AMS considera os desafios de responder a elevado volume de saída e de qualidade de demandas em operações de fresamento
Fornecimento de peças fabricadas para os setores automotivo traz um conjunto único de desafios, em grande parte devido à combinação de volumes de produção elevados e exigências de qualidade meticulosas. O problema é exacerbado em operações de fresagem pela natureza prismática da fabricação. Aqui, apenas máquinas cuidadosamente considerando dispositivos e ferramentas podem fornecer a receita para autopeças produzidas com sucesso.
Um caso em questão pode ser visto na fábrica Welshpool, Reino Unido diecaster de alumínio, CastAlum, que começou agregando valor aos seus produtos por mecanização de peças fundidas. O desenvolvimento foi desencadeado pela adjudicação de dois importantes contratos automotivos de longo prazo para o fornecimento de caixas de engrenagem de direção mecanizada e cárter de caixas de velocidade.
Os volumes de produção previstos a partir dos dois novos contratos, que este ano terá a máquina CastAlum fazendo 700.000 peças fundidas, garantido a consideração de uma linha de transferência. No entanto, a empresa diz que teria sido difícil de se adaptar às mudanças dos componentes automotivos no futuro. A linha de transferência também significaria um investimento substancial antes que os volumes tivessem melhorado.
Instalação progressiva de HMCs
A compra sequenciada de paletes gêmeos, centros de mecanização horizontais de quatro eixos (SGUM) foi considerada a resposta, uma vez que elas poderiam ser instaladas progressivamente para atender ao aumento da produtividade e são fáceis de reconfigurar para quase qualquer componente. CastAlum optou por modelos Heller H2000 em combinação com ferramentas fornecidas pelo Mapal, que audita armários de ferramentas de CastAlum duas vezes por semana para garantir disponibilidade contínua.
Hoje, um total de 10 H2000 HMCs preenchem a sala principal de produção em Welshpool. Cada máquina é capaz de qualquer tipo de produção de caixa de direção ou cárter de transmissão em duas operações, proporcionando flexibilidade de fabricação. Guindastes posicionado entre cada duas máquinas permite que os acessórios sejam mudados rapidamente.
Fundição chega em uma longa linha em forma de U, passado por todos os H2000s, criando um ambiente de fabricação enxuta em um espaço apertado. Cada transportador tem um chip que identifica o tipo de fundição e a máquina de destino pretendido, desviando automaticamente as peças vazadas nas áreas de amortecimento de ambos os lados da linha, o que permite o acesso do operador.
A fundição em bruto é carregada manualmente em um dispositivo elétrico em uma segunda máquina pronta para a primeira operação, uma parte totalmente descarregada e um componente parte mecanizado foi transferido para outro dispositivo elétrico para a segunda operação. Ambas as operações são realizadas em dois componentes diferentes por palete de cada vez. Assim depois de um índice de paleta, uma fundição de acabamento fabricado sai e é enviada através do transportador para o departamento de inspeção, e para o despacho.
"Os centros de mecanização Heller têm um tempo de em média 95%, o que é muito elevado para máquinas twin-paletes carregadas manualmente", diz Keith Brown, diretor-gerente da CastAlum. "É devido à apresentação eficiente de material para o segundo palete e de lá para os eixos, o que minimiza os tempos de troca. As máquinas trabalham o dia inteiro, seis dias por semana, mantendo tolerâncias de até 10µm com uma capacidade de processo de 1.67Cpk".
Reduzindo o tempo de transferência
Outro fabricante subcontrato do Reino Unido, BCW Engenharia de Burnley, também suporta uma preferência aparentemente crescente de centros de usinagem do eixo horizontal. A empresa investiu recentemente em uma Okuma MB5000H HMC com um conjunto de 10 paletes para adicionar capacidade de produção de precisão de componentes automotivos.
"A redução que estamos vendo em tempos de produção é, em parte devido ao fato de ser capaz de apresentar um componente sobre o palete ao fuso mais rapidamente, uma vez que sai do conjunto de paletes já em seu suporte, de modo que a configuração não atrase o início do o próximo ciclo", explica o diretor de engenharia do grupo, Tony Kilfoyle. "Mudança é, portanto, limitada ao tempo de troca de paletes automático, que não é mais do que 35 segundos. Uma vez que a peça está sendo mecanizada, o ciclo também é mais rápido porque o tempo ocioso são curtos devido aos 60m/min nos eixos lineares e 2.5 segundo de troca de ferramenta. Além disso, os elementos de corte do ciclo são mais curtos, uma vez que a remoção de metais é rápida com o fuso de 15.000 rpm."
"O nível de qualidade e grau de inovação é extremamente elevado nesta indústria, por isso devemos manter o ritmo de uma perspectiva de produção, a fim de manter a competitividade" – Thomas Kaiser, Kaiser Werkzeugbau
Grandes reduções em tempos de mecanização são evidentes em muitas peças automotivas produzidas na célula no BCW para clientes como Jaguar Land Rover, Ford e Aston Martin. O subcontratado é um fornecedor de primeira linha para muitos deles, desenvolvendo e fornecendo protótipos, bem como fornecendo componentes de produção para horários apertados.
Kilfoyle aponta que mais de 70 máquinas-ferramentas do BCW são centros de produção que trabalham duro e que funcionam 24 horas por dia. Como resultado, a empresa procura robustez de construção, não só da estrutura, mas também do sistema de entrega de fuso, trocador de ferramentas, eixo de rotação e refrigeração. Esses itens, em particular, podem causar problemas em um HMC, mas diz que o BCW MB5000H foi classificado mais alto de todas as máquinas pré-selecionadas por sua fiabilidade funcional e agora padronizará em Okuma para todas as compras futuras HMC.
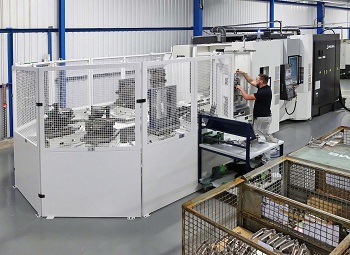
Uma abordagem modular
A alternativa para HMCs, ao que parece, é tomar uma abordagem mais modular usando vários eixos simultaneamente. Centros de maquinagem modulares, tais como o Mikron multipasso XT-200, por exemplo, definem a produção de peças prismáticas em um único aperto com tempos curtos de frabricação de cavaco, tipicamente menos de 1 segundo. Além disso, o sistema pode ser refeito em apenas alguns minutos, com um máximo de quatro eixos de usinagem em uso ao mesmo tempo.
O resultado é um custo menor por peça, em cerca de 35% no caso de um fabricante alemão, que produz 500 mil carcaças de turbocompressores em cinco variantes diferentes a cada ano.
O tamanho dos lotes das carcaças de turbocompressores variam entre 500 e 10.000. Como resultado, os operadores de máquina tem que reequipar a intervalos frequentes. Com as máquinas anteriores, este costumava levar 80 minutos, mas hoje, com a de várias etapas XT-200, 20 minutos é suficiente. Além disso, havia anteriormente 12 funcionários que operavam quatro máquinas em uma área de 300m². As máquinas eram centros de usinagem multi-fuso e tornos automáticos, e peças tiveram que ser presas duas vezes. Agora, a empresa alemã produz casings do turbocompressor com apenas seis funcionários e duas máquinas em metade do espaço. Todos esses fatores têm ajudado a diminuir o custo por peça em 35%.
Os múltiplos passos XT-200 de máquinas de turbocompressor caixas em lados cinco e meia em uma configuração. Dependendo da variante, entre 30 e 40 passos de usinagem, como torneamento, fresamento e furação, são necessárias, com uma tolerância de ± 25 um e uma capacidade de processo de 1.67Cpk. De acordo com Mikron, outras aplicações de sucesso desta tecnologia incluem sistemas ABS, rotores do turbocompressor, porta-bicos para sistemas de injeção de ferrovia comum, carcaças de bombas hidráulicas e dissipadores de calor.
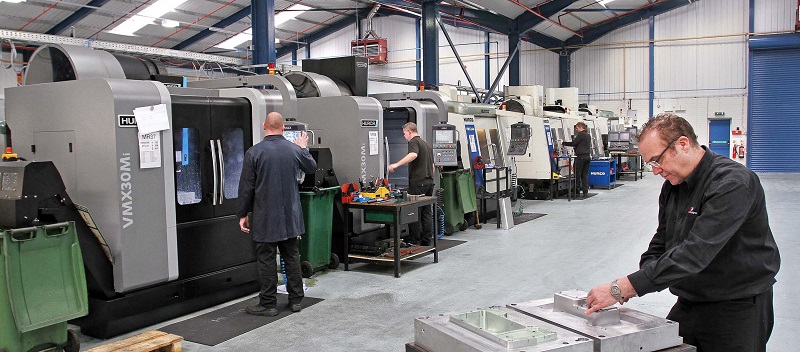
Fidelidade à marca
A empresa optou por Hurco no início devido à rigidez das máquinas, que ela acreditava que asseguraria uma estreita tolerância de aços de ferramenta para conseguir um bom acabamento de superfície e minimizar polimento manual. Claro, permanecendo fiel a uma marca de máquina e controle tem a vantagem adicional de que qualquer dos operadores da empresa podem usar qualquer centro de usinagem e de trabalho podendo ser trocados entre eles sem problemas. Todos estão em rede com sistemas CADCAM mais de 10 quilômetros de cabeamento na fábrica.
Há uma carteira de encomendas de seis semanas para moldes em RP Technologies com cerca de duas dezenas progredindo através do departamento de fabricação de ferramentas, em qualquer altura, e isso tende a aumentar ainda mais. Existe espaço para mais 20 Hurco VMCs na fábrica e é provável que alguns dos próximos modelos serão maiores máquinas de cinco eixos para expandir o escopo de RP Technologies para trabalho mecânico de cinco lados e profiling interpolativo de superfícies 3D.
Algumas milhas a leste, a instalação de fabricação de ferramentas de Birmingham Elkington Brothers, é outro beneficiário da tecnologia de moagem Hurco. A empresa adicionou duas máquinas extras Hurco nos últimos 18 meses, ambas oferecendo velocidades de trabalho mecânico mais altos e melhor acabamento superficial. Diretor-gerente James Kelly está procurando agora adquirir primeira máquina contínua de cinco eixos da empresa, depois de muitos anos de operação de equipamentos 3 + 2.
Tempos de cálculo mais rápidos
A empresa produz diversos tipos de ferramentas, incluindo padrões, peças e acessórios. Quase 90% do trabalho é para a indústria automotiva, incluindo muitos RIM (moldagem por injeção de reação) ferramentas para produzir soleiras, pára-choques e spoilers.
As máquinas em Elkington Brothers são executados em conjunto com software CAM PowerMill de Delcam, o que ajudou a empresa a ajustar-se a um aumento de trabalho resultante dos grandes investimentos feitos pela Jaguar Land Rover na região. De acordo com Kelly, os tempos de cálculo mais rápidos de PowerMill term contribuído para substancial economia de tempo: um projeto como uma ferramenta de moagem para um headliner costumava a levar 24 semanas, mas isto agora é até seis semanas.

Com sede na Alemanha Helferskirchen, Kaiser Werkzeugbau está usando 17 máquinas-ferramentas fornecidas pela DMG Mori para ajudá-la a entregar peças para projetos de alto perfil motosport, incluindo o Porsche 919 híbrido na classe LMP1 do World Endurance Championship (WEC).
"Quanto mais sofisticada é um componente, mais ele se enquadra na nossa gama de serviços", diz Thomas Kaiser, proprietário da empresa e diretor-gerente. "O nível de qualidade e grau de inovação é extremamente elevado nesta indústria, por isso devemos manter o ritmo de uma perspectiva de produção, a fim de manter a competitividade."
Cerca de 70% dos produtos Kaiser WERKZEUGBAU são destinados para a pista de corrida, com o restante compreendendo pedidos de repetição de peças de protótipo automotivo. No que diz respeito ao Porsche 919 híbrido, a empresa fabrica uma variedade de componentes mecânicos.
"A partir da câmara de disco de freio de componentes para a direção, e de motores de peças estruturais, podemos construir quase todas as peças essenciais de um carro de corrida", diz o gerente de vendas Ragnar Bregler. "Devido à alta complexidade, o foco está em soluções produtivas como a tecnologia de fabricação de cinco eixos. Quanto menos afinações necessárias, mais eficiente e, acima de tudo, o nosso trabalho pode ser preciso. Porsche está colocando muita energia neste projeto e está contando com fornecedores de confiança ".
Entre as mais recentes aquisições estão dois centros de maquinagem Mori DMG DMU Evo, enquanto que no futuro próximo a empresa está procurando adicionar uma máquina de moagem de alta velocidade HSC 70 linear a partir do mesmo fornecedor.