On advanced robotics, skills and training: “Machines can’t do everything”
Next-generation vehicles require new production processes, above all in automation, digitalisation and employee qualifications. Carolin Platz from the Auto-Motive Academy and Jörg Reger from automation expert ABB discuss the intersection of major topics in scaling up EV manufacturing.
At this year’s automatica trade show in Munich, AMS partnered with its German sister title, Automobil Produktion, to host a panel discussion on changing skills in automotive manufacturing in the era of electrification and artificial intelligence. Below is an edited recap of the discussion, moderated by Götz Fuchslocher.
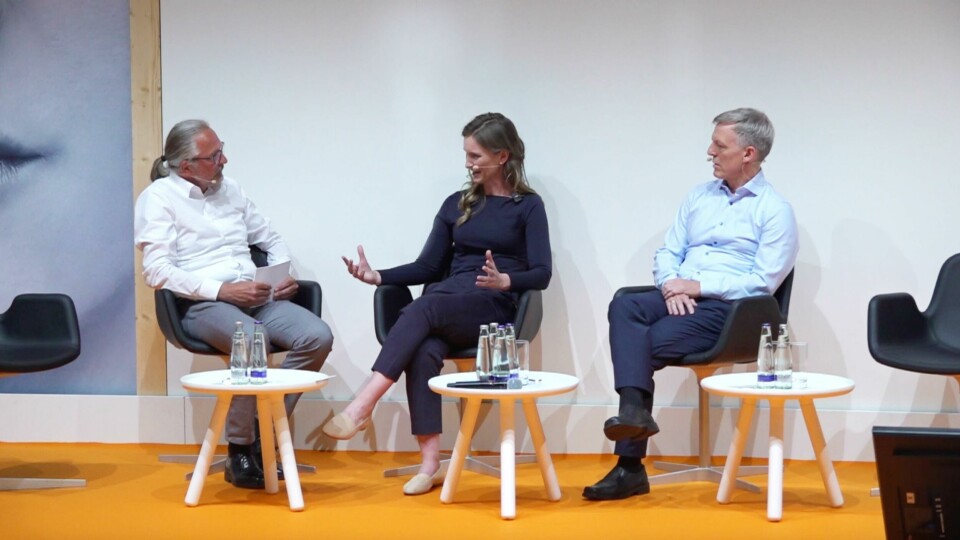
Ms Platz, at the Auto-Motive Academy you combine ‘the advantages of the dual study [work and study] university system with those of an independent educational institution, for maximum flexibility and sustainability’. How would you describe your work?
Carolin Platz: Our Auto-Motive activities are essentially based on three building blocks. In essence, we are concerned with creating platforms for a sustainable exchange of knowledge and experience. To this end, we regularly bring together scientists, industry experts and top decision-makers. The automotive industry is in the midst of a profound transformation. In this context, we are evaluating, among other things, which competencies the industry needs to build up, and this is precisely where we are starting with our cross-university academy concept as a second building block. In doing so, we interlink experts from science and research who are well acquainted with the dual study concept, so that employees can continue their education at the cutting edge without having to leave their working environment.
In the third building block, we look at how we can ensure continuous training for employees that does justice to the industry’s new, significantly shorter product cycles and takes into account the needs of individuals. In this context, we are increasingly focusing on the possibilities of digitalisation and generative AI, which we are evaluating, researching and developing in our own lab in Munich.
Mr Reger, automation and digitalisation are considered indispensable tools in view of the challenges facing the automotive industry. With what steps and offers is ABB approaching the market especially for automotive OEMs and suppliers?
Jörg Reger: We see ourselves as a ‘one stop shop’ for robot-based automation. ABB has the technology to support customers in the transformation towards sustainable mobility. To this end, we offer one of the broadest product ranges with 6-axis robots, Scara, Delta, painting robots and autonomous mobile robots (AMRs). We also offer functional packages for various applications such as welding, spot welding, gluing, sealing and much more. Special mention should be made here of PixelPaint, which allows individualised painting without additional masking. This allows for a more sustainable and flexible production.
Our manufacturing offer ranges from standardised production cell concepts with minimal integration effort and lower risk for OEMs, up to customised, smart production lines. Using our AMRs, the different cells can be loaded and unloaded automatically, creating flexible production lines that can be quickly adapted to requirements and also allow multiple model and variant changes on the same line. Of course, we also offer everything necessary around these products, such as various software solutions and the entire service area.
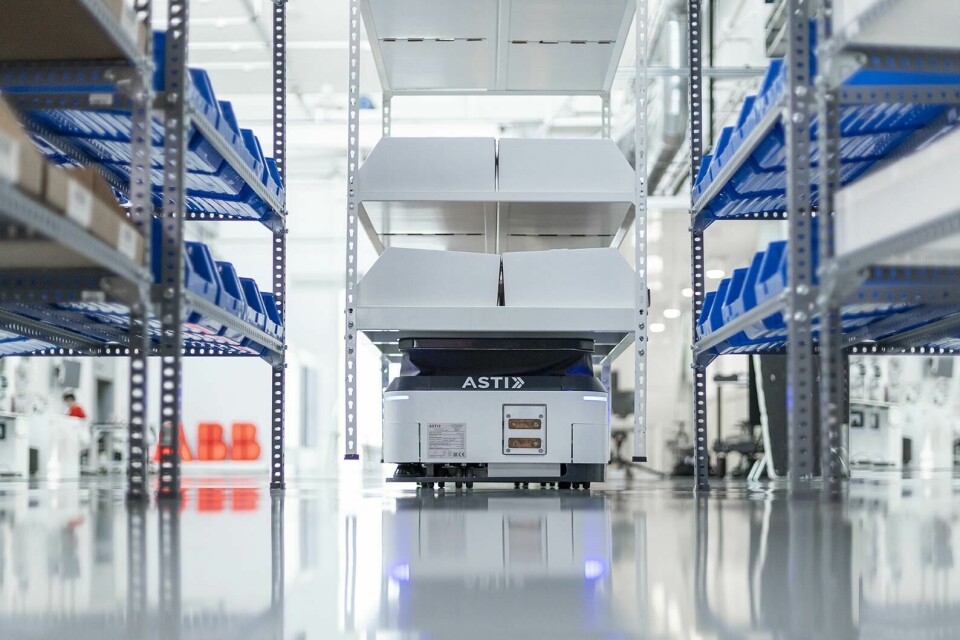
In addition to automation and digitalisation, the qualification of employees is one of the top issues in this rapidly changing industrial environment. What does ABB offer here?
Jörg Reger: Our worldwide services include a large training department. We are expanding this further with a view especially to the new technologies that electromobility brings with it, and particularly in training for our customers. Examples for OEMs include the assembly of electric motors or batteries. In our training centre, participants can learn about these topics directly, including working with the corresponding software.
According to a survey conducted by ABB together with AMS late last year, 59% of those surveyed said that achieving 100% EV production between 2030-2040 would be too ambitious. How do you see this, especially in terms of training the workers involved?
Carolin Platz: The transformation towards low-carbon production and mass adoption of electric drives is a complex challenge. Technical hurdles must be overcome, production capacities must be built up and the public infrastructure also has to be adapted. I think it is important that the technological and economic goals are realistic and achievable, and that the transformation can take place gradually. This also means that companies need to consider adequate investment in research, development and in training people. Many will need new skills and retraining. It is important to support workers in this process and to ensure that no one is left behind by the changes.
Taking all factors into account, it seems difficult to me, to set a concrete timeline to reach full electrification, but I expect significant progress to be made in the coming years.
Jörg Reger: The survey reflects the pressure and strain the industry is under now. Whether the committed targets can be met, depends on various factors. What is certain is that automation is a crucial element in making production more resilient, efficient and faster. That’s why we’re seeing high demand for our robots, especially those specialised in electric vehicle assembly. These solutions help to radically reduce build times, improve flexibility and further simplify the production process. Ultimately, this also reduces production costs. The latter is crucial, as electric vehicles are still more expensive than combustion engines.
Another important point is that the transition to EVs will vary geographically. Some regions will need a longer time to provide the appropriate infrastructure, or they may never go completely EV. This also explains why the combustion engine will not disappear completely anytime soon. This is another challenge for manufacturers, as the diversity of powertrains they need to produce is increasing. There is also a huge need for training people.
The factory infrastructure exists. The challenge, however, is to shape transformation and to look at how to gradually enable people to produce electric cars while at the same time keeping conventional powertrains running for years to come. This is feasible if all stakeholders pull together and work collaboratively on the common goal of achieving sustainability.
Where are automation and digitalisation in the automotive industry particularly advanced, and what can still be further automated more quickly? And how do you support small and medium-sized enterprises in automation?
Jörg Reger: The automotive industry is already a highly automated sector, and there is a trend towards automation in other industries, too. There are currently more than 3m industrial robots in use in the global economy – a number that has more than tripled in the last ten years. The cost of robots has dropped significantly, making them affordable for medium and small businesses and offering a shorter payback period. As robots free workers from tedious, repetitive tasks, they allow employees to focus on work that adds real value and which cannot be automated.
By their very nature, car manufacturers are already highly automated and digitised. The supplier industry is also catching up strongly. However, there is no general answer to the question of the degree of automation, as this always depends on the existing conditions. It also doesn’t always make sense to automate everything down to the very last process step. This is where collaborative robots, so-called cobots, offer a good opportunity for cooperation between the employee and the machine.
At the automatica trade fair, cobots were one of the big topics. But where are humans still indispensable and irreplaceable?
Carolin Platz: Robotics and automation offer many advantages and enable us to perform certain tasks more efficiently. Nevertheless, the machines can’t do everything. People will always be needed in areas that have to do with design and aesthetics, but also those where quick decision-making and adaptability are important, and where predefined processes and algorithms must also be bypassed at times. The cooperation between humans and machines will increasingly lead to a shift in competencies, in the course of which job profiles will tend to become more demanding.
Jörg Reger: Higher-value work will continue to be done by people. And people also must maintain and service the machines and evaluate information. Manufacturers will put more focus on training operators in factories. Meanwhile, a higher level of automation can also reduce the need to offshore jobs, helping to protect or regain jobs here in Europe.
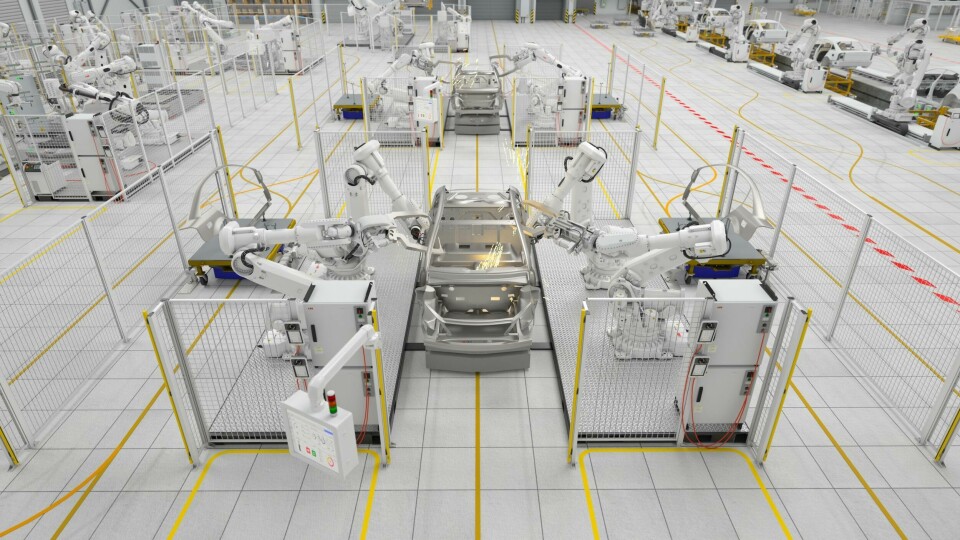
Greater automation could bring some jobs back to high-wage countries, for example in the production of cable harnesses and wiring systems…
Jörg Reger: Production chains must become more resilient to external influences. We have had to learn this painfully with the pandemic and from the war against Ukraine. Automation and technology are a means to bring production closer to the consumer again, for example through nearshoring and ‘friendshoring’. However, it doesn’t always make sense to try to automate all existing processes, and instead we have to keep on the lookout for new technology. In your example of cable harnesses, rather than automating their production at great expense it may be better to look for technology that can replace them completely.
But of course, there are always new technologies coming along in automation, too, which will make it possible to automate production processes tomorrow where this is not yet possible today. In recent years, we have seen strong progress in vision technology, for example. AI and machine learning are new additions.
I believe education must become more continuous, flexible, personalised and accessible, including through virtual assistants, adaptive learning platforms and intelligent tutoring systems -Carolin Platz, Auto-Motive
Ms Platz, training and qualification for advanced technology will also require modern tools. How should we imagine future learning systems?
Carolin Platz: Basically, we are dealing with the same topics in continuing education as you, Mr Reger, are in industry. Digitisation and artificial intelligence have become indispensable here as well. This is what I meant at the beginning by ‘moving away from traditional learning systems’. This is where we must answer the question of how continuing education should evolve as people and machines move ever closer together and product life cycles become increasingly shorter?
I believe education must become more continuous, flexible, personalised and accessible, including through virtual assistants, adaptive learning platforms and intelligent tutoring systems. Regarding AI, this means, for example, playing personalised learning content to students in real time, showing their learning progress and any deficits immediately, and adapting their individual learning paths accordingly. In the process, AI answers questions, gives feedback and carries out objective evaluations.
Mr Reger, what is the difference between the established OEMs and the new players when it comes to automation and digitalisation? How clear is the advantage in greenfield over brownfield operations?
Jörg Reger: The new players simply have no legacy to worry about. We see some highly successful carmakers from China now pushing into the European and North American markets. Companies like Tesla focus exclusively on battery electric vehicles and don’t have to worry about multiple drive variants like ICE, hybrid, BEV and so on. This gives them a big advantage in terms of the complexity of their production sites. They also question existing production methods because they do not have to use existing facilities. One key topic in new production processes is megacasting – the production of large car body components from die casting – which can reduce complexity. These new players are bringing a lot of innovation to an established industry. Established OEMs, meanwhile, are having increasing problems finding skilled workers. Along with engine engineers, they now need battery experts and electric motor specialists, who are not easy to find.
Mr Reger, are you feeling the competition from the machinery and plant engineering sector from Asia? What does this mean for your company, and what USPs can ABB point to in response?
Jörg Reger: ABB is globally positioned, as are our major customers. This means that we can serve our customers locally and draw on a portfolio of services and technology, available globally. This provides security for the users and brings various advantages in education as well as training of the employees. Skilled workers and equipment can be deployed where they are needed. We also have the broadest portfolio on the market. As mentioned, we cover everything from robot products to standardised production cells to entire lines with the corresponding software. For automotive, we can cover the entire process steps of an automobile in the factory. What differentiates us even more from the competition is our expertise and process knowledge in various industries, together with our automation know-how, which sets us apart from most suppliers.
Ms Platz, if you had one wish to change or accelerate something immediately in the automotive industry, what would it be?
Carolin Platz: Acceleration is a good focus point. Compared to other regions, [Europe] is not doing well in terms of speed. To permanently gain speed, innovative strength and competitiveness, I would like to see fewer bureaucratic structures and targeted cooperation between government, science and industry.