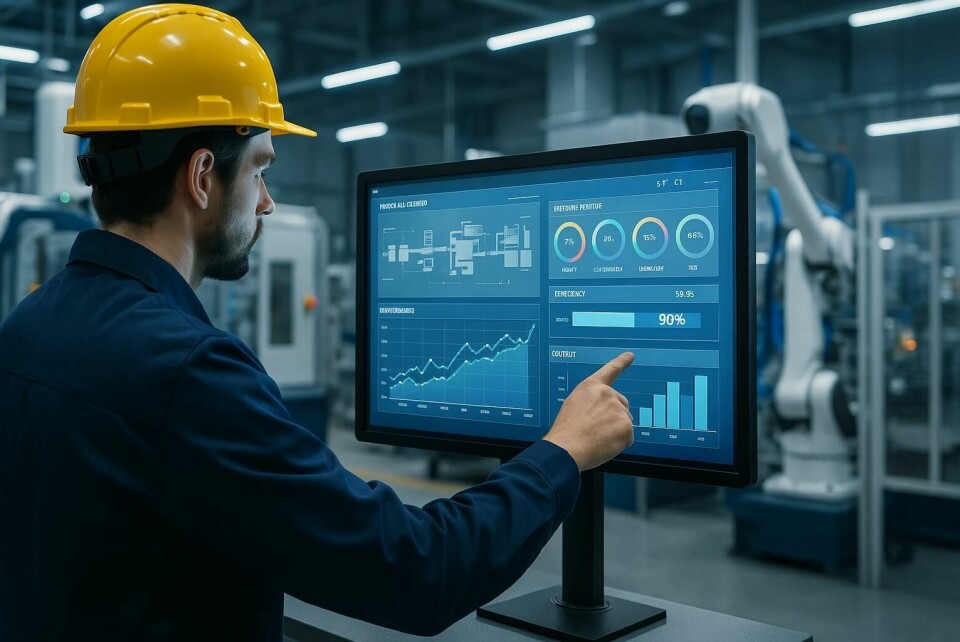
The rise of HMI: Human-machine synergy in smart manufacturing
Human-Machine Interfaces (HMIs) are no longer simple control panels; they are intelligent, connected systems that empower operators with real-time insights, intuitive workflows and predictive guidance. As HMI technology evolves, it is reshaping how workers interact with automation, improving ergonomics, safety and efficiency, while bridging the gap between cyber-physical systems and human expertise.
In the age of smart manufacturing, it’s not man versus machine – it’s man with machine.
In today’s automotive manufacturing landscape, HMI systems are no longer just functional dashboards – they are critical, intelligent channels linking humans with complex cyber-physical systems. As smart factories take hold, HMIs have evolved into decision-support platforms, capable of synthesising and visualising real-time data, enabling operators to act with speed, precision and foresight.
At the heart of this evolution is connectivity. Modern HMIs are embedded in broader networks that connect shopfloor machinery with higher-level systems such as SCADA (Supervisory Control and Data Acquisition), MES (Manufacturing Execution Systems), and enterprise ERP software. This connectivity enables seamless data exchange across the production stack, offering workers a unified view of system performance, machine health, and quality trends.
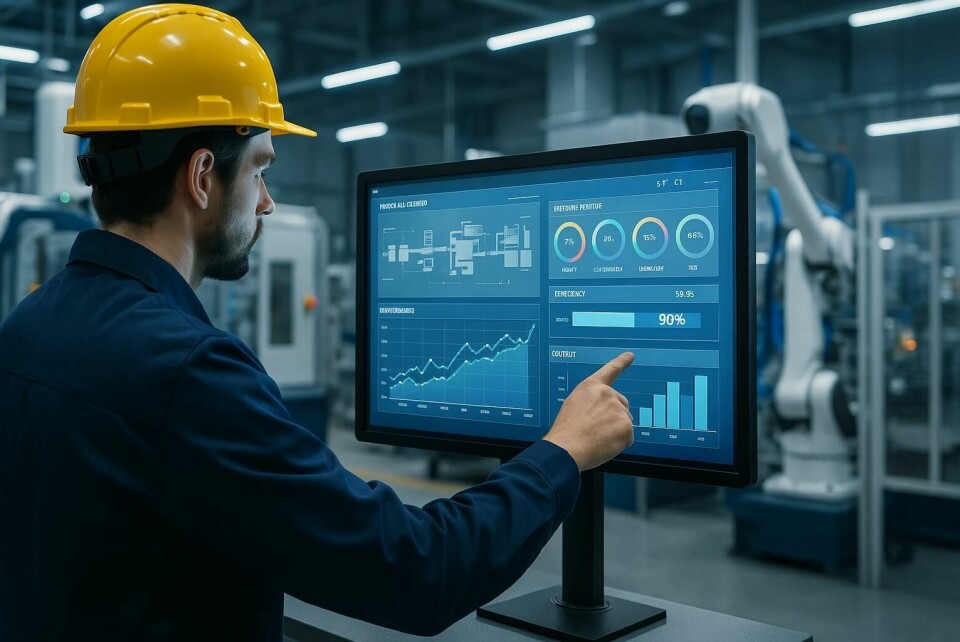
Unlike traditional control panels that reacted to simple machine states, today’s HMIs are equipped with IoT-enabled sensors, edge computing capabilities, and AI algorithms. These allow for predictive maintenance, real-time diagnostics, and contextual alerts. For instance, a stamping press operator may receive an HMI notification that vibration levels are trending out of tolerance – accompanied by a suggested corrective action, drawn from past machine learning insights.
In the near future, workers in plants will also be able to use generative AI (genAI) to help manage production eqiupment repair and maintenance logs and records, use voice commands for work orders, along with predictive insights to avoid machine downtime. Tier-1 supplier Dräxlmaier Group is already testing genAI platforms for maintenance in battery system production.
User interface design has similarly advanced. Automotive OEMs and suppliers now deploy user-friendly, multi-modal HMIs – often with touchscreens, gesture inputs, and even voice recognition. These systems are tailored to individual user roles and access levels, helping reduce operator fatigue and training requirements. As the workforce becomes more digitally diverse, HMIs that mirror the UX standards of smartphones and consumer apps are boosting adoption and usability.
Smart factories, smarter roles – HMI in daily operations
HMIs are becoming embedded in the day-to-day operations of production teams and support a range of frontline operations, including assembly guidance, process monitoring, equipment control, and quality verification. On a high-mix assembly line, a worker might begin a shift by logging into a mobile HMI panel to view their workstation setup, confirm changeover completion, and receive step-by-step visual instructions tailored to that day’s vehicle variant.
Meanwhile, the same interface feeds sensor data back to the MES, alerting the operator if there is a deviation in tooling torque settings, sequence, or material flow.
This transition is reshaping the operator’s role. Line workers are no longer limited to reactive, repetitive tasks but are instead positioned as decision-makers, interpreters of real-time production data, and collaborators with automation. For example, when an autonomous guided vehicle (AGV) delivers components to a station, the operator receives a visual cue on the HMI to confirm receipt. If parts are missing or out of sequence, the operator can flag the issue instantly, triggering a process correction upstream.
Similarly, collaborative robots (cobots) working side-by-side with humans rely on intuitive HMIs to coordinate tasks – adjusting speed, pausing motion, or requesting human input through touchscreens, indicator lights, or gesture prompts.
This type of human-machine collaboration is essential for smart factory functionality. As seen in powertrain manufacturer HORSE the project, real-time HMI integration enabled workers and cobots to share task ownership dynamically, with interfaces adapting to user inputs, machine state, and safety protocols. Their use has also led to a reduction in the physical space required for production. “This is because cobots can operate safely alongside human workers without the need for protective barriers or enclosures,” says Antonio Vaz, HORSE’s Chief Process Engineering Officer, “which are typically necessary for traditional industrial robots.”
Omron offers another compelling case of integrated automation. At its demonstration plant, operators, cobots and autonomous mobile robots (AMRs) work in harmony. The AMRs autonomously navigate the production floor, delivering components from injection moulding to assembly stations, while cobots perform tasks like screwdriving and quality checks. HMIs serve as the central command layer, enabling operators to monitor and intervene as needed.
These advances align with a wider transformation in how shopfloor data is visualised, interpreted, and acted upon. Operators are now expected to interact not just with hardware, but with dashboards, decision-support tools, and AI-enhanced controls. The result is a more agile, responsive workforce capable of adapting to complex workflows without compromising speed or quality.
Designing with people in mind - Ergonomics, safety & efficiency
While HMIs serve as digital gateways into the smart factory, their success depends heavily on how well they serve their most important users: the people on the shopfloor. As production environments grow more complex, HMIs must be designed not only for functionality, but for usability, safety, and ergonomics.
One of the most significant developments is the creation of adaptive HMIs that tailor interfaces to individual users. These systems can automatically adjust layout complexity, language settings, visual cues, and levels of interactivity based on the user’s role, experience, and cognitive load.
Safety features integrated into HMI systems have also advanced. Beyond traditional e-stop functions, new HMIs often incorporate vision systems and proximity sensors that feed data into real-time safety alerts. If an operator crosses into a robotic cell unexpectedly, the HMI can trigger a staged shutdown or issue a warning both visually and audibly. This type of machine-human communication reduces reliance on rigid physical barriers and instead uses intelligent awareness to maintain safety.
Ergonomics is another key focus. With many automotive plants embracing wearable tech, hands-free controls, and gesture-based commands, HMIs must now interact seamlessly with smartwatches, AR headsets, or motion capture devices. Systems are being designed to minimise repetitive movements and promote neutral postures, which help reduce fatigue and injury risk over time.
Grupo Antolin is also investing in smart HMI interfaces integrated directly into vehicle interiors. At its Chakan plant in India, the company manufactures Central Touch Control Panels for Tata Motors, combining smart surfaces, capacitive switches, ambient lighting and control electronics. These panels deliver a seamless, intuitive interface experience for drivers—demonstrating how HMI design increasingly blurs the line between factory-floor usability and in-vehicle user experience.
Human-first, data-rich, future-ready
Future HMI systems are expected to be more mobile, intuitive, and personalised, allowing workers to interact with machines and systems wherever they are on the shopfloor.
As systems become more advanced, the focus isn’t just on technology – it’s on making that technology work better for people. Whether it’s wearable devices, AR overlays, or voice commands, the next generation of HMIs will be built around real operator needs. The goal isn’t to replace human workers, but to support them with tools that make the job easier, safer and more efficient.
The shift is already happening. From collaborative robots to AI-enhanced dashboards, automotive factories are building a new kind of partnership between humans and machines – one where data flows both ways, and where people remain at the centre of innovation. HMI will continue to be a key part of that story.