How BMW will maintain quality in its 3,000-step battery cell production process
At its recently opened German Cell Manufacturing Competence Centre (CMCC) in Parsdorf, BMW is aiming to achieve ‘expertise in every cell’ of its generation six batteries for its Neue Klasse EV models. But to do this, the carmaker needs to ensure the 3,000-step production process is consistently quality checked along the way.
The importance of battery design
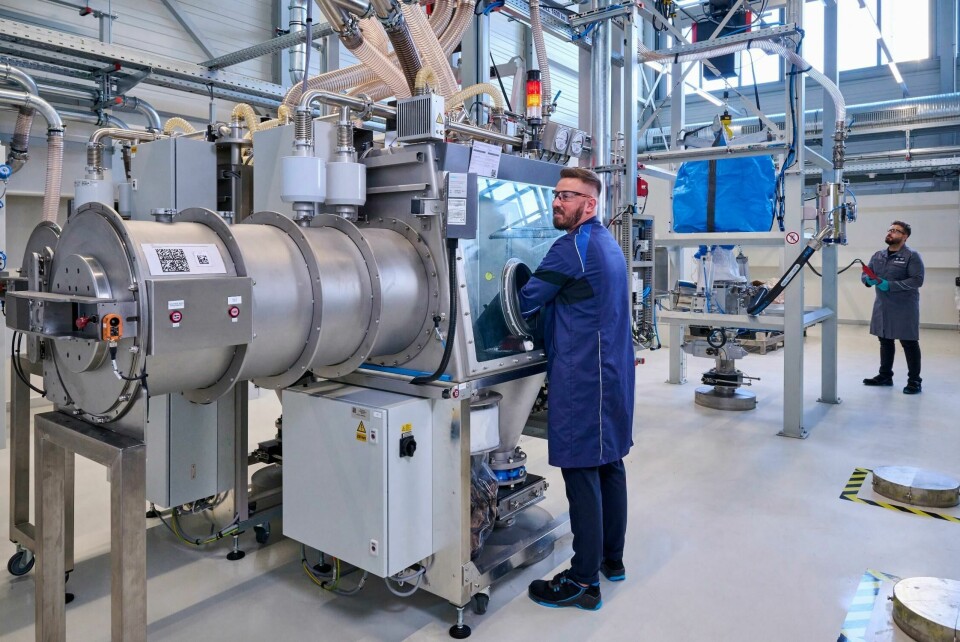
Quality control begins long before production starts – with the battery cells’ chemistry. BMW is using a new cell format and advanced cell chemistry at its CMCC facility. The new round battery cell (in comparison to previous generations of battery cells which were prismatic) has been specially designed for the e-architecture of the Neue Klasse models, making it possible to increase the range of the vehicles by up to 30% whilst reducing emissions and costs in production, according to the carmaker.
The cylindrical cells have a standardised diameter of 46mm and two different heights of 95mm and 120mm. Compared to the prismatic cells of the fifth generation, the nickel content is increased on the cathode side and the cobalt content is reduced at the same time. The silicon is then increased on the anode side, resulting in volumetric energy density in the cell being increased by more than a fifth. Voltage of the energy storage, drive and charging technology will increase to 800 volts, which optimises the feeding of energy into fast charging stations. The charging capacity has also been increased with a current of up to 500 amps, cutting the charge time by 30%.
“The quality control starts before we start production, with incoming inspections of the raw materials and powders,” said Martin Schuster, head of battery cell development, BMW. “We monitor various process parameters at every step.”
Milan Nedeljković, member of the board of management of BMW AG, responsible for production said: “The raw materials are important and that’s why we try to achieve maximum stability. It is a very elementary part of quality assurance that we know exactly which parameters influence the process and which must not to overlooked.”
This begins with sourcing. Nedeljković said: “For us it is very important that we know and control the process chain up to the raw material. Especially in the case of cobalt and lithium. We have concluded contracts with mines and raw material producers in the current generation in order to ensure we have a firm grip there. We then make these raw materials available to the battery manufacturers through our own contracts.”
He added: “The second thing is testing and checking. Checking is very reactive and regulating is proactive. That is exactly the approach that is pursued here.”
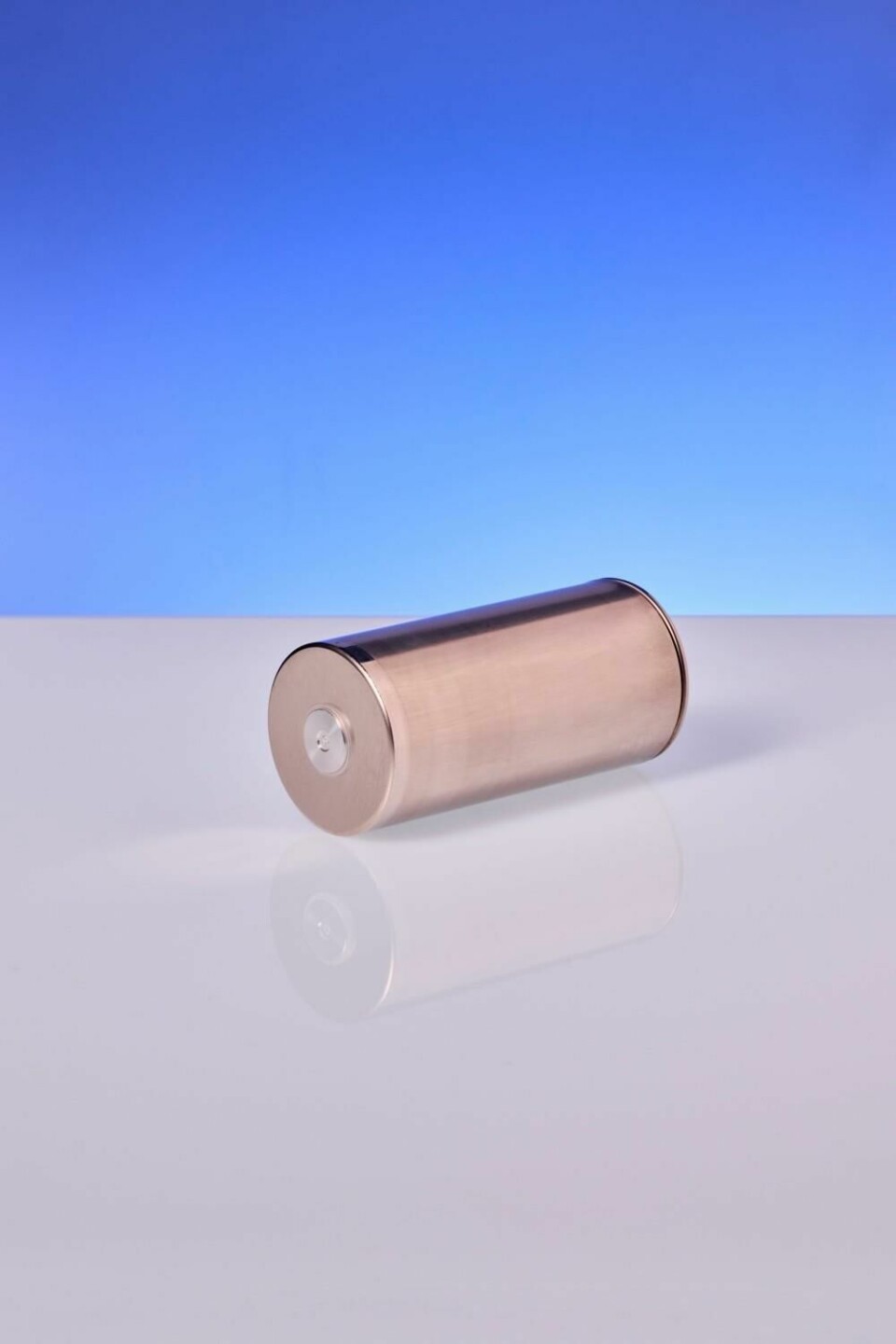
Once the materials have been quality checked, the CMCC begins the manufacturing of the cell with electrode production. Base materials are then mixed precisely with binders and solvents to create a “slurry” in the dosing and mixing part of the process. Schuster explains they use an innovative process here by continuously mixing, which allows the quality to be continuously controlled. “The paste that is produced is already monitored there, and this happens at every step of the process,” he says. The slurry is then precisely coated onto wafer-thin metal foils, which are then dried in the most energy-intensive part of the process. “The decisive factor is actually the amount of material that is subsequently applied, and that is very homogenous.”
Ensuring quality to scale up the recipe
The CMCC works with BMW’s Battery Cell Competence Centre (BCCC) which is located nearby in Munich, with the BCCC providing the “recipe” for the battery’s chemistry. This recipe is then passed on to the CMCC which tests it for production, and then the CMCC passes it on to BMW’s suppliers to produce the battery at scale.
Nedeljković said that by ensuring quality at a smaller scale, starting at the BCCC and then scaling that up within the CMCC, the OEM can help ensure that same quality will be present when production is fully scaled up.
“I like to use the analogy with cooking,” he said. “If I want to make a good dish, I have to know the ingredients and how much of them to use. Then it’s about the process parameters, such as how long to bake, how much to stir, how long to let it stand afterwards. If I know that on a small scale, it doesn’t mean that it will work on a large scale, because the ratio is greater and the whole thing reacts differently. That’s why we’re doing this carry-over that’s taking place here at the CMCC.
Using this cooking analogy, with the 3,000 process steps in manufacturing these cells, there are 3,000 steps to getting the recipe right. Nedeljković said that means if you overlook ten of those steps which could be relevant for the stability of the process, they won’t get the end result needed.
He said that high investments in facilities such as the CMCC are necessary so that BMW can remain flexible when developing new battery technologies, such as the cylindrical cell, before mass producing them. “The plants are designed for this specific shape and design of the battery,” he explains. “That’s why we attach great importance to this battery competence, by defining the formulation of the battery. But we can adapt and change quickly on a small scale. Once we have established ourselves on a large scale, it becomes difficult to follow the latest trends.”
He said that at the CMCC, BMW is able to work with the suppliers who will end up manufacturing the batteries. The suppliers can input on how each parameter of the manufacturing process, such as pressure, speed, humidity and cleanliness, will affect the quality of the overall battery.
“It’s important to make use of their know-how and to get the best our of our requirements and demands on the battery,” he said. “This is more of a development and research-related production [at the CMCC]. It serves as a pilot for the worldwide rollout. We’re doing to make a few hundred cells, then we’ll adjust the recipe and parameters, and again we’ll make a few hundred and test them. The cells that we build here will be used to upgrade the plant technology worldwide.”
Markus Fallböhmer, senior vice president of battery production, BMW said that having access to expert suppliers is one of the reasons that Parsdorf was chosen as the location for the CMCC. “We have European suppliers here in particular,” he said, “and we built up the plant technology together with them.”
But sharing the recipe for the battery cells with the suppliers isn’t showing BMW’s hand to competitors. Fallböhmer explains: “Just knowing the recipe helps them, but it doesn’t bring them to the final product. There are 3,000 interdependencies in the production. To get the final product you have to produce it in the same way as it was produced by us, that’s the challenge. Development, purchasing and production have to work closely together to understand and come up with this optimal product.”
Using technology to make scaling up more efficient
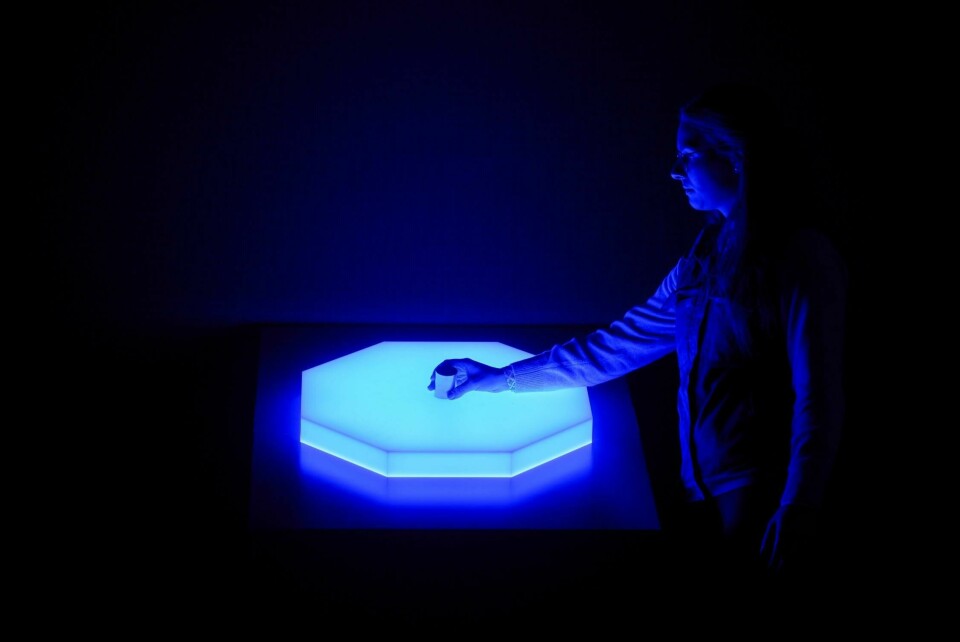
The use of technology, specifically digital twins, is helping BMW to keep track of these 3,000 different process steps and how they are adapting and developing them as they go along, and will also help replicate the recipe for its suppliers. As the chemistry used can change very quickly, digital twins can keep track of this and get that information to everyone involved in the manufacturing process, so everyone is keeping up with developments in real time. The digital twin was used to create and plan through this next generation battery cell, and will not only be used by the suppliers but also the storage facilities for the batteries.
Nedeljković said: “That’s where the planners can come together and optimise the processes so that we can design this whole thing as optimally as possible. It also helps us to pick up speed, because of the parallelisation of execution and planning on site. When everyone comes together and meets in this virtual world, the hardware processes are also being developed in parallel. It is an enormously powerful tool.”
Using a digital twin will also help control and manage battery assembly, as there are implications from the chemistry and cell design at CMCC on the overall battery production process on a global scale for BMW, affecting its battery plants in Woodruff, South Carolina, China, Mexico and others.