The state and stipulation of automotive production: Retrospect 2023 to prospect 2024
Using 2023 as a launchpad into the coming trends of 2024, we take a dive into the coming automotive production trends set to shape the industry
2023 was a bustle of several trends that saw vehicle manufacturers quickly adapting their infrastructures to keep up with and even pre-empt disruptions in one form or another. The automotive industry addressed growing carbon emissions regulations by expanding its adoption of alternative powertrains and prioritising sustainable value chains and eco-friendly materials. There was a notable move towards digitalisation, allowing OEMs and tier suppliers to assess and enhance production processes, driven by a heightened focus on sustainability and significant investments in electric vehicle production and battery technologies. But our eyes are on the year ahead. What does 2024’s vehicle manufacturing look like? and what clues can 2023 give us about it?
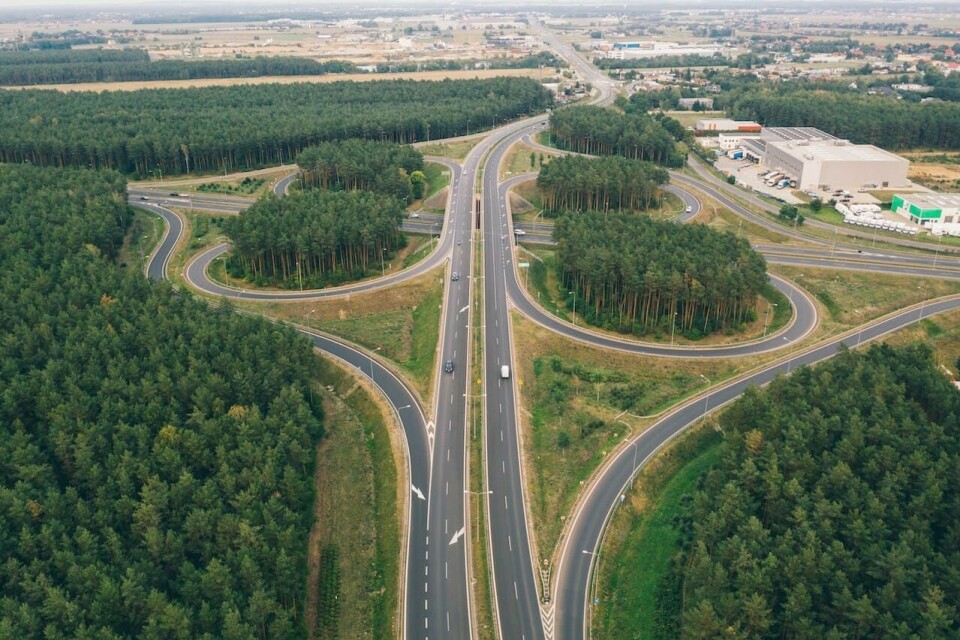
Sustainability
2023 was marked by a confluence of factors driving sustainability in automotive production. The industry is responding to increasingly stringent carbon emissions regulations through the adoption of alternative powertrains and fuel cells and baking-in manufacturing-led circular economies through reuse and recycling.
One of the interesting trends has been the industry’s focus on reducing carbon emissions by implementing innovative solutions such as battery recycling and biodegradable components. 2023 showed us that the industry is undergoing a transformative shift towards sustainability by embracing bio-based materials such as flax, hemp, kenaf and jute. These natural fibres offer durable and lightweight alternatives for various vehicle components, from dashboards to electric vehicle batteries.
Last year, we saw that leading automakers like Renault, Volkswagen and Toyota are now incorporating bio-based materials into their vehicles. For instance, Renault’s electric Scenic E-Tech features a dashboard cowling made from 43% bio-sourced kenaf and a 51% bio-sourced steering wheel cover. Ford has been a pioneer in this shift, using soy-based foam, hemp and agave fibre, emphasising the environmental and cost benefits of bio-based materials. In motorsport, Swiss natural fibre company Bcomp has collaborated with BMW to introduce bio-based materials in racing cars, showcasing the potential for innovation and durability. The success of such materials in motorsport has led to mainstream collaborations, with Bcomp delivering natural fibre composites for Volvo’s EX30’s dashboard and door trim. Companies like Stora Enso and UPM Biochemicals are also contributing to the industry’s sustainable efforts.
Stora Enso’s lignin-based solution, Lignode, offers a sustainable alternative to graphite in electric vehicle batteries, addressing concerns about the graphite supply chain. UPM Biochemicals focuses on renewable functional fillers derived from wood-based sources, offering sustainable alternatives for various automotive applications. The industry’s adoption of bio-based materials aligns with the concept of “dematerialisation,” emphasising the use of minimal material to achieve weight reduction and enhance energy efficiency.
The success of sustainable materials and their integration into mainstream automotive applications signals a promising future for sustainable and eco-friendly manufacturing in the automotive production industry.
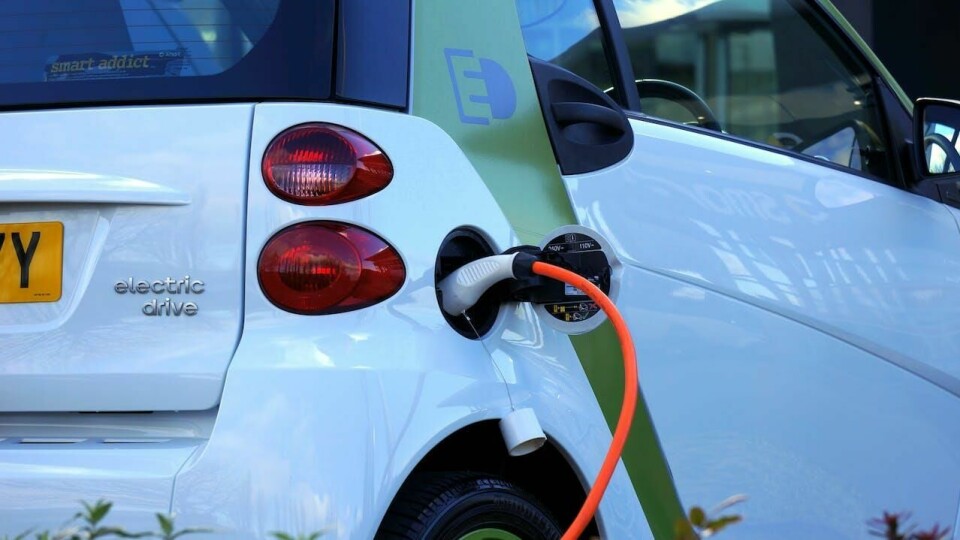
Electric Vehicles (EVs)
2023 also reaffirmed that there are several key factors stimulating the rise of EVs in automotive manufacturing. The global emphasis on sustainability and environmental awareness is propelling the rapid growth of the electric vehicle industry with many countries setting ambitious targets to phase out internal combustion engine vehicles and promote the manufacturing of EVs.
Auto manufacturers are actively making substantial investments in EV production and battery technology, with many committing to transitioning to exclusively electric production by 2050.
As an example, the Ford Motor Company celebrated its 120th anniversary last year, with the Dearborn Truck Plant emerging as a pivotal player in the automotive giant’s ambitious transition towards electrification. This Michigan manufacturing hub stands as a testament to Ford’s commitment to both tradition and innovation, notably exemplified by its production of the iconic F-150 pickup and the forward-looking electric F-150 Lightning. Under the leadership of Plant Manager Corey Williams, the Dearborn Truck Plant has undergone a transformative journey, embracing the leap towards EVs
Launched in 2022, the REVC symbolises Ford’s proactive stride into EV production, marked by cutting-edge technologies and sustainable practices - an overlap that can’t be ignored. The plant’s emphasis on quality and efficiency aligns with Ford’s broader vision, including plans to increase hybrid production and enhance ICE and hybrid manufacturing processes at the Dearborn Truck Plant.
The broad picture in 2023 highlights that the transition to EVs will necessitate a complete overhaul of automotive production processes, manufacturing technologies and the automotive supply chain itself. As a result, the future of electric vehicle manufacturing is intricately linked to the industry’s capacity to adapt and innovate. This transition is projected to continue gaining momentum in the year ahead.
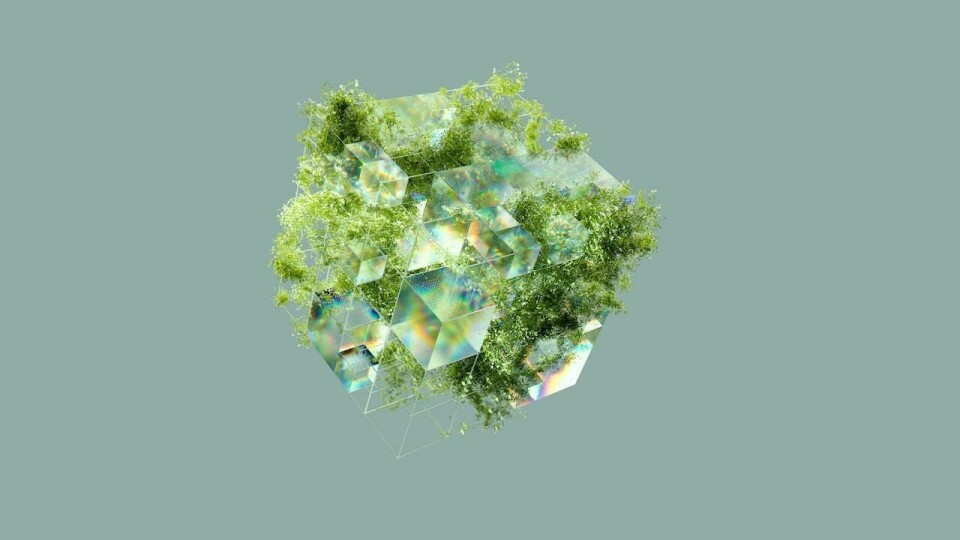
Digitalisation and the metaverse
2023 also revealed that the imperative to enhance efficiency, offset disruptions and prepare for the future is driving the digitalisation of automotive production. The automotive industry is actively adopting digital tools and technologies to streamline manufacturing and retailing processes, reduce production costs and extend its reach to a broader customer base.
This shift towards digital transformation aims to boost productivity, flexibility and customisation, ultimately benefiting both manufacturers and consumers - with demand ultimately reshaping the supply and production infrastructure.
This was seen last year with BMW pushing to lead the automotive industry’s digital transformation by designing its upcoming Debrecen production plant in Hungary entirely through virtual simulation. The plant, slated to produce BMW’s next generation of all-electric vehicles, is leveraging NVIDIA’s Omniverse system, a breakthrough in virtualisation and artificial intelligence (AI). Virtualisation and AI are allowing for ecosystems that accelerate planning processes by enabling global teams to collaborate in real-time.
The partnership with NVIDIA facilitates real-time digital twin simulations, optimising layouts, robotics and logistics systems virtually.
This digital-first approach offers tangible benefits, allowing OEMs like BMW to validate and optimise manufacturing processes before physical construction begins. The system contributes to near-zero loss launches, minimising the need for rework during production. Omniverse’s ability to detect planning mistakes and integrate diverse data enhances decision-making and accelerates the planning process.
The implementation of Omniverse aligns with BMW’s broader initiative to make the software pervasive across its global operations. Beyond immediate applications in Debrecen, BMW also aims to use virtual factory models to generate synthetic data for AI training, enhancing digital operations.
Digitalisation and the metaverse are allowing many OEMs to further cut costs and improve efficiencies related to EV production. For example, Renault recently announced its ambitious plan, “Re-Industry,” aimed at fundamentally reshaping its industrial landscape. The overarching objective of this ecosystem is to achieve a substantial reduction in production costs, targeting a 30% decrease for internal ICEs and an even more ambitious 50% for EVs by 2027. Renault characterises Re-Industry as a comprehensive 360° transformation plan. The cornerstone of the transformation is Renault’s Industrial Metaverse; a digital ecosystem designed to enhance competitiveness and reshape its vehicle production environment. The Metaverse is recognised as playing a key role in fostering agility within the industrial base, facilitating a quicker response to customer expectations.
The OEM’s digital manufacturing plans include reducing vehicle development times from three to two years, and is a persuasive production argument for the metaverse being a peak maturation of digitalisation as a whole. The automotive industry anticipates continued growth in the use of digitalisation, with substantial projected investments in digital technologies and digitalisation now deemed to be a vital strategy for automotive manufacturers to adapt to evolving market dynamics, enhance competitiveness and address future challenges.
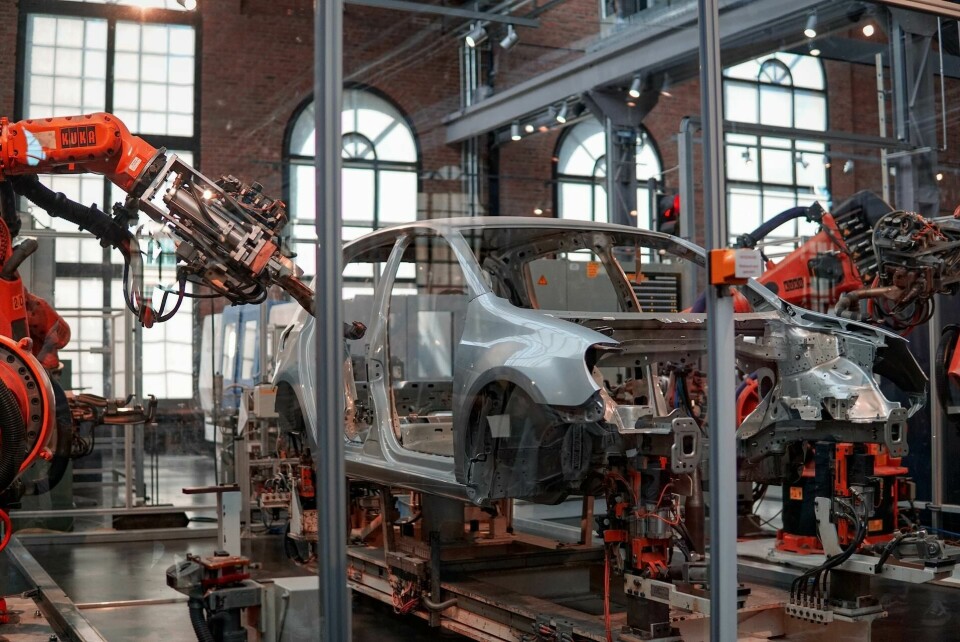
Manufacturing engineering
Manufacturing engineering is actively shaping the various processes essential for developing, assembling, testing and delivering the next generation of vehicles in automotive production. This dynamic field, serving as a critical bridge between research and development (R&D) and manufacturing, involves process and assembly development, with the adaptability and balance required to meet the evolving needs of both R&D and manufacturing being particularly crucial in an industry where requirements can swiftly change.
2023 demonstrated how manufacturing engineering has been playing an important role in efficiently managing change and increasing flexibility to reduce lead times. But its effects are far-reaching.
For example, Audi’s manufacturing engineering, led by Jörg Spindler, is spearheading the company’s digitalisation and innovation efforts, driving advancements in production planning, battery production and emissions reduction through data utilisation.
Audi’s groundbreaking Edge Cloud 4 Production is the first of its kind globally, allowing virtualisation of the OEMs control systems. Beyond innovation, Audi’s systems allow for the prioritisation of sustainability by targeting energy savings and emission reduction. Initiatives include transitioning paint shops to electric ovens and phasing out pneumatic energy, aligning with Audi’s goal of carbon-neutral plants by 2025. Embedded in Audi’s ’360factory’ strategy, Spindler’s team plays a pivotal role in global electrification goals by 2029, phasing out ICE vehicles by 2033, and halving factory costs. The strategy prioritises maximising productivity and updating existing plants, emphasising sustainability, cost-effectiveness, flexibility, and employee appeal.
In the transition to electric vehicles and batteries, Audi’s increased digitalisation and virtual planning is crucial, as is leveraging data and AI-based algorithms for production and maintenance decisions.
2023 was proof that the automotive industry’s growing emphasis on digital tools and technologies, such as virtual development, is driving innovation and efficiency, with virtual development in manufacturing engineering emerging as a fundamental aspect of the industry’s evolution.
The pursuit of efficient engineering in automotive manufacturing is further evident in the adoption of cold forming to reduce scrap material and offer faster lead times. This again feeds into the broader trend towards sustainability, waste reduction and cost-saving initiatives in the automotive sector.
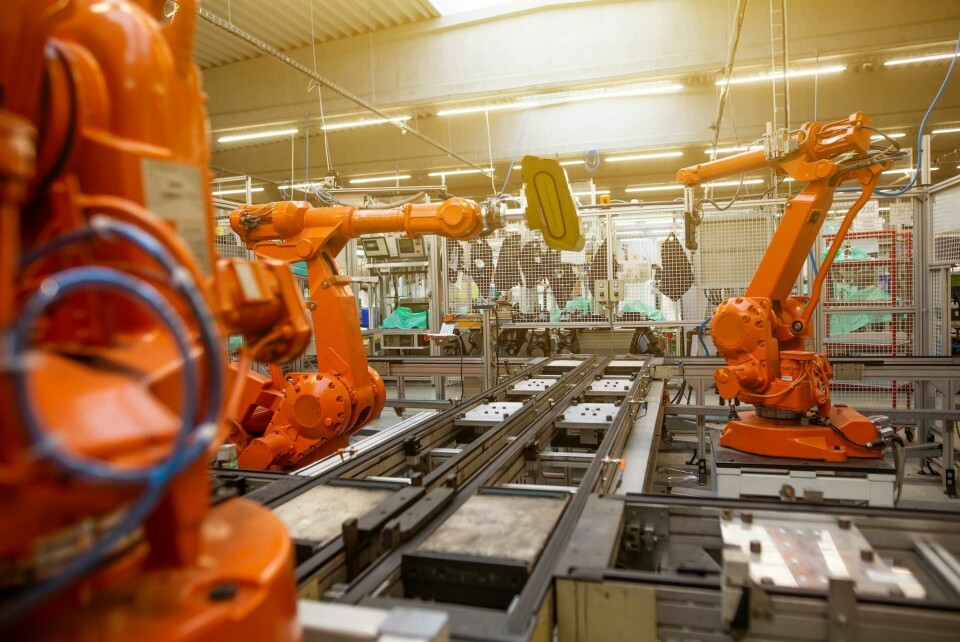
Further predictions for 2024: simultaneous engineering
In 2024, the automotive manufacturing landscape is poised for a significant transformation with the widespread adoption of simultaneous engineering, propelling an acceleration in the design, development and commissioning of production lines. As EV competition intensifies, major OEMs, including BMW, are at the forefront of this paradigm shift. A pivotal case study emerges from the collaboration between NIO and Comau, showcasing their successful acceleration of new e-motor line commissioning.
This collaborative effort involves a simultaneous engineering approach, where production line design and development run parallel to the creation of new EV products. Notably, Comau’s high-performance, automated production lines for assembling electric drive systems (EDS) for NIO underscore the seamless integration of simultaneous engineering methodologies.
The use of AI-powered tools and close collaboration between the companies are instrumental in meeting tight deadlines and ensuring line efficiency without compromising product quality.
2024 heralds a manufacturing future where simultaneous engineering, virtual simulations and AI-powered tools redefine production line efficiency. Notably, strong partnerships, as exemplified by NIO and Comau, reflect a deeper level of trust, enabling parallel project progression and reducing impacts on development times. This transformative approach is reflective of a broader industry trend, where suppliers actively participate in early stages of new vehicle projects to optimise manufacturing solutions and streamline the transition to EV production.
The success story of NIO and Comau sets the stage for a dynamic and collaborative future in automotive manufacturing, navigating challenges and capitalising on the benefits of simultaneous engineering methodologies, and if these predictions bear fruit, which we are sure they will - the year ahead is going to be full of action.