OEMs estão usando agora compósitos em aplicações mais amplas e maiores volumes para auxiliar a leveza do veículo.
No início deste ano, a BMW anunciou que faria uso extensivo de plástico reforçado com fibra de carbono (CFRP) no chassi da próxima geração de seu sedan de luxo Serie 7. Os novos modelos serão até 130 kg mais leves do que os que substituem, apesar de ter havido um aumento na quantidade de conforto dos passageiros e equipamentos de segurança. Além de reduzir o consumo de combustível e emissões de CO2, esta redução de peso diminui o centro de gravidade dos veículos, melhorando o manuseio.
De acordo com Jürgen Köhler, presidente da SGL Group, que é um parceiro-chave em projetos de CFRP da BMW, "O uso dos nossos produtos à base de fibra de carbono no novo BMW Série 7 é mais um marco na aplicação de série em grande escala de materiais de carbono na indústria automotiva."
Abordagem de material mista
Os veículos são construídos em torno de uma estrutura de material mista de 'Núcleo de Carbono'. O uso de CFRP para elementos estruturais da célula de passageiros, tais como os pilares B, aumenta a força global e a rigidez à torção e flexão da célula de passageiros. Como resultado, a configuração dos elementos de chapa metálica do habitáculo podem ser ajustadas, para permitir uma redução significativa do peso da carroceria.
CFRP também é empregado na estrutura do telhado do veículo híbrido. As fibras de carbono para esta aplicação serão produzidas por fibras SGL carbono Automotivo (SGL-ACF) - um empreendimento conjunto entre a BMW e a SGL Group - em sua fábrica em Moses Lake, Washington, onde a capacidade foi incrementada de forma constante ao longo dos últimos anos. Os pré-formados serão fabricados a partir destas fibras usando um processo totalmente automatizado de produção. As pré-formas serão então entregues diretamente a BMW Group para serem convertidas em peça.
SGL Group também está fornecendo tecidos de fibra de carbono e materiais reciclados fabricados no local SGL ACF em Wackersdorf, na Alemanha. Desenvolvido em cooperação com a BMW, estes produtos reciclados de fibra de carbono serão usados no pilar-C e na partição de cabine.
BMW diz que suas experiências na fabricação dos modelos i3 e i8, os modelos CFRP-intensivos – e a infraestrutura relacionada colocada em prática - têm sido fundamentais para permitir este desenvolvimento.
O volume global de fibra de carbono utilizada no novo BMW Série 7 o torna o segundo maior projeto de produção de CFRP de série na indústria automotiva, após os modelos i.
Concepção, produção e montagem
A rigidez e peso leve do CFRP o torna um material ideal para a produção de componentes automotivos estruturais, mas seu uso em larga escala requer uma mudança completa em como essas peças são concebidas, produzidas e montadas - um investimento significativo para as montadoras.
Anunciado em 2010 e vendido em número muito limitado, o Sesto Elemento da Lamborghini (em italiano "Sexto Elemento”) é um dos exemplos mais marcantes do que pode ser obtido através do uso extensivo de CFRP. Com base no Gallardo e construído em torno de um monocoque de CFRP, 562bhp, V10 do Sesto Elemento impulsiona os 999 kg do veículo a 100 km/h em apenas 2.5 segundos e para uma velocidade máxima de 300 kmh. Além disso para alcançar este desempenho surpreendente, a produção do Sesto Elemento permitiu que os engenheiros da Lamborghini testassem uma variedade de tecnologias para a fabricação de peças CFRP.
A empresa tem uma longa história de uso de CFRP em seus veículos. O Murciélago, em produção de 2001-2010, contou com cerca de 31% (em peso estrutural) de fibra de carbono reforçada de epóxi pré-impregnados. Estes materiais foram utilizados para todos os painéis de carroceria exteriores e algumas peças estruturais internas, que foram ligadas a um quadro de aço.
Custo versus volume
Na construção deste veículo, a Lamborghini observou o alto custo associado com a colocação até das lonas CFRP para estas estruturas, e o tempo longo de cura autoclave necessária. No entanto, a empresa determinou que este processo foi adequado para o Murciélago, do qual a taxa de produção foi de aproximadamente 400 unidades por ano.
O sucessor do Murciélago, o Aventador, foi divulgado em março de 2011, no Salão do Automóvel de Genebra, e apresenta um design todo de composto monocoque contendo 50% de fibra de carbono em peso estrutural. Este design aumenta dramaticamente a resistência à torção do veículo e melhora o seu comportamento de queda em comparação ao Murciélago.
Produzido em volumes de aproximadamente 800 peças por ano, componentes CFRP do Aventador são principalmente fabricados com tecnologias de resina líquida, tais como assistida por vácuo por meio de moldagem de transferência de resina (VARTM) e moldagem por transferência de resina-(RTM). Enquanto Lamborghini considerou estas tecnologias eficientes para tais volumes, para volumes mais elevados sentiu a necessidade de desenvolver novas tecnologias.
Composto forjado
Uma das inovações principais que Lamborghini introduzidas na Sesto Elemento foi um material chamado composto forjado, o qual é utilizado em braços de suspensão e monocoque do veículo. Desenvolvido em parceria com a fabricante Callaway Golf Club, o material reforçado com fibra descontínua foi concebido para permitir a produção de peças de CFRP em volumes mais altos.
Composto forjado baseia-se em composto de moldagem com uma folha de fibra de carbono reforçado (CFSMC) fornecida pela Quantum Composites. É feita de estopas de 25,4 mm de comprimento, de fibra de carbono (53% do peso do material), distribuídas aleatoriamente em uma esteira e ensanduichada entre duas camadas de resina de éster de vinilo. Essa pilha é compactada entre os rolos em forma de folha, e bobinado em rolos semelhantes ao pré-impregnado padrão.
O material é concebido para moldagem por compressão de uma ferramenta metálica ajustada numa prensa aquecida. A sua temperatura de cura é de cerca de 132-160°C, a pressões de 6.9-10.3MPa, e o tempo de cura varia de três a cinco minutos. Lamborghini diz que o material permite reduções drásticas nos ciclos de produção e fabricação de peças com geometrias tridimensionais complexas que não são tipicamente viáveis com laminados reforçados com fibras contínuas.
Usando Composto Forjado, a empresa reduziu o peso dos braços de controle de suspensão do Sesto Elemento em aproximadamente 27% em comparação às versões de alumínio encontradas no Gallardo LP570-4 2010 Superleggera Lamborghini. Além disso, estas peças levam apenas seis minutos para produzir.
Desde o desenvolvimento do Sesto Elemento, o Composto forjado tem sido usado para produzir os assentos de duas peças do roadster Aventador J e também no compartimento do motor do novo Huracán. No entanto, o chassis do Huracán é uma estrutura de material misturado partilhada com os seu companheiro Volkswagen, Audi R8. O quadro R8 Audi Space (ASF) é uma estrutura de alumínio e CFRP pesando apenas 200 kg - 10 kg a menos do que seu antecessor.
Enquanto os módulos de carroceria dianteiro e traseiro do ASF são construídos exclusivamente de alumínio, CFRP é usado para a parede traseira, o túnel central e as três partes dos pilares B. Esses componentes grandes, que são produzidos através de um processo RTM, formam a espinha dorsal da ASF e contam com uma participação de 13% da estrutura.
Na travessa da parede traseira, onde é necessária uma alta resistência no sentido transversal, as camadas de fibra CFRP são amplamente alinhadas unidirecionalmente. Até 14 delas são colocados no topo uma da outra de modo a formar uma folha de 5 milímetros de espessura com uma resistência à tração de 3.95GPa. Nos reforços do pilar B, as camadas de fibras são alinhadas em todas as direções para suportar cargas longitudinais e transversais. A resistência à ruptura destas peças é 0.9GPa.
A semelhança entre esta abordagem e uma tomada pela BMW com o Série 7 é impressionante.
Aplicações mais "mainstream"
Na verdade, parece que a Audi também terá a introdução de peças de CFRP em seus veículos mais mainstream. Em junho deste ano, o parceiro de pesquisa CFRP da Audi, a Voith, anunciou que tinham recebido uma encomenda da montadora alemã para a produção de alto volume de um componente CFRP para um de seus modelos futuros.
"As rodas de fibra de carbono [sobre o Shelby Mustang GT350R] reduziram o peso do veículo em 60 libras em comparação ao alumínio, mas são mais rígidos para uma melhor resposta da direção" Adam Wirth, Ford
Recentemente, o CFRP tem sido utilizado para produzir componentes estruturais para um veículo significativamente mais barato do que quer o Huracán ou R8. Com um preço de cerca de £45.000 ($ 69.500), Alpha Romeo dobrou seu 4C o "supercarro acessível". Lançado no final de 2013, o 4C é produzido na fábrica da Maserati em Modena, Itália. Ele é capaz de acelerar de 0-100km/h em apenas 4.5s, atingindo uma velocidade máxima de 258 kmh.
Este desempenho é alcançado, garantindo que o carro tenha uma relação peso-potência inferior a 4 kg por cavalo-vapor; os designers do 4C optaram por reduzir o seu peso em vez de aumentar sua potência. O carro pesa apenas 895 kg e possui alumínio, composto de moldagem para folha de baixa densidade (SMC) e CFRP.
Construção de peça única
O 4C apresenta um monocoque de CFRP produzido utilizando processos semelhantes aos utilizados para o LaFerrari de £1 milhão. O monocoque de uma peça pesa 65 kg e é fabricado pelo Grupo Adler de Nápoles. Para produzi-lo, a fibra de carbono E700 pré-impregnada da TenCate Composites avançadas são colocadas à mão, ensacada a vácuo e depois curada em autoclave.
Usando este processo, Adler é capaz de produzir componentes que normalmente requerem várias peças múltiplas e etapas de produção em uma única fase. Um pilar de porta de aço convencional, por exemplo, seria normalmente feito a partir de cerca de seis peças diferentes; no 4C, a coluna da porta faz parte do monobloco. A complexidade e os custos de fabricação deste monocoque só poderiam ser justificados pelos volumes de produção baixos envolvidos; um máximo de 3.500 4Cs serão produzidos a cada ano.
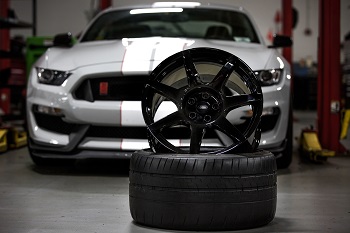
O uso de CFRP não tem de ser limitado ao trabalho de carroceria-em-branco e o painel de um veículo. Ford afirma ser a primeira montadora a produzir rodas CFRP em massa.
Estas rodas - que são quase 50% mais leve do que as alternativas de alumínio - contarão com a Ford Shelby GT350R Mustang, e serão montadas como equipamento padrão. Elas foram desenvolvidas em parceria com a empresa australiana Carbon Revolution.
Carbon Revolution desenvolveu uma técnica de infusão de resina de vácuo que lhe permite evitar a utilização de pré-impregnados, que necessitam ser transportados e armazenados em temperaturas baixas (quase congelantes), têm uma vida útil limitada após a formação, são caros, têm dificuldades em conformidade com geometrias complexas e - como vimos - necessidade de ser moldado e curado sob altas pressões.
Polímero flexível
O método da empresa emprega um elemento de molde de polímero flexível. Este elemento flexível pode moldar áreas rebaixadas e cavidades que moldes rígidos convencionais não podem. Além disso, o molde de polímero flexível é mais barato de produzir do que os seus homólogos rígidos e permite que os outros componentes do conjunto de ferramentas sejam fabricados para reduzir tolerâncias. Em comparação, moldes sólidos combinados devem ser fabricados com tolerâncias altas para obter o ajuste correto com os componentes do molde adjacentes.
Adam Wirth, Supervisor de chassis da Ford Performance, diz: "As rodas de fibra de carbono reduzem o peso do veículo em 60 libras [27 kg] em comparação ao alumínio, mas são mais rígidos para uma melhor resposta da direção." Segundo a Ford, ao reduzir o peso não suspenso (aqueles componentes não suportados pela suspensão), as rodas leves podem ter um impacto significativo sobre a manipulação e desempenho do Shelby. Abaixar o peso das rodas reduz a sua inércia rotacional em quase 40%, o que ajuda o veículo a iniciar, parar e girar mais rápido - melhorando seu tempo de resposta para o motorista. Além disso, as rodas mais leves reduzem a carga de trabalho dos componentes da suspensão - as molas e amortecedores MagneRide - uma vez que eles mantêm os pneus em contato com a estrada sobre superfícies onduladas ou quebradas.