La Fábrica Transparente es una instalación atípica de Volkswagen en Dresden que se ha rehabilitado para ensamblar en eGolf y ser la referencia de la filosofía de movilidad eléctrica de la marca Después de 14 años ensamblado modelos de gama alta y gran potencia la fábrica de Volkswagen en Dresden comenzó un nuevo ciclo en primavera de 2016. En ese momento dejó de producir el modelo Phaeton y el ensamblado del Bentley Continental Flying Spur se trasladó a Crewe. Entonces comenzó el rediseño de una planta multiusos.
Se conoce ahora como la Fábrica Transparente, un nombre con connotaciones literales y figurativas. Una estructura de vidrio cubre las áreas de producción y el centro de I+D, pero además sus puertas se abren al público para 85,000 visitantes anuales que pueden ver las líneas de ensamblado en funcionamiento, recibir información sobre las tendencias automotrices e incluso conducir un vehículo eléctrico.
Para Volkswagen su planta de Dresden siempre ha sido una instalación diferente y atípica dentro de su red internacional de producción. Después de que comenzara a operar en 2001, la comunidad arquitectónica de Alemania la describió como un “sueño de cristal”, un edificio donde “el vidrio no es solo un material, es también una metáfora”. No es habitual que las fábricas automotrices reciban este tipo de halagos por su aspecto exterior. Normalmente para las plantas automotrices de todo el mundo el factor clave es la funcionalidad y no la estética. Algo comprensible.
El diseño abstracto y las elevaciones de cristal en Dresden son el legado del uso original de la planta, el ensamblado del nuevo Volkswagen Phaeton. Dos años más tarde se encargó de la producción Bentley Continental Flying Spur. La planta producía por lo tanto dos de los modelos de gama alta de la marca y la idea de Volkswagen era crear una estructura que fuera línea de ensamblado y centro de exposición, por ello se acuñó el término Gläserne Manufaktur, la Fábrica Transparente.
Lars Dittert, director de la Fábrica Transparente, comenta: “La línea no se limita a una única plataforma. Esta es la fábrica más flexible del grupo. El modelo eGolf está en gran demanda ahora mismo pero podemos producir cualquier modelo del grupo”.
Esta flexibilidad no era posible en la anterior configuración de la planta, que estaba diseñada para la plataforma compartida de Phaeton y Flying Spur. Durante esta fase los cambios en la demanda eran un gran reto. Ahora Dittert confía en que la línea cuenta con flexibilidad para producir series pequeñas de varios modelos del catálogo de VW.
Diseño compacto Se trata de una línea de ensamblado de 1.5 km en un edificio que solo tiene 150 m de longitud. El diseño inteligente de los circuitos se debe a las limitaciones de espacio. Además del aspecto sorprendente de las elevaciones vidrio, la planta también es atípica en su localización en el centro de la ciudad. El área fue anteriormente la zona de ferias de Dresden, pero los elegantes edificios del siglo 19 sufrieron los bombardeos aliados durante la segunda guerra mundial. Volkswagen adquirió el terreno a mediados de la década de los 1990 y anunció sus planes para abrir una planta. El anunció fue una sorpresa para las autoridades de Dresden que ofrecieron otros emplazamientos en las afueras de la ciudad. Pero Volkswagen quería mantener el contacto con la ciudad, los clientes y los visitantes de la Fábrica Transparente.
Esta opción conlleva cumplir con las limitaciones de planificación urbanística. Por ejemplo, la iluminación del edificio por las noches debe ser muy suave para respetar la fauna nocturna. También se ha instalado un sistema de altavoces que en primavera y otoño emite los sonidos de las aves territoriales. Esto permite evitar que las aves migratorias choquen con el edificio ‘transparente’.
Los edificios industriales tienden a priorizar la funcionalidad respecto a la estética por motivos obvios. Pero este es un ejemplo donde se aúna lo mejor de los dos mundos.
Estilo de gama alta Al entrar en el vestíbulo del edificio es evidente que la temática de vidrio es la misma tanto dentro como fuera. Cualquier visitante de la puede ver desde allí la línea de producción en funcionamiento constante sobre sus cabezas.
Encima en las plantas de producción hay mucha luz natural, el suelo es de parque de madera de arce y los tiempos de ciclo pausados son muestra de su anterior función para la producción de deportivos y sedán de lujo. Incluso los grandes robots combinan estéticamente con un color gris claro en lugar del habitual naranja chillón.
La planta cuenta con 65 estaciones de trabajo, un gran contraste respecto a la otra línea del eGolf en la planta de Volkswagen en Wolfsburg. Sus tiempos de ciclo destacan la diferencia. En Dresden son de 12 minutos y en Wolfsburg son de 70 segundos. Wolfsburg cuenta con 250 estaciones de ensamblado y puede distribuir la carga de trabajo de manera completamente diferente.
En Dresden un trabajador operará en hasta 8 estaciones durante un ciclo de 12 minutos. Cuando AMS visitó la planta operaba en un único turno (estaba previsto un segundo turno a partir de marzo de 2018).
El 40% de la producción de Dresden está destinada a a Noruega, donde el eGolf es muy popular. El resto de los vehículos se distribuyen en Europa continental. La planta de Wolfsburg suministra al Reino Unido y al resto del mundo, sin embargo, el eGolf comparte en Wolfsburg la línea con los demás modelos Golf. Los pedidos son variables, pero la línea puede producir 120 unidades del eGolf al día, el límite en Dresden es de 35.
Planificador de rutas El ensamblado se realiza en tres circuitos en diferentes niveles. Las carrocerías llegan a Wolfsburg pintadas y se secuencian en el depósito de logística de Dresden. Los vehículos entran uno a uno por una esquina del edificio para entrar al circuito inicial. La primera estación realiza un ‘baptismo’ con robot, donde se graba el número de identificación del vehículo en tres puntos de la carrocería.
Un transportador suspendido lleva la carrocería a la bandeja en la que realizará todo el primer circuito, la bandeja se elevará y rotará según la necesidad durante el viaje. Cuando avanza la nueva carrocería, la cinta transportadora vuelve para recibir a la carrocería que ya acabó el primer circuito. En el primer circuito se aplican entre otros el panel de mandos, faros, sellado de puertas, cableado y luces traseras, luego parte hacia el segundo circuito.
En total se ensamblan más de 1,000 piezas en el eGolf. Un dato interesante es que en el modelo Phaeton el número de componentes era cinco veces superior. Naturalmente, con un modelo de gama alta el nivel de personalización es muy superior también. En el eGolf hay una mayor estandarización.
El 50% de las piezas necesarias para cada vehículo viaja también en la bandeja. Las partes posteriores se almacenan en la mitad trasera y las partes frontales se almacenan delante. El otro 50% se almacena en estanterías junto a la línea y son componentes comunes a todos los vehículos, con indiferencia de las especificaciones.
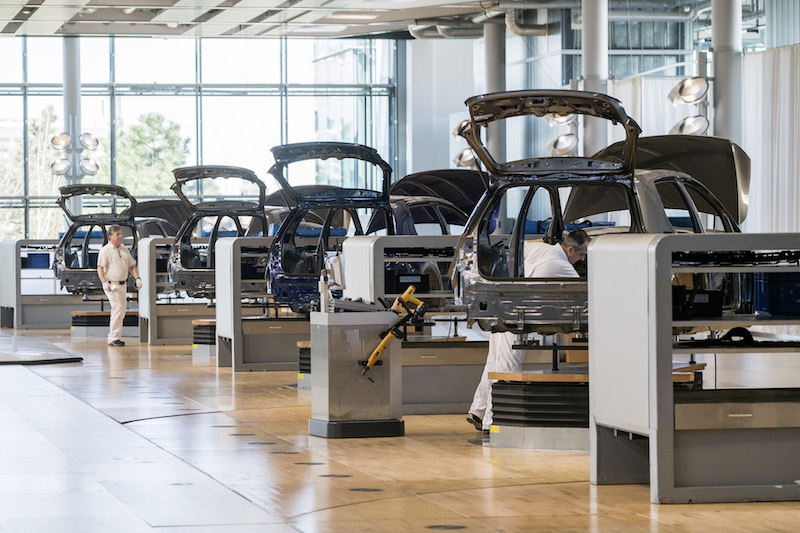
El parqué de madera de arce ofrece un aspecto muy atractivo, pero también resulta práctico. El suelo cuenta con secciones fáciles de retirar junto al circuito de ensamblado, lo que permite acceder a los sistemas de energía, HVAC y guía magnética que controlan las bandejas y la flota de vehículos automáticos guiados que suministran los recipientes junto a la línea. Esta disposición permite flexibilidad para realizar el mantenimiento y el rediseño de la línea de ensamblado.
En la estación de matrimonio se unen la carrocería y el tren de potencia y luego se transporta pre-ensamblado desde el subterraneo de la fábrica. La estación cuenta con una máquina de fijación de pernos que emerge del suelo y fija las tuercas en 30 puntos. Se trata de un proceso automatizado adaptado de los procesos originales: la misma maquinaria utilizada en el Phaeton y Flying Spur se ha reprogramado para la estructura del eGolf.
Luego se aplican 10 tuercas más en la siguiente estación, inclinadas o en horizontal. Los parachoques traseros se colocan antes de que una estación completamente automatizada coloque las ruedas. También se colocan automáticamente los parabrisas delantero y trasero con robots que disponen de visión de máquina. A pesar del elevado nivel de automatización, todavía hay espacio para sencillas técnicas analógicas. Una vez aplicado el adhesivo, se aplica una cinta blanca en los bordes del vidrio y sobre el marco. Se trata de una asistencia visual ya que será evidente cualquier movimiento del vidrio mientras se asienta el adhesivo en el marco.
Planta pionera Mario Blank, director de logística y planificación en la planta, nos comenta que Dresden está demostrando su valía dentro de la red de Volkswagen: “La gente que viene a visitarnos queda fascinada. Cuando se construyó la planta en 2002 todavía se desconocía el concepto de industria 4.0. Era algo todavía muy lejano. Pero aquí podemos mostrar algunos de los conceptos que eran vanguardistas en aquél momento. Por ejemplo, los vehículos autónomos guiados son comunes pero hace 15 años eramos prácticamente los únicos”.
Su equipo se encarga de proponer nuevas innovaciones con tecnologías más inteligentes y según comenta Blank, uno de los enfoques está en la colaboración entre robot y humano: “Estamos preparando por lo menos cuatro casos de uso que queremos aplicar este año”.
La fábrica no es la más rápida por tiempos de ciclo, reconoce Blank, pero se trata de una operación compacta, por lo que tiene una mayor capacidad para probar nuevas innovaciones y ser vanguardista en nuevas técnicas.
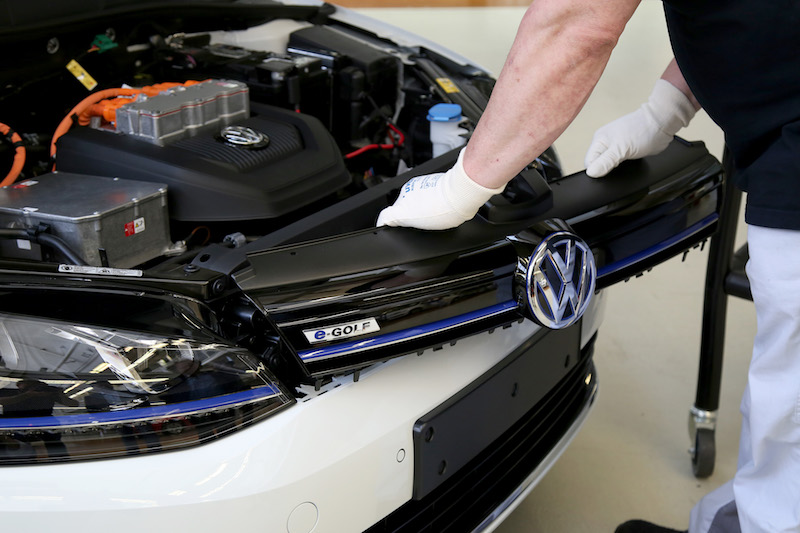
“Siempre hemos producido aquí, siempre hemos tenido invitados, pero cuando volvimos a lanzar la Fábrica Transparente queríamos aportar valor añadido a la marca Volkswagen. No somos la fábrica más grande, no tenemos el mayor volumen y debido a la naturaleza del eGolf tampoco tendremos los modelos más económicos del grupo. Nuestro tiempo de ciclo es ahora de 12 minutos pero utilizamos esta desventaja para sacar provecho de ella”.
Desde nuestro equipo intentamos responder a los pasos más complejos de la producción. Por ejemplo, los acabados textiles superiores son especialmente difíciles de colocar en el auto, gracias a su forma especial y la posición invertida. Como comenta Blank, es una tarea en la que los empleados no temen perder su puesto a las máquinas: “La automatización es el paso más lógico para un entorno de trabajo más cómodo y un mayor apoyo desde un punto de vista ergonómico”.
Por eso invitamos a toda la red a que utilice Dresden para sus pruebas antes de la producción en masa, que traigan sus ideas a la Fábrica Transparente para ensayarlas. Blank resume: “Esa es la idea que presentamos a nuestro jefe de producción y la entendió inmediatamente. Apliquemos primero las nuevas tecnologías en Dresden. Lo ensayamos aquí y podemos probar si funciona o si resulta beneficiosa. Así ofrecemos valor añadido a la marca”.
Desde agosto de 2017 la planta cuenta con una incubadora de nuevas empresas que colaboran con los desarrolladores y clientes de Volkswagen en diversas áreas automotrices, incluida la producción. Además de centro de producción es un centro de I+D y un punto de acceso a los clientes, todo el edificio es una exposición de la marca. En medio de la crisis del Diésel, Volkswagen considera que la Fábrica Transparente es un símbolo de la nueva orientación de la empresa y una herramienta en la enorme tendencia hacia la movilidad eléctrica, conducción autónoma y nuevas formas de propiedad.