Megacasting: a chance to rethink body manufacturing
The aluminium die-casting process could revolutionise body construction. Professor Wolfram Volk, the department head for forming technology and casting at the Technical University of Munich, explains the advantages and disadvantages of so-called ‘mega’- or ‘gigacasting’.
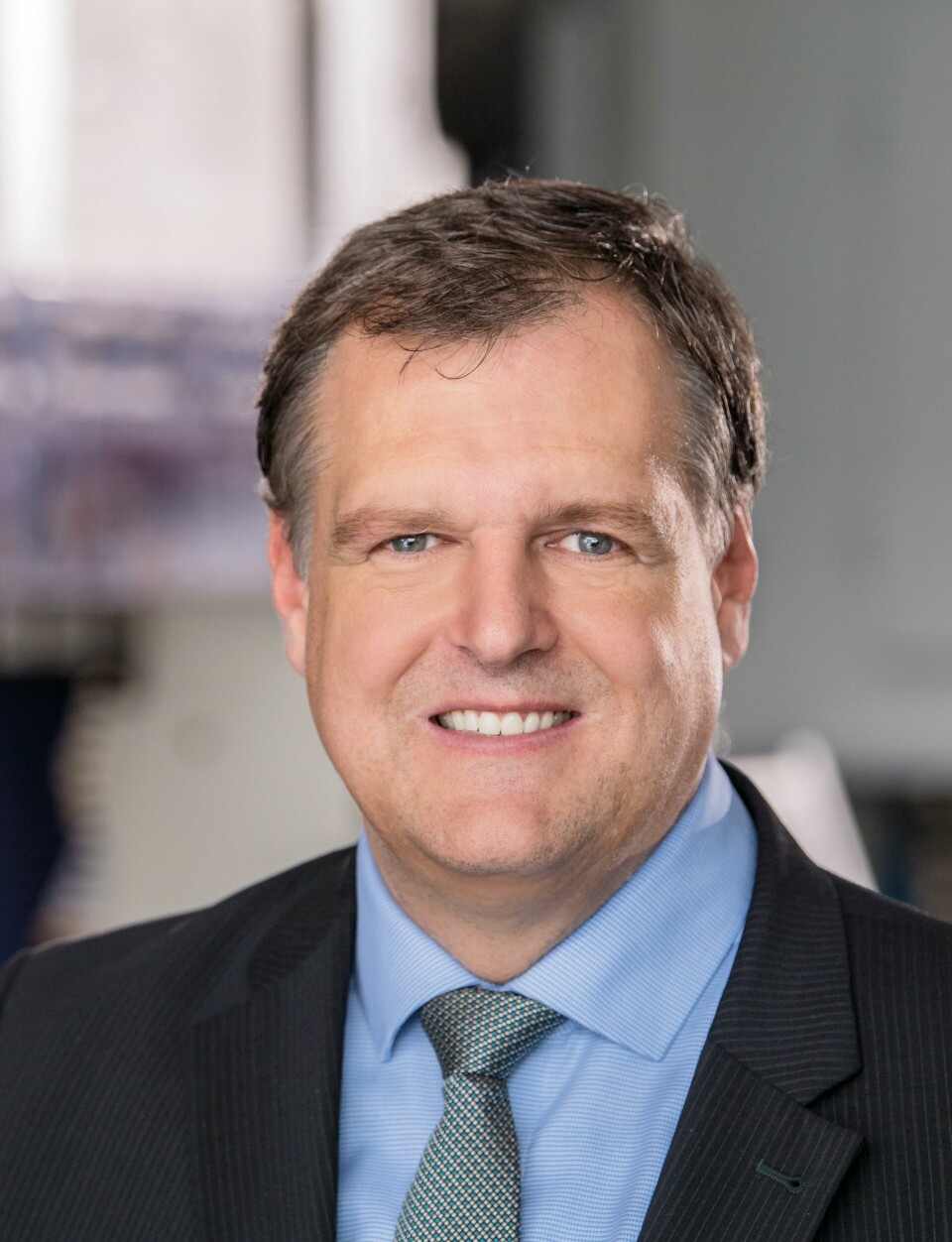
Several vehicle manufacturers are ramping up investment in the use of megacasting as they build new plants and revamp others for electric vehicle production. While Tesla has been a frontrunner, using the process to cast large body structures that are reported to save 70 parts for each large piece, Volvo Cars has also just announced a plan to switch to aluminium megacasting for rear body structures starting at its Torslanda plant in Gothenburg, Sweden for new electric vehicle platforms starting in 2025.
The process offers potential benefits in parts reduction, which can remove logistics and emissions in various processes, while providing more flexibility in aspects of vehicle platform engineering. However, according to Prof. Wolfram Volk, the head of the department of forming technology and casting at the Technical University of Munich, it also brings space challenges to factories, and may not always be as effective for certain facilities and models compared to sheet-metal shell construction. Volk, a manufacturing expert who has previously worked for BMW, outlines limitations while pointing to exciting opportunities.
What’s the potential of megacasting in the automotive industry? How new is it?
What’s new is that extremely large shell components can be manufactured using a casting technology. Until now, the largest cast parts produced with die-casting technology have been suspension strut domes and side rails, like those on the larger Audi and BMW model lines. We have seen bold decision-making on expanding the technology to much larger components, especially to the rear floor panel, which is considered especially critical to avoid distortion. This means our established material concepts will have to be modified.
In what respect?
Tesla is getting around the issue of heat treatment. The new technology involves working with natural hard alloys. Yet precipitation-hardened alloys offer advantages in terms of strength and ductility. With natural hard alloys, you make compromises, but you save money on later expenditures. No one has deep insights into how to deal with distortions resulting from heat treatment in components of this size.
Tesla, for example, uses this process to ultimately drive the number of parts down to one component. How realistic is that?
I had the opportunity to observe the Model Y in the so-called disassembly area. Tesla has greatly reduced the number of its parts. But it’s clear that parts reduction still does not confer operating advantages. That’s because you must look at the production and material costs, along with the cost of the investment, in their entirety. That’s what we established while working with various Fraunhofer Institutes such as IAO (Institute for Industrial Engineering), IFAM (Institute for Manufacturing Technology and Advanced Materials) and IWU (Institute for Machine Tools and Forming Technology).
In addition, the car bodies do not necessarily become lighter. A large part simply requires the right wall thickness. At the same time, you are reducing the potential for bringing the right material qualities to exactly the right point – the way that the classic shell construction using sheet metal often does. Furthermore, the production of sheet-metal parts is very cost-effective, and the joining technologies for them can be automated very easily.
What is the attraction of manufacturing large parts with aluminium die casting instead of the sheet-metal shell approach?
Along with spot welding, the different variations in sheet-metal shell construction have developed into a tried-and tested-process over the decades. You see metal thicknesses with a lower boundary of 2-3mm in die casting, while wall thicknesses down to 0.7mm are possible with sheet-metal shells. That means giga- or megacasting cannot be classified either as an efficient or a lightweight solution – or as a higher-performing process. But it is likely to be an alternative that adds an interesting variation to the entrenched modular systems in car body manufacturing. For electric mobility especially, gigacasting is a way to rethink car body construction. In electric mobility, you have the battery tray, a new core part that must be integrated. The progress that has been achieved over the years in internal combustion vehicles only has a limited applicability to electric vehicles, especially when you consider the rear-end and the middle of the vehicle. With the greenfield approach that Tesla is taking in Brandenburg [for its new factory in Grüneheide, near Berlin], for example, the automaker can save significant space in its electric-vehicle body department. On the other hand, it is important to assess whether aluminium gigacasting is likely to make sense for brownfields.
Media reports are citing savings potential of 20-30%, primarily because the number of welding robots and forming processes can be reduced.
Here I would be careful since investments, especially in a particular model generation of welding robots, are depreciated. For forming processes, the depreciation can even extend over three or four model generations. This technological write-off – bear in mind that this is not tax-related – runs over a timeframe of 30 years. For the OEMs that are already using these machines for existing vehicle generations, the use of the new technology makes no sense. On the other hand, thanks to its greenfield approach, Tesla can save itself these typical investments in shell-type construction. In a brownfield, it would be operationally nonsensical not to keep using long depreciated machinery. So, in this situation, I would not support the 20-30% cost savings that were cited.
What volumes would be practical for aluminium casting?
With die casting, one important aspect is that there is a noticeable reduction in the service life of the die-casting moulds. Due to so-called thermal shock, the rule of thumb is that a die-casting mould is good for 100,000-150,000 shots. By contrast, one forming tool is used to make 5m-6m parts. So, we are talking about a factor of 20 to 30. There is quite clearly a limited volume range for which the casting-intensive solution would be appropriate. To me, aluminium casting holds little appeal for very small and very large volumes. Especially for mass production in the millions, you would need about six or seven of these expensive die-casting moulds. We estimate that the die-casting form for the single part, rear-end of a Tesla would weigh about 80-100 tonnes. This translates to huge costs for handling and the peripheral equipment, in the form of cranes, for example. Die-casting moulds also pose technological obstacles and hazards. The leakage of melted material is cited as one example. The risks of not even being able to operate in some situations are not negligible.
In this view, how fragile is aluminium die casting?
To put it simply, the casting process is much more complex than a cold-forming process. The key word here is scrap. Cooling is an important issue in this connection. It must be clear to the operator that his scrap rate could be in the 10-20% range or more. This in turn has an impact on the flow of car body manufacturing, that is, on the number of body parts he must set aside to offset any stoppages in vehicle production.
To me, aluminium casting holds little appeal for very small and very large volumes. Especially for mass production in the millions, you would need about six or seven of these expensive die-casting moulds.-Professor Wolfram Volk
Other automakers are considering the use of aluminium casting for electric vehicles and are even talking about increases in body rigidity.
It is important to know exactly what is referred to here. You should consider the major conflicting objectives in car body manufacturing collectively. On one hand, there are the issues of body stiffness, strength and resonant frequency. On the other hand, there is crash performance. The smaller the component, the more the leeway you have for improvements. With die casting, we have a great advantage: stiffening elements of greater complexity can be produced directly.
But there are also clear limitations. For example, nothing can be changed on the e-module, which contributes significantly to the vehicle’s rigidity. Compared to steel alloys, you are very quickly at the limit of what can be achieved with aluminium die-casting alloys in terms of engineering. The same question applies here: What are you comparing? The architecture of an electric vehicle has a completely different look. Then you have the issue of optimising its degrees of freedom. Especially with natural hard alloys for die casting, the opportunity is very limited.
What is the strength of aluminium compared to steel?
There is a wide spectrum once you look at the alloys. Natural hard alloys that do not tolerate heat treatments range between about 250 MPa (megapascal pressure unit) to a maximum of 350 MPa. In the case of press-hardened steel, you have a range for the soft, deep-drawn steels going from 140 to 1,500 MPa. The construction kit of available materials is much greater in this case. The range of aluminium wrought alloys is certainly respectable as well. The so-called 7,000 series, for example, offers about 500-600 MPa.
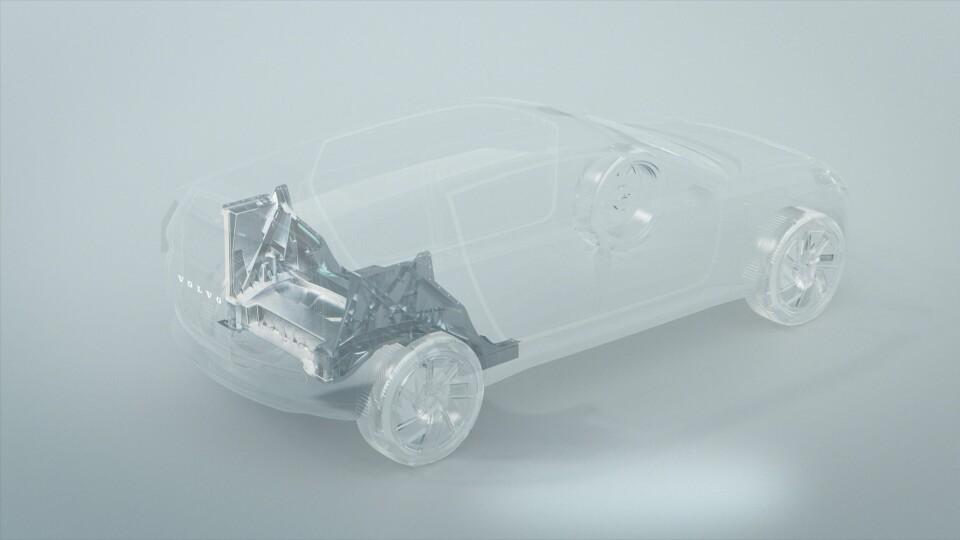
Volvo Cars has recently decided to use megacasting for the rear bodies of a new EV platform, an body part which Prof. Volk thinks makes the most sense for megacasting
Then where does the use of aluminium, especially for certain specific parts of the car body, make sense – especially when OEMs consider crash performance?
It is destined for the centre floor and the rear-end. In a crash, ductility does not need to be very high there. On the other hand, I only foresee limited use in the front structure. One reason is that significantly greater ductility and resilience are needed there, especially to handle the frontal crash requirements. But it should also be clear that the design of the front end is completely different for electric mobility anyway, for example, when the electric motor is a mid-engine. On the other hand, the demands on the centre floor, including battery trays, on electric vehicles are significantly greater. Here the focus is more on strength than ductility. Large components certainly have an impact on the opportunities for repairs and repair-friendliness – and thus ultimately on costs. There are still some questions to clarify here.
Would the ‘cell-to-chassis’ approach, where batteries take on a structural role for the body, be an important way forward?
Thanks to the low placement of the heavy elements, this architecture offers benefits for driving dynamics. They contribute to a low centre of gravity and a good weight distribution. The functional integration of the battery housing is the basic principle of body design for electric mobility. But this can also be achieved with appropriate joining operations and does not necessarily depend on gigacasting.
There still aren’t very many machines for the processing of large aluminium components. One manufacturer is Idra in Italy. What is your forecast for this type of machinery and for the process?
Idra is currently one of the manufacturers in the field, but there are other companies that recognise the market’s potential. Machines are envisioned that reach up to 80,000 kN (kilonewton) of clamping force. But then they reach their physical limits. At present, we can only speculate on the availability of these facilities. We will only learn more about disruptions and so-called growing pains when manufacturing operations are underway. So overall facility efficiency is still a major issue.
On the one hand, if you use aluminium die casting, you save space in your plant’s body department because fewer robots are used, as we discussed at the outset. On the other hand, these die-casting machines are huge. Do you see space benefit overall, or disadvantages?
Aluminium casting requires substantial space in factories. An important aspect is that die-casting moulds can only be changed vertically, with the aid of a crane. Swapping tools that weigh up to 100 tonnes takes 10-12 hours. By comparison, tool changes in today’s large pressing plants with their efficient servo presses only take about three minutes. The tools can be moved in and out horizontally. Die-casting moulds must be inserted vertically. Otherwise, there will be problems with the separating agent. This situation, along with the inability to produce more than one component per machine, is a major limitation.
Nonetheless, gigacasting is bringing dynamism to manufacturing. Other automakers are giving more fundamental thought to the idea and achieving new degrees of freedom in production. I can’t wait to see which concepts prevail in the future.