How JLR’s circular manufacturing drives global EV growth and decarbonisation
Tomasz Jozwiak explains how Jaguar Land Rover is driving circularity across its operations by reusing and refurbishing manufacturing assets, cutting emissions, saving millions, and supporting electrification.
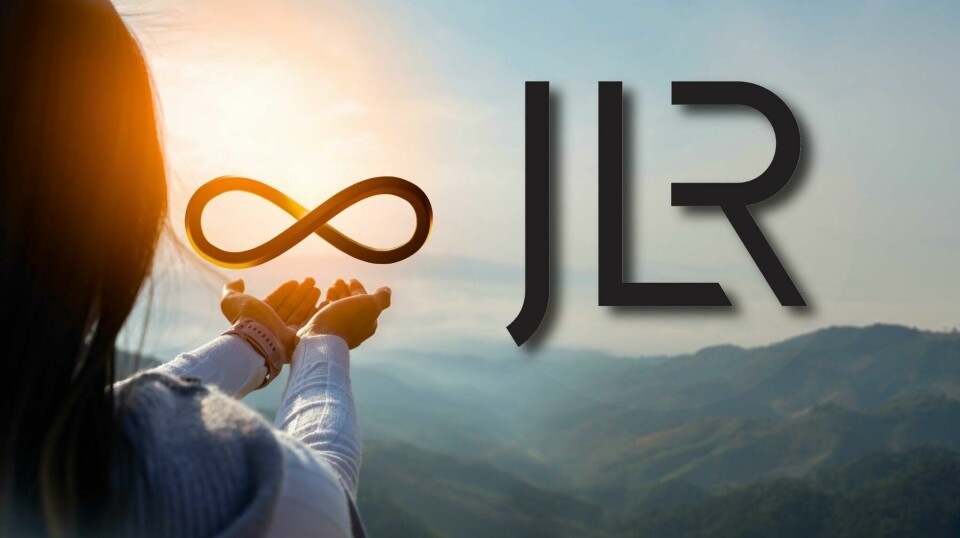
JLR is turning old tools into new value. As the carmaker pivots towards full electrification, it is not just the powertrains that are being reinvented. Across its industrial network, the luxury carmaker is rethinking the value of its past. Behind the scenes of gleaming vehicle launches and next-generation battery plants lies a less conspicuous, but equally transformative effort: the systematic and comprehensive reuse and refurbishment of tools, robots and even entire production lines.
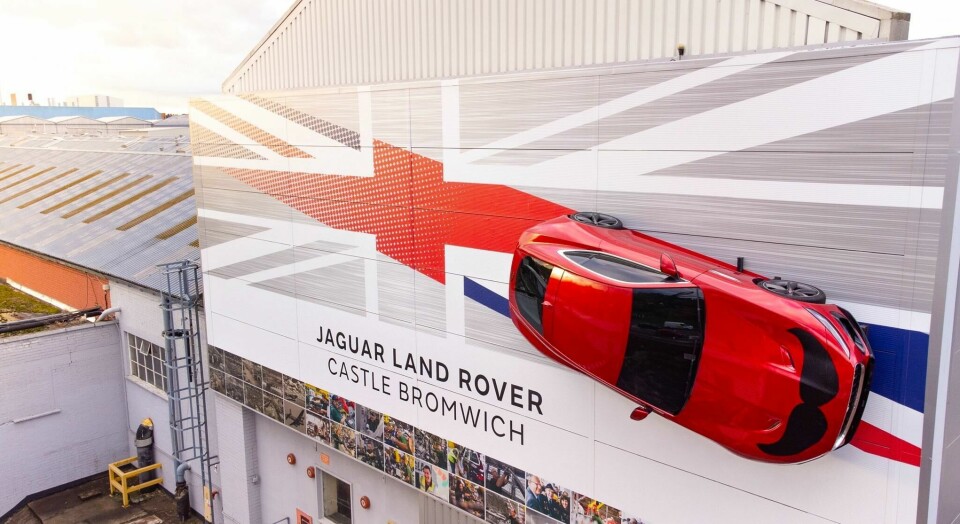
This is not recycling in the conventional sense. It is industrial circularity at scale, measured not only in ‘tonnes-of-scrap-avoided’, but in strategic flexibility, supply chain resilience and millions saved. At the heart of this programme is Castle Bromwich, once a full-vehicle plant and now a goldmine of industrial inheritance.
From this and other legacy sites, equipment has been redistributed, recalibrated and repurposed across JLR’s global footprint, supporting everything from body shops in Slovakia to battery assembly lines in Halewood.
Tomasz Jozwiak, Manufacturing Engineering Manager at JLR, is one of the architects of this transition. In this interview, he reveals how asset reuse has evolved from a reactive cost-saving measure into a proactive engineering discipline.
He explains how reuse decisions are driven not just by depreciation tables but by risk modelling, carbon calculations and digital asset tracking. And he shares how these initiatives are quietly reshaping the skills and culture of JLR’s industrial workforce.
As the carmaker seeks to electrify all brands by 2030 and hit net zero by 2039, this circular ethos is no longer a sustainability sideshow. It is central to how JLR intends to build its electric future - less wastefully, more intelligently, and, as Jozwiak makes clear, with tools that have been given a second life.
A conversation with Tomasz Jozwiak, Manufacturing Engineering Manager at JLR:
Hi Tomasz. Thanks for sitting down with us today. Diving in - can you describe how the cross-functional team identified and prioritised assets for reuse across JLR’s manufacturing network? What criteria were most important when deciding whether to refurbish, redeploy or scrap?
Tomasz Jozwiak, Manufacturing Engineering Manager, JLR:
So I’d say it started with setting up an asset governance forum for the projects I was directly involved with, particularly vehicle cessation projects, like the full vehicle cessation at Castle Bromwich. We also exited Plant Graz, our contract manufacturing facility in Austria, and there has been significant transformation at our propulsion centre.
We pulled together a group of senior figures from relevant technology areas - final assembly, body-in-white, paint, stampings - so we had a director-level steer on strategy and approach. Frankly, we weren’t prepared for the amount of assets that suddenly became surplus in such a short period. That wasn’t the original plan, but plans changed rapidly for various reasons. So we had to act quickly to stay in control.
”If you wait long enough, more assets can potentially be reused, but there’s a threshold”
Tomasz Jozwiak, Manufacturing Engineering Manager, JLR
We included technology leads to ensure we had visibility into what assets might be required in future projects. These directors typically have a good forward view of what’s coming. We also involved our procurement team - both those buying new equipment and those responsible for selling surplus assets. Finance colleagues were brought in to ensure compliance with depreciation procedures and business policies. We had regular conversations with the affected plants and the site strategy team to understand what was coming into our manufacturing footprint and when.
If you wait long enough, more assets can potentially be reused, but there’s a threshold - you have to draw a line somewhere and say, “This space is better used for something else,” and reduce the asset footprint in storage. It became about understanding what assets we had, what we might need, and over what timelines - essentially a master schedule outlining what was becoming surplus and what we were likely to procure over a 12-to-36-month time horizon.
Storage logistics also came into play. Keeping unused assets means additional CO2 from transporting them back and forth to offsite storage. Strategically, we had to think about the footprint, asset shelf life, and sustainability.
On the technical side, we pulled in subject matter experts to help assess the assets, see how they fit into our current standards and controls, and consider changing legislation. We worked with commodity buyers to understand spare parts availability and engaged with maintenance teams to identify which assets were breaking down and which were still serviceable.
Risk mitigation was another critical aspect - reuse introduces risk. For example, reused robots might be strategically placed in accessible locations so they can be easily replaced if they fail in 5 years, rather than placing them deep inside a critical production area. Planning and risk management were key.
Used assets are never quite the same, even if we aim to refurbish them to a standard. Like cars, they can last longer if well maintained, but not forever. We educated ourselves on what these assets are made of, what wears out, what lasts, and how to find a balance between reuse potential and the operational footprint.
Read more JLR stories
- JLR creates 150 EV manufacturing roles in the UK
- 5G networking: How JLR is building smarter factories
- Making vehicle manufacturing more flexible at JLR and Daimler
- JLR resumes US exports as automotive tariff risk looms
We also considered sales if assets couldn’t be reused within three years. And if neither reuse nor sale was viable, we assessed scrapping options. That involved segregating metals and improving recycling outcomes - not something we typically do with full equipment. We normally think about scrap from offcuts, not whole systems.
Sometimes the choice between scrap and sale came down to a fine margin. In those cases, we leaned towards doing the right thing - selling and giving the equipment a second life, provided it didn’t significantly diverge from the plan.
It was a heavily cross-functional process, constantly evolving as new inputs came in. Deciding what to reuse, sell, or scrap has been and continues to be a dynamic assessment.
What role would you say Castle Bromwich has played in this reuse initiative? You’ve touched on redistribution, but what about adapting legacy tooling for modern or EV-focused production lines?
Castle Bromwich played the lead role in this repurposing effort. In 2021, under our Reimagine strategy, we decided to stop full car production at the site. At one point, Castle Bromwich had capacity for building 200,000 vehicles per year with several body shops, a paint shop, and a large trim and final area.
We managed to reuse assets from Castle Bromwich across Solihull, Halewood, Nitra in Slovakia, and even Brazil. Just this week, I was on a call discussing the dispatch of final assembly carriers to Tata Motors in India, where they’ll be used to build JLR vehicles. That gives you a sense of the global reach of this effort.
We had been preparing Castle Bromwich for electric vehicle production, so much of the equipment there was unused - still in shrinkwrap. That made the scale and value of reuse opportunities unprecedented. People who’ve been at the company for 30 or 40 years said they’d never seen anything like it.
One achievement I’m particularly proud of is our ability to reuse across different technologies. Body shop to body shop is relatively straightforward - modular systems like robots, riveters, welders, and conveyors can be transferred easily. A lot of equipment now building Range Rovers and Range Rover Sports - including the BEV variants launching later this year - originated in Castle Bromwich.
We also reused body shop equipment in the propulsion centre. For example, surplus riveting machines once used to build the Jaguar XE and XF are now assembling aluminium frames for EV battery packs for the EMA platform at Halewood.
We repurposed roller beds from body shop for use in Castle Bromwich’s paint shop for a new Special Vehicle Operations project - there’s even been an article about bespoke paint at Castle. We’ve supported training for apprentices and graduates by supplying them with robots and AGVs, and we’ve provided equipment for technical workshops and labs at our engineering centres in Whitley and Gaydon. Even pilot plants for EDU and battery frame assembly have benefited.
My team’s role is to connect the dots across the business. We visit plants, learn about projects, and when someone says they have surplus equipment, we know who might need it. It’s about avoiding duplication - scrapping something in one place while buying the same thing elsewhere.
We follow a structured hierarchy: Can it stay where it is? Can we repurpose the space? Can we lift and shift the whole system? If not, can we break it down into components? Can it be sold? Only then do we consider scrapping.
”Future phases will incorporate detailed asset data. We want acquisition details, technical specs, and maintenance records logged - like a birth certificate for every asset”
Tomasz Jozwiak, Manufacturing Engineering Manager, JLR
Tell us about the digital asset management system… Has it, or will it change how JLR tracks and manages tools and equipment?
The system itself is still under development. But the first phase will go live at Castle Bromwich for testing later this summer. It’s essentially an internal marketplace - like eBay - where teams can advertise surplus assets using a standardised template. This enables browsing and direct connections between teams, rather than funnelling everything through my team of ten.
This will help scale the reuse effort, making it sustainable in the long term. We identified it as a fundamental requirement if we’re going to maintain momentum over the next 3–5 years.
Future phases will incorporate detailed asset data. We want acquisition details, technical specs, and maintenance records logged - like a birth certificate for every asset. That record will be maintained throughout its lifecycle so that end-of-life decisions are informed by full service histories.
This helps us determine whether an asset can be reused on a high-volume line or not. For example, if a robot has already done a high number of cycles, it might not be suitable for a 10-year programme.
Right now, we’re starting from the back - we have lots of assets already, so we’re building the marketplace first. That helps us reach more internal customers. But over time, this enterprise-grade platform - which we already use for customs, vehicle development, and more - will transform how we manage reuse.
”For the 40–50 pumps we reused, the total carbon savings exceeded 200 tonnes, and we saved just under £2 million”
Tomasz Jozwiak, Manufacturing Engineering Manager, JLR
Can you give an example of a specific reuse or refurbishment project that delivered significant cost or carbon savings?
The best example is the reuse of adhesive pumps from Castle Bromwich’s body shop. These pumps are used extensively in aluminium body construction for both sealing and structural bonding.
We asked the supplier to propose a plan to lift, refurbish, and integrate them into the new EV body shop at Halewood - before the Castle line even stopped. The supplier returned a detailed breakdown: cost savings and CO2e savings pump by pump. These are industrial-scale pumps for 200-litre barrels, worth about £100,000 each.
Refurbishing them saved 75–80% of CO2e versus buying new. For the 40–50 pumps we reused, the total carbon savings exceeded 200 tonnes, and we saved just under £2 million. So it’s like a rule of thumb: £1 million saved equals about 100 tonnes of CO2e - though it’s not perfectly linear.
We’re applying similar thinking to robots. We’ve repurposed around 600 robots so far from Castle Bromwich. Suppliers estimate that refurbishing a robot saves 8.5 tonnes of CO2e. That opened our eyes. We’re now working with our sustainability and procurement teams to create a matrix for estimating CO2e for bulk-buy items like pumps and robots.
It’s a journey. The goal is to eventually integrate carbon impact into our decision-making alongside cost savings.
How has this reuse strategy influenced upskilling within technical teams? Are calibration and safety skills more embedded now?
It’s been a learning journey for everyone, including my team. Most of us came from specific technologies like final assembly. But in the last two years, we’ve worked across all areas - body shop, paint shop, stampings - on reuse projects.
We’ve learned so much about facility design and operation. We’ve had deep discussions with standards and controls teams about obsolescence, efficiency, and new technologies. For example, pneumatic clamps are being replaced by electric ones, which are more efficient over a plant’s lifetime. Pneumatic clamps drive up compressed air costs - some plants spend £2 million a year just on that.
Teams have grown used to buying new. But refurbishing teaches them much more about equipment capabilities, limits, and compliance - including CE and UKCA marking. Every day’s a school day in this space.
From an engineering perspective, how do these circularity practices support JLR’s electrification journey? Are there any reuse applications directly supporting EV or battery production?
Nearly all our future programmes are electrified or electric. So by definition, every reuse we’ve done contributes to electrification.
We’re not building new engine assembly lines. It’s all about batteries, EDUs, and associated facilities. Reused assets have gone into battery frame assembly and EDU lines.
It also made us more resilient during the post-COVID supply chain disruption. Lead times suddenly extended from three to 12 months. But we had surplus equipment at Castle Bromwich. That helped projects stay on schedule.
This also strengthens our commercial hand. When we tender for new projects, we now ask suppliers how much they can help us reuse. If they want to keep working with JLR, they need to get onboard with our sustainability goals. Some suppliers weren’t ready for that - it’s a shift we’re driving.
Sustainability isn’t optional. It’s core to our Reimagine strategy. And if suppliers want to join us on that circular journey, they’ll need to change their business models accordingly.