Jan-Philipp Büchler, the Free University of Dortmund, calls it “revolutionary,” noting it eliminates traditional automotive production steps and reduces complexity.
”Other manufacturers, including Toyota, Ford, and Kia, are reportedly exploring similar hyper-modularity production methods, driven by competitive pressures”
Yet, sceptics question the process’s novelty. James Womack, co-author of The Machine That Changed the World, argues it’s primarily an assembly process, unlike Toyota’s holistic production system. On the more cynical side, Hide Oba, a former Toyota executive responsible for model line activities, warns of rigidity, saying, “it won’t work unless production of these big, high-content unboxed vehicle modules are completely synchronised, and finished blocks arrive for a final put-together just-in-time.” An unnamed German premium manufacturer’s production director dismissed it as, “not compatible with our quality promises.”
Learn More About Lean Production With Leaders In Automotive… Detroit Is Where the Future Connects.
As Tesla redefines modular production, join the manufacturers, engineers and leaders shaping the next industrial revolution in automotive.
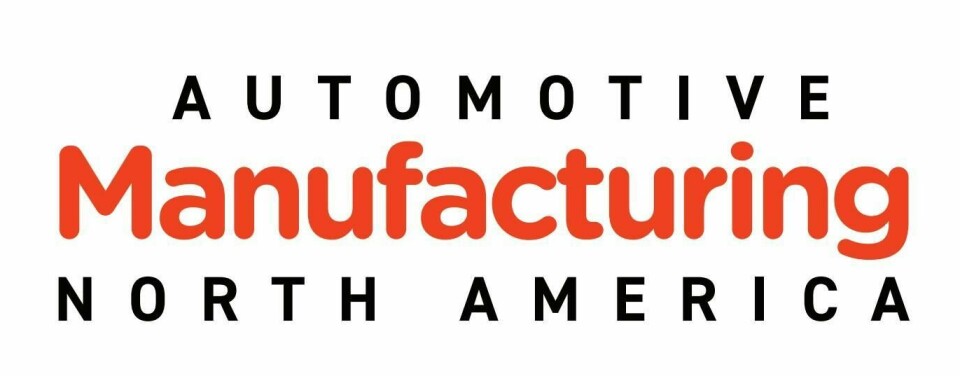
Automotive Manufacturing North America returns to Detroit at The Henry Hotel on 22-23 October 2025 - the place to debate, benchmark and connect with those putting radical ideas into practice.
Attendance by global OEMs is confirmed.
Vehicle production challenges on the horizon
While larger carmakers have a competitive advantage, smaller players could find it more difficult to utilise the process, if proved successful. Consequently, implementing the “Unboxed” process across global vehicle production ecosystems, is not without its hurdles. The high cost of giga-casting machines and accompanying robotics poses a barrier, particularly for smaller manufacturers. Technical challenges include ensuring stable attachment of modules without damaging interiors, maintaining consistent paint quality, and preventing corrosion issues.
Supply chain dependencies, such as rare-earth magnets for Optimus Bot actuators, add complexity, especially with export restrictions from China. Moreover, Tesla’s history of missing deadlines raises doubts about the 2025 rollout for its affordable EV.
Tesla’s rollout: Giga Texas and beyond
Tesla is testing the Unboxed Process at its Gigafactory in Texas, with plans to expand to Mexico (as mentioned) and Germany. The Model Y already uses giga-casting, reducing parts and robots significantly (Grant Thornton). The process is expected to be fully operational in Tesla’s main plants by late 2025, supporting the Model 2, codenamed Project Redwood.
Other manufacturers, including Toyota, Ford, and Kia, are reportedly exploring similar hyper-modularity production methods, driven by competitive pressures. Interestingly, there are reports that Chinese carmakers, known for agile production and supply chains, are particularly keen to adopt Tesla’s approach.
Read more Tesla-related stories
- Tesla’s EV battery production and global gigafactory network
- Megacasting: a new frontier or unfounded flare-up?
- The robots are here: How humanoids are changing auto production
- Musk halts Tesla Mexico gigafactory until after US election
Unboxing the future of Tesla’s “GAME” for automotive manufacturing
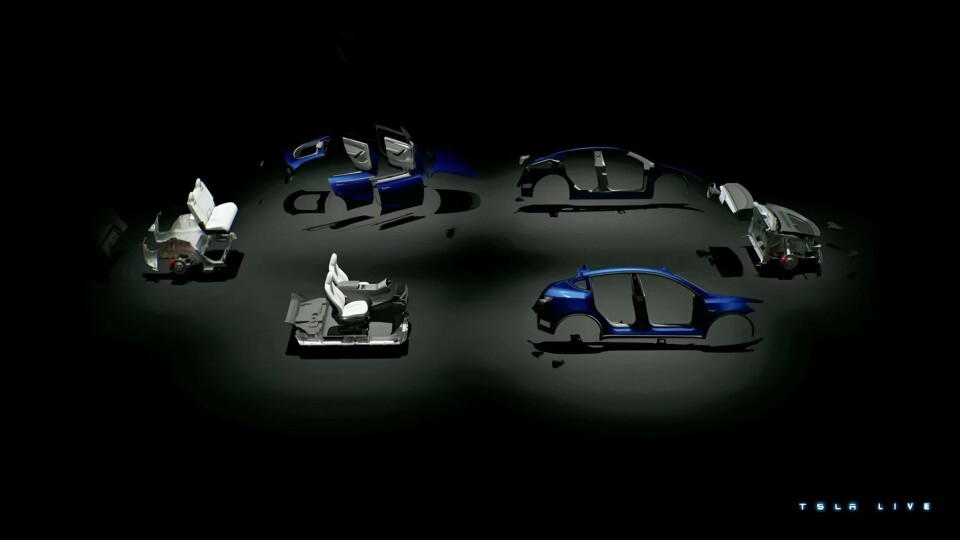
If successful, the “Unboxed” process could redefine automotive production industry standards. Advances in AI and robotics could further enhance its capabilities, enabling real-time adjustments and greater flexibility. However, its success hinges on overcoming technical and financial barriers and proving scalability across diverse vehicle models.
The process could also impact the workforce. Requiring 40% fewer personnel, it may lead to major job displacement, though new roles in robotics maintenance and data analytics could emerge - but of course, not on the same scale as those lost. For automotive manufacturers, the choice is to either adapt to the shift or risk falling behind in an increasingly competitive market.
Tesla’s “Unboxed” production process is a big bet on high-modularity and automation, with the potential to make EVs more accessible and sustainable. While its cost-cutting and efficiency gains are compelling, challenges like quality control and high initial costs temper current enthusiasm. As Tesla rolls out this method in 2025, the industry watches closely. Whether it proves “revolutionary” or simply incremental, its impact will resonate far beyond Tesla’s own production factories.
Have you heard about our new brand?
Automotive Digital Transformation!
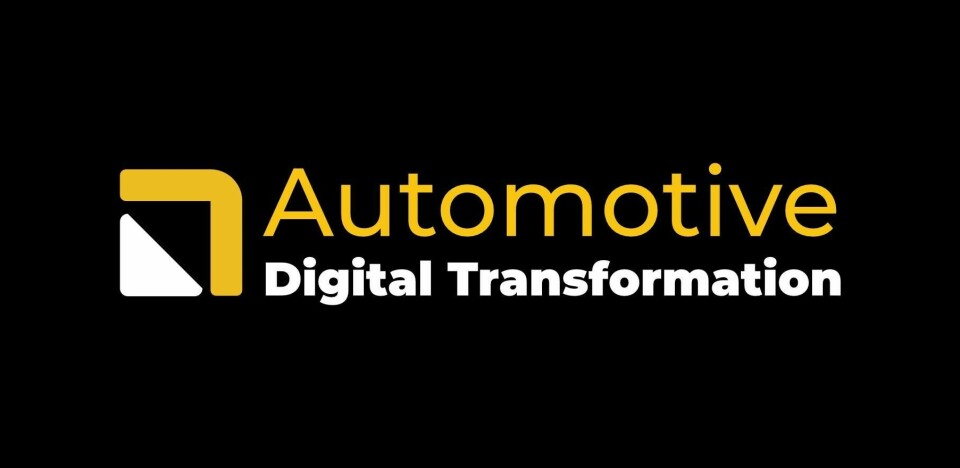
ADT is designed to be the go-to hub for the innovators and changemakers driving the digital evolution of the automotive industry.
Closely connected with our other brands, ADT is here to lead the paradigm shift.