As OEMs increasingly explore the use of additive manufacturing in production AMS looks at its unique advantages
The 2014 Chevrolet Malibu from General Motors boasts several neat features intended to increase driver and passenger convenience as well as vehicle appearance and performance. On the former count, there is a redesigned centre console with sculpted recesses for mobile phone storage and front seat backs that give rear passengers more legroom. On the latter, there is a restyled, aerodynamic lower grille for the front fascia in which black grille textures are offset by a chrome surround.
Something which all these features have in common is that rapid prototyping, using an additive manufacturing technique, played a key role in their development. As confirmed by David Bolognino, director of the GM design fabrication operation based in Warren, Michigan, the technique is used in all GM vehicle development projects, taking place “24 hours a day, seven days a week”.
The facility at Warren is the location not just for the company’s Global Design Center, but also for Design Center Fabrication, a key integrated operation that uses additive manufacturing to support vehicle development. This involves 18 additive manufacturing machines, 12 of which use the stereolithography (SLA) technique in which a laser creates parts layer by layer, by curing a liquid resin. The other six employ the selective laser sintering (SLS) technique in which a laser fuses successive layers of dry powder into a final polymer-like form. All of the equipment comes from a single supplier, US-based 3D Systems.
Most of the dozen staff at the fabrication centre are trained craft workers rather than graduate engineers, many with woodworking qualifications. “They have good spatial abilities,” Bolognino explains. Such traditional skills come in useful. Although the additive machines are programmed with 3D modelling data generated by a Siemens PLM NX CAD system, particularly large fabrications may be produced by manually glueing together a number of additively manufactured parts.
Bolognino suggests that no areas remain off limits. “We have made absolutely everything,” he confirms. The most intensive area for additive parts is now prototype testing rather than aesthetic evaluation. This testing may be static but is increasingly likely to involve prototype vehicles. Bolognino identifies growth in the use of additive parts in test-track vehicles as the “single largest” advance in the company’s deployment of additive parts over the last five to six years.
A major facilitator of that development has been the availability of additive parts with enough physical resilience to be used in such practical applications. At the moment, says Bolgnino, GM’s SLA operations use three grades of material and its SLS activities two. In each case, one of the grades is a tough, ABS-like formulation able to withstand the rigours of a test vehicle, while the others are less robust, but also less expensive variants suitable for laboratory test procedures. In the latter, Bolgnino points out that additive parts have not supplanted traditional clay modelling but supplement it by providing extra realism.
Since additive parts are derived from the primary design database and are therefore accurate representations of design intent, they can also be used in isolation for highly specific test routines. Bolognino cites wind tunnel testing for aerodynamic performance as one arena in which GM now routinely uses additive parts.
Significantly, Bolognino says he currently cannot foresee any obvious end point for GM’s use of the technology, though as a high-volume manufacturer, he concedes it is unlikely that the company will make substantial use of it any time soon for production vehicles.
From prototyping to production
Nevertheless, additive techniques do seem to be on the cusp of making the transition from prototyping to production operations. Confirming this is Terry Wohlers, founder of US-based Wohlers Associates, which publishes an annual report on developments in additive manufacturing technologies and the state of the market.
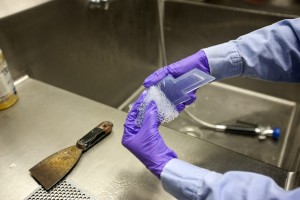
As Wohlers explains, one of the fundamental advantages that additive techniques offer is that they are free of the constraints on component geometry that are imposed by requirements to release parts from moulds, or to allow machine tool cutting heads access to the interior. This makes it feasible to produce unitary parts with optimal use of materials that are light and strong, offering payback throughout the life of the vehicle via reduced running costs.
The question is, how far can additive manufacturing go as a means of making major body sections of cars? How far in the future is the first car with a visible surface almost entirely made by additive means? Those are not quite different ways of asking the same question. [sam_ad id=17 codes='true']
Although the answer to the first is yet to be determined, the answer to the second is rather more definite: a one-off demonstrator vehicle has already been produced.
The vehicle in question is the Urbee, a low-slung, two-seater urban car which was designed by engineering consultancy KOR EcoLogic in Winnipeg, Canada, in a quest to make a vehicle that would use the ‘least energy possible’ when driven. Part of that remit is fulfilled by its power source (the ‘ee’ in ‘Urbee’ stands for ‘electric with ethanol back-up’), but as president and senior designer for the company Jim Kor confirms, additive manufacturing has played a key role. It also forms a major part of plans to develop the concept even further.
Making the Urbee
Kor explains that the first Urbee came into existence roughly three years ago in a project that cost around $1m. The car has a metal chassis which supports a tubular framework to provide driver protection “like a NASCAR vehicle”, but otherwise all of the external structure above the chassis was made in ABS using the fused deposition modelling (FDM) additive technique. Production of the FDM parts was carried out by equipment supplier Stratasys through its RedEye manufacturing service.
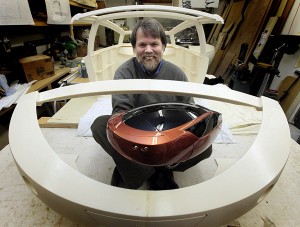
Nevertheless, the use of additive techniques was not initially envisaged by the project team. According to Kor, the original plan after physical scale modelling in clay and digital aerodynamic testing was to build the vehicle from fibreglass panels, but it was soon realised that the lead times would be too long. A manually intensive process would have taken two people at least eight months, while CNC milling driven by the CAD database might still have required three months.
After the EcoLogic team made contact with Stratasys to discuss the possibility of an additive approach, it became evident that the timescale could be compressed. Once the first files derived from the team’s AutoDesk Inventor 3D modelling software were sent to Stratasys, only a few weeks elapsed before the first physical panels were delivered for assembly. The finished car has now been driven, although mostly on test-tracks.
Kor’s thoughts have turned to more ambitious plans. The latest idea is to build a second car and drive it on the highways between New York and San Francisco using only a single tank of pure ethanol fuel. As Kor points out, that particular route has a symbolic significance for the US automotive industry since it was the one travelled in 1903 in the first coast-to-coast car journey across North America.
As yet there is no timetable for the venture, though Kor hopes work will get underway fairly soon. The team intends the new project to represent an advance over the first in terms of both design and manufacture. Kor says the design software will be the Alias system that is used as the tool for vehicle surface modelling by several major OEMs, while a minimum of 50-60% of the vehicle will be built using additive techniques and the complexity of the parts concerned will also be significantly greater.
Kor envisages that the body panels will not just be shaped sheets, as in the first vehicle, but will also incorporate structural elements such as air ducts. Additionally, in order to maximise weight savings, he wants to fabricate the internal structures of elements such as bumpers in a much more economical and targeted fashion than before, with material used “only where necessary”. Kor is confident that the approach is one that can and will eventually make it into production vehicles.
FDM & polyjet methods
Kor is by no means an isolated visionary for additive manufacturing in the automotive industry. Another believer is Jeff Hanson, business development manager for the Stratasys RedEye service in Minneapolis. The organisation currently comprises around 170 globally dispersed additive systems providing contract services to a wide range of clients, including automotive OEMs and tier one and two suppliers.
Most of those companies use FDM technology, says Hanson, though a minority opt for the polyjet method that was originally developed by Israeli company Objet, with which Stratasys merged in 2012.
As Hanson explains, FDM uses a ‘glue gun’ technique to apply a thermoplastic material, meaning that the items it produces are similar to those made by injection moulding. By contrast, the polyjet technique sprays a photopolymer liquid, in the same manner as an inkjet printer, which is then cured with ultraviolet light.
Both methods have their advantages, but Hanson attributes the predominance of FDM to its ability to allow development and prototyping work to be carried out with a material likely to be similar to that of the actual part, whether or not the final manufacturing is additive.
Hanson confirms that most additive manufacturing by OEMs seems to be for prototype parts used in crash test and pre-production vehicles. The key advantage can be summarised in a single word: flexibility. As Hanson explains, the overwhelming advantage provided by additive techniques at the prototyping stage is that they avoid the time and expense required for the machining of ‘hard’ tooling in which parts are moulded or pressed.
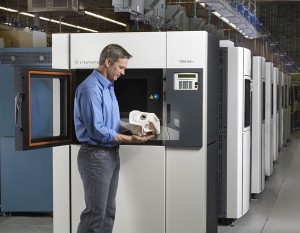
Hanson is confident that the current use of additive manufacturing will expand to include production vehicles as a matter of routine. Just how this will happen is another matter.
Hanson says that three key variables are involved – “part size, complexity and production volumes” – and that the way they interact makes it difficult to speculate on the point at which an additive technique might make sense financially. At the moment, he says that while a requirement for part volumes in a few dozen would tilt the balance in favour of additive manufacturing, one where it is 10,000 or more would not.
Ultimately, Hanson believes the real issue that will govern the progress of additive techniques as a means of manufacturing final parts will not be one of immediate production costs. Instead it will be the growth of an appreciation amongst OEMs and tier one suppliers of the potential for much more efficient use of materials, particularly in ‘lightweighting’, which could offer significant cost-savings over the vehicle lifetime. In other words, the further take-up of additive manufacturing is as much a design as a production issue.
In this respect, Hanson echoes the views of Jim Kor. For example, he observes that parts intended for final production by additive techniques can dispense with the supporting ribs in conventional, moulded parts. Asked if there is a wide appreciation of this capability within the automotive industry, his answer is an unequivocal “no”.
Nevertheless, Hanson believes that an appropriate understanding will develop and is confident that a realistic future scenario is one in which additive manufacturing systems are co-located with vehicle assembly lines, supplying parts directly to build operations – perhaps “within five years”.
* Click here for the Wohlers Associates annual report.