Operators, cobots and mobile robots work in harmony
How introducing autonomous mobile robots and collaborative robots, manufactured and supplied by Omron, can help achieve a modernised and more sustainable factory
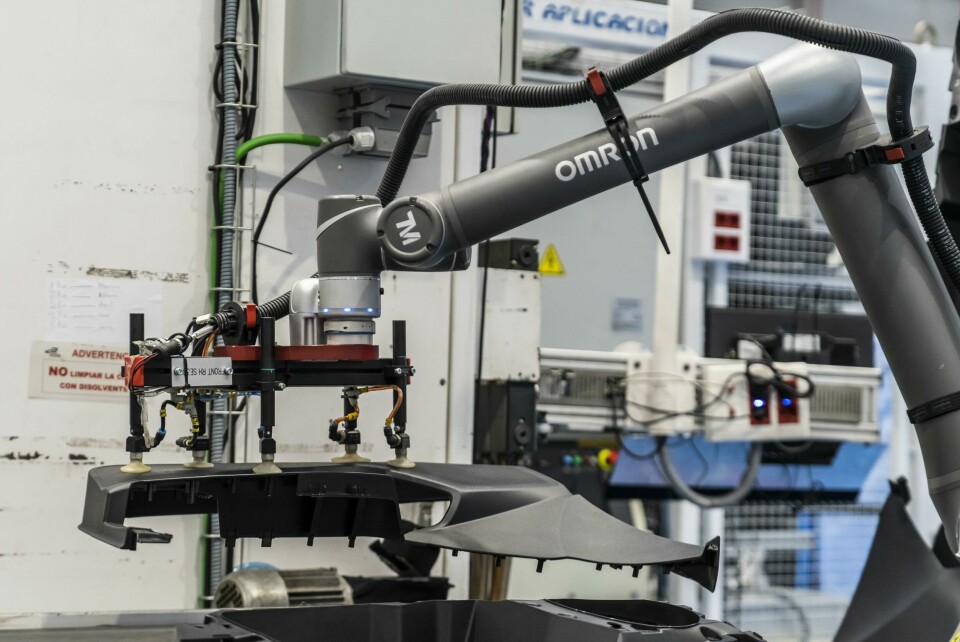
Major trends in the automotive industry – including an increasing emphasis on issues such as electrification, digitalisation, and sustainability – are also driving changes in vehicle interiors. One of the largest international players in this sector is Grupo Antolin. As a key player in the global automotive supply chain and a high value manufacturing leader, the strategy of the company, Adv. Manufacturing 4.0, looks into integration of digital technology in the operations.
One of the focus areas is the reduction and optimisation of movements in internal logistics. Introducing autonomous mobile robots (AMRs) and collaborative robots (cobots), manufactured and supplied by Omron helps achieve a modernised and more sustainable factory where people and machines are working in harmony.
Grupo Antolin is a global supplier of technological solutions for automotive interiors. The company supplies the world’s leading car manufacturers through 145 factories in 26 countries. The company’s operations cover the complete component cycle - from concept and design through to development and delivery. It offers high added value products via four Business Units: Overheads, Cockpits & Doors, Lighting & HMI (Human Machine Interface), and Electronic Systems.
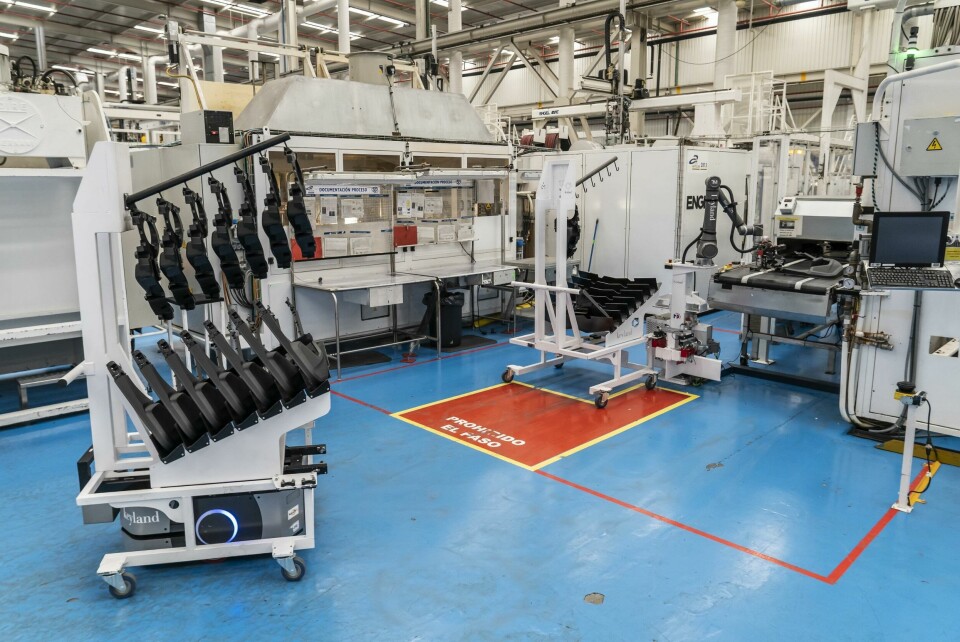
Changing needs
Since 2001, Aragusa, one of Grupo Antolin’s plants in Burgos, has pioneered the manufacture of auto interior parts, which can be used in a wide range of OEMs. Until recently, tasks such as loading and transporting car interior components from the injection area to the assembly area were carried out manually.
However, to keep pace with global changes, continuous improvement, and digital strategy, Antolin looked for an improvement and efficiency of processes and wanted to automate such procedures, which in turn would help it to develop a more sustainable business model. This would also free up employees to work on high-value production processes.
The company chose Omron and a system integrator to supply the hardware and software solution needed. The system integrator is owned by Grupo Antolin and is a technology consultancy dedicated to the optimisation, development, innovation and implementation of technological processes and solutions for industrial companies.
The new autonomous automatic transport solution needed to replace the manual processes. One of the key criteria was overall equipment effectiveness (OEE). Making a positive contribution to the OEE of the injection and assembly systems.
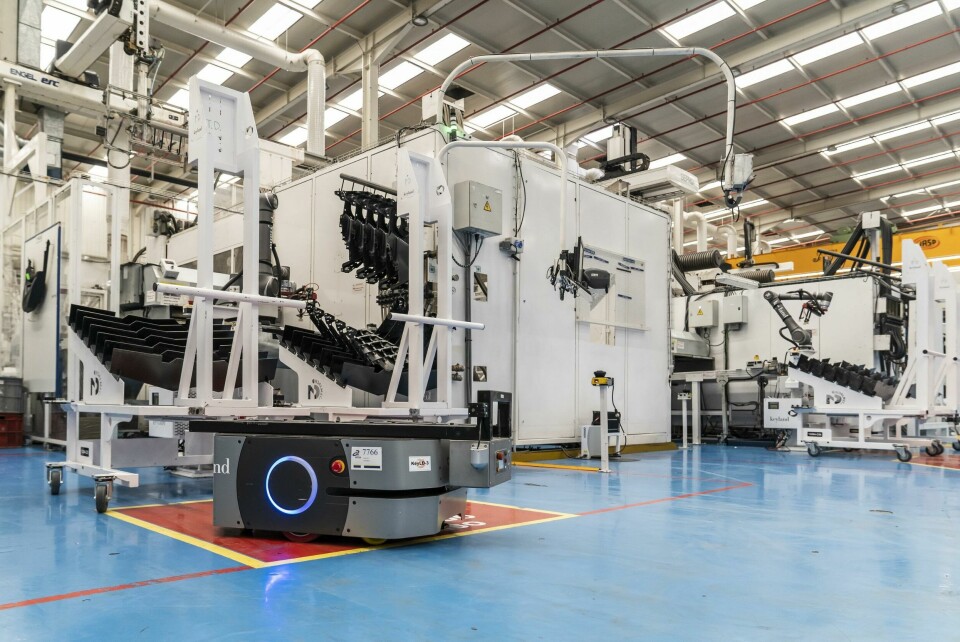
Choosing and developing the solution
Jaime Ruiz Alonso, engineering manager plant in Grupo Antolin, explains: “When we were looking for a solution, it was vital to select the right automation solution with integrated robotics; something that would be scalable and flexible; and robots that could work safely in closer proximity with people in harmony. In terms of a supplier, we wanted a company that could provide both the AMRs and the cobots (along with integrated vision systems) and would become involved with the whole project. Omron filled all these needs.”
The new solution was based around Omron LD-250 AMRs and Omron TM12 cobots. The LD-250 is fully autonomous and has been designed to dramatically increase productivity in manufacturing and logistics operations. It achieves this by increasing throughput, eliminating errors, and improving material traceability. The AMR has a maximum payload of 250kg. Unlike a traditional autonomous guided vehicle (AGV), Omron’s AMRs navigate by the natural features of a facility and do not need any expensive facility modifications.
The Omron TM12 is a collaborative robot designed specifically for assembly, packaging, inspection, and logistics applications. It has an integrated vision system that provides additional functionality and flexibility through colour, object, and pattern recognition.
Grupo Antolin had already been working with vision systems from Omron with good results. Omron could supply the level of support that the company needed for the new project and had a good understanding of Grupo Antolin’s needs.
Refining the solution
Prior to installing the new solution, there was a manual movement of components between injection and assembly. These processes are now carried out by the cobots and AMRs. Security lasers enable the cobot to work at high speeds, with no need for physical fences, adding the maximum safety levels between operators and robots to work collaboratively and increasing productivity.
On the other hand, the fleet manager software controls and naturally manages the traffic between the AMRs and allows the number of AMRs to be increased easily in the future if necessary.
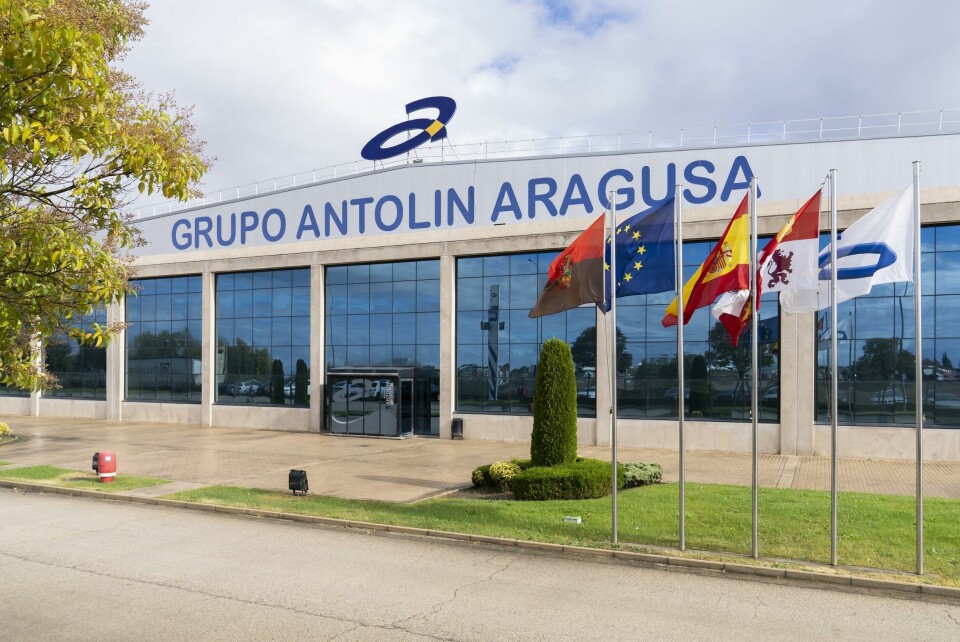
Meeting the customer’s needs
Jose Antonio Baquedano, automotive key account manager in Omron, says: “This flexible robotics solution is a fantastic example of how we bring innovation through automation to solve issues in the production environment to meet customer needs.”
Jaime Ruiz Alonso engineering manager plant in Grupo Antolin responds: “Omron has been very proactive in ensuring that the project was a complete success. The coexistence between the cobots and the AMRs makes the new system completely independent, seamlessly connecting the injection area to the assembly area. We have therefore achieved the desired result – an autonomous system that achieves the same aim as the previous, labour-intensive solution.”
Alonso concludes: “We enrich our ecosystem to develop the manufacturing 4.0 strategy. This can be done by reducing low value activities and by increasing safety at workplace level.”