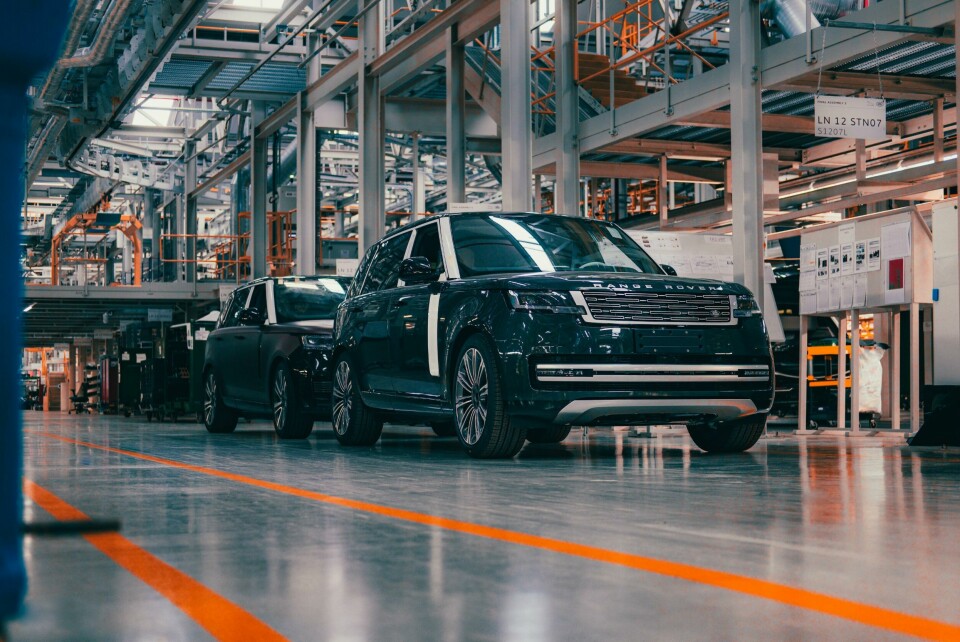
JLR – Putting sustainability at the centre of its strategy
Sustainability is a key of JLR’s Reimagine strategy, but this goes beyond developing and manufacturing a new generation of electric vehicles. The OEM’s manufacturing sustainability transformation lead, Garrett Bell, shared some insights in how the business is reducing its carbon footprint across its operations.
Another big transformation is happening at JLR, alongside upgrading production operations for electric vehicles (EVs). A key pillar of the OEM’s end-to-end Reimagine strategy is sustainability. This involves a major programme of evaluations and assessments across the entire production network, focusing on identifying and implementing efficiencies in the management of operations in relation to production activities and infrastructure that will reduce the company’s carbon footprint in line with Science Based Targets and Net Zero by 2039 commitments.
Garrett Bell is responsible for leading the sustainability transformation for Manufacturing Operations, focussing on energy, carbon, water and waste reduction across 11 global manufacturing locations to support the delivery of JLR’s commitments. Discussing his role and the company’s sustainability strategy, Bell outlined the way the programme has been structured.
“The local teams will develop ideas and create the business cases which I support from a central funding point, which they then execute. If we need to bring in outside consultants, then I support with engagement in these cases. But the focus is for these teams, within their respective areas, to take on as much ownership of the projects as possible, it’s something I’m actively encouraging.”
As well as its commitment to achieving Net Zero across operations, supply chain, locations and products by 2039, JLR has taken this a step further by establishing an interim target of 2030, which is tied into the Science Based Targets initiative (SBTi), something a number of other OEMs and tier suppliers are also doing.
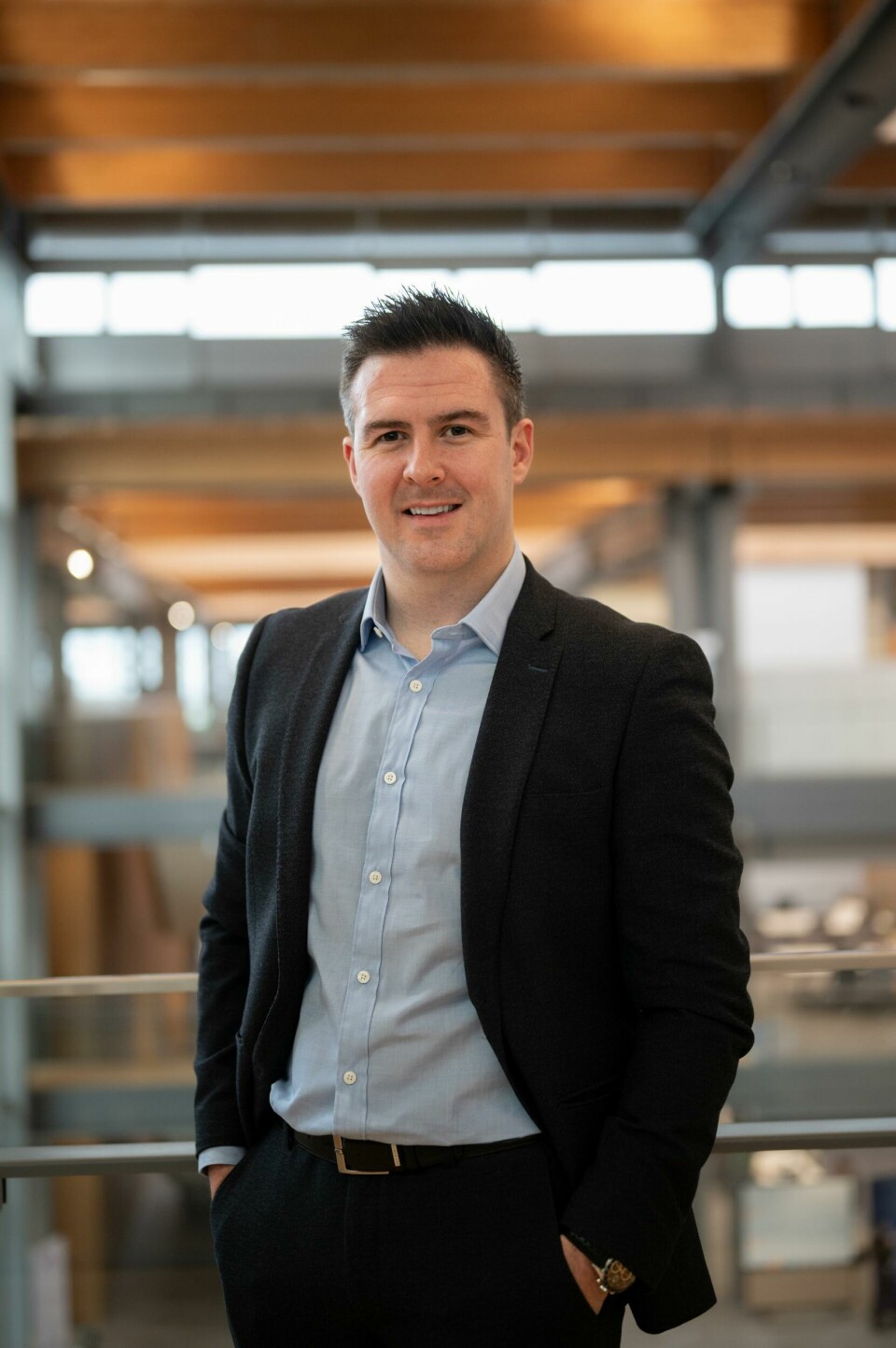
Sustainability as part of the Reimagine strategy
JLR’s Reimagine strategy offers a roadmap to the company’s transition to electric vehicle production. And while this transition is a challenge across the automotive industry, it also offers a huge opportunity to reshape business operations as they are modernised and upgraded. It allows for sustainability to become embedded in operations, processes and company culture. Bell points to four statements in Reimagine, which highlight the company’s ambitions in relation to sustainability.
“We set out to put sustainability at the centre of our brand strategy, but beneath that there are these four parts: to be identified as a green industrial leader, to transform the business into a genuinely sustainable organisation, to have sustainability a key concern at all levels and lastly around innovation, to try and anticipate regulatory requirements and customer expectations. So, I think these statements cover what we want to achieve, end to end at an enterprise level.”
This process is more than just about the visible aspects of reducing the company’s carbon footprint; for Bell it’s also about attracting and retaining talent and creating the right kind of culture within the company.
“Some aspects of this are easier to see, such as big projects involving solar farms, or hydrogen projects or electrification of products and processes, people can see this and understand it, but also very important to establish a culture and mindset around sustainability, throughout the business.
“Parts of the Reimagine strategy are looking at the mid- to long-term, but we also have short term commitments and we have established an internal programme that’s managing some of the more immediate quick wins. The culture we are building here really is from enterprise to associate levels to create a very clear connection on this topic.”
While the overall sustainability strategy is mid- to long-term in its approach, the resources needed are being put in place right now to move on actioning projects that can be completed in the short term.
“One of the things we have done quite quickly is establish teams to manage specific areas. I set up a team to manage waste, water and scope 1 and 2 issues. Part of my job is to look over our operations in relation to sustainability and identify what we’re missing and to work out how we fill these gaps.
“We have a new target setting structure following the SBTs and there are also simple things to address, such as energy management, base loading optimisation, shutting down equipment, systems, etc. when not in use, and looking at shift planning in more detail in relation to energy consumption. It’s creating a mindset around these types of things.”
The rising energy costs over the last 12-18 months has put the focus energy management. Bell explains the team working on this set clear targets using SBTs but notes that these follow a linear path that requires regular improvements year on year, so it’s important to avoid having one big reduction at a single point after doing nothing over a period of years.
“This can be challenging for us as we don’t produce the same number of products, or necessarily have the same shift patterns each year, and there’s now further variation with the shift to electric vehicles. The work and resources involved in producing the vehicles and powertrains isn’t linear year on year. For example, the Halewood plant had been running one shift, which makes it easier to hit its C02 target, but in January moved up to two shifts, which increases energy consumption. And there’s all the new products that will come online over the next few years, so we must work out what impact this will have on our targets and how we manage this.
“To manage this, we’ve now got teams resources in place covering governance and central enterprise. The approach we take is to have an enterprise target of so many kilotons, we then break that down into every single plant that I’m responsible for, that’s split by plant, and then by technology within plant. So, we have clear view of ownership and accountability right down to a block level within the plant.”
“If you compare Halewood, which is an older plant, with Nitra, which is a more modern facility, you would expect Halewood to be consuming way more energy than Nitra, when actually they’re comparable, when they’re at similar volumes.” Garrett Bell
Managing a global remit for sustainability
Part of Bell’s remit is managing sustainability across 11 different manufacturing locations globally. This would seem to add further challenges as no two plants are the same and then factoring in any regional, supply chain and output differences would certainly be a consideration in terms of production operations, but from Bell’s sustainability perspective the management challenges are not where you might expect.
“If you compare Halewood, which is an older plant, with Nitra, which is a more modern facility, you would expect Halewood to be consuming alot more energy than Nitra, when actually they’re comparable, when they’re at similar volumes.”
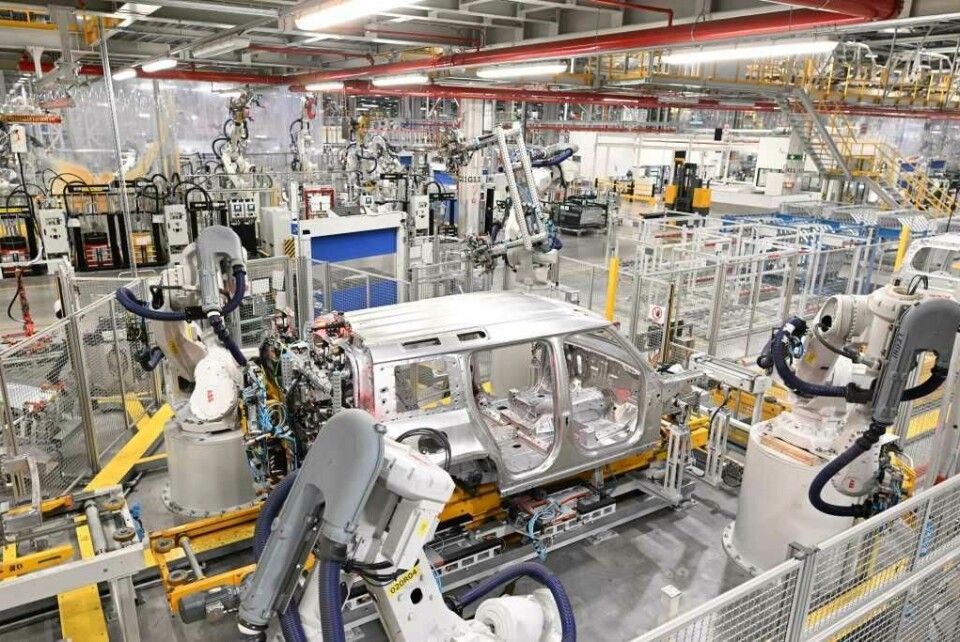
Bell notes that although Nitra runs more modern equipment than Halewood in this case (compressors) it’s as much about optimising the equipment than just have the latest technology.
“It’s not clear cut when it comes to comparing plant to plant. There are some common projects across plants like set point reduction, such as turning down the temperature within the production areas. So, although the themes are similar, the actual actions are variable. These common things are shared within an energy expert’s forum. We meet every month as a group and share best practice, biggest load optimisation, etc.”
In 2014, as part of a joint venture with Chery, JLR established a vehicle assembly plant in the Changshu Economic Development Zone, north of Shanghai to produce vehicles for the Chinese market. In 2017 a 12-acre engineering manufacturing plant was opened on the same site. With much of China’s industrial network powered energy produced from coal fired sources it would be easy to imagine that this would be a major challenge for JLR’s sustainability targets, but, as Bell notes, JLR’s China plant has a great deal to offer in terms of production efficiency.
“China’s slightly different, mainly because energy is cheap there and it is predominantly coal fired, so you’ve got some regional differences in terms of the energy supply, and you’ve got the complexity of the equipment differential and how they operate in the plants. But in China during COVID they were given a ration of energy, so if they consumed what they were allowed to consume in a week, on a Thursday, then the power could just be turned off and shut down production. So, the granularity of control and consumption and planning in China is far more extensive than what you would see elsewhere. And they’ve taken the COVID regulatory control, government control, and continued to apply this to production operations and it is our most efficient plant when it comes to energy per car.”
Visibility through good data
Looking at some of these cases there is much, which from the outside, seems counterintuitive in making production operations more sustainable, but Bell points to the importance of good data to establish where improvements are needed or can be made. And data gathering and, perhaps more importantly, proper analysis is key to making an undertaking of this scale and scope possible. Although transforming a large-scale production network into a sustainable operation is undoubtedly complex, Bell notes that complex problems can often be solved with simple solutions.
“We put real emphasis on data. If you asked me, without having seen any numbers, should we spend money at Halewood or in Nitra? Straight away you choose Halewood because it’s the oldest factory and they need all these improvements, led lighting, new compressors and a new paintshop etc., where they’re actually as efficient as a brand-new factory in nature. At Nitra it’s got new modulating compressors, where you can change the set points remotely, they’ve got metering and granularity right down to a tool on a line. Where we are spending money here is flu gas economisers and the boiler systems and the paint facility, because that’s the biggest win we’ll get, rather than spending this equivalent amount of money in Halewood where we wouldn’t reap as much benefit as quickly.”
Working with Tata Consultancy Services, JLR has started a large-scale data gathering pilot project at its Solihull plant. The system called Clever Energy has seen 800 new energy meters installed and created 2500 production data points. This allows the teams to take multiple energy metering systems and consolidate them into one visualisation suite, and then pair that with operating parameters. This covers live volume build within bodyshops, paintshops, trimshops, off track areas and then all the parameter settings.
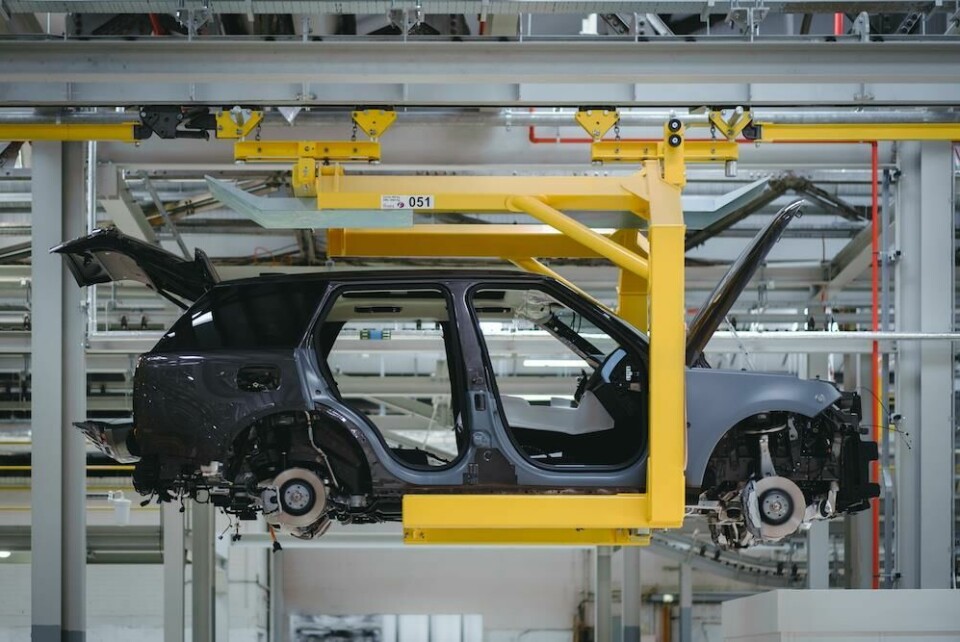
Bell explains the benefits of this system: “Previously all those were isolated, disconnected systems. So now we’re looking at leveraging artificial intelligence and machine learning capabilities for future simulations and future forecasting capabilities.
“The system also creates auto alerts. So, for example if a compressor is running at seven bar pressure and it needs to be running at six bar, we have a threshold point. I’ll get an alert to tell me that’s the case by email and eventually on an iPhone. I know then that I need to bring someone in from maintenance to address the issue. It offers that level of control, fully integrated management systems and energy metering.”
Solihull is the most advanced at the moment in terms of new systems, but Bell’s team plan to improve the level of metering further at that plant and then replicate that across all JLR’s facilities to bring them all up to the same standard.
Bell notes that the amount of work to do this varies. For example, Nitra is quite advanced but doesn’t have the visualisation suite and still has separated systems. The Chinese plant has its own solution to what’s deployed in Solihull.
“The question we have for the Chinese plant is do we retrofit that, or do we just let them run as a joint venture and they do their own thing where they’re already quite good in terms of efficiency management. We’re working on the whole digital solution to roll out across all the plants, and we’ve piloted it at Solihull and Whitley. So far, we’ve done a production site and an office non-production site.”
People are also a big part of this project and in contrast to the digital approach at Solihull, teams at Halewood were redeployed with the same goal.
When the Halewood plant was ramped back to one shift for modernisation and transformation activities, some of the second shift heads created an energy team, tasked with going into all the technology areas at the plant and looking for improvements. This has delivered people-driven ideas versus system-driven ideas. The results for both have been positive and Bell observes that when Halewood returned to two shifts those shift heads returned to their normal roles with valuable experience gained in this exercise.
“I don’t feel that there’s too many people that really understand the complexity of this space, and the enterprise, integration requirements to it. We need to put a programme in place that gives everybody in our organisation the understanding of how we’re building sustainability into our operations. Our site services or maintenance teams will need the skills to understand BMS systems, data visualisation, etc. So, this is also an important part of the transformation programme from an education perspective.”
Considering the right renewables
Renewable energy is another important part of the sustainability picture, but there are several considerations in choosing the right technology. On a large scale, solar and wind powered energy sources are popular and widely used for automotive manufacturing. However, decisions around deployment and investment in these technologies are more complex and nuanced than it might at first appear. Bell explains.
“To get to Net Zero, you need to remove gas from your processes, which requires you to electrify or look for a gas alternative, such as biogas, synthetic fuels or hydrogen. The easiest solution would seem to be electrifying those processes and it’s what most OEMs are doing. So, you replace a gas boiler with an electric boiler, or you remove gas fired heaters from a paintshop and install an electrified solution.
”But that increases operating costs by two and a half times, based on the current price differential. When you go from gas to electricity on a piece of equipment, you see about a 20% to 30% efficiency improvement, but you’re still having to pay more to run it because you’re consuming energy at a higher cost base. So, you must find ways to offset that operating cost differential in the first instance.”
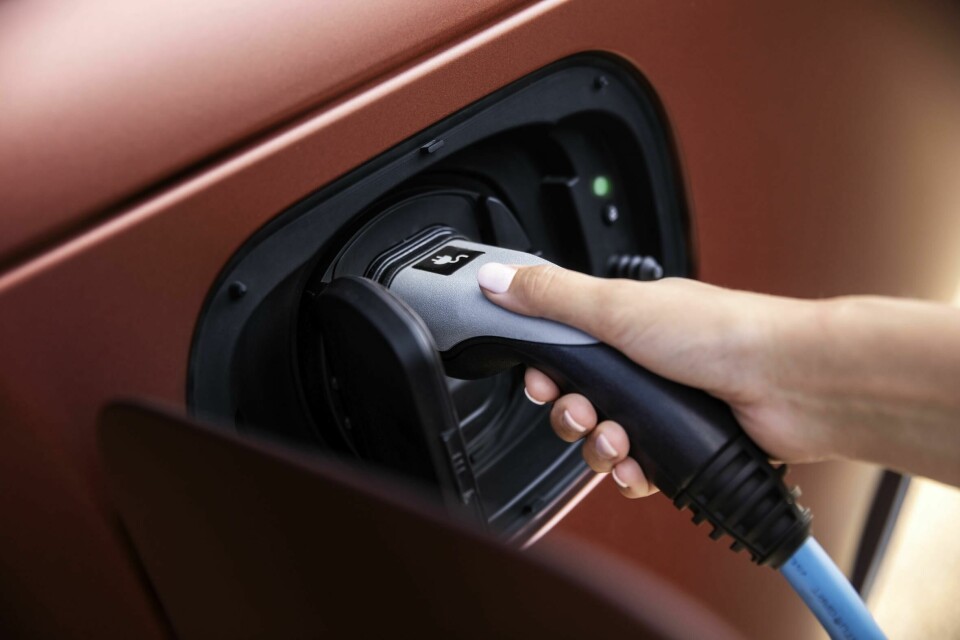
Sustainability: the hidden transformation
The automotive industry’s drive to achieve a more sustainable footprint is often viewed through the prism of producing electric vehicles and while this will see the biggest reduction in total business emissions, Bell suggests this might be easiest part of the process. Taking nothing away from the enormous levels of investment and development going into EV and battery production, the remaining areas of operations for OEMs are diverse and complex.
“Once you get fully established with EV products and production, you’ll remove about 70% of your total business emissions. The residual 30%, which sits within scope one, two and three in terms of supply chain and logistics, is where it’s going to be most difficult. Most see the battery tech and the scrap side of the batteries as an important factor from a waste perspective and a sustainability view, but in terms of the actual energy consumption and direct carbon, the biggest challenge is going to be in operations and in supply chain.”
Bell acknowledges the scope and scale of his role and the work being done by teams across the business, but sees good progress being driven by a positive culture throughout JLR.
“We’re in a good place and it feels that we’re really starting to get some momentum. There’s lots to do and sometimes we feel frustrated that we’re not doing it quickly enough, but as I said, you have to be cognizant of the constraints, challenges and priorities that we’ve got manage.”