How the Audi Q6 e-tron series is proof of the OEMs flexible and sustainable vehicle production ecosystem
Audi’s Ingolstadt plant pioneers sustainable manufacturing with net-zero emissions, showcasing flexible integration and cutting-edge technology: Q6 e-tron leads the way
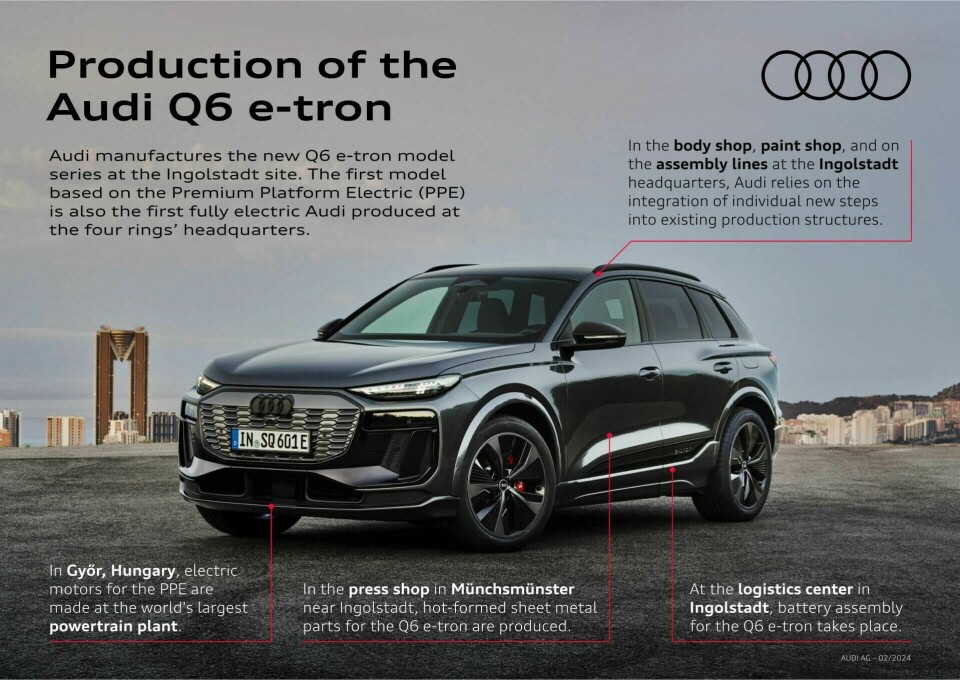
Since its production launch in late 2023, the Audi Q6 e-tron series stands as Audi’s inaugural high-volume fully electric model series produced at its headquarters in Ingolstadt. Aligned with the brand’s 360factory production strategy, Audi has integrated individual production steps into existing body shop and assembly structures and processes.
As of the beginning of 2024, Ingolstadt joins Brussels (2018) and Győr (2020) as the third Audi location to operate with net zero emissions. The headquarters, sporting the four rings emblem, also marks the first Audi facility in Germany to house its own battery assembly facility.
Gernot Döllner, Audi CEO, underlines the significance of the inaugural model based on the Premium Platform Electric (PPE), stating, “The PPE, and with it the Q6 e-tron series, form the basis for subsequent electric Audi models. In this way, we are taking a decisive step towards offering an electric model in all core segments by 2027.”
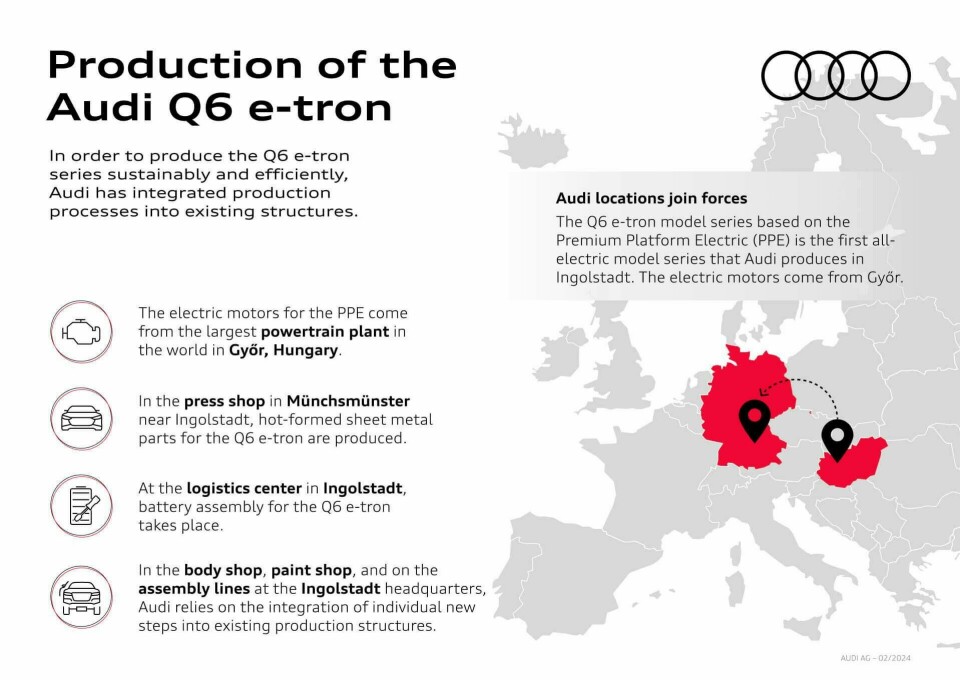
Gerd Walker, Audi Board Member for Production and Logistics, views the commencement of production as a pivotal milestone for the 360factory production strategy, stating, “By the end of the decade, we will have successively equipped all Audi locations for the production of electric models. We are harnessing electrification to comprehensively transform our existing plants. With the production of the Q6 e-tron series, the Ingolstadt plant is taking the next step towards becoming a 360factory.”
Audi’s vision for the future of production revolves around a holistic, sustainable approach, encompassing modernisation, digitalisation, and transformation of existing plants. Since 2024, the Audi Q6 e-tron series, alongside all other vehicles manufactured at the site, boasts net zero emissions.
Battery, Bodyshop, paint and press: Audi reaches for radical flexibility
The battery assembly facility, spanning approximately 30,000 Sq. m, accommodates 300 employees across three shifts, and boasts an automation rate nearing 90 percent. Initially catering to the Q6 e-tron series, the facility serves as a foundation for Audi’s eventual in-house production of battery modules.
With its location at the Logistics and Goods Transport Center (GVZ) in Ingolstadt, the facility operates solely on green electricity, enhancing production flexibility and efficiency without necessitating additional construction.
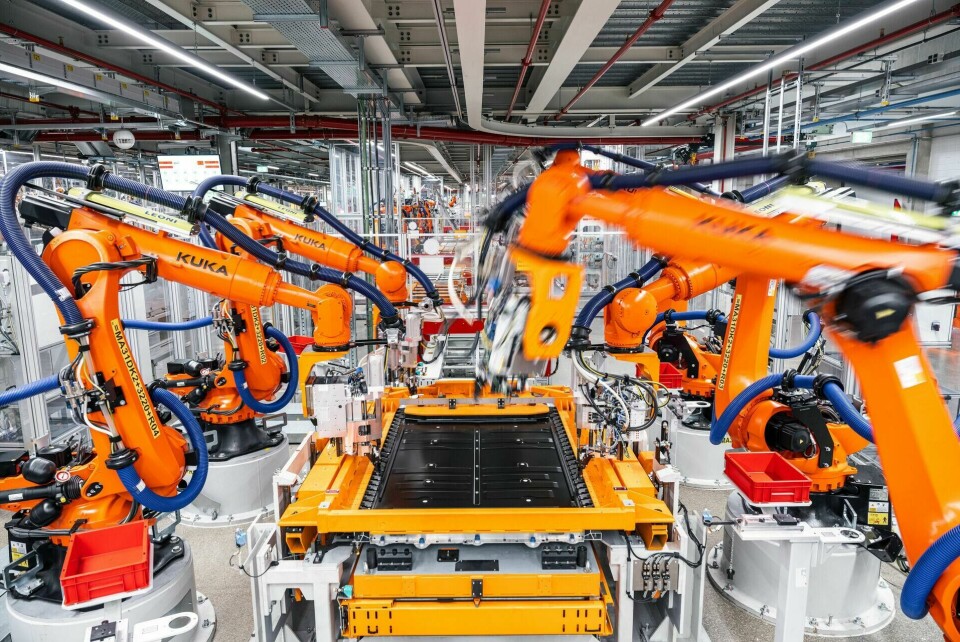
In a bid to bolster sustainability and efficiency in the production of the Q6 e-tron series, Audi has integrated several production domains, such as the bodyshop for the PPE, into existing structures.
WIth an area of 148,000 Sq. m, the Ingolstadt plant easily facilitates the assembly of bodies for PPE models. Flexibility remains a key focus, with Audi repurposing 680 robots and introducing a fleet of over 40 automated guided vehicles (AGVs) to streamline operations.
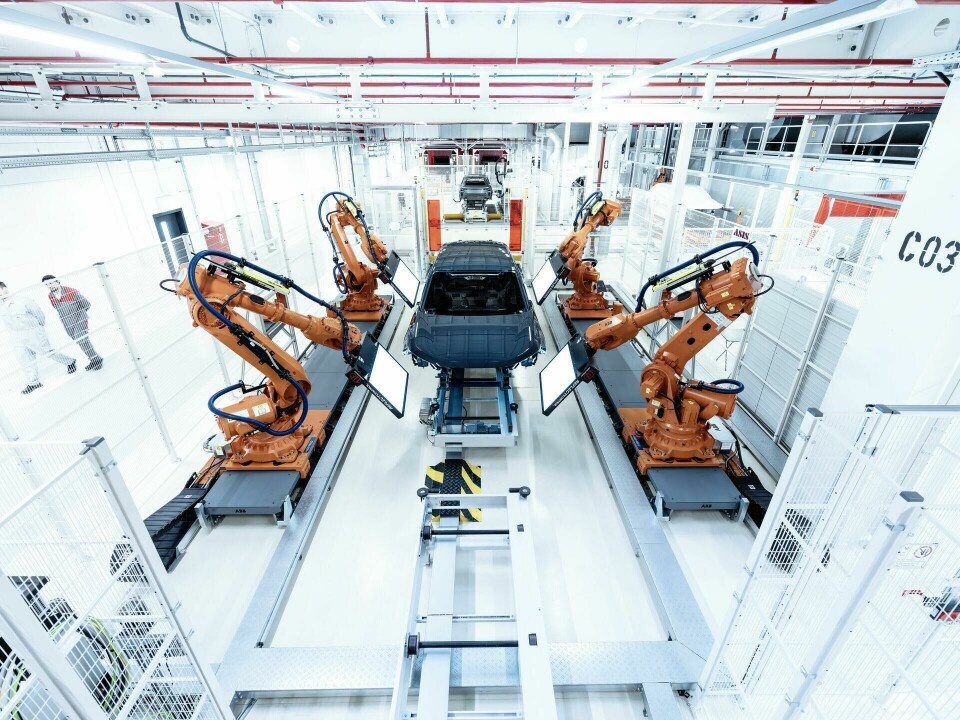
Audi’s sustainable production projects extend into assembly processes, where existing systems are leveraged for the integration of the Q6 e-tron. An official press release confirms that the assembly line, shared with Audi A4 and A5 models, underwent eight stages of modification to accommodate PPE models.
The paint shop has also undergone enhancements to accommodate the new fully electric series, including extensions to the dryer post-cathodic dip coating (CDC) and the implementation of an automated sealing procedure. These modifications ensure optimal curing of bodies post-CDC, while automated production technology enhances surface inspection, bolstering process reliability and transparency in quality monitoring.
In the press shop at Münchsmünster, the OEM has upgraded the hot-forming process to bolster stability and crash safety for PPE-based vehicles. This entails locally cooling heated metal sheets to influence component strength, subsequently employing special lasers for contour cutting.
The enhanced flexibility of the production equipment allows for the manufacture of a diverse range of components, catering to both PPE and PPC-based models.