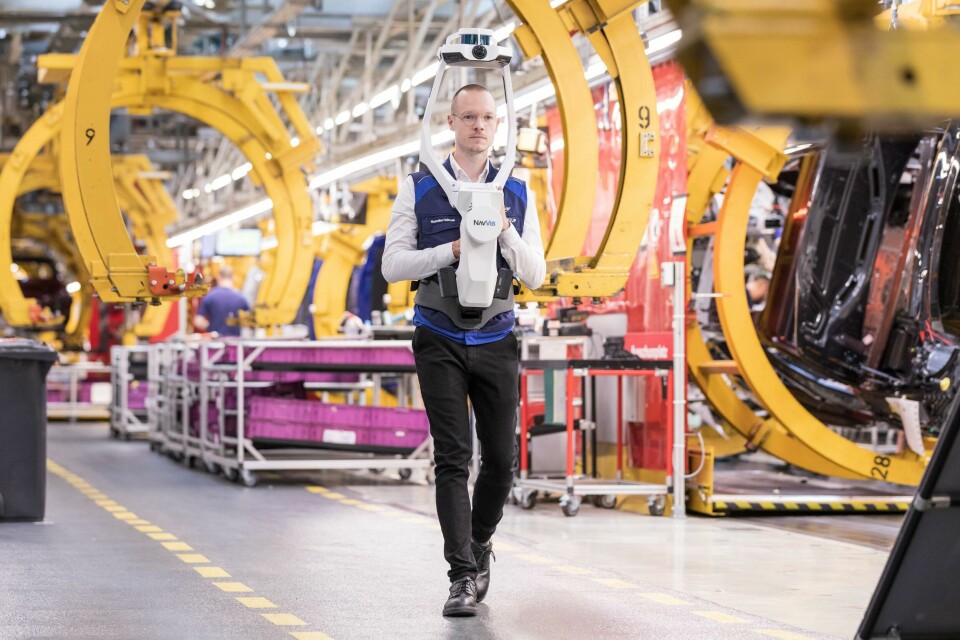
BMW Digitalisation – Virtual becomes a reality
By the early part of next year BMW aims to have doubled its production facilities around the world – not physically, but instead virtually in the digital environment
That is the target date for the OEM to have completed a project in which it will have recorded a digital scan of both the structures and production equipment in every single one of its vehicle plants worldwide. The aim then will be to use the resulting database to support both the planning of new production operations and the remodelling of existing ones in a highly efficient and flexible manner that will be facilitated in large part by enabling real time collaboration between different locations in different time zones for all forms of production planning.
Efficient planning, processes and reduced costs
The basic strategy underlying the project is confirmed by Michele Melchiorre, head of production system, planning, tool shop, plant construction at BMW Group. “This will enable us to integrate the virtual product into the virtual factory at an early stage,” he states. “This will not just reduce planning effort and capital expenditure but also ensure processes are more efficient and more stable during ramp-up.”
More detail is provided by Juergen Wittmann, head of innovation, virtual plant and digital systems, who stresses that though the scanned processes data will be dynamic, the data itself will be a record of static factors. “The digital scans provide a highly detailed and precise image of all building structures and all production facilities, including georeferencing,” he confirms. “We use the technology both inside and outside buildings, but they do only provide static data.”
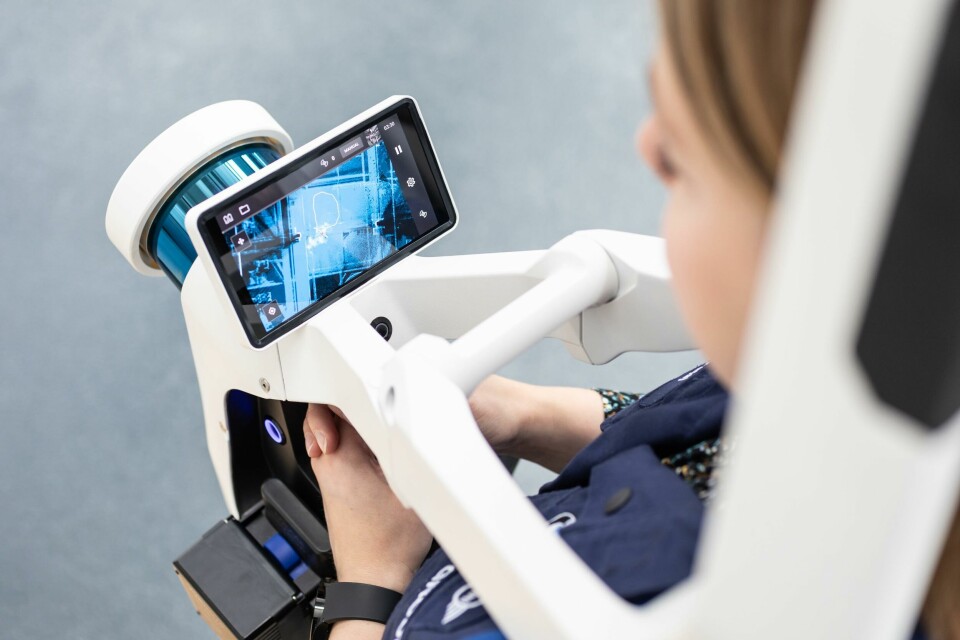
Nevertheless, the sheer volume of the data involved is massive. The project started in November 2020 and by the middle of this year BMW’s own figures are that around 4 million square metres of indoor space and nine million square metres of outdoor space at BMW Group plants had been scanned using either portable mobile scanning systems carried by humans or, for more inaccessible areas, drone-mounted systems.
This means that by mid-2022 ‘digital twins’ were already available for the US plant in Spartanburg and both the main plant in Munich and Plant Regensburg in Germany. Two more plants in Germany, Dingolfing and Leipzig, were due to be recorded by September this year along with Tiexi in China. Finally, by the spring of 2023, digital data will also be available for the BMW Group plants in Mexico, South Africa, the UK and Dadong, China. Wittmann says that when completed, the database will be in the region of 40 terabits in size.
“This approach forms the basis for planning and developing our new vehicle plant in Debrecen in Hungary. Today, around three years before the series launch, we are already able to simulate core processes at that future plant virtually”
Juergen Wittmann
Developing autonomous scanning
Interestingly, Wittmann also indicates that the company is working towards upgrading the basic data gathering methodology. He confirms that though the scans are done primarily by a human using a portable 3D scanner, the company is aiming to develop its own autonomous scanning robots. He says that one of the capabilities this will facilitate is the continual updating of the digital master data so that it remains current in the long term without requiring additional personnel effort. To this end the company is therefore using in-house solutions, such as the Smart Transport Robot (STR) developed by BMW Group subsidiary Idealworks.
But Wittmann makes it plain the project is very much aimed at the enhancement of actual production processes on a continuing basis. BMW has massive expectations for the impact the project may have on its operations. “By systematically merging the real and virtual worlds, we will be able to tap into the enormous potential for highly efficient planning of future plant structures and production facilities,” he states. “It will open up entirely new possibilities for us.”
Planning and simulation to be 100% virtual
Indeed, achieving the project’s goals is seen as fundamental to ensuring the company attains its long-term strategic objectives. “Alongside data science and artificial intelligence, virtual planning is a core element of digitalisation within the strategic vision of BMW production: the BMW iFactory,” confirms Wittmann. “The aim is to make the planning and simulation of all processes and the entire production system one hundred per cent virtual.”
“This approach forms the basis for planning and developing our new vehicle plant in Debrecen in Hungary,” states Wittmann. “Today, around three years before the series launch, we are already able to simulate core processes at that future plant virtually.”
A couple of sets of externally supplied software play key roles in the project. These are Ivion Enterprise platform from Munich-based start-up NavVis and the Omniverse platform from US-based Nvidia. The first of those provides the ability to create the digital twin, in other words the digital replica of reality, from the huge data volumes involved, while the second facilitates its exploration as if the user was actually present in the real physical environment.
“Both systems are essential,” confirms Wittmann. “BMW is digitalising its existing plants in cooperation with NavVis, which is considered one of the world’s leading providers of technology in the field of reality capture and digital twins. 3D laser scanners will be used to create photorealistic panoramic images, floor plans and scatter plots for all BMW Group vehicle plants that are accurate down to the last detail, including all building structures.”
Then for the practical exploitation of this virtual world, Wittmann continues, BMW will rely on cooperation with Nvidia and its Omniverse software. ““It will mean that planners can conduct a virtual walk-through of BMW Group plants at any time, from anywhere,” he states. “They can develop production systems together in the simulated world, compare best practices and share information quickly and easily within the network. Partnerships like these allow us to combine our own spirit and process know-how with cutting-edge technologies.”
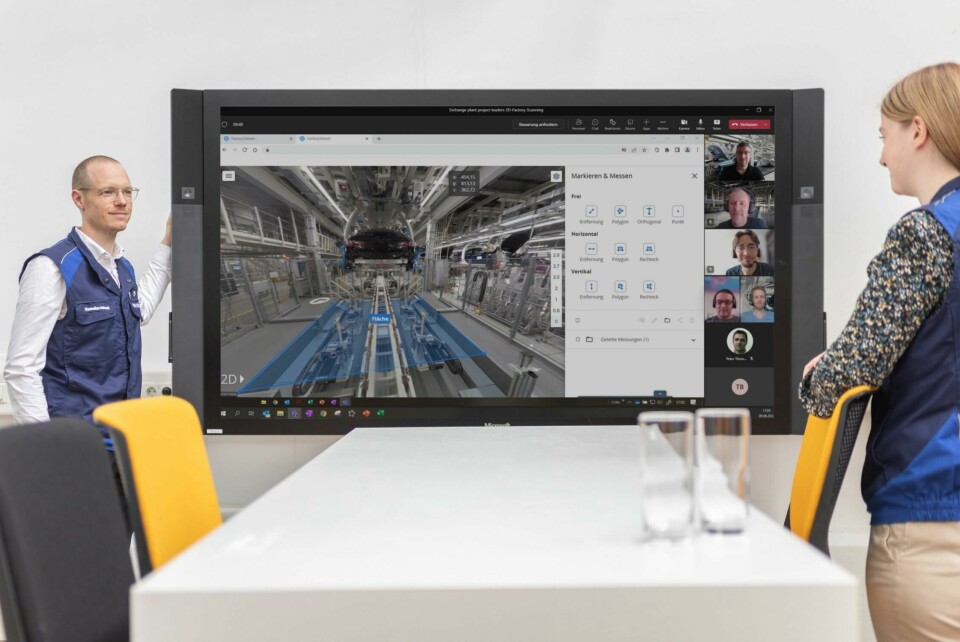
Inspections via the BMW Factory Viewer
Working within this virtual counterpart to the physical world is already pervasive within the company. “Around 15,000 BMW employees, who are predominantly production and building planners, are already working with this data, using a cloud- and web-browser-based software called the BMW Factory Viewer,” confirms Wittmann. “With the help of this software and with just a few clicks, existing plants can be virtually inspected, specific points in production found via points of interest (POIs) and highly precise measurements carried out.”
The system also facilitates enhanced cooperation with third parties. “Individual sections of the 3D scans can be cut out and made available to external suppliers, if need be,” reports Wittmann. “This saves time and effort during production planning, improves collaboration with internal and external interfaces and eliminates planning errors.”
Nevertheless, Wittmann admits that while it can serve as a useful communication tool with outside parties, the overall operation of the system does not at present have deeper strategic external implications. “It currently has no direct influence on supply chains,” he says. “But, of course, the results from the data obtained from the scanning do improve logistics flows within the plant.”
Wider applications across different operations
But the usefulness of the system within the company is also surprisingly broad. “It is accessed by engineers from vehicle development, our fire brigade and the purchasing operation, who can all also make use of the data,” reports Wittmann. Meanwhile the hardware interfaces involved are mainstream, but also appropriately contemporary. “When using Omniverse data, we use VR headsets and VR glasses.”
At a more general level the benefits provided by the system are not, as Wittmann admits, immediate and quantifiable but instead derive from the way it is integrated with other similar software-based technologies. “Required maintenance measures, for instance, cannot be detected by the scans,” he says. “However, we do use artificial intelligence systems to become significantly more efficient in this field through predictive and smart maintenance.”
Wider connectivity is the key enabling factor. “Cloud-based digital platforms and the Industrial Internet of Things connect every product, process and person through transparent, always-available and integrated data,” states Wittmann. “This extensive use of data science enhances quality control, boosts efficiency and enables predictive maintenance. The widespread use of artificial intelligence, data analytics and algorithms has shifted decision-making from ‘experience-driven’ to ‘data-driven’.”
The ultimate benchmark for all of this, though, is whether it helps BMW design and make better vehicles and Wittmann has no doubt it does. “Of course, at the end of the day highly efficient and optimised manufacturing processes lead to more freedom in vehicle design and also to further improved quality of the final product due to more efficient systems.”