BMW: ‘Flexibility is in our genes’
BMW, Mini and Rolls Royce are driving a tight electrification course. Nevertheless, the group remains open to drive diversity. In an interview, production director Milan Nedeljković talks about flexibility and the concept of the iFactory.
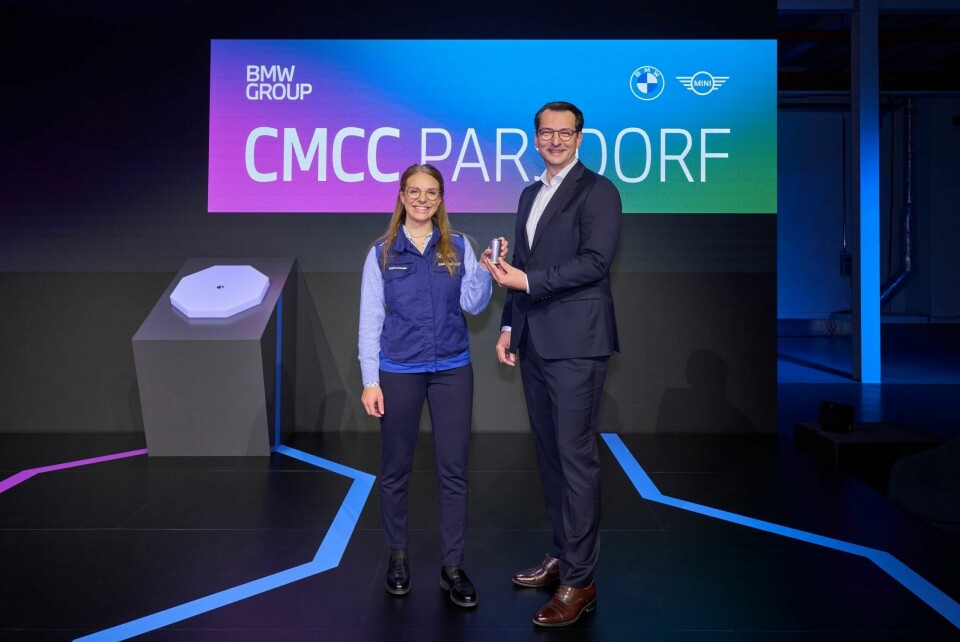
One of the latest breakthroughs the carmaker has made is in the opening of its Cell Manufacturing Competence Centre (CMCC) in Parsdorf, Germany. The CMCC is aiming to achieve ‘expertise in every cell’ for its sixth-generation battery cells that will be used in its Neue Klasse EVs. Nedeljković, being a key player within the competence facility, believes that being flexible in developing EVs, and cooperating with both inhouse departments and outside suppliers alike, will be the key to being successful in scaling up electrification globally.
Mr Nedeljković, BMW pursues the philosophy of being able to produce vehicles of all drive types in the same plant on the same production line. How well do you do with this maxim of high interchangeability?
Flexibility is in the genes of BMW production in many respects. Flexibility with regard to the derivatives per production line, the exchange between the plants and the working time models at the locations. Particularly in times of volatility, flexibility is a crucial tool for manoeuvring safely through crises, such as the recent Covid or semiconductor shortages. As we look to the future, which for us means further volume growth in all-electric drives, but also the continued offering of plug-in hybrids and internal combustion engines, this high level of interchangeability and flexibility in the plants gives us very important tools. Our employees have a high level of expertise in how to carry on this philosophy as an integral part. Incidentally, this is one of the reasons why all our plants are currently working at very high capacity.
Let’s take the Dingolfing plant as an example, which is not only the largest in Europe but also the lead plant for the luxury class. How is the integration of the new i5 going there?
In Dingolfing, we began integrating electric mobility many years ago. First in the form of plug-in hybrids, then two years ago we added the iX. With this model, we enabled assembly for the production of fully electric vehicles. Last year we added the i7. So both models have created the structural preparation for electromobility there. The integration of the i5 is therefore now proceeding very smoothly. The Dingolfing plant has long been in a position to offer all types of drive. We are also positioned there to meet demand flexibly in areas other than the drive system. In the past two years, we were able to use the plant holidays in particular for the preparatory activities for the integration of new vehicles.
The share of i models in Dingolfing is expected to rise to over 40% as early as 2024, correct?
That is correct. You can see from this how quickly we are ramping up electromobility. Last year, we were able to double the number of e-vehicles compared to the previous year. This year, we are continuing to grow significantly and next year, every fifth vehicle in the BMW Group will be electric. By 2025, it will be every fourth vehicle, and by 2026 every third vehicle. Dingolfing will become one of the driving plants with three derivatives and an electric share of 40%.
In the current global production of BMW, Mini and Rolls Royce, what is the share of pure electric drives, what is the share for hybrids and what is the share for pure combustion engines?
Last year, we produced around 11% fully electric vehicles. If we break this down by brand, BMW has a BEV share of over ten per cent and Mini 15%. At Rolls-Royce, the all-electric Spectre is now starting up. Plug-in hybrids and BEVs together accounted for just under 20% last year. And this year we are also doing well.
The concept of the iFactory is a kind of master plan for worldwide production and is part of BMW’s guiding premise “Lean.Green.Digital.” What strategies and next steps are hidden behind the iFactory?
The iFactory describes our vision for the future and is our master plan. The focal points are electrification, profitability, sustainability and digitalisation. Each of these four fields has a strategic orientation. E-mobility is about transformation and growth. Most of the plants are already capable of fully electric vehicles and are continuously ramping up production. At the same time, we are preparing for the next generation of drives - we call it Generation 6.
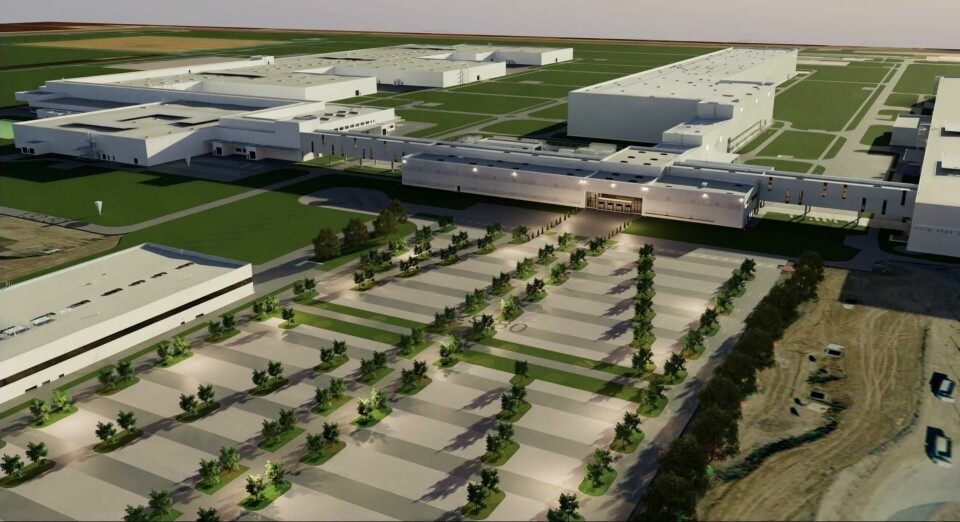
We are starting with this at the Debrecen plant, followed by the Munich, China and Mexico sites, among others. We see digitalisation as one of the biggest levers for the future and the corresponding processes and procedures as well as the efficiency of the plants. Automation, as it was known until now, replaced repetitive activities, to put it simply. With digitalisation, we are now at a point where a certain amount of new intelligence is added. Digitalisation is therefore becoming an enabler of automation in new fields. With its help, we can make the entire production network much more integrated. We are talking about a large network that has no redundancies within it. As far as sustainability is concerned, we have already achieved a 20% reduction in CO2 emissions in our global production network between 2019 and today. We are working on a footprint at each location and exploiting local opportunities, such as geothermal energy, where we have potential, for example, in Munich, Debrecen and China.
The Debrecen plant is often referred to as a kind of showcase plant in terms of sustainability. What are the special features of the plant and how does it influence others?
Debrecen is a very good example of the implementation of our sustainability strategy. We consistently use technologies that completely dispense with gas. For example, we are implementing heat exchange concepts, testing geothermal energy as well as solar and wind energy to ensure the supply of regenerative energy. At the existing locations, we cannot do without gas in the short term, as we need it to heat the halls and as process gas for the paint shops. Here we rely on individual technical solutions to reduce energy consumption. We also rely on a clever energy management system that allows us to control consumption over the course of the day and compensate for any peak consumption.
Let’s come to Munich: The BMW main plant faces special challenges due to its location close to the city centre. This is one of the reasons why the plant is to be turned into a particularly green factory - visually as well - in the shortest possible time. And this is where the Neue Klasse will start in 2026. What about progress?
A factory in the heart of a city is and remains a unique selling point. In recent years, we have implemented our projects with a high sustainability standard, for example the new paint shop building. Now we are preparing the Neue Klasse in Munich, which will also entail a renewal of the assembly building. With these changes, the plant will meet the demands of sustainability both structurally and technically. Last year we developed a master plan, which also included an architectural competition with renowned architectural firms. With this, we are venturing a look into the future of an urban plant in the years 2040, 2045 or 2050, for example. With this vision, the upcoming renovations can be embedded in a master plan. In the long term, this includes a new appearance for the entire plant with traffic areas, greenery and bio-zones.
Munich has always been a kind of heart and image-bearer for the “Bayerische Motoren Werke”, because many of the engines with a particularly strong image were manufactured here. How drastic is the relocation of engine production to Great Britain and Steyr for the workforce?
The Munich plant has always been characterised by a strong orientation towards the future. Over a hundred years of history prove that people here have always been able to change constantly. The fact that we are looking into a future in which electromobility plays an increasing role, and that the Neue Klasse is being created here, were such strong motivators for the workforce that the issue of combustion engines took a back seat. We developed a jointly supported concept for the site, which we communicated clearly to the employees at an early stage. Getting everyone involved is an important basis for change. In addition, the site offers a high degree of change options and vacancies. For example, the battery competence centre or the prototype production for cells and high-voltage batteries in Parsdorf.
With the new Mini generation, the Mini Countryman is now coming to Leipzig. What advantages do you expect from the expansion of the Saxon location, where BMWs and Minis will roll off the production line together for the first time?
We produce vehicles of our UKL platform in Leipzig. With Mini, we are now adding another derivative. The flexibility of the site makes it possible to run the Mini off the same production line there as well. This will increase utilisation and ramp up capacity. We will expand production in Leipzig to over 300,000 units. To achieve this, we are increasingly using the synergies between the derivatives.
What role is left for the contract manufacturer Nedcar in the Netherlands, where the Mini Countryman has been coming off the production line so far?
The Countryman will continue to be produced there until it is phased out. The Mini Convertible will also roll off the production line there until next year. This production will later move to Oxford. All this is based on agreements we made with Nedcar very early on.
How much does Brexit affect the trade in goods between Great Britain and Germany?
The trade agreements and arrangements between the EU and the UK are beneficial here. These create a basic basis for economic trade. However, the administrative processes, customs clearance, tax formalities and the handling of logistics will be more difficult after Brexit. This simply means more effort and takes more time. Spontaneity is curbed, as is the exchange of staff. Short-term rotations, even for further training, can only be organised with more effort. My conclusion is therefore: open markets are simply the be-all and end-all for our industry.
What plans do you have with regard to your production in China?
At the beginning of the year, we celebrated the 20th anniversary of our production in China. We are looking at a steadily growing production footprint there. Last year, we expanded the two locations in Shenyang. The plant that produces the 5 Series and the X3 has now also added the X5 for local production in China.
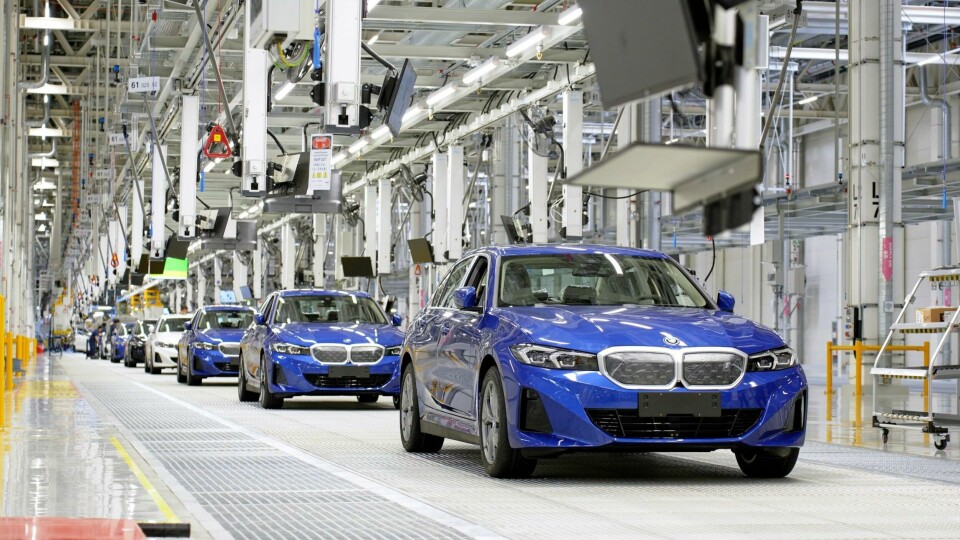
At the other site, where we manufacture UKL and KKL vehicles, we have mirrored the capacities with the help of a new structure and have now been able to start production of the all-electric i3 (editor’s note: the vehicle corresponds to the electric 3 Series and not the i3 from European production). Our capacities now exceed 800,000 units. This sets the course for further growth in China. As mentioned at the beginning, the plants there are also prepared for the Neue Klasse.
What are the plans specifically for the Mini brand in China?
Mini production in China will start soon as part of a joint venture with Great Wall and a plant near Shanghai. Together with our partner, we will produce the new all-electric Mini Cooper there and also a small crossover.
In order to increase efficiency and reduce costs in production, a high degree of automation is also on the agenda at BMW. What steps are you taking and how and where are you already using artificial intelligence tools in production?
We see AI strongly in the area of quality on the one hand, and in logistics on the other. In quality, AI is able to recognise error patterns and make decisions through its learning ability. In logistics, AI enables AGVs to make their own decisions, for example when turning off on a route. These capabilities grow with increasing computing power and become better and better.
The networking of systems enables them to exchange information with each other and AI can ultimately also be used to control entire production sections. From this, decisions can be made about resources as well as maintenance measures. These are examples of applications that we are putting into practice. The potential is growing steadily, as applications such as ChatGPT show.
We are also currently evaluating such topics very intensively. A good example comes from our Spartanburg plant - there, an application supports our maintenance staff with questions about repair requirements. The system also uses knowledge from manuals and compresses this knowledge for the user. The time that employees would have to spend in archives can be significantly reduced with the help of such technologies.
With a view to such tools, how important is the topic of training and further education and what distinguishes your company in this area?
The basis of every change and every technological development is the staff and their expertise. Last year, we trained more than 30,000 employees on the topic of electromobility alone. This starts with the simplest topics such as handling vehicles and extends to complex training in programming, control, maintenance and the planning of systems. Digitalisation is playing an increasing role in this. An essential goal is that employees are aware of the potential of digitalisation and can implement it for their own needs. The times when there was a predefined concept for the employee - a central IT system to which he adapts his way of working - are over. Today, we rely on streaming services within production as well as apps that employees can partly programme themselves to get support. Of our 150,000 employees, about 80,000 are going through a kind of digital boost, which includes basic and advanced qualifications. You have to build up skills and reduce the awe of technology. This creates growth and change.