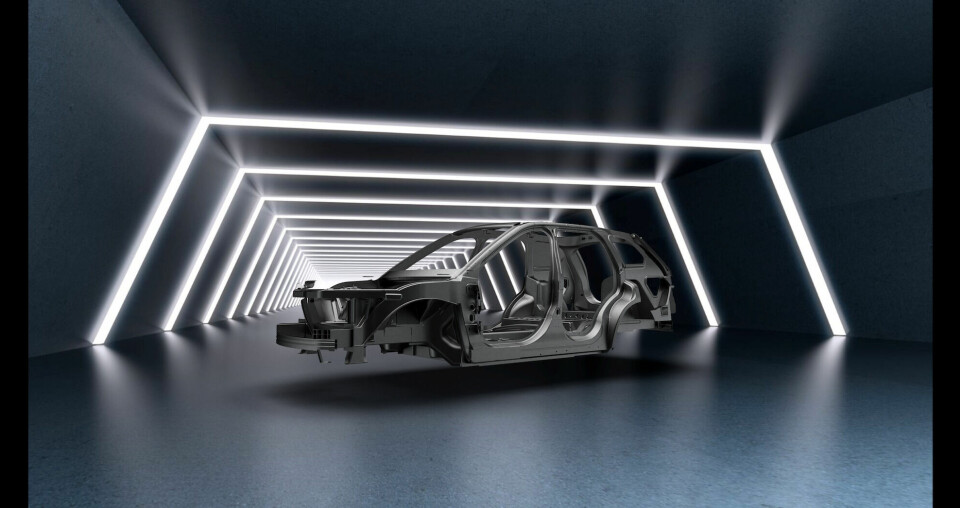
Changing dynamics– developing the next generation of vehicle architectures
Building electric vehicles has demanded big changes in OEM production operations and increased support from tier suppliers. Gestamp’s director of R&D North America, Paul Belanger, shares some insights into the company’s development and how it’s managing the engineering challenges around EVs
One of the biggest changes in automotive manufacturing we’ve been seeing in recent years, is in the working relationships between tier suppliers and their OEM customers. This has evolved from simply supplying parts at an agreed volume and price, into much more collaborative partnerships where they are involved much more upstream in the design and development stages.
Commenting on these developments and the challenges currently being faced by the industry, Paul Belanger, Gestamp’s director of R&D North America, notes that volume uncertainty and changing market dynamics around the transition to electric vehicles are something that OEMs and tier suppliers are having to manage.
“There are certainly a couple of big talking points. On the business side, the volumes aren’t quite what they were predicted to be, and so that poses some challenges. And I think the whole industry is trying to figure out how to wrangle with that one.
“But also on the technical side, when you are dealing with vehicle architectures, you’re looking at the long term, at planning the lifecycle of a product, and this is also being affected by this uncertainty.”
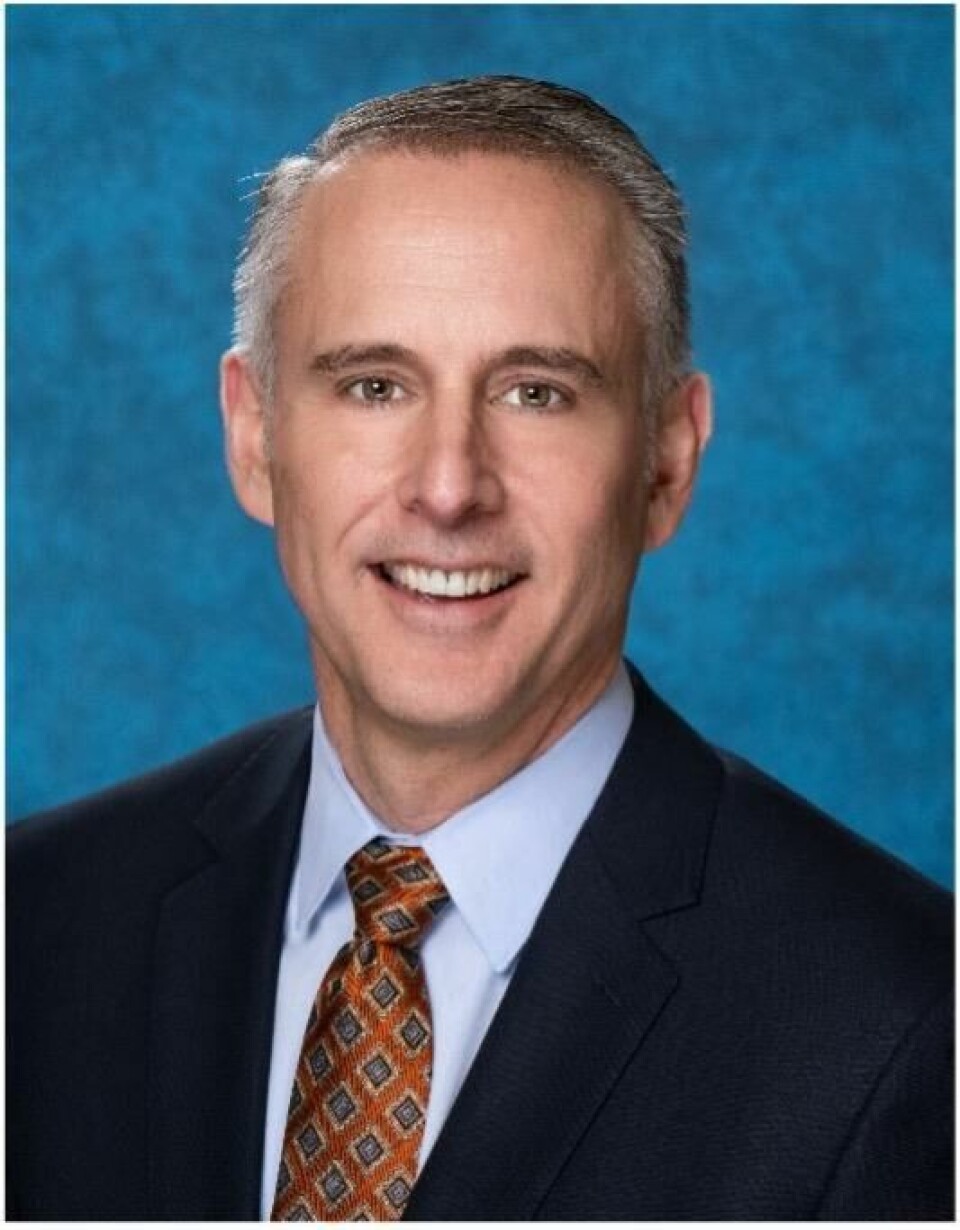
Simplifying components and boosting flexibility in production
As a designer, developer and manufacturer of vehicle platforms and body components, Gestamp recognises the importance of close working relationships with customers and is well placed to see areas of demand and the trends emerging in the automotive industry.
As we’ve seen the transition to electric vehicles is complex, especially for those OEMs building both ICE and electric powered vehicles. Here, managing costs and process complexity are key to viable production operations. For the major OEMs having established manufacturing facilities can be both a help and a hindrance; while these facilities and the production expertise can mean reduced capex to build new platforms, they can also be more challenging to flex to new vehicle technologies. As such, a big trend is to simplify the production processes.
Belanger points to reducing complexity in the vehicle structures as one solution.
“We’re seeing more interest in part consolidation, ways of making larger parts with fewer components and simplifying that design development process. And this is coming from start-ups and also established vehicle makers.
“For us this is helping the customers reduce costs, vehicle weight, cycle time in their bodyshops and CO2 emissions in production, and this is coming into play more and more, even with the battery electric vehicles.”
The large-part idea is something which has initially been seen front or rear floor sections, produced using a gigacasting process, utilising aluminium as the material. This marks a big process step for the vehicle makers, even where they are not producing the parts themselves. In response to the increasing demand for these components, Gestamp has itself developed a large-part production process for stamped, steel parts, Gigastamping.
Belanger offers an example of the type of large-scale component that Gestamp has been developing.
“If you look at an established OEM’s bodyshop, this will take A- or B-pillars, or a sill, and welding those together, and then present that part of the structure into the body framing line. But, if they’re able to get that as a single part from a supplier, that can help them rebalance their line.
“Their goal might be to produce more derivatives, so reducing the number of processes they do, they’re able to maybe add a derivative into that bodyshop by freeing up floor space. This could be one potential driver why a legacy OEM might want to entertain using extreme size parts. The other aspect of these large parts is the value proposition, whether it’s a weight reduction or a cost reduction.”
Supporting manufacturing engineering and design decisions
This offers a good insight into the manufacturing engineering decisions OEMs are making in adapting their production lines and managing costs and complexity. For tier 1 suppliers like Gestamp there is considerable development required in the design for production of the part and the process. Belanger notes that the R&D team utilises both external and internal development tools. Software represents the external side, being sourced outside of the company to support development projects, and Belanger notes, except for AI at some point, yet to be fully explored, these are relatively stable tools, regularly deployed.
But it is with the internal tools that the scope and scale of development resources required is revealed. Here is where Gestamp has created its G-Lab vehicles. Belanger shares some insights into this.
“Our G-Lab vehicles are basically fully built, virtual vehicle models, and we have just updated two of them for the battery electric vehicle (BEV market). We have a C-segment sedan, which is a full BEV, and a D-segment SUV, for which we have two versions, a hybrid and a BEV. These are internal tools that we’re developing to help prove out our concepts to our customers, whether it’s a gigacasting, or Gigastamping, etc. We can design it virtually and show how it performs in the virtual world.
“We employ a lot of benchmarking services, and we can look at all the OEMs and what they’re putting on the market. The newest ones, of course, get evaluated. So, for example, we can simulate the best A-pillar section, the best sill or rail structure from range of OEM’s models and combine these features together in these virtual vehicles. We do a lot of benchmarking to establish what we think are the best concepts, then virtually make sure they satisfy all the required crash loads that we must design for.”
Belanger notes that this enables Gestamp to develop the best solution for key parts of the vehicle structure and provide OEMs with the right solution, or even a complete architecture.
”We can take it down to the subsystem level, put in different materials and also input older architectures to see how the newer ones compare. So, we’re able to pull a lot of different levers to show the benefit of the new architecture and the new materials.”
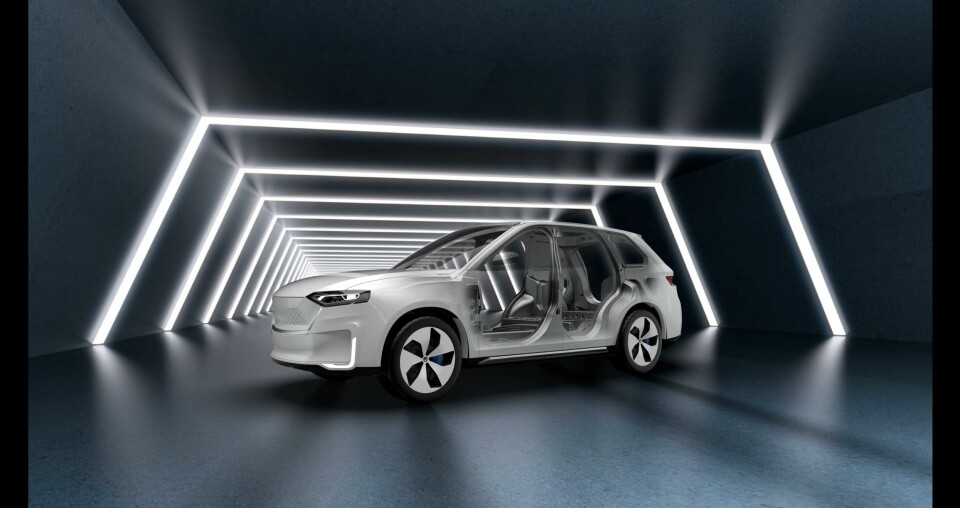
Tech watch and managing disruptors
Designing chassis and body structures for production has always been part of Gestamp’s remit but with the ongoing transition to electric vehicles the development teams need to have a greater awareness of systems outside of this remit which impact on structural designs. Battery integration is one such area. While the company is actively developing and producing the enclosures (what Gestamp calls the battery box) it isn’t involved in battery cell or pack design and assembly. But as Belanger observes this critical component presents many engineering challenges, so understanding the different facets of battery design is important.
“There’s always an element within Gestamp and our innovation technology organisation where we’re on ‘tech watch’ to understand what those disruptors are that could impact our business. So, we are always looking at those new developments that happen in areas that really aren’t our specialty.
“For example, we’re trying to always make sure we understand the battery chemistries.It’s so dynamic. We don’t produce batteries and we don’t have any plans to produce batteries but understanding its impact to the things that we do produce (the battery box) is critical. If we understand the trends and then we’re properly prepared for our innovation to meet those future requirements.”
Even in the more familiar areas of vehicle structures there are new features which require a different approach to provide a solution. One such feature is the result of space being freed up by the absence of the ICE powertrain; the Frunk, a new load space found under the hood of Ford’s F-150 Lightning. While this might seem a novelty, it illustrates how designers are taking advantage of the new EV powertrain layouts. But from an engineering and production point of view, there’s far more to this than simply adding an appropriate liner to the empty space, as Belanger explains.
“To take full advantage of this body structure you want that front area to be really deep, so you can fully utilise the storage. This means that the chassis component is going to be lower than it was typically, and that gets down into the area of crash management.
“In the past, chassis components were mainly for ride and handling, dynamics and durability. Those were the attributes that they needed to be designed for. In this case they’re now in the load path and so they also have to operate for crash, and it has to work simultaneously with the body. So, it requires a lot of collaboration between the chassis engineering teams and the body engineering teams, and organisationally, we’re starting to see those two groups come closer together because those components now have to interact with each other so closely.”
Building sustainability into the design
Developments in the production processes are also ongoing with the company expanding its research in joining technologies. Belanger points to the potential need to integrate non-metallic materials into the body structure. The company has established a new laboratory in Bilbao, Spain (part of the 13 R&D centres Gestamp has around the world), which is focusing on friction stir welding to study different parameters and materials. There’s also a strong emphasis on remote laser welding..
Sustainability is also an important consideration in the development and production process, with Gestamp having signed several agreements for the supply of fossil free and recycled steels. Belanger explains how factors into the R&D process.
“This topic, Environmental, Social and Governance (ESG) is important to Gestamp. From a technology, R&D standpoint we have been focused on safety and lightweighting for years, and there’s a direct correlation between lightweighting and CO2 reduction. So, it’s been in our ‘DNA’ for a long time, and now lines up really well with the ESG goals of reducing greenhouse gas emissions. So, we continue to work on trying to find the best lightweight designs because that’s one definite way of reducing CO2.
“But we also look at the raw materials. With these ‘low-emission’ steels we need to understand how they work, how they perform, especially with hot stamping. Because in some cases they might have different residual levels from the scrap content, and we must ensure those residual levels are going to not adversely affect the product. As a result, we do a lot of work on validating those new materials to make sure that they work in forming, in crash applications, but also a lot of that development is focused on the decarbonisation of the raw materials.”
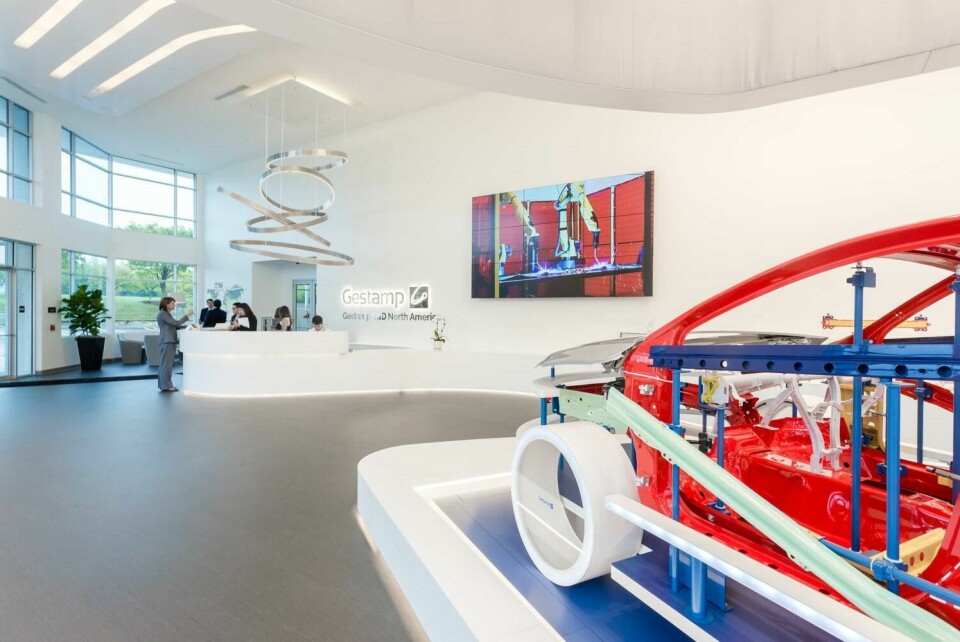
Refocusing teams and adding competences
The transition to electric vehicles and adopting new technologies has required many companies operating in the automotive manufacturing sector to bring in, or develop new competencies, restructuring teams or establishing new ones. Gestamp is no exception and Belanger outlines how his R&D team is responding to this requirement.
“Over the last two or three years we’ve added several new competencies into our innovation and technology office. For example, we’ve added aluminium technology, focusing on extrusions, but that team is going to expand into castings as well.
“We’ve also added a group focussing on composites and non-metallics, as we see an opportunity for some of these composite materials to play a role in battery tray covers, that have thermal protection capabilities. And we’re also looking at some of our existing technologies and how we can adapt them to better serve the battery electric vehicle architecture.”
Belanger notes that there has been a significant reorganisation of R&D operation over the last 12 months. This has seen a reshuffling of some of the teams and a small amount of expansion. He adds “It’s a very dynamic industry that we’re in, so we’re always going to have to be changing to adapt to it.”
Continuing EV architecture development
EV architectures occupy a lot of R&D time now and Belanger offers some insights to the key areas of development, noting considerations around vehicle weight and battery integration as two big challenges.
“At a high level, lightweighting continues to be very important because it directly correlates to range for electric vehicles. On more on a local level, when you move that big, heavy battery to the bottom of the vehicle, handling side impact is probably one of the tougher challenges right now. And the weight of the batteries (the EVs are getting heavier) means roof crush strength has to be addressed, for example working out how to strengthen your pillars.
“We really think the Battery box is going to become less complex in the future. The first-generation Battery boxes were very complex, and therefore, quite expensive. What we see going forward is that the body architecture will take on more of the crash responsibility to protect the tray and its content, lightening those requirements on the battery tray itself. This will result in a simpler and less costly Battery box.”