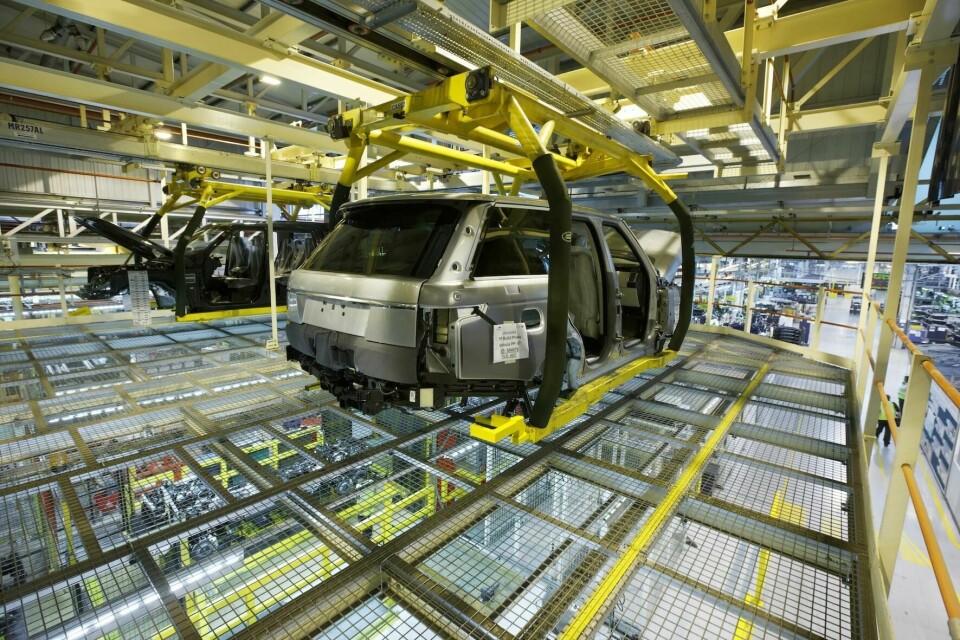
5G networking: How JLR is building smarter factories
As manufacturing operations become more data-driven, traditional network technologies are struggling to keep up. Steve Mason, JLR’s Advanced Digital Technologies Manager for Global Industrial Operations speaks to AMS about the integration of 5G networks into factory environments.
Mason describes the 5G implementation at the Solihull plant as “a bit of a natural evolution,” explaining that the company didn’t set out to adopt 5G for its own sake. “We had a number of challenges,” he says, specifically around the growing number of connected devices, sensors, and mobile technologies like tablets, phones, and vision systems. JLR’s existing Ethernet network was reliable but rigid. “We primarily use Ethernet, but we don’t flood it and every time we want to change something it’s time consuming and expensive to move a network socket up and down the line.”
Attempts to use Wi-Fi had also been unsuccessful. “We’ve had all sorts of issues with signal penetration, AP handoff, number of devices per access point, etc.” Mason explains. These limitations created a bottleneck for JLR’s push towards more agile and data driven operations. “The more data you give to the business, the more operational efficiencies they want to make,” he adds. But the existing infrastructure couldn’t support that pace.
“We have a moving production line… so, a small wifi dropout could, if it was at the wrong time, cause a software download failure”
Steve Mason, JLR
JLR’s journey with 5G began working with Ericsson, on a small proof of concept project in one of its trim and final assembly facilities. “We only did one cell, to prove the technology, and we got quite a lot of learning from that,” Mason explains. The test helped JLR understand how 5G could be deployed as an extension of its existing network, though it wasn’t without challenges – particularly with networking configuration and fixed IP setups.
“There was a lot of challenges trying to find how you configure a 5G DC tool onto a private 5G network,” Mason said. That hands-on experience gave JLR the knowledge it needed to scale the solution.
Today, JLR is deploying 5G more broadly, with Ericsson and Fujitsu as key partners. “The work we’re doing at the Solihull plant is being supported by them.” he says. It’s a collaborative process – a mix of both vendor expertise and internal operational goals.
Importantly, Mason emphasises that the problem wasn’t legacy IT systems, but the limitations of current technologies like Ethernet and Wi-Fi. “Ethernet is basically copper wire, and you have to physically wire it,” which is expensive and time-consuming in a 24/5 production environment. Wi-Fi posed other issues. “We have a moving production line… so, a small dropout could, if it was at the wrong time, cause a software download failure.”
The spectrum congestion in factory environments only made things worse. “Even if you’ve got devices which are not on our Wi-Fi network, the noise they generate just being on that spectrum would cause us issues. Whereas we’ve got a clean spectrum with the 5G,” he explains.
JLR’s primary use case is real-time IoT data ingestion. “Vision systems, for AI, real data-heavy use cases… that’s what we base this around,” Mason says. With 5G’s low latency, high bandwidth, and reliability, the company finally has a wireless solution that suits the complexity and scale of its smart factory ambitions. “This is for us the industrial form of wireless technology that suits the environment we have,” says Mason.
“What they really want is predictive maintenance, prescriptive AI, etc. But that starts with the data and the data starts with the connectivity”
Steve Mason, JLR
Edge computing strategy
Mason makes it clear that the 5G rollout isn’t just about bandwidth. When asked if JLR was increasing its use of sensors and edge devices, he observes “It’s a tenfold increase. We’re on a big journey now of with IoT data ingestion, industrial IoT, etc.”
While 5G is the enabler, the real effort is in deploying edge computing devices at scale – computers that sit in the production environment and process data close to where it’s generated. “We’re deploying edge computers which run our IoT data ingestion platform,” Mason says. “We then have an IT device in an OT space [automation area cabinets, the actual line control PLCs]. Initially that’s for ingesting the IT data, but now it’s got the ability to compute, so we can now consider running AI models on edge.”
That evolution matters because of the scale and complexity of the data involved. With hundreds or thousands of devices on the shop floor, centralised data processing is simply inefficient. “AI gets heavy,” Mason explains. “When you try running all of this in a data centre, there’s still a level of complexity there. So, the ability to start to do some of this computing on the edge devices offers a lot of potential.”
The ultimate goal? Predictive maintenance and condition-based monitoring. “It’s something that all businesses should have had a long time ago,” notes Mason. “What they really want is predictive maintenance, prescriptive AI, etc. But that starts with the data and the data starts with the connectivity.”
To support this, JLR is building a Unified Naming Standard (UNS) to contextualise its sensor data – a key step toward meaningful analytics. “You’re very limited if you haven’t got good data,” says Mason. “Starting with the connectivity, moving into the data, contextualising it, then moving into condition monitoring – and that then really puts us on the journey for all those other technologies.”
The journey hasn’t been quick. The initial 5G trial took place nearly two years ago in a live plant environment. After proving the technology, JLR had to evaluate where the real business value lay.
Today, JLR has active 5G network cores and radio coverage deployed across its Solihull bodyshop. “We’ve deployed the connectivity across the bodyshop in terms of the radio, the data ingestion and connecting the edge devices,” says Mason. The next step is ingesting that data and applying logic to turn it into actionable insight.
That logic will come from a blend of AI and human expertise. “We’re working with the manufacturing teams, with sensor controls, with maintenance to get the insight,” explains Mason. “How do we know when it’s going to fail?” Some off-the-shelf models can help, but much of the knowledge lies in the heads of experienced employees.
Interestingly, many of the sensors already exist. “We’re not really deploying new sensors… they’re already there,” says Mason. The problem is access. “This data is there but it’s essentially wasted if you don’t connect to it.”
Before 5G, accessing it was outdated. “We would do this with USB sticks retrospectively,” Mason admits. “We want to be proactive, preventing a failure.”
With the foundation now in place – connectivity, computing power and a data standard – JLR is well-positioned to make the most of its digital investments. The future isn’t just about having the data but using it to drive decisions in real time.
“We’ve never seen this level of engagement before and this level of wanting to engage with it,” Mason says of the maintenance, manufacturing, and controls teams. “It’s really brought us closer together.”
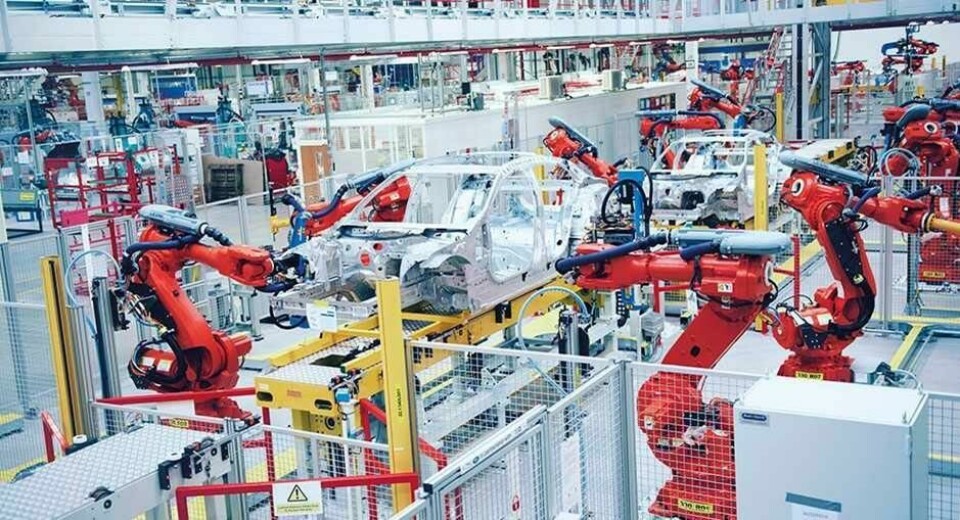
Testing and deployment
JLR began its first full 5G deployment in the bodyshop at its Solihull plant, following a successful proof-of-technology trial in the trim and final assembly area. Mason explains the strategic reasoning behind the choice. “In final assembly there’s so much steel work and people interference factors. It presents the worst scenario to try this technology. So, we were almost trying to make it fail.” Despite those challenges, the test exceeded expectations: “We got 250 meters away from the last access point with a perfectly usable signal. It was incredible.”
The bodyshop was selected for full deployment due to its value and accessibility. “It’s a very high value area when it comes to data… it’s a highly automated area,” notes Mason. This contrasts with final assembly, which involves more manual labour. The goal is to establish a working template in this relatively accessible area before tackling more complex environments like the paintshop, which Mason describes as “a really interesting challenge… five stories high with split levels, huge vats of liquid.”
The 5G system’s software-defined architecture also supports scalability. “It becomes really easy to replicate,” says Mason. “We are getting to grips with this now in terms of setting it up correctly, documenting it correctly, making sure it’s scalable, repeatable and so on. That’s really key.”
5G connectivity and a culture shift
The integration of 5G and edge computing has made an impact reaching beyond technology – it’s changing how teams work and think. According to Mason, the increased data access and insight have created a new level of collaboration between technical teams.
“We’ve never seen this level of engagement before and this level of wanting to engage with it,” Mason says of the maintenance, manufacturing, and controls teams. “It’s really brought us closer together.” While digital transformation is often framed as a technical upgrade, Mason describes this as a convergence of IT and OT – not just systems, but people.
Traditionally, preventative maintenance routines at JLR were time-based – tasks were done at fixed intervals regardless of actual need. Now, with access to real-time, sensor-driven data, those routines are shifting toward intelligence-based scheduling.
The benefits extend beyond just saving time. With predictive analytics, teams can focus on areas that have the most impact on production. “The intelligence can tell you where your efforts are best spent,” says Mason. For example, understanding which faults would unlock the most vehicle throughput helps prioritise resources and improve efficiency.
It also helps prevent major failures, which can be severely disruptive to production operations and output. “A drive failing that runs the production line… the outage there is absolutely enormous,” notes Mason. But now, some of those critical failures can be predicted, and while repairs may still require downtime, they can be managed and planned more effectively.
It’s clear to see that the implementation of the 5G network has boosted JLR’s data gathering and management capabilities, going a long way to improving efficiency and reducing downtime. What’s also significant is how this transformation is changing mindsets. This shift is empowering frontline teams to become more proactive, data-driven, and aligned with broader business objectives.