Cold forming is experiencing a resurgence in the automotive industry and it is a trend that is likely to continue — so what are the advantages?
Today, some car manufacturers are using a high amount of hot forming steels in their vehicles, while other automotive companies are almost exclusively relying on the cold forming production method. One of the reasons for the trend towards cold forming is that more and more companies are realising that hot forming is a costly process and less favourable from a sustainability perspective. For years, hot forming steels flourished in the automotive industry simply because there was not a cold formable range of steels with the right properties. Times are changing and more cold forming steels have been developed that can live up to the high strength and geometric demands of modern automotive applications. As these steels become available the trend towards cold forming is likely to continue. By learning how to best design an application for cold forming, these companies will have a competitive cost advantage.
Compelling advantagesSo what are the advantages of cold forming steel? To begin with, cold forming steels are easier to weld and join due to leaner alloy composition. Furthermore, the fact that they are easier to weld means that some challenges with different kinds of embrittlement can be avoided with cold formed applications.
Without the need for energy intensive heating processes used for hot forming steels, cold forming steels are also a more environmentally friendly alternative. In contrast to hot forming, cold forming is a method that can be turned on and off without any issues. While the hot forming method works best when running 24/7, the cold forming setup can be utilised when needed. Finally, the main advantage with cold forming compared to hot forming is the difference in processing costs, including tooling costs, productivity, energy consumption and the need for more expensive laser trimming when hot forming is used.The 3rd Generation of AHSSCurrently, there are many Docol steels from SSAB that meet the automotive industry demands of high strength and formability for cold forming materials. However, the development of many more are planned for the future. We call them 3rd generation AHSS and they will reduce the need for hot forming. In addition, SSAB can also contribute to the automotive industry with our extensive knowledge and experience with cold forming steels. By helping our customers determine the best way to use them, there is a huge potential for further upgrades without having to use press-hardening, which is more expensive.
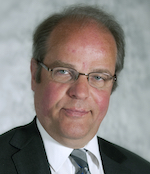
50% Docol in future carsIs it possible that in the future, 40–50% of a car’s body weight could be made from cold formable Docol steel? If so, how would the car compare to one built with other materials – in terms of emissions and recyclability? Kennet Olsson, business development specialist at SSAB, explains: “Really high strength steel should be used where it makes sense in a car. If a car body were to be made up mostly of cold formable Docol, with component innovations that match the properties of the steel, we can expect a vehicle that will obtain high crash test ratings while also being lightweight. Fuel consumption and emissions will decrease as a result and since steel is 100% recyclable, more of the car could be repurposed at the end of its lifecycle.”
Cost effective lightweight design helps sustainabilityNew, innovative advanced high-strength steel (AHSS) types are successfully reinventing themselves to help the industry. By increasing the share of AHSS steel in components, car manufacturers can both lower vehicle weight and increase the percentage of recyclable parts. Advanced high-strength steels, such as Docol, help improve fuel economy and reduce greenhouse gas emissions at little or no extra cost to manufacturers or consumers. In fact, using AHSS for selected applications will cost you only a third of the price of aluminium. Docol’s high strength-to-weight ratio means that thinner steel can be used without sacrificing strength, so you can significantly cut weight, boost fuel efficiency, improve driving performance and cut your costs.