BMW Munich plant to go full electric with Neue Klasse and revamped, digital production system
BMW’s home plant will produce only EVs by 2027, with much of the century-old factory rebuilt to meet new levels of efficiency and digitalisation, without missing a beat of ongoing production.
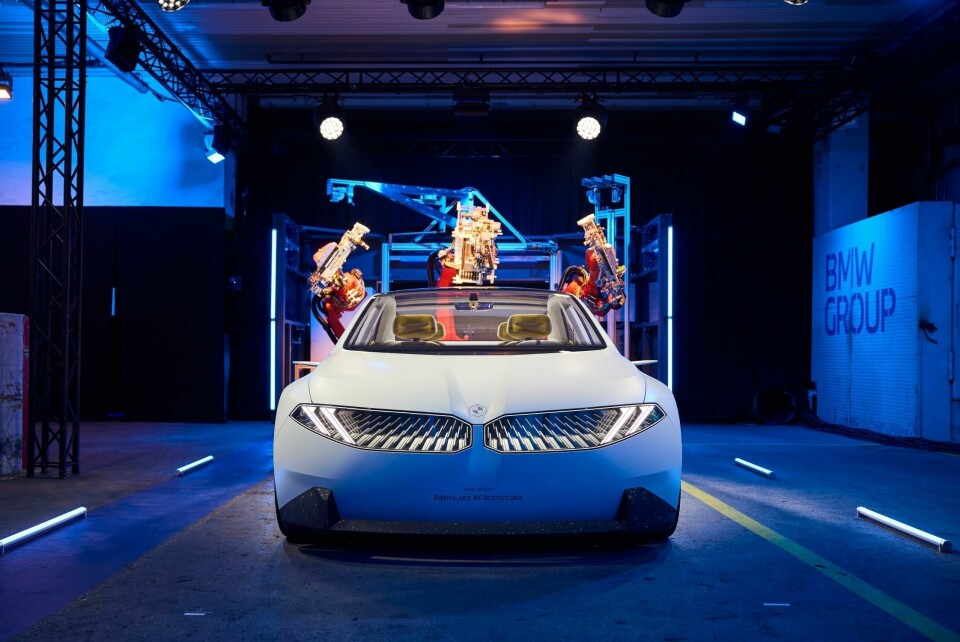
BMW’s Munich plant will produce a new EV Sedan based on its Neue Klasse platform, and thereafter end ICE production
A class of its own: transforming BMW production for next-gen EVs
BMW Group has confirmed that it is on track to transform its vehicle plant in Munich, Germany for full electrification. Serial production of an electric sedan version based on the group’s new EV-focused architecture, the Neue Klasse, will begin as scheduled in 2026 following a €650m ($715m) overhaul, which BMW executives say will make the 100-plus year-old factory nearly as efficient and sustainable as a greenfield factory.
BMW has also annouced that the plant will stop production of internal combustion engine and hybrid vehicles by the end of 2027, making Munich the first existing BMW plant to convert fully to all-electric vehicles, which will be built using the same processes and technology. That will help the plant to exploit more completely the engineering and manufacturing benefits of electrification, including reduced production costs and complexity.
It’s a transformation hailed during a press event held at the plant by Milan Nedeljković, board member for production at BMW Group, as a shining example of the need to manage “production and transformation at the same time, and with record figures”.
Despite significant construction work, which began more than two years ago and includes adding new body, assembly and logistics halls, Munich has continued to produce across 10 shifts per week without interruption, churning out an average of 1,000 cars per day. In 2023, the factory built around 200,000 vehicles across ICE and plug-in hybrid variants of the BMW 3 Series sedans, M3, 4 Series Gran Coupé and the electric i4 – the latter of which now accounts for around 50% of production, according to BMW.
The plant’s results contributed to an all-time production high for BMW Group, which manufactured nearly 2.6m vehicles in 2023 as in semiconductor and supply chain shortages eased. Over the past year, BMW also launched 12 new models, including six all-electric vehicles. According to Nedeljković, one in seven vehicles built last year globally were all electric, or more than 350,000 vehicles; in 2024, that is expected to be one in five vehicles, or more than 500,000 vehicles. By 2030, BMW expects every second vehicle it builds to be electric.
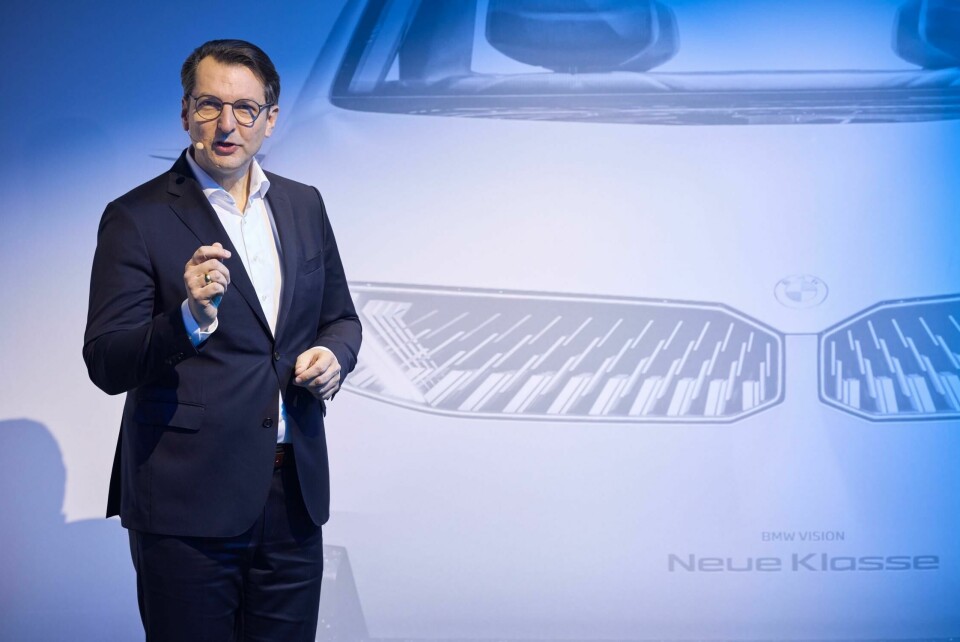
Despite this growth, Nedeljković stressed that BMW will maintain a high level of flexibility across its global production network to account for uncertainty in the pace of demand for electric vehicles and varying economic and regulatory situations across major markets. BMW continues to build powertrain variations along the same assembly line in many plants, and it will be ready to scale up or down EV production, as well as to add alternative technologies, such as hydrogen fuel cells.
A new class of manufacturing efficiency and digitalisation
The Neue Klasse sedan that enters production in Munich will benefit from a redesigned layout, production flow and value chain, as well as new technology to support greater flexibility. According to Peter Weber, director at Plant Munich, these changes represent a new production system, based on the principles of BMW’s iFactory manufacturing strategy, which pursues ‘lean, green and digital’ manufacturing principles.
“Over the next three years, we will develop and implement a production system in Munich that will last for decades,” Weber said. “There will be no reason to talk about a 2030 strategy or the years after, because we are already defining the future of the plant.”
According to Nedeljković, production of Neue Klasse will usher in greater levels of cost efficiency in manufacturing, thanks to use of fewer parts and modules, as well as reductions in overall emissions due to a higher use of recycled materials and renewable energy. BMW also expects production cost, energy and emission benefits thanks to its upcoming switch to the energy density advantages of the cylindrical cells it will use in its sixth generation (Gen Six) battery packs versus its current generation, which uses prismatic cells.
BMW is targeting a cut in manufacturing costs of 25% for the Neue Klasse architecture compared to 2019 manufacturing levels, says Nedeljković. To achieve that, Nedeljković and Weber stressed the importance of manufacturing working in close alignment with design and engineering, including in making material decisions. “Production starts in the product development phase,” says Peter Weber.
”There will be no reason to talk about a 2030 [production] strategy or the years after, because we are already defining the future of the plant.”
Peter Weber, BMW Group
The i4, which BMW has built in Munich since 2021, is fully electric but based on a multi-powertrain platform and Gen 5 batteries, produced using existing technology at the plant.
Nedeljković also predicted that BMW plants, which are already increasingly digitalising processes from virtual factory planning to artificial intelligence applications, will take another leap in connected, self-steering production thanks to intelligence systems in the battery and software in the Neue Klasse.
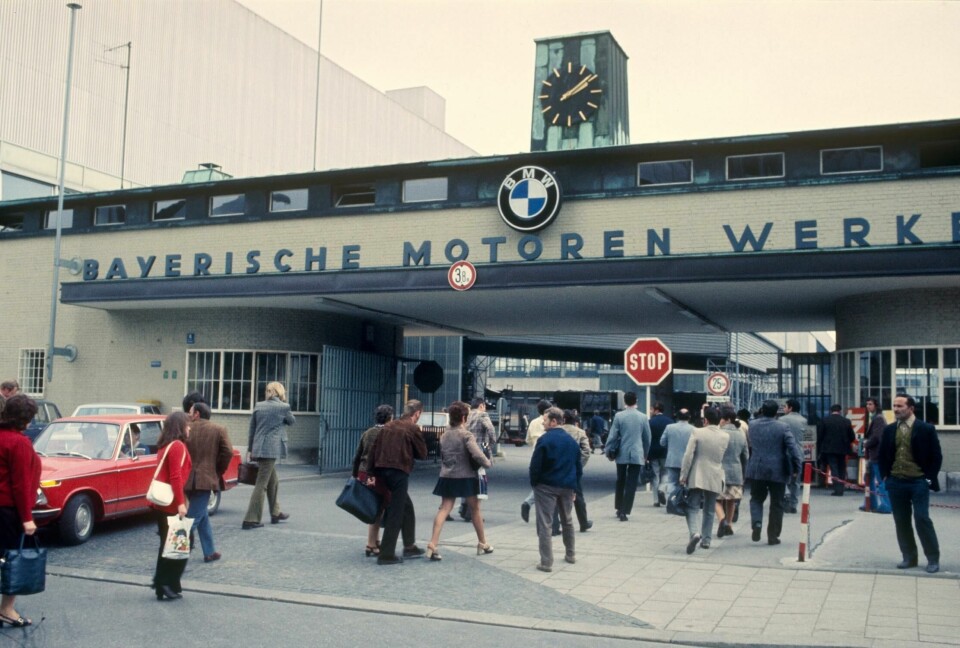
The end of an era is the beginning of a new one in Munich and beyond
The regeneration of Munich, which BMW refers to as its ‘parent’ plant thanks to its historic role and location near the carmaker’s headquarters, is an important transition for BMW in rolling out its next generation of EV vehicles. It is also a point of symbolism and pride for the Munich plant, as the original Neue Klasse was launched and built here in 1962, a successful model whose chassis and powertrain were the forerunner to the BMW 02 and the 3 Series sedan, which launched in the 1970s and would become the best-selling BMW of all time.
The next generation Neue Klasse sedan – a preview version of which was shown at last year’s IAA motorshow in Munich, which BMW has said was close to the production model – is another bend in the long arc of Plant Munich’s history. The plant started building aeroplane engines in 1922, and would go on to produce military equipment, motorcycles and engines, before adding passenger vehicles in 1952. Eventually, two-wheeler production was shifted to Berlin to make more room for passenger cars. Last year, the plant ended assembly of combustion engines after around 75 years, moving output to plants in Steyr, Austria and Hams Hall, England.
The emotional link to the plant and its history was evident during the press event that announced its full electrification. BMW filled the former engine hall with the original Neue Klasse, along with other historic models and engines built at the plant; it dressed the concrete floors – still marked with lines from workstations – with 1960s furniture and old television sets showing original adverts, while songs from Motown, The Rolling Stones, The Beatles and others from the era pumped from the speakers. For the team, it was a fitting end to the plant’s close connection to motor production – and indeed, the company’s very name, Bayerische Motoren Werke. The parting celebrations now over, however, work will begin in the coming weeks on repurposing the former motor hall into a new assembly centre for the Neue Klasse.
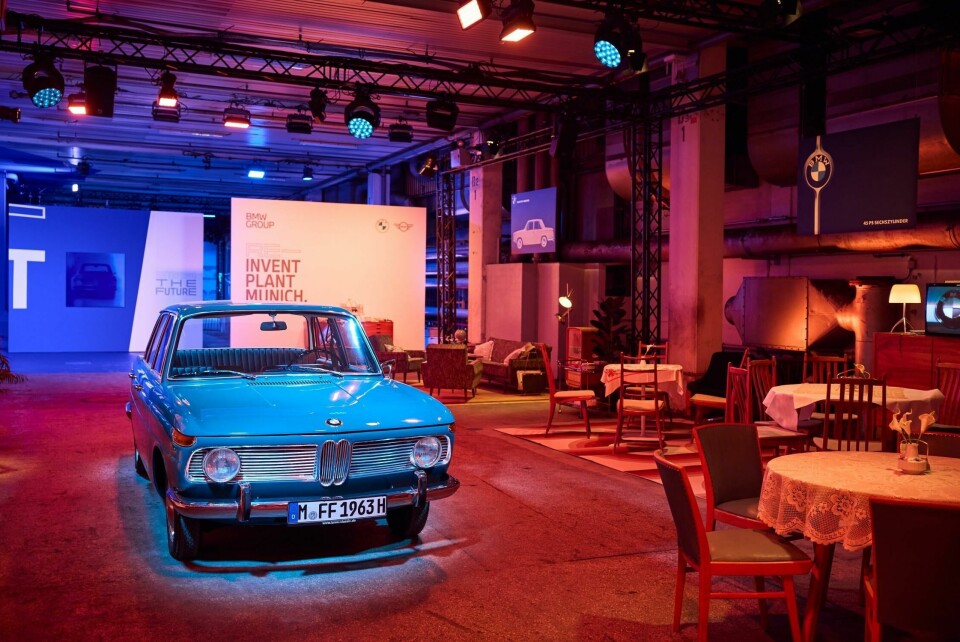
The Neue Klasse was a forerunner to the BMW 3 Series, and was part of earlier BMW shifts in how it sold and produced cars
Nedeljković similarly nodded to the past and future in production, tracing a direct line not only from the design of the original Neue Klasse model but also in how it coincided with changes in BMW’s business processes that are once again seeing major changes. In the 1960s, BMW introduced its first dedicated dealerships, while today it is developing a direct sales model; BMW began an early version of mass data modelling 60 years ago and now is increasingly moving to cloud-based systems; and just as the first phase of mass robotics and automation accelerated in the 1960s and 1970s, BMW is today implementing more artificial intelligence across robotics and production processes.
However, the investment in Munich for Neue Klasse is more than a finely choreographed change story. It will help Plant Munich to stay competitive and continue to play an important role in BMW’s changing German and global production network. Munich will be the first site in Germany to build the model series and to install Gen 6 batteries, which will be supplied by a battery assembly plant set to be built in Straßkirchen and Irlbach in Lower Bavaria, which will eventually serve the carmaker’s other major Bavarian assembly plants in Dingolfing and Regensburg. Today, Munich receives Gen 5 batteries for the i4 from Dingolfing.
The first plant to start assembly of Neue Klasse models, however, will be the upcoming BMW plant in Debrecen, Hungary, which is set to produce an electric SUV and battery packs in 2025, and will be BMW’s first all-electric factory. Neue Klasse models and Gen 6 batteries will also being added at BMW’s joint venture plant in Shenyang, China in 2026, and in San Luis Potosí, Mexico in 2027, both of which will also continue to produce a mix of powertrains. BMW’s largest global plant by vehicle output, in Spartanburg, South Carolina, is also preparing to launch production of a new electric SUV in 2026 alongside ICE and hybrid variants, with a new battery plant opening nearby.
BMW’s manufacturing leadership highlights that the changes to its production, along with such innovations, will ensure that the plant is competitive both in the face of other OEMs and new players in the European market – including Chinese EV manufacturers – as well as with other BMW global plants.
Thanks to updates its layout, systems and equipment, Plant Munich, although more than a century old and constrained in terms of space and its location within the city limits, will produce EVs at an efficiency level “very comparable” to the greenfield in Hungary, says Nedeljković.
Speed and flexibility in transformation
Speed of implementation and development will be critical factors for BMW, and indeed other European and legacy manufacturers as they face competition from new players and startups. On the one hand, BMW is making important moves to increase the pace of its development and implementation. In battery production, for example, its Munich research centre focused on changing cell chemistry, together with a pilot plant for battery cells in nearby Parsdorf that opened last autumn, are examples of how the OEM is trying to stay ahead of fast-changing technology and innovation. In digital production, Peter Weber emphasises “speed, speed and speed” in implementing new technology and tools, which he describes as a competitive factor for BMW.
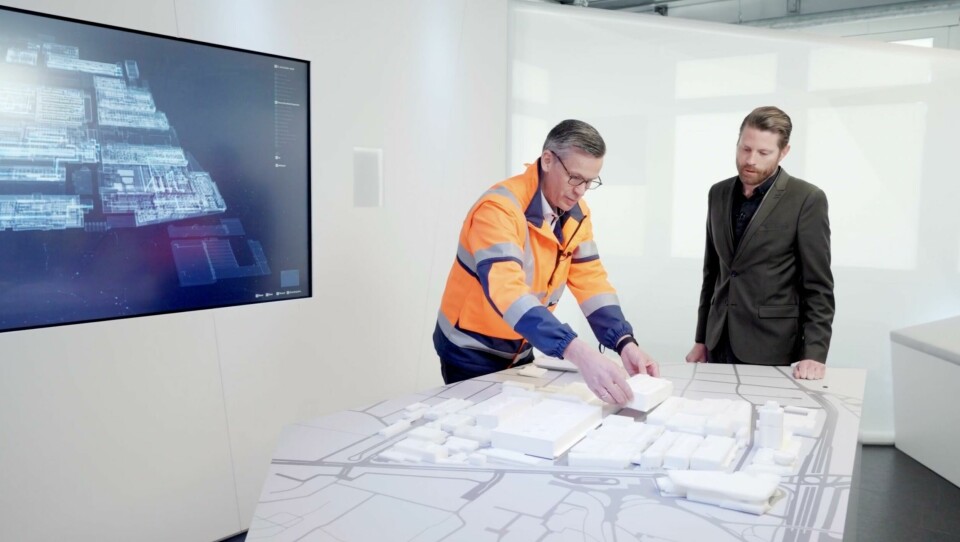
Nonetheless, BMW and other manufacturers in Germany and Europe face challenges, admitted Nedeljković. Validation and approval times for batteries and vehicles takes years and means that any technology that enters serial production will, almost by its nature, be out of date. Meanwhile, construction projects, including the revamp of Plant Munich, must be done in a careful way together with officials. “It’s not always the production or technology that takes time, it is gaining the approvals and permissions,” he said.
Energy prices in Germany and much of Europe, meanwhile, remain high. “Energy prices for industrial manufacturing are a disadvantage in Germany, that is just a fact we have to face,” he said.
But the carmaker is facing those issues head on. In Germany, including Munich, BMW is using geothermal energy for heating, including efforts to “bring the source of that energy closer” to the plant.
Meanwhile, Nedeljković suggests that the time it is taking BMW to prepare its plant for the Neue Klasse architecture should be the point at which the market “reaches the tipping point” when having a dedicated EV architecture makes sense in terms of customer demand and volume. However, flexibility will remain at the heart of BMW’s production philosophy, including the ability for plants to produce multiple powertrains on the same assembly line. He also does not rule out adding new technology such as hydrogen fuel cell, for which BMW currently has a small pilot plant in Munich.
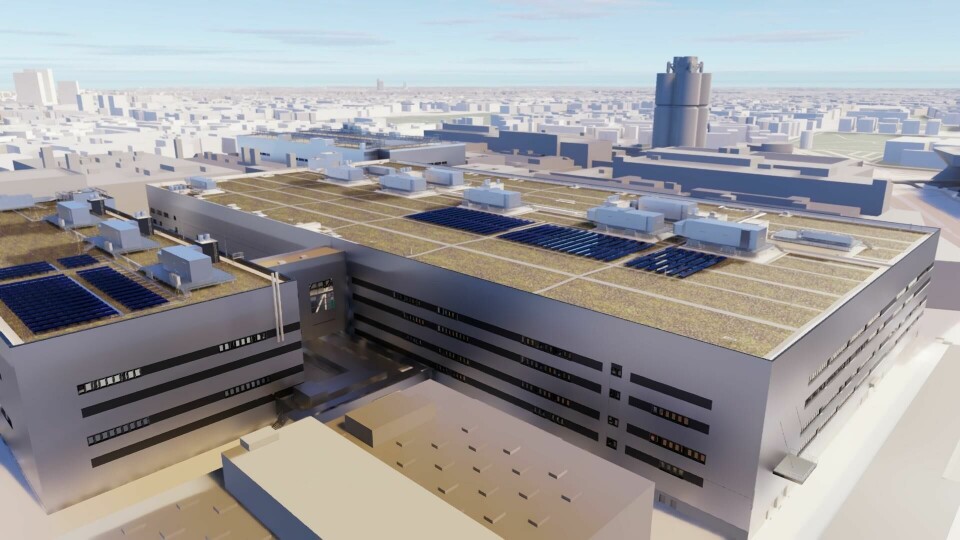
“Hydrogen is one of the main, very important alternatives to be considered. That’s why we keep the facilities flexible towards hydrogen and other technologies,” said Nedeljković. “But we are not investing into the technical facility right now.”
Whilst flexibility is important, Nedeljković is also clear that BMW won’t be investing further in ICE technology for plants that no longer produce this technology. Rather, he describes flexibility in determining when other plants will introduce Neue Klasse and EV platforms.
“All of our plants worldwide will be capable of running both [ICE and EV] in one line, and we are prepared to integrate the Neue Klasse at any site alongside existing combustion engines,” he said. “It will be a matter of time, depending on how fast one [powertrain] is growing or declining. We are very critical on that point. We are not sure what the demand will be, so we will maintain flexibility.”