The evolution of EV battery enclosures: balancing optimisation, safety and cost-effectiveness
They protect the most valuable part of an EV—but what are battery enclosures currently made of? What could they be made of? And what are their key design considerations?
One of the most important components in an electric vehicle (EV) is arguably the part that keeps the battery dry, secure and safe in the event of a crash or fire. There are many terms used to describe this part, including housing, casing, tray, box and enclosure; more, indeed, than the number of materials used, which currently amounts to steel, aluminium and heavy-duty plastic.
Not surprisingly, complete EV battery packs are considerably heavy, often accounting for around 40 percent of gross vehicle weight; and when you consider the contents of battery packs—cells and modules, thermal management, battery management system (BMS), separators, wiring and the electrolyte through which the ions travel—it’s easy to see why they can also be very costly, totalling up to 50 percent of the vehicle’s value.
That’s why batteries need to be handled with care when in use, as well as after their time in an EV; and when an EV battery reaches the end of its useful life in an electric vehicle, it still has much to offer the world, either through recycling or second life applications, so its contents need to be accessible.
Sealed firmly shut
But the battery enclosures used in the first wave of EVs to hit the market after 2010 were designed to be sealed firmly shut. This took to an extreme the need to be impenetrable, crash proof, fireproof, waterproof and tamper-proof and resulted in mostly irreparable batteries and recycling processes that frequently require people in protective clothing using crow bars to prise open the enclosures protecting these very heavy, high-voltage machines.
Critical for contemporary battery enclosure strategy is design for disassembly, fire and thermal runaway protection, crash performance and recyclability. But the EV battery market is evolving fast, with frequent changes in battery chemistries, battery formats (pouch, cylindrical, prismatic) and battery technologies, with the arrival of solid-state battery technology drawing ever closer. And all of these have implications for the EV battery enclosure.
What, then, are the material considerations for battery companies and automakers when designing EV battery enclosures? Abey Abraham, Principal, Automotive and Materials at consulting firm Ducker Carlisle notes that safety is always a primary consideration, but there’s a trade-off between cost, size and weight – and these latter considerations are complicated by packaging space and battery formats also influencing material selection.
As will be seen, the role of the battery enclosure within the vehicle structure is evolving, adding structural requirements, continues Abraham, which in turn raise questions about material availability, joining technologies and serviceability requirements.
The SAE notes that around 80% of current EVs have an aluminium battery enclosure, with steel dominating the remainder, but new thermoplastic solutions offer a lightweight and innovative alternative to metal solutions.
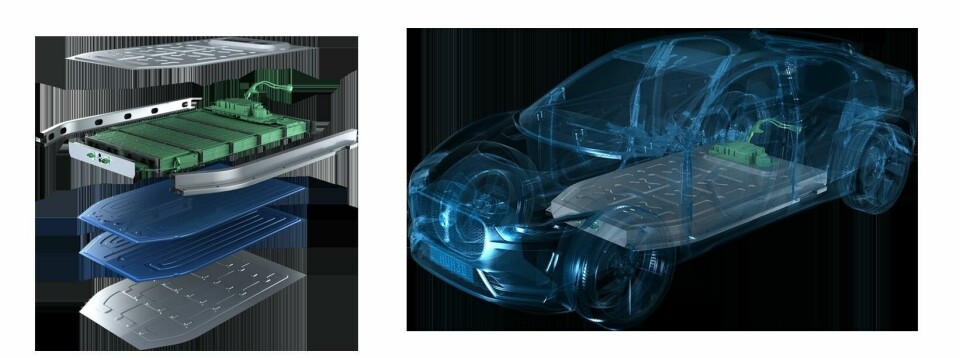
Material considerations
The age-old steel versus aluminium debate continues in the world of battery enclosures, with suppliers of each claiming greater suitability than the other.
Makers of steel promote its advantages in high strength and formability and repairability, and cost-effectiveness, with less carbon intensity in production than other materials.
Aluminium suppliers emphasise lightweighting, recyclability, cost advantages and for sheet aluminium, higher pack energy density than steel or aluminium extrusions.
There is, however, an acknowledgement of potential for multi-material solutions and ArcelorMittal is keen to work with other materials suppliers. “I’m a steel maker, but nobody is going to believe in my solution if I try to sell just steel,” says Jesse Paegle, Automotive Steel Solution Director at ArcelorMittal Europe.
“You could think of us as a steel company supplying solutions, rather than a company supplying steel solutions.”
Unsurprisingly, Paegle doesn’t expect to partner with aluminium suppliers, but he does see opportunities for plastics and even glass fibre. “We need a solution because our customers are exploring different options. And we believe we can be cost competitive versus aluminium.”
Karisma Leftinger, who heads up the Novelis Solution Centre in Detroit, counters this, saying that “Compared to steel, an aluminium enclosure is in the realm of 30 to 40 percent lighter. It ultimately depends on the structure itself.
Some structures can be more efficient than others, depending on customer requirements not only for strength, but also stiffness.” With that in mind, why would anybody not choose aluminium?
Leftinger notes that steel’s lower cost reputation prevails and Novelis is working to challenge this notion with studies that show the impact of weight savings on a whole-vehicle level, with secondary weight savings rather than a per-part comparison.
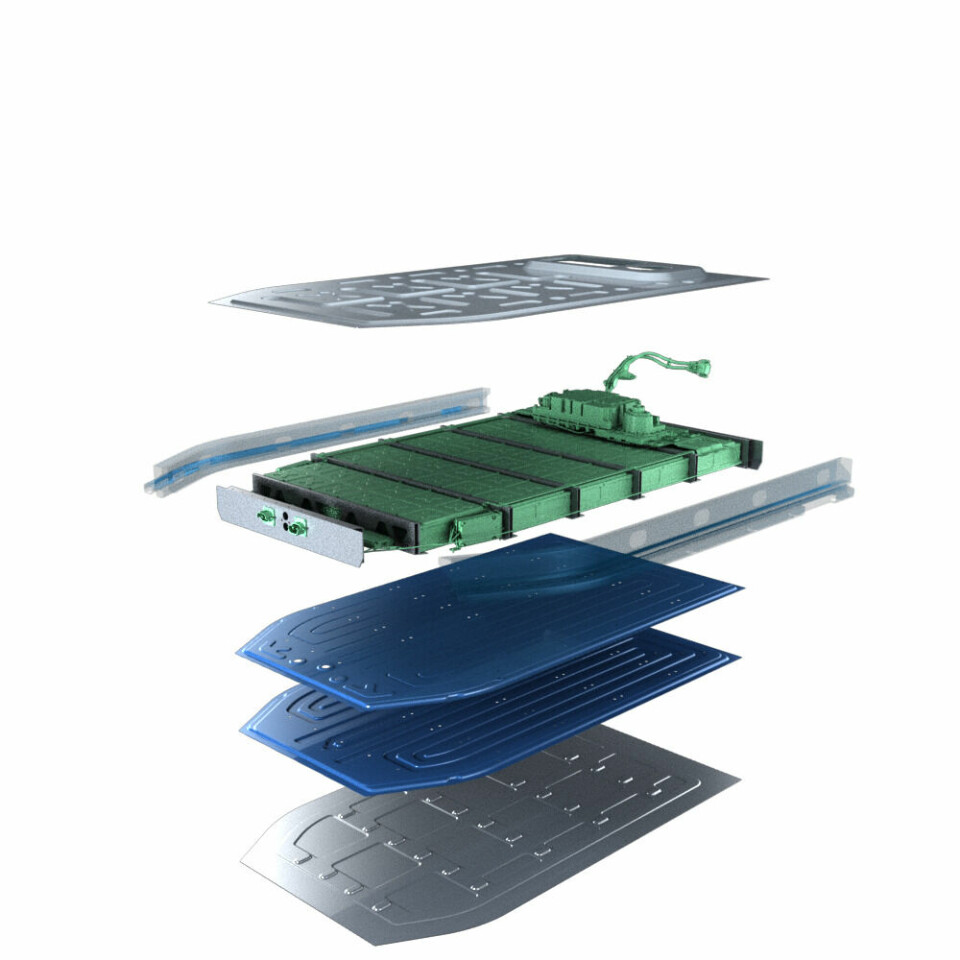
“We’ve learned that often customers use steel because they were unaware there was a highly formable aluminium solution in our portfolio that would meet their requirements,” explains Leftinger, “or that with small modifications to their design, they could use aluminium and benefit from the material’s weight savings. In terms of top covers, aluminium competes with mixed-material solutions and thermoplastics which are moulded around the electronics to fit the passenger space.”
There are, of course, considerations other than simply the weight of the ‘raw’ enclosure, such as thermal runaway protection and recyclability, to name but two.
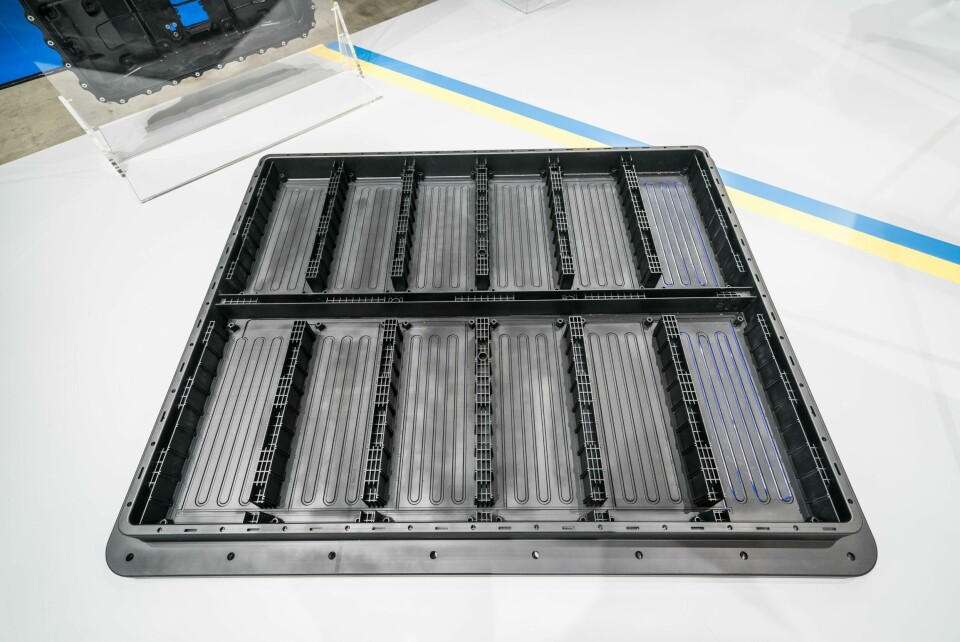
“We offer plastic solutions that reduce weight and cost, improve safety and have reduced environmental impact in terms of recyclability and a lower CO2 footprint than steel or aluminium,” says Dhanendra Nagwanshi, Global Automotive Leader EV Batteries & Electricals at SABIC, which has developed an award-winning thermoplastics solution for EV battery enclosures. “Producing parts in aluminium is a very energy-intensive process,” says Nagwanshi. “Our initial lifecycle analysis study shows that we can reduce 11% of CO2 emissions and 13% of the energy required to make this large part with thermoplastics instead of aluminium.”
SABIC supplies the thermoplastic battery enclosure for the Honda CR-V plug-in hybrid, for which it won an Edison Award. A large part measuring 1.6-metres by 1-metre and 2mm thick, the 6kg injection moulded polypropylene glass fibre resin solution delivered Honda a 10% weight saving and a 10% cost saving compared to a steel solution with a thermal blanket.
Living in a box
Clearly much more than a simple box, the battery enclosure is a large, structural safety part and its role and performance requirements create opportunities for creativity and innovative engineering.
For materials suppliers, success will depend on creativity and for ArcelorMittal, this comes in the form of its Multi Part Integration (MPI) initiative, which combines several parts stamped from one LWB (laser welded blank) into one single hot stamped part, in turn reducing the number of joining operations required.
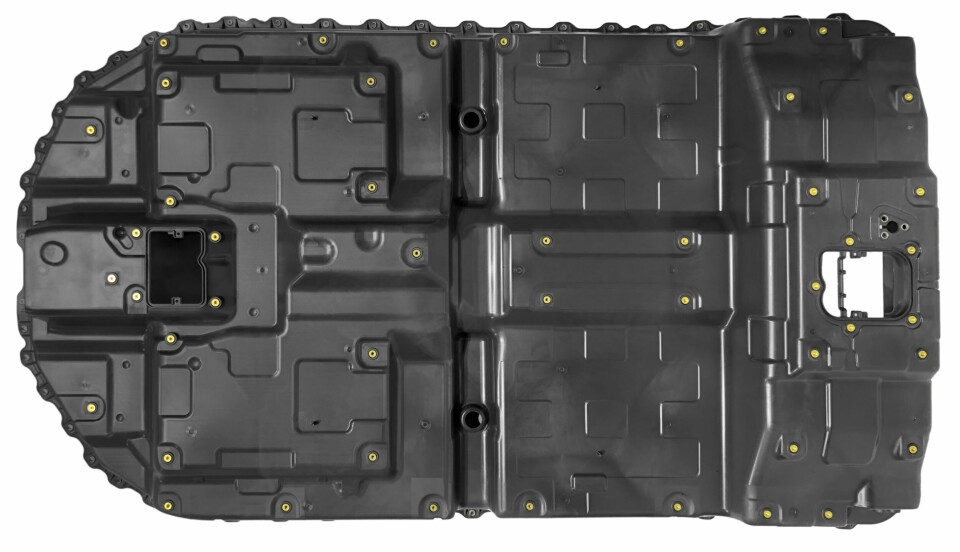
Paegle describes MPI as a range of Lego-like component solutions. “The battery is going to be integrated in the body-in-white (BIW) and automakers and Tier 1 chassis suppliers are starting to bring their chassis or BIW divisions together with their battery divisions in the same engineering centre for the design of future vehicles. This is a threat for the steel industry – and it is an opportunity. MPI enables us to address that opportunity.”
Thermal runaway protection
A major area of concern in EV batteries is thermal management and thermal runaway protection and it’s here where thermoplastic shines.
A new rigorous thermal runaway test developed by safety organisation UL Solutions, known as UL 2596 (“Test Method for Thermal and Mechanical Performance of Battery Enclosure Materials”), sees the material to be validated, subjected to a thermal runaway involving 25 cylindrical cells (18650) inside a steel box.
The properties of SABIC’s thermoplastic material are such that during this test, when a material sample is subjected to a 1100-degree Celsius flame for over five minutes, the pack-side temperature is less than 200 degrees Celsius, without the need for a thermal blanket as required by aluminium and steel enclosures. “In this test, aluminium fails at 1100 degrees Celsius in couple of seconds, but our plastic does not,” says Nagwanshi.
That’s because the thermoplastic material developed by SABIC begins to char when subjected to fire and over time becomes intumescent. “This means it doesn’t convey heat, a unique property of our thermoplastic material,” explains Nagwanshi. “After some time, it acts like a turtle shell, a protective layer against fire and heat transfer. Standard plastics don’t pass this test, but our plastic in millimetre-thickness underwent the test and passed every time.”
Furthermore, the moulding of thermoplastic enclosures enables creativity and increases the material’s versatility.
For example, cooling channels can be moulded directly into plastic enclosures. “With our thermoplastic products,” says Nagwanshi, “customers can have thermal runaway protection embedded into the battery tray, with integrated cooling channels in the plastic tray and an aluminium plate that goes on top to transfer heat from the battery module to the coolant. This is lighter than current all-metal solutions.”
By contrast, embedding cooling channels in a steel enclosure would require a multi-material solution. It can be done, notes Paegle; and Leftinger says aluminium also enables the integration of cooling systems. “Aluminium is very thermally conductive, so we’ve been working with several consortia recently to develop coatings that address situations involving thermal events,” she explains. “There’s plenty you can do in line as far as putting in attachments, bolts and fixings to help incorporate cooling solutions,” she continues, “and we’ve been researching structural cooling plates, which allow the integration of cooling into the system.”
EV battery Swap shop
One particular development in EV battery technology where the enclosure will play a key role is in battery swap, where the safe and efficient removal and storage of the battery will depend heavily on the performance on the battery enclosure. Until the demise of Better Place in 2013, battery swap appeared to have a guaranteed place in any EV ecosystem. But it’s on the rise, thanks to Chinese automakers Nio and Geely in particular.
“Battery swap requires extra precision in battery enclosure dimensions so the mounting points on battery enclosure can be positioned correctly during the swap process,” explains Abraham. “Lightweight is another consideration, as the battery packs need to be transported from station to station. Aluminium extrusion is, so far, the main solution for battery enclosures with swap capabilities.”
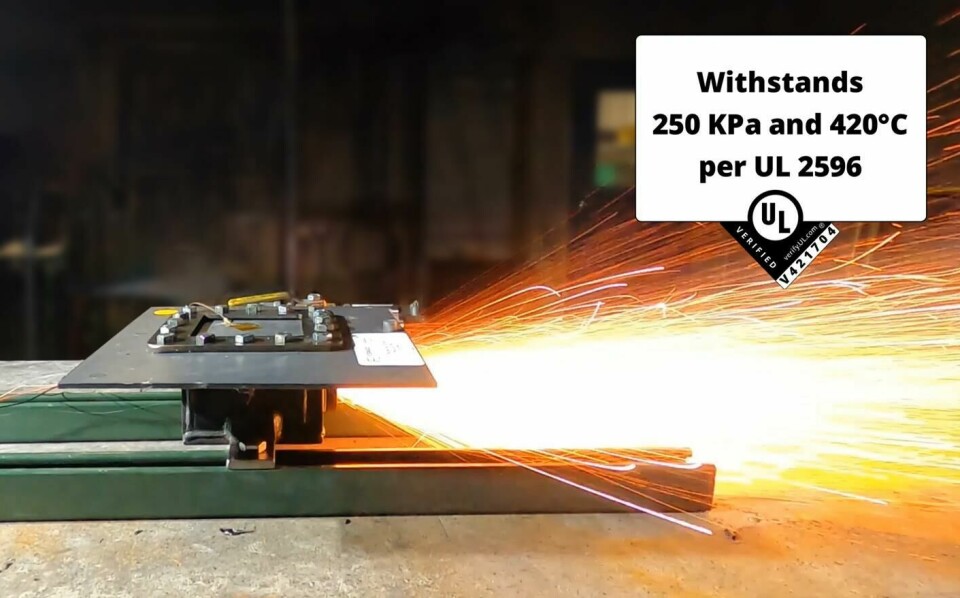
Uwe Frieß, who leads the Department for Body Construction, Assembly & Disassembly at German research organisation Fraunhofer Institute for Machine Tools and Forming Technology (IWU), believes that if plug-and-play battery replacement were to become established, the impact would be enormous. “Based on practical experience of how shared items are handled, we see the need for an additional impact protection casing and a necessary condition monitoring system to detect improper handling. Both systems represent additional components and costs.”
Another key development in battery technology that will affect the enclosure is the evolution of the role of the EV battery within the BIW. Originally a part supported by the BIW, battery enclosures are becoming a structural part of the BIW and automakers are even exploring cell-to-body and structural batteries and the design of the enclosure could be a critical factor.
For battery packs integrated into the BIW, Paegle says the steel industry is currently competitive in terms of cost and performance for battery top covers, lower shields and frames.
Aluminium, says Leftinger, is a very efficient solution for cell-to-pack, when compared to some other options, due to thermal conductivity and weight savings versus either plastics or extrusions.
And Nagwanshi emphasises the design freedom offered by thermoplastics, which in a cell-to-chassis design, “can deliver good value with respect to functional integration and the production of complex geometries with reduced number of components.”
Sustainable battery pack production and calls for development
However, developing battery packs as structural parts have significant impacts elsewhere, notably for sustainable production, component lifecycles and circularity. “From what we’re currently seeing, it’s going to make dismantling even worse,” says Frieß.
Leonard Ling, Global Automotive Knowledge Manager at Ducker Carlisle, notes that most automakers value repairability, making the battery enclosure generally accessible, removable and replaceable. But he also acknowledges the current lack of repairability. “Most dealerships will not repair a battery, but rather send it back to the OEM or other designated third party to handle.”
And when it comes to EV batteries, repairability is at least as important as—and much more efficient than—recyclability in the quest for sustainable mobility.
The rapid evolution of EV battery technology is good news for consumers. It also presents exciting opportunities as well as challenges for automakers and suppliers alike. “We need to act quickly,” says Paegle, “because we’re facing complete change in the automotive industry