AMS inspeciona os mais recentes desenvolvimentos tecnológicos impulsionando o controle de qualidade e monitoramento de processos de soldagem
Soldadura de ponto é um processo mais comumente aplicado para unir chapas finas em estruturas corporais automotoras, com um carro da família típico contendo até 5.000 pontos de solda. No entanto, um aspecto do processo de soldadura por pontos, que não é rigorosamente controlado é o desgaste das pontas dos elétrodos. Durante a soldagem, a tensão mecânica e difusão térmica causam abrasão contínua para as frentes das pontas de soldagem. Por sua vez, o tempo de vida operacional das pontas de soldadura afetam diretamente a qualidade de fabricação.
Aços revestidos de zinco são o material de carroceria de carro mais popular, mas zinco degrada rapidamente o eletrodo até o ponto em que é necessária a manutenção para garantir a qualidade da solda adequada. Desgaste do eletrodo pode ser reparado através de uma técnica conhecida como "ponta vestida", onde um cortador mecânico remove material da face de ponta, reparando assim qualquer dano e retornando a ponta a partir de sua geometria ideal.
Hoje quase todas as linhas de solda a ponto modernos automotivos executam produção de ponta automatizado, mas esses sistemas não oferecem uma solução completa e problemas com qualidade de ponta do eletrodo permanecem a causa número um de paradas nas linhas de produção de automóveis. Além disso, ponta convencionais removem uma grande quantidade de material, resultando no consumo rápido dos elétrodos caros de cobre.
Entre as mais recentes inovações para combater qualidade ponta do eletrodo está SmartDress, o resultado de um projeto de investigação europeu de dois anos envolvendo três institutos de pesquisa e quatro empresas: Fraunhofer IMPS (Alemanha); Instituto de Soldadura (Reino Unido); Teknologian Tutkimuskeskus (Finlândia); Sinterleghe (Itália); Acabamento Aids & Tools (Reino Unido); Software Swantec & Engineering (Dinamarca); Fisher e Smith (Reino Unido).
O terceiro elemento do sistema é uma cômoda mecânica projetada para minimizar a remoção de cobre durante a ponta, e o elemento final é um trocador de ponta automatizado capaz de substituir pontas desgastadas durante a produção sem a necessidade de uma parada de linha e de intervenção manual.
Em termos de função do sensor, uma avaliação da condição de soldagem de ponta requer vistas de frente e de lado. A vista frontal fornece informações sobre a coloração da frente de ponta, o que é necessária para decidir sobre o tipo de procedimento. Entretanto, a vista lateral apresenta o diâmetro da parte dianteira da ponta e o comprimento do elétrodo. A informação de ambas as vistas são usadas para decidir sobre a necessidade de um corte de contorno ou, se o comprimento do eletrodo restante for pequeno, em uma troca.
Comprimento de onda de iluminação
Para os vários materiais em folha usados no processo de soldadura, são observados tipos específicos de coloração. Portanto, o comprimento de onda de iluminação deve ser ajustado para a aplicação particular. Estas são escolhidas para coincidir com a absorção ou propriedades reflectoras do material respectivo, que se aglomeram a superfície frontal corada.
Para chapa de aço, luz vermelha é usada (absorção do contaminante), enquanto que para as folhas de alumínio luz azul é utilizada (reflexão do contaminante) como uma iluminação difusa. O sensor é construído de modo que a pistola de soldagem trave no lugar e os eletrodos de ambos os lados serão medidos simultaneamente em ambos os pontos de vista. Dependendo do projeto, três ou quatro câmeras são obrigados a fazer isso, cada uma para a visão lateral e um ou dois para a vista frontal.
Michael Leuckefeld, gerente de projetos da Fraunhofer IPMS, diz: "Os nossos monitoram o sistema tanto do ponto eletrodos superiores e inferiores de solda simultaneamente a partir de várias perspectivas. Usamos difusa monocromático LED de iluminação gerada pelo vidro opala para esta finalidade. A luz é enviado ao elétrodo através de uma disposição de espelho e o divisor de feixe, e, em seguida, de volta para o detector de foto. Iluminação e gravação de imagem, portanto, utilizam os mesmos elementos de óptica".
Otimização da produção
Pareto analisa e mostra todo o potencial para a otimização da produção. Os parâmetros para inspeção de qualidade podem ser ajustados durante o processo de produção e são aplicados automaticamente para o próximo ciclo do sistema, minimizando o retrabalho e desperdícios. Além disso, 100% de inspeção garante que as peças só são admitidas aos processos de fabricação a jusante se eles estiverem livres de defeitos.
Durante o processo de configuração do software, todos os parâmetros relevantes, como a inspeção de procedimentos, limites e critérios, são configurados de acordo com os requisitos específicos de produção. A empresa diz que seu sistema VIRO-WSI é também menor do que a unidade de geração anterior, enquanto o consumo de energia foi reduzido em 75%.
Mantendo o tema da costura, Meta Vision Systems lançou recentemente o seu SLS (Smart Laser Sensor) ARC para aplicações de soldagem a arco robóticos. É apropriado para a constatação de costura e rastreamento em tempo real de costura de solda em todos os processos de soldagem usuais, incluindo alta GMAW atual e FCAW.
Steve Thacker, gerente geral da Meta, diz: "Meta saiu da Universidade de Oxford em 1984 para comercializar um projeto de pesquisa que desenvolveu um sensor de visão a laser para uso em soldagem MIG robótica na indústria automotiva. O SLS ARC representa o mais recente desenvolvimento em uma sequência de 30 anos que começou com esse primeiro sensor da Meta.
"O setor automotivo representa uma parte importante e ainda em crescimento do nosso negócio, e onde tivemos um bom sucesso recentemente", continua ele. "Sentimos que era oportuno construir em cima disso com um novo sensor e aperfeiçoá-lo para aplicações de soldagem de robô agressivos. O ARC é apenas uma parte de um plano global de desenvolvimento de produtos que visa alargar a soldagem de robô de primeira classe".
SLS ARC inclui a otimização da qualidade de imagem automática, combinada com novas ópticas de sensores e um projeto mecânico correspondido às exigências do robô de solda a arco. Ele explora conexão Ethernet da cabeça do sensor diretamente para o controlador do robô para rastrear a costura em tempo real.
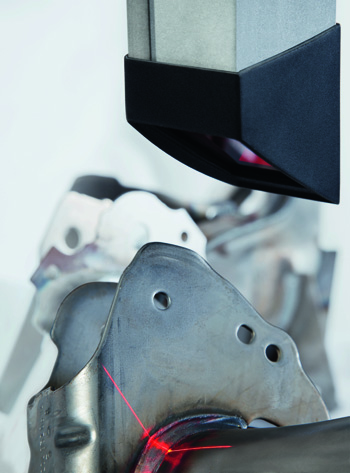
Considerando lasers
Então, em termos de soldagem a laser, qual a estrela em ascensão do setor automotivo? Bem, entre os recentes inovações para a cadeia de abastecimento está o recém-desenvolvido SmartRamp do Prima Poder Laserdyne, que foi projetado para fornecer controle de ponto final consistente durante a soldagem a laser, eliminando áreas onde a falha de solda potencial pode ocorrer. SmartRamp é a adição mais recente de recurso para o controle Laserdyne S94P, que controla a operação dos sistemas de multi-eixos de solda a laser Laserdyne 795 e Laserdyne 430BD.
Na prática da soldadura a laser padrão, a energia é muitas vezes desacelerada no final da soldadura após o ponto de início ter sido sobreposto. Este método deixa uma depressão perceptível no ponto final, que em muitos casos é indesejável. Por exemplo, em soldas herméticas, que são usados amplamente em embalagens eletrônicas para o setor automotivo, esta depressão pode ser um ponto de vazamento. A qualidade e a durabilidade da vedação hermética nestes pacotes deve ser alta uma vez que a falha do selo pode levar à corrosão do conteúdo da embalagem e falha prematura do dispositivo.
Por comparação, controla SmartRamp parâmetros do laser em conjunto com o movimento do feixe, eliminando a ocorrência de um ponto final de solda visível. Para validar a eficácia da tecnologia, Prima Poder Laserdyne realizou uma ampla análise metalográfica de soldas produzidas usando SmartRamp. Estes mostraram consistentemente a ausência de porosidade, ou quaisquer outros defeitos de soldadura no final da soldadura. Em contraste, os testes metalográficos realizados em amostras de soldagem padrão confirmaram que o ponto final pode ser o local de alguma porosidade e penetração da solda inconsistente.
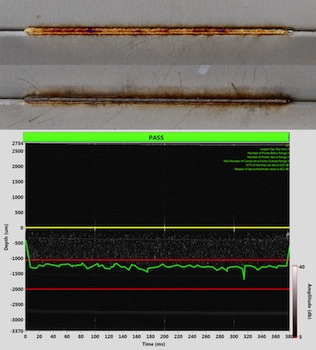
Rastreador de costura de solda
Em outros lugares, Laser Depth Dynamics, o que criou a abundância de interesse da indústria com sua tecnologia patenteada ICI (linha coerente de imagem) para medição de profundidade de solda a laser, tem vindo a apostar no desenvolvimento da solução para aplicações de rastreamento de costura a laser de solda. A empresa diz que a capacidade do ICI de cortar ruído óptico intenso nos processos de laser de alta resolução e fornecer dados geométricos permitiram tecnologia que oferecem capacidade combinada de auto-foco e costura de rastreamento Desde que o sistema ICI é imune a cegueira pelo feixe de processo, sensores adicionais são necessárias em torno da região de processamento. É importante ressaltar que as ações de feixe de imagem compartilha a mesma óptica como o feixe de processo e, ao contrário de técnicas de triangulação, não requer acesso angular adicional à parte. Como resultado, a solda a laser costura rastreamento em torno dos cantos e através da óptica remotas é possível sem a necessidade de girar a cabeça.
Ao medir a distância da cabeça de laser para a superfície de trabalho anteriormente, durante e após a soldadura, o foco e a posição exatas podem ser mantidas mesmo sob condições instáveis. Na verdade, a proximidade do ponto de medição-seguimento de costura para o ponto real de interação está limitada apenas pelo tamanho do depósito de fusão.
Soldas especiais que não são fundidos completamente ou estão subdimensionadas raramente são visíveis para inspeção óptica, enquanto os testes de tração destrutivas são trabalhosos e limitados a algumas amostras. No entanto, usando os mais modernos equipamentos e técnicas de ultra-som de inspeção ponto soldado pode rapidamente e de forma não destrutiva fornecer informações valiosas sobre a qualidade da solda.
Testes de ponto soldado requerem som de acoplamento em uma solda em forma de taça normalmente de três a seis milímetros de diâmetro e geram parede traseira múltipla que ecoa em alta frequência. Uma variedade de linha de atraso e em cativeiro transdutores de coluna de água na gama de frequências de 10 a 20 MHz estão disponíveis a partir da Olympus para esta finalidade.
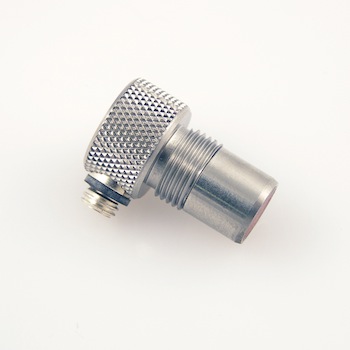
Transdutores linha de retardo utilizam um pequeno guia de ondas de plástico para acoplar a energia do som do elemento de transdutor para o pedaço de teste, enquanto que em cativeiro transdutores de coluna de água incorporam uma membrana de borracha flexível que encerra uma coluna de água que está em conformidade com a topografia do ponto de soldadura para optimizar acoplamento.
No caso dos transdutores de linha de retardo, o diâmetro da linha de atraso e do diâmetro do elemento são geralmente adaptados ao diâmetro nominal pepita para poucos décimos de milímetro.No caso de cativeiro transdutores de coluna de água, o diâmetro do elemento é normalmente adaptado ao diâmetro nominal pepita.
Como com qualquer outra inspecção soldadura ultra-sônica, testes de pontos soldados envolvem comparar o padrão de reflexão a partir de uma peça de ensaio com os padrões obtidos a partir de padrões de referência do mesmo tipo de soldadura, onde a condição é conhecida. Uma linha de atraso ou transdutor de coluna de água cativo pode ser usada para gerar uma série de ecos representando múltiplas reflexões sonoras no interior da solda, a qual pode, então, ser interpretada.
Em uma boa soldadura, o espaçamento entre os ecos será proporcional à espessura da junta soldada, e a taxa de decomposição (a taxa na qual ecos sucessivos diminuem em amplitude) estará relacionada com a atenuação no pepita. Haverá um padrão de eco característica associado com uma boa soldadura, tais como: se não houvesse fusão entre as duas peças de metal, em seguida, os ecos sucessivas estarão muito mais juntos e em maior amplitude; e no caso de uma soldadura subdimensionada, uma porção do feixe de som refletirá a partir da espessura total das duas folhas de metal, enquanto uma porção reflecte a partir de uma única espessura. Isso cria um padrão no qual pequenos picos que representam a espessura de uma única folha aparecem entre os picos maiores e mais amplamente separadas representando a espessura da solda completa.