Green Revolution: How renewable energy is fuelling sustainable automotive manufacturing
Adopting renewable energy in automotive production requires a comprehensive strategy, integrating solar, wind, biogas and electric solutions to drive sustainability and mitigate environmental impact effectively. OEMs, strategies and technologies are converging on different approaches to achieve sustainability goals across regions. Here are some notweworthy projects to keep an eye on…
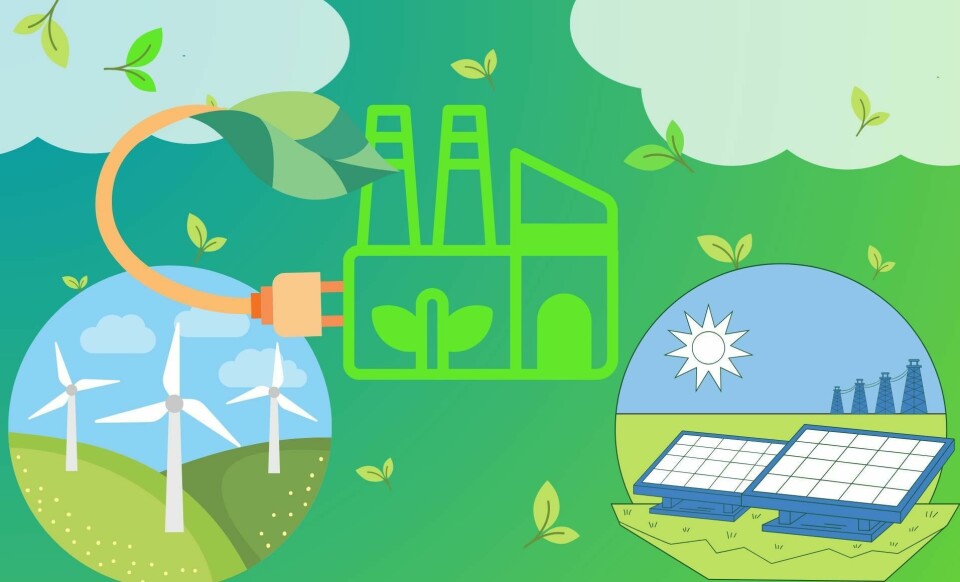
What does a genuine effort towards sustainable automotive manufacturing look like? As decarbonisation efforts were extended beyond Scope 1 (emissions directly from a company’s operations), to include Scope 2 (those generated indirectly from purchased energy) and Scope 3 (those of all n-tier suppliers across the value chain); automotive production realised that genuine sustainability efforts demand a holistic approach.
For automotive OEMs and tier suppliers, this means that the carbon footprint produced by finished vehicles is only only a small fraction of the equation. The energy output generated during production is essential to the entire decarbonisation formula. Put another way, what can an OEM profit if it creates green vehicles using coal-black processes?
The automotive manufacturing sector is now increasingly turning to renewable energy sources such as wind, solar, biogas and electricity to underpin its operations, as the industry shifts towards sustainability and carbon neutrality.
However, to get a clearer picture, to what extent this can be achieved in the face of various geopolitical and economic pressures is as yet undecided.
“One challenge moving forward with renewables will be a slowdown (or even reduction) in global production capacity,” says Kevin Tynan, Senior Automotive Analyst at Bloomberg Intelligence. But the industry seems undeterred, and is combating the carbon question on multiple production fronts.
Solar Energy in production: Ford and Audi get the green light
Solar energy is at the forefront of the renewable energy portfolio of automotive manufacturers due to its scalability, relative ease of integration and measurable impact on carbon emissions. By definition, solar energy obviously relies on the sun. For example, Ford’s renewable production operations serve as a prime example of this trend, with the carmaker’s Cologne plant running entirely on renewable energy since 2008. In Cologne, solar installations both power all the plant’s renewable energy needs, and are all sourced from local provider, RheinEnergie, and certified by regional third-party, TÜV Rheinland.
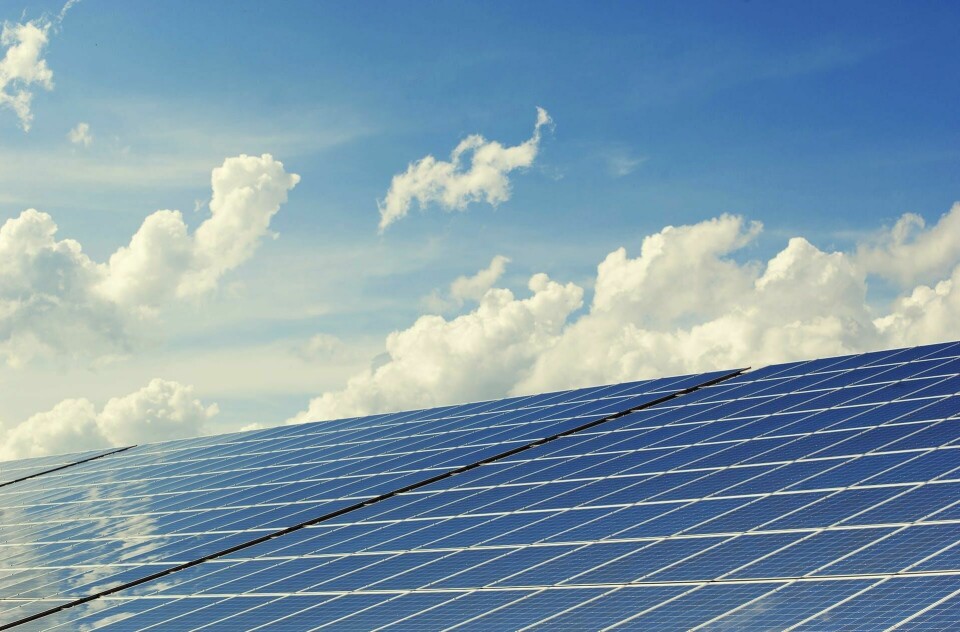
Ford’s initiatives in China and South Africa work to reduce reliance on conventional energy sources by curtailing emissions through substantial solar installations. Ford’s Hangzhou Plant in China has been equipped with a solar photovoltaic system since 2019; a system which currently supplies approximately 25% of the plant’s total power needs, and reduces carbon emissions by an impressive 10,000 tonnes. Additionally, in South Africa, Ford’s Silverton plant receives 35% of its electricity needs from solar panels.
The question of whether renewable energy sources supporting production initiatives should be baked-in from the outset - or implemented mid-operation - is an important one. After all, the point is to lower the carbon footprint of production outputs - and to do so without upsetting operations, (which potentially come with their own carbon cost).
Tynan comments: “Changing the energy solution for the facility will be much easier to do on a greenfield plant, than it will be to retrofit. If those greenfield plans pause for a time – for fear of overbuilding capacity, adoption rates will drag.”
But installations continue on the OEM front. Ford’s Almussafes plant in Valencia, Spain is also home to an ambitious project aimed at increasing solar energy generation for production operations. Initially boasting a 4.64MWh per year solar installation, the company announced an augmentation by an additional 3.76MWh per year. The OEM aims to push the installation’s peak capacity to nearly 10MW by this year, which if successful, would significantly reduce its operational reliance on non-renewable energy sources. Since the beginning of 2022, the Almussafes plant has procured all its electricity from renewable sources.
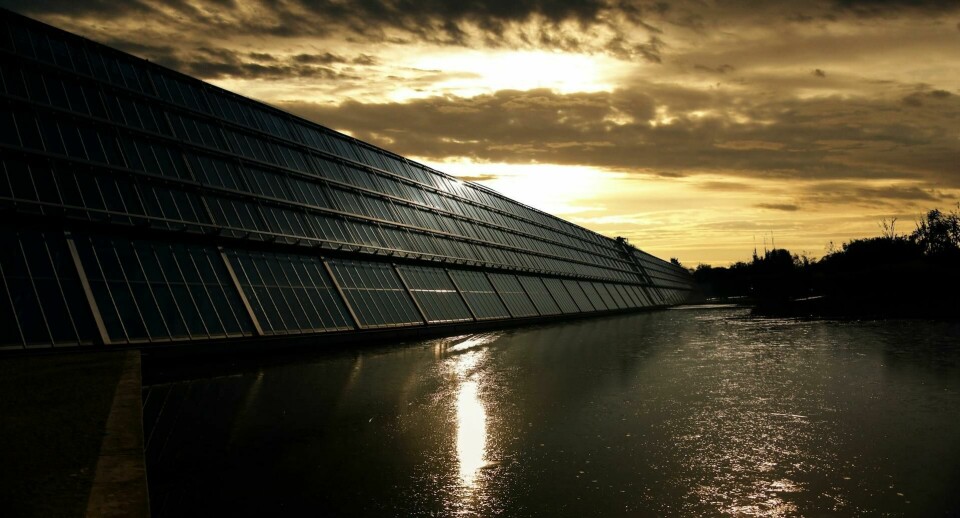
Meanwhile, Audi, another automotive giant, is no stranger to the green (and solar flare) production transformation. The carmaker has systematically transitioned its production sites to renewable electrical energy since 2012, beginning with its Ingolstadt site.
Presently, Audi proudly procures electricity solely from renewable sources for vehicle production across all its locations. A noteworthy example is the Brussels facility, which houses the largest photovoltaic plant in the region. This solar power behemoth generates approximately 9,000 megawatt-hours annually, impressively contributing to the plant’s energy requirements and marking it as the world’s first certified CO2-neutral large-scale production site in the premium segment since 2018.
Audi’s Győr site in Hungary further exemplifies the carmaker’s solar commitment, hosting Europe’s largest photovoltaic rooftop system on an area of around 160,000 square metres.
Wind Energy: harnessing the breeze
Though solar power is often highlighted, wind energy plays another crucial role in the industry’s transformation towards renewable energy manufacturing. The automotive sector’s engagement with wind energy, through direct generation or power purchase agreements, demonstrates another strategic and creative renewable energy infrastructure aimed at leveraging low operational costs and substantial output.
Nissan is channelling a significant portion of its £3 billion investment into the EV36Zero hub, a cornerstone project centred around its Sunderland plant in the UK, with a special focus on wind energy as a renewable power source for its operations. The investment is part of Nissan’s broader vision to make all its new cars in Europe fully electric by 2030 and includes the creation of a third gigafactory to support the production of its three EV models: the Qashqai and JUKE crossovers, and the next-generation LEAF.
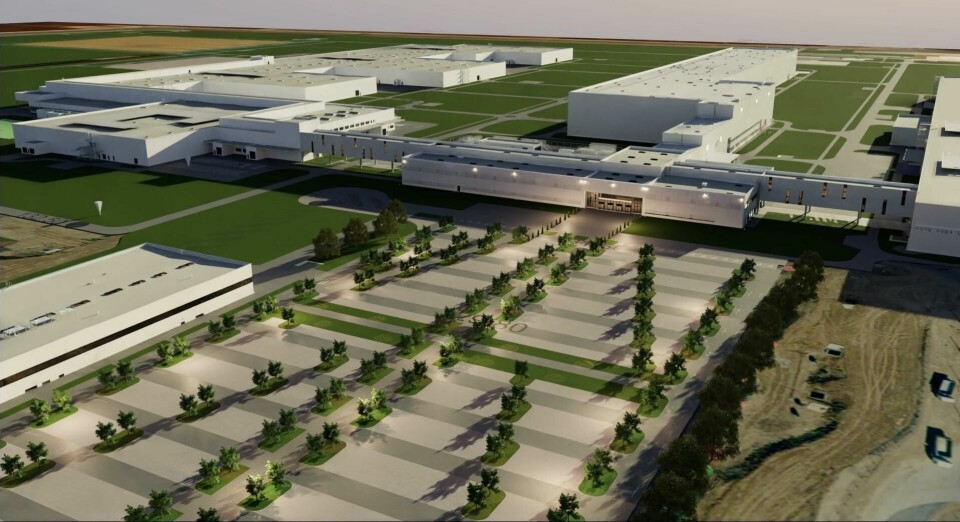
Central to this initiative is the EV36Zero Microgrid, a pioneering energy system that integrates wind farms alongside other renewable energy solutions. This microgrid is designed to supply 100% renewable electricity not only to Nissan but also to its neighbouring suppliers.
Milan Nedeljkovic, Member of the Board of Management of BMW AG, recently stated that wind ensures the supply of renewable energy at the carmaker’s Debrecen plant. He said: “Debrecen is a very good example of the implementation of our sustainability strategy. We consistently use technologies that completely dispense with gas.”
The renewable energy push is tied closely to other technological processes such as automation. But weighing the two against each other, there is still a lot of renewable energy ground left to plumb.
Tynan says: “while there are not significant portions of the new vehicle manufacturing process left to be automated – (see Elon Musk’s ‘Excessive automation at Tesla was a mistake. Humans are underrated’ comments) – there is opportunity for increased use of renewables in the production process.
“But the growth will come from the transition to new energy technologies and not from a revolution in manufacturing techniques.”
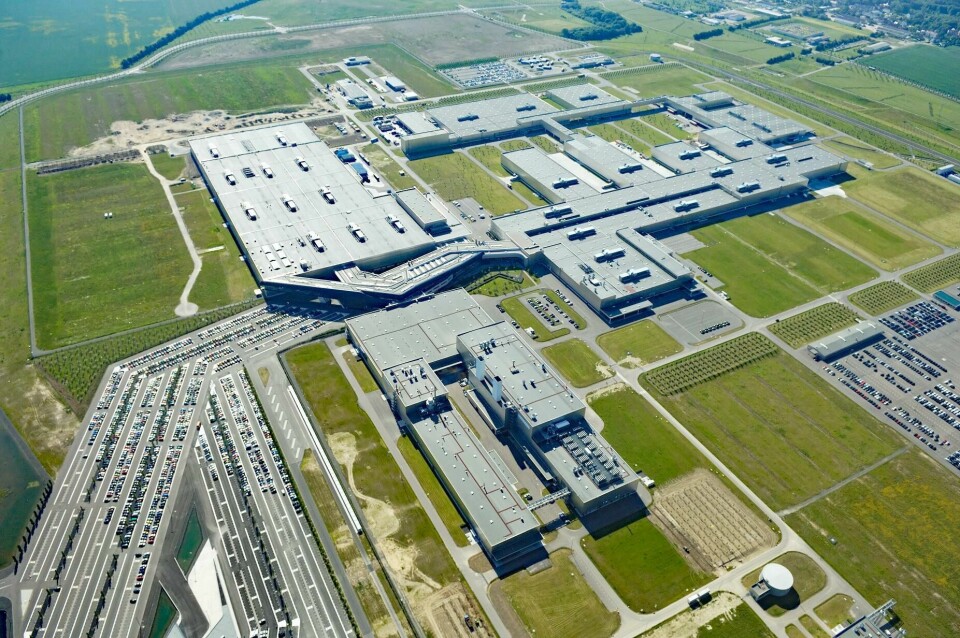
As for OEMs, BMW’s Leipzig plant is another example of clear commitments to sustainability efforts, actively integrating renewable energy sources into its automotive production processes. Strategically situated directly on the plant’s premises are four towering wind turbines, each standing at an impressive height of 190 metres. These turbines are not just architectural feats but are crucial to the plant’s sustainable energy strategy. In the year 2021 alone, these wind turbines successfully generated a significant 21.9 gigawatt-hours (GWh) of electricity purely from wind energy.
Biogas for production: realities and potentials
In addition to solar and wind energy, the automotive industry is also exploring biogas and other renewable sources to address specific challenges like waste management and ensuring a continuous power supply. These alternative renewable energies provide robust solutions to enhance the sustainability quotient of many manufacturing operations.
Back in South Africa, BMW’s Rosslyn plant actively sources part of its energy from a nearby biogas plant, known as Bio2Watt. BMW plans to use the South African base as “a pilot market for innovations”, and has stated that the Rosslyn plant will be “a blueprint for social, environmental and economic sustainability”. This may point to biogas in vehicle manufacturing becoming more ubiquitous across wider production operations.
The carmaker has demonstrated an innovative and longstanding relationship to harnessing biogas which it derives from local landfills to power and heat its facilities, which it has been doing for the past two decades. This renewable approach has resulted in a substantial reduction of over 9,200 tonnes of CO2 emissions annually, equivalent to eliminating emissions from vehicles driving over 23.5 million miles each year.
Currently, approximately 20 percent of the Spartanburg plant’s energy needs are met by landfill-derived biogas. BMW’s partnership extension with Ameresco Inc. is ensuring the continued utilisation of biogas, expected to reduce an additional 74,000 tons of CO2 emissions over the next eight years.
By capturing and repurposing methane from landfill gas, BMW mitigates its environmental impact while also realising significant cost savings and promoting a cleaner, more sustainable manufacturing process.
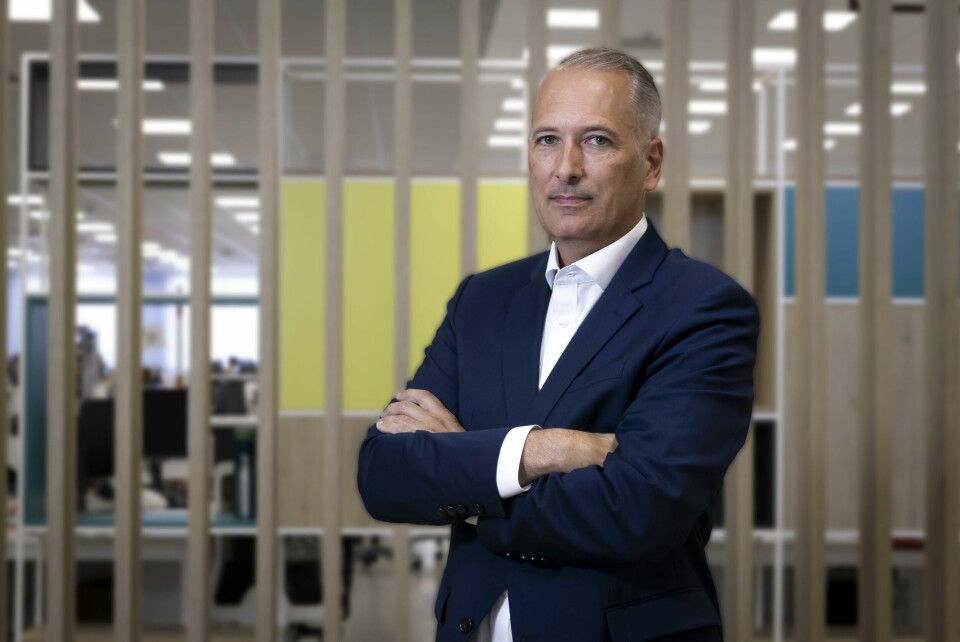
Then there are projects in the production pipelines. Markus Haupt, the Executive Vice President of Production and Logistics at SEAT, S.A., recently underlined the role of biogas in making the company’s production operations more sustainable.
Haupt discussed how using biogas will allow Seat to quickly shift many of its processes towards more environmentally friendly practices.
He also mentioned ongoing talks on the possibility of completely phasing out natural gas use across Europe, highlighting the broader sustainability context in which Seat is considering biogas for its production operations.
The Gigafactory factor and renewable energy integrations
The emergence of gigafactories for battery production is closely tied to the journey towards renewable energy integration. Gigafactories are not merely about scaling battery output; they epitomise the industry’s shift towards green manufacturing. For instance, Northvolt’s selection of Quebec for its gigafactory; benefitting from the region’s hydroelectric resources.
The Northvolt Six Gigafactory, situated in Saint-Basile-le-Grand and McMasterville suburbs of Montreal, will be a pioneering lithium-ion battery facility with an annual cell production capacity of 60 GWh. The project integrates cathode active material manufacturing, battery production and sustainable facilities, fostering a closed-loop, circular production process.
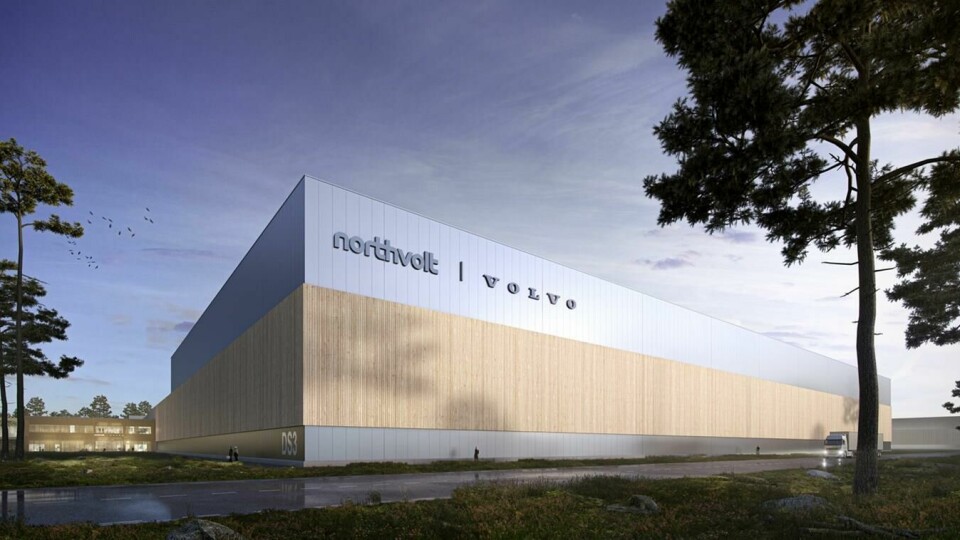
The initial phase, targeting 30 GWh of cell production, is slated to begin this year, with the first battery deliveries anticipated in 2026. This phase includes cathode manufacturing, cell assembly and sustainable production.
Northvolt’s CEO, Peter Carlsson, sees this move as a significant step towards establishing a novel, sustainable model for battery manufacturing, tapping into the extensive hydroelectric power available in Quebec.
But North America may be particularly challenging in terms of renewable energy choices. Many variables feed into the way OEMs and Tier Suppliers decide on setting up shop at their locations; not least the fiscal impacts of geographical selection in the vehicle production race for sustainability.
Daniel Harrison, Automotive Analyst at Ultima Media, comments: “EV battery gigafactories are highly energy intensive. Furthermore, in some parts of the world battery regulations, rules of origin, and resulting tariffs and/or purchase subsidies are contingent upon the carbon footprint of EV battery production, sometimes detailed within a ‘battery passport’.
”Therefore,” he says, ”when new gigafactory locations are being decided, increasingly the local access to cheap renewable energy is a growing, and decisive factor.”

Tynan adds: “Global auto production – specifically in North America – is not concentrated, but reasonably fragmented across the landscape, making the achievement of scope, scale the best technology choice a little more challenging.”
Paolo Cerruti, co-founder of Northvolt, envisions Northvolt Six as a means to meet North American demand for sustainable batteries. With its commitment to 100% renewable energy and raw materials, Northvolt is set to make Northvolt Six an example of sustainable investment, reinforcing the global shift towards eco-friendly battery production and seeking to position Quebec as a key hub in the EV-driven, renewable energy world.
Tata’s bold move to invest £4 billion in its battery cell gigafactory in the UK, Somerset, marks another key moment for renewable energy and production operations. The endeavour, undertaken through its subsidiary Agratas, will power the automotive sector’s transition to electric mobility while anchoring its own business, Jaguar Land Rover (JLR), as a key client.
The gigafactory’s primary objective is to produce 40 GWh of battery cells annually, serving Tata Motors and JLR across the UK and Europe. The venture represents Tata’s first battery plant outside India and is set to commence production in 2026. As a renewable manufacturing facility, Tata aims to maximise renewable energy sources, with aspirations of achieving 100% clean power, thereby reducing environmental impact.
JLR’s ‘Reimagine’ strategy, initiated in 2021, has seen substantial investments in supply chain operations and facility upgrades to prepare for electrification. By integrating battery cell production into existing plants like the one in Wolverhampton, JLR ensures a stable supply chain while enhancing manufacturing and operational efficiency.
The future of production looks green
Integrating renewable energy into automotive manufacturing processes presents various challenges, including technological and infrastructural barriers, regulatory hurdles and economic considerations. However, the transition to renewable energy offers significant opportunities for renewables in vehicle manufacturing.
Automotive manufacturers continue to innovate and adopt green energy practices, with the integration of renewable energy sources in production processes becoming evermore central to the sector’s operations.