The co-evolution of EVs, architectures and production processes
Electric vehicles and batteries are influencing automotive manufacturing decisions, driving changes in vehicle architectures, production processes and material choices. Gestamp and ArcelorMittal discuss their strategies
Different forms of energy lead to different forms in body. Despite sounding mystical and dubious, this is a hard fact of automotive engineering. The movement away from traditional combustion engines towards new battery chemistries driven by EVs is leading to new architectures, but with this, come added complexities as OEMs and tier suppliers focus on optimising platform performance and cost efficiencies.
The key development areas around these shifts naturally include platform choices that require flexibility; adaptations to the emerging EV body assembly processes; and material choices for battery enclosures. Integrating a battery pack into a vehicle body involves a significant level of engineering which impacts battery enclosure and crash protection systems.
“In the past, the focus was on weight saving through materials like press-hardened steel. Now, the total cost, including manufacturing costs inside OEMs, is crucial”
Jesse Paegle, Automotive Steel Solutions Director, ArcelorMittal
Paul Belanger, Director of North American R&D Centre at Gestamp, and Jesse Paegle, Automotive Steel Solutions Director at ArcelorMittal, recently discussed how electric vehicles are driving manufacturing decisions in an exclusive AMS Automotive Evolution Livestream which was hosted by AMS Editor, Nick Holt. The conversation looked into how vehicle bodies face the challenge of balancing weight, durability, sustainability and cost while maintaining production viability without compromising vehicle structure.
The evolution of vehicle architectures - and strategies
Automotive architectures are constantly evolving. Previously, front loads in crash events were handled by combustion engines, now replaced by central heavy battery packs. Legacy OEMs are adapting existing assets, while newcomers use a clean sheet approach, incorporating large aluminium high-pressure die castings. The industry is seeing a trend in part consolidation and different approaches between legacy and non-legacy OEMs, says Paul Belanger, R&D Director at North America for Gestamp.
The cost of innovation
At ArcelorMittal, Jesse Paegle, Automotive Steel Solution Director says the company is adapting to both brownfield scenarios, with existing production lines, and greenfield scenarios. Their approach varies depending on whether they’re dealing with pure electric vehicle producers or those making ICEs, plug-in hybrids, and BEVs.
ArcelorMittal is focusing on flexibility and integration of components, especially in high-pressure diecasting approaches. It’s crucial to integrate as much as possible to provide OEMs with the flexibility to produce different models. Design now involves integrating the manufacturing process, moving beyond just weight reduction.
“Integration offers opportunities for innovation in designing seamless load paths while considering system cost and complexity”
Paul Belanger, Director of North American R&D Centre, Gestamp
In the past, the focus was on weight saving through materials like press-hardened steel. Now, the total cost, including manufacturing costs inside OEMs, is crucial. ArcelorMittal is evaluating costs by considering the assembly process within OEMs, moving beyond just weight evaluation. This approach is vital for flexibility, especially in brownfield scenarios where different vehicles with various powertrains are produced on the same line.
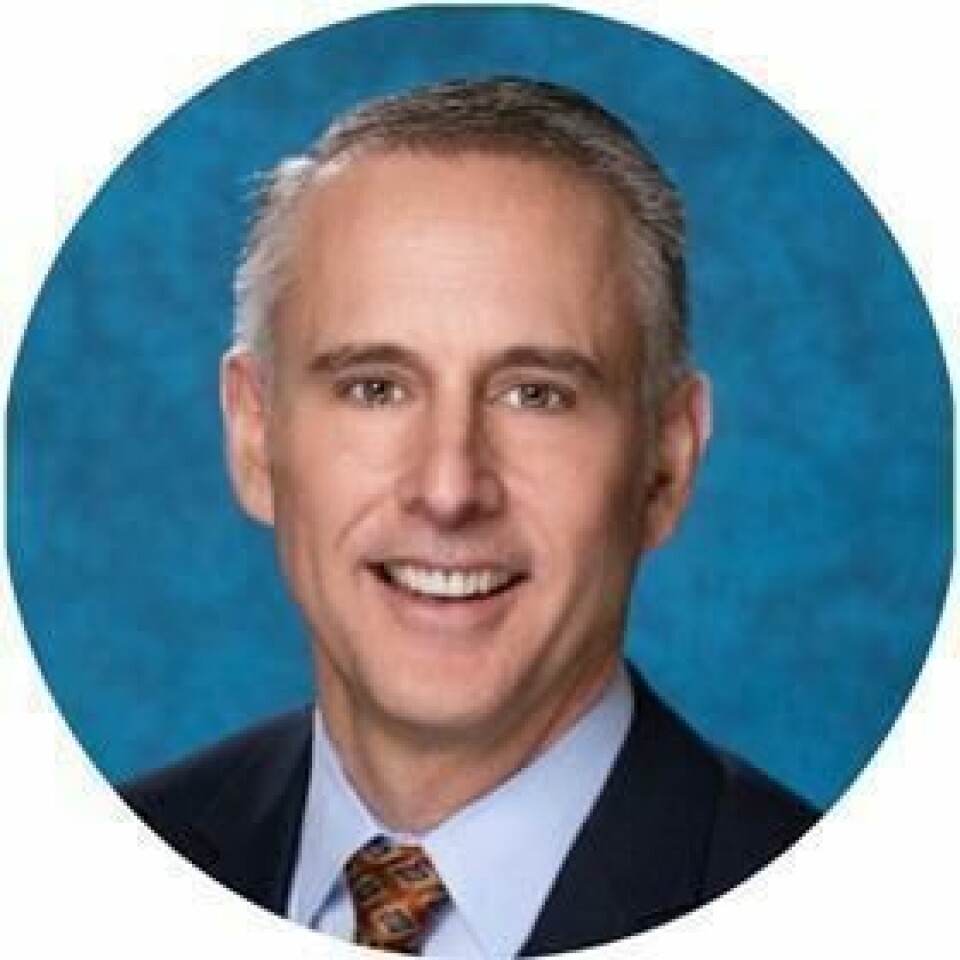
For Gestamp, certain cost considerations have always been important, but now there’s a stronger focus on system costs. The EV market growth in the U.S. hasn’t met predictions, partly due to cost parity issues. Gestamp is seeing a shift in crash management responsibility from battery trays to the vehicle body, through simplifying battery trays and reducing system costs. CO2 reduction is also a growing concern, with trends like lightweighting and hot stamping to reduce material costs and CO2 content.
Key differences between ICE and EV structures
With EVs, the absence of a front combustion engine and the presence of a heavy battery pack change the load and require different architectural designs. Chassis components now have a role in crash management, necessitating integration with the body.
This integration offers opportunities for innovation in designing seamless load paths while considering system cost and complexity, says Belanger.
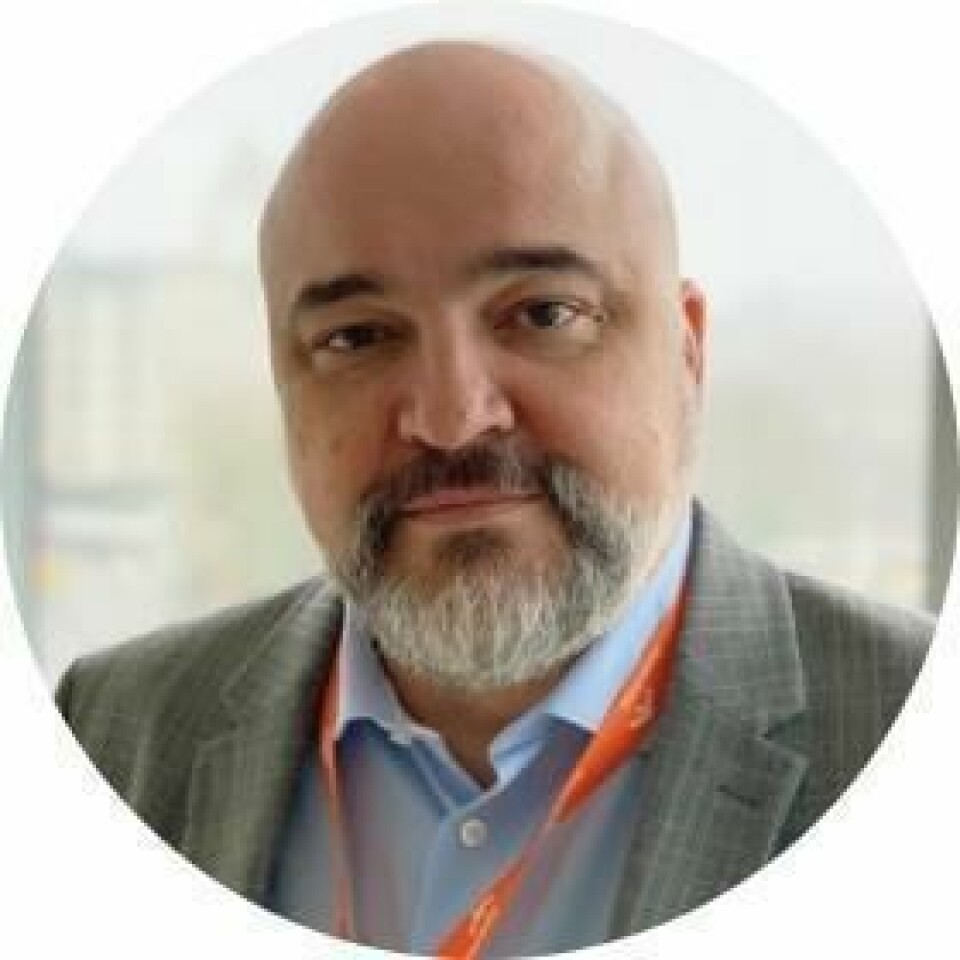
Paegle says designing EVs requires a holistic approach, integrating chassis, battery pack, and body in white. The development process involves all OEMs and tier ones working together, integrating design with the manufacturing process.
Baking vehicle design into the development process
For Gestamp, early involvement in co-development is crucial for driving innovations. This approach allows it to influence vehicle design significantly, especially in areas like crash management and system cost optimization.
The EV market is still very dynamic, with continuous iterations and benchmarking. Battery chemistries are evolving rapidly, and the industry is not yet at a point of stability in vehicle design and production. The market is highly dynamic, with changes occurring rapidly. As ArcelorMittal needs to be agile and responsive to these changes.