Reshaping the future: Innovations and developments in automotive production engineering: propulsion by Electrification and Digitalisation
Manufacturing engineering both powers and underpins production ecosystems across the industry. From BMW’s Munich plant to Porsche’s Zuffenhausen facility and Toyota’s expansions in Kentucky, we take a look at transformative initiatives shaping the industry.
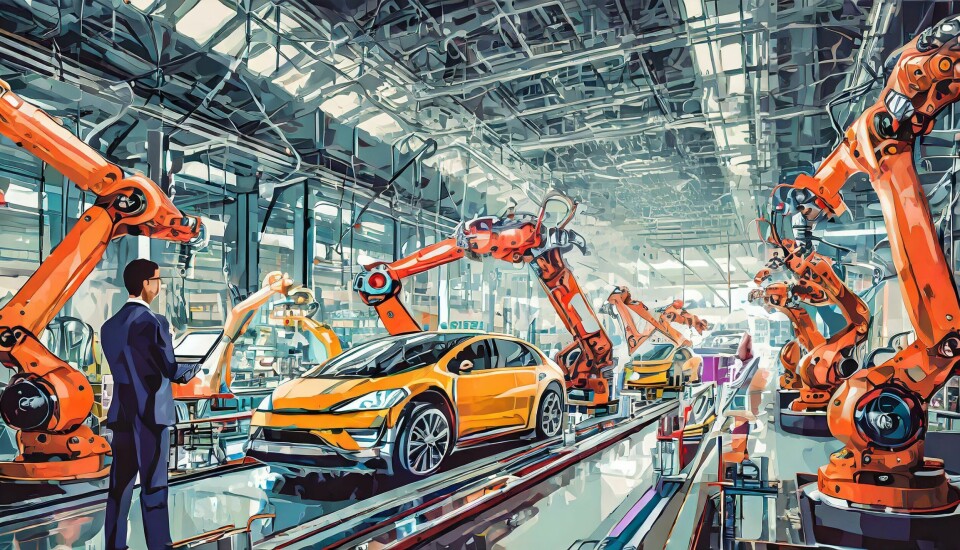
The fast pace of the automotive production world would not be possible without manufacturing engineering. With the rapid rise of electric vehicles (EVs), engineers are reshaping production processes to accommodate unique components such as advanced batteries and electric drivetrains, while ensuring efficient production and maintaining high quality standards. Sustainability has also become a key focus; and whether repurposing existing brownfield sites or designing new greenfield facilities, engineers are leading the charge towards a more sustainable and efficient automotive manufacturing framework.
Every time a new plant is constructed, manufacturing engineers lay the systemic and operational foundations, and already-operational vehicle production lines are models of complexity, with any development, change or improvement intrinsically adding complexity to complexity; with the catch being that the entire process needs to be streamlined.
With the ramp up to EVs and digitalisation acting as major catalysts, significant developments are underway in automotive production for both OEMs and Tier Suppliers, manufacturing engineering is playing an increasingly important role in this global transformation.
OEMs: centre stage in production engineering
Currently, BMW’s Munich plant is undergoing a comprehensive transformation towards full electrification; a huge undertaking for manufacturing engineering. The plant will exclusively produce electric vehicles by 2027, with the introduction of the Neue Klasse sedan, based on BMW’s new EV-focused architecture.
The transformation will cost €650 million ($715m) and aims to significantly enhance the century-old factory’s efficiency and digitalisation - said to attain close equivalency to that of a greenfield site. The plant has undergone extensive renovations, including the addition of new body, assembly and logistics halls; leveraging the same advanced processes and technology for EV production, to drive down costs and complexity.
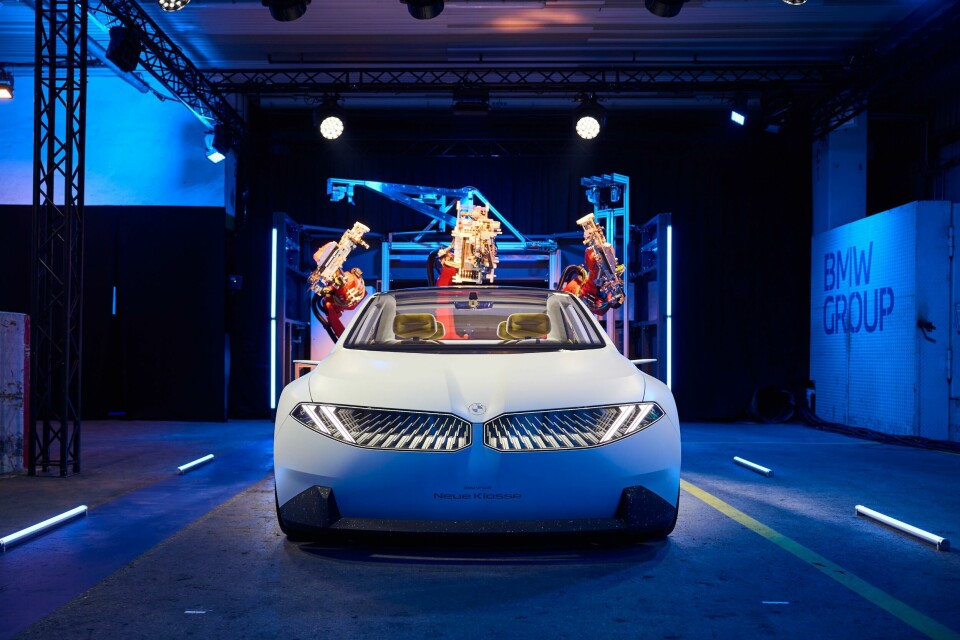
Despite construction challenges during this phase, production continued uninterrupted, with the plant outputting an average of 1,000 cars per day across various models. BMW anticipates a significant 25% reduction in manufacturing costs compared to 2019 levels, driven by fewer parts, greater use of recycled materials, and energy-efficient production processes. The plant’s revitalisation extends beyond Munich, with BMW’s global production network preparing for full electrification. Flexibility remains paramount, with plants prepared to produce multiple powertrains simultaneously, including potential integration of hydrogen fuel cell technology.
Over in Leipzig, BMW has invested €700 million ($751.4 million) over the past five years, to boost production capacity in preparation for the fully electric Mini Countryman. Leipzig’s production transformations include nearly 200 individual measures, described as ‘speed-up measures for individual technologies’, which are currently in the process of being implemented. This is one of the few examples where manufacturing engineering has meant that vehicle production lines “at a standstill”, due to the sheer volume and scope of upgrades to the production ecosystem.
The Leipzig facility is also emerging as a key hub for battery technology within BMW’s production network, recently adding two new production lines dedicated to the carmaker’s latest generation of high-voltage batteries. Additionally, there are now five cell painting lines and three module lines covering almost the entire battery production process chain. Leipzig aims to expand its production capacity to around 350,000 units per year, up from the current output of around 200,000 vehicles annually.
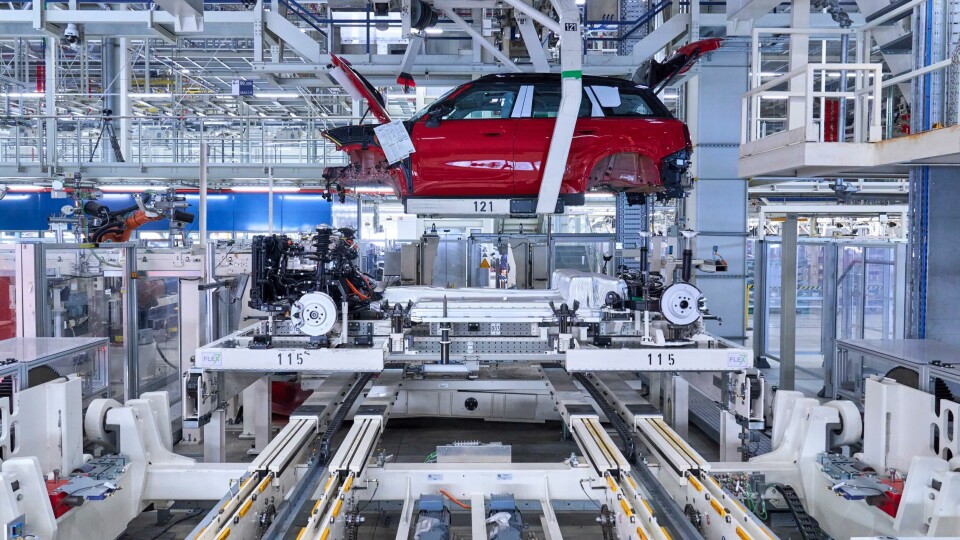
The carmaker’s electric vehicle strategy is expansive, and sees the construction of a new logistics centre for high-voltage batteries being built near Leipzig on a twelve-hectare site. The battery facility has an estimated cost of €100 million euros ($107.3 million), and will serve as a central distribution hub for electric vehicle components across BMW’s production network.
Beyond BMW, Porsche’s Zuffenhausen plant is undergoing a €250 million ($270.4 million) transformation. Embracing smart factory principles, the facility is integrating traditional and electric models on mixed production lines, aiming to enhance efficiency and quality through several upgrades. Automated guided vehicles (AGVs) are being introduced for producing two-door sports cars (both the traditional boxer engine model and the next-gen eSports models within the 718 series), replacing conventional assembly lines with a more flexible system called Flexiline. The shift, however, enables future production of vehicles with both combustion engines and electric powertrains on the same line.
The Zuffenhausen production workflow is being advanced with both new assembly processes and quality assurance stations. Emphasis is being placed on achieving first-time-quality through standardised quality checks and approval checkpoint points along the assembly line. A new light tunnel is also being incorporated for enhanced quality inspections. In terms of logistics at Zuffenhausen, the body shop areas are being expanded, with plans for a new building by 2025. High-bay racks over two floors are supplying vehicle parts for Taycan and sports car production, with a fully automated high-bay rack already in operation since September 2023.
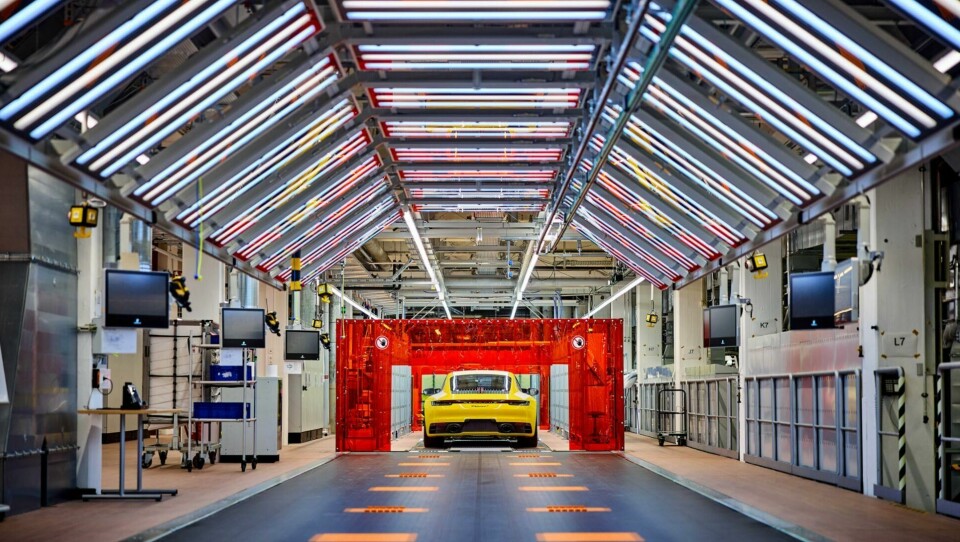
Integration efforts are underway for new generations of vehicles. Assembly for electric Macan motors is being integrated into the existing engine plant, originally established for V8 combustion engines, anticipating production of the new generation Porsche Macan in Leipzig in 2024.
Over in the US, Japanese automaker Toyota is expanding operations at its Kentucky plant with a $1.3 billion investment to introduce battery electric vehicle (BEV) production into the facility. The investment will support the assembly of a new three-row BEV SUV specifically designed for the US market. With this addition, the total investment in the Kentucky plant reaches nearly $10 billion. Additionally, a battery pack assembly line will be incorporated into the facility, with batteries sourced from Toyota Battery Manufacturing North Carolina.
Toyota also plans to invest $5.9 billion in its lithium-ion battery plant in North Carolina. A significant portion of this investment, $2.5 billion, will be directed towards sustainability measures, while $2.1 billion will support infrastructure enhancements for future expansion. Since 2021, Toyota has announced a total of $17 billion in new investments in its US manufacturing operations to advance its electrification efforts.
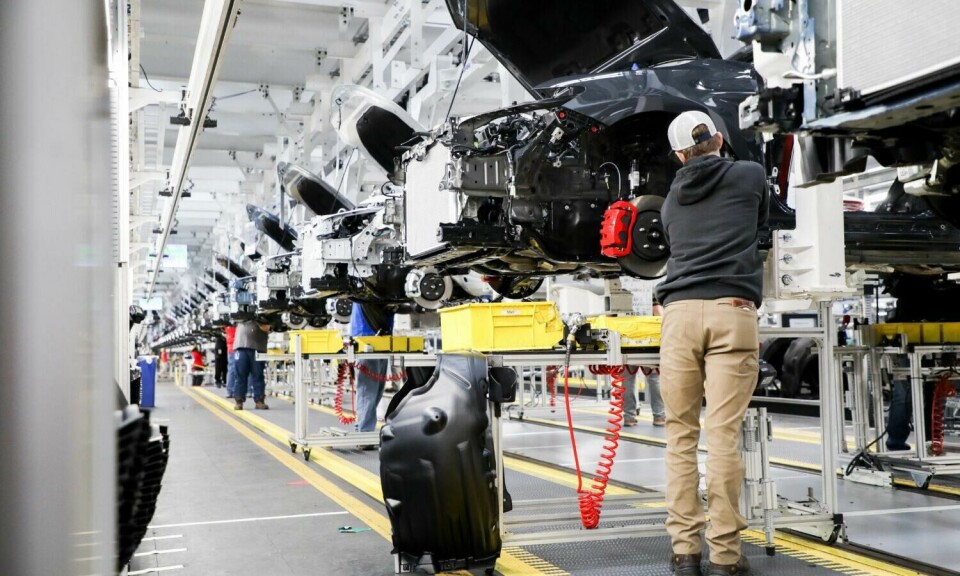
Manufacturing Engineering: The tier-supplier connection
Automotive Cells Company (ACC), backed by Stellantis, Mercedes-Benz and Saft (a subsidiary of TotalEnergies), has secured €4.4 billion ($4.7 bn) for the construction of three gigafactories across Europe. These gigafactories will be located in Germany, Italy, and France, expanding ACC’s production capabilities beyond its existing facility in Billy-Berclau, France. The funding will facilitate the development of four additional production blocks, with expansions planned for the existing facility in Douvrin, France, and two new blocks to be built in Italy and one in Germany.
ACC’s existing gigafactory in France, operational since June last year, has a production capacity of 56,000 battery cells per day, equivalent to powering 200,000 to 300,000 vehicles annually. The company plans to replicate this success in Kaiserslautern, Germany, and Termoli, Italy, with initial production capacities of 13.4 GWh and eventual expansions to 40 GWh, enabling the production of over 600,000 electric vehicles per year.
The push for European gigafactories has gained momentum, with companies like CATL and Volvo-Northvolt also investing in production facilities. Additionally, Chinese battery makers, such as Farasis, are entering the European market, with plans to regionalize manufacturing through ventures like the Siro gigafactory in Turkey.
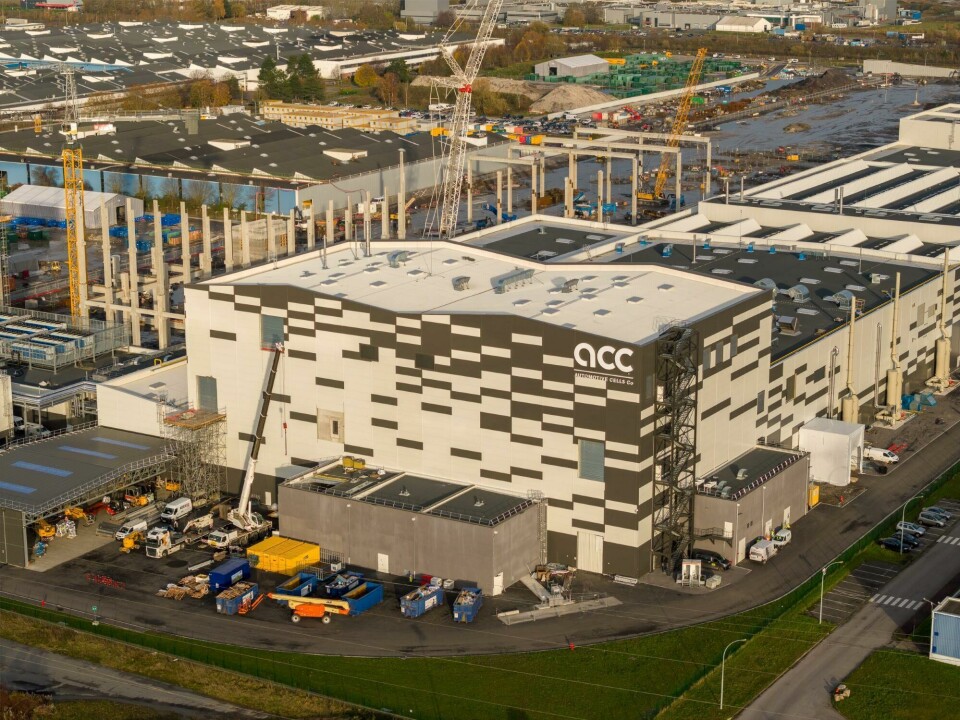
Tata Passenger Electric Mobility (TPEM), a subsidiary of Tata Motors, recently began production of passenger vehicles at its newly established facility in Sanand, Gujarat. The inauguration was marked by the rollout of the first Tata-branded vehicle, the Nexon, from the facility on the west coast of India.
Acquired from Ford India in January 2023, spanning 460 acres and situated in the industrial hub of GIDC Sanand, the new facility is Tata Motors’ second plant in Gujarat dedicated to manufacturing both Internal combustion engine and electric vehicle models. The facility underwent significant retooling and technological upgrades across several key areas, including Press Shop, Weld Shop, Paint Shop and Assembly Shop, equipping it with high levels of automation and technology for precision manufacturing.
Several major OEMs, including Hyundai and Maruti Suzuki, have announced investments and expansion plans in India, reflecting the expansion of manufacturing engineering projects in the region.