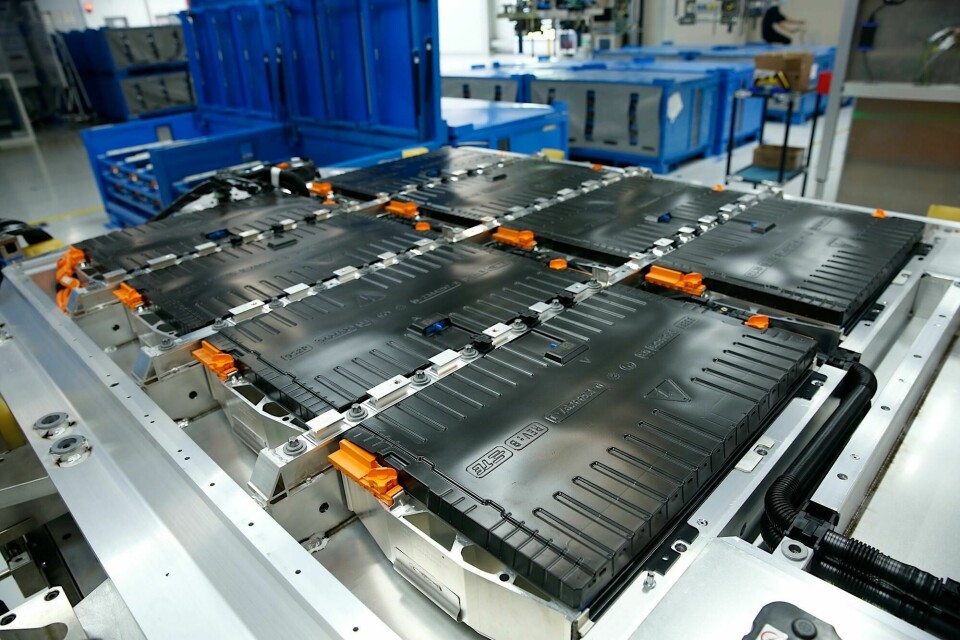
Focus on flexibility – optimising battery pack production
The AMS Evolution Livestream expert panel representing Ford, AMTE Power and Henkel, discussed the fast-changing production requirements as cell manufacturers and OEMs ramp up Gigafactories and battery pack assembly.
OEMs and battery cell producers are updating cell chemistries, designs and software at a faster rate than would be typical for traditional ICE powertrains. So, manufacturers need to adapt plants to new products, understand technology integration and become more agile and flexible in change management.
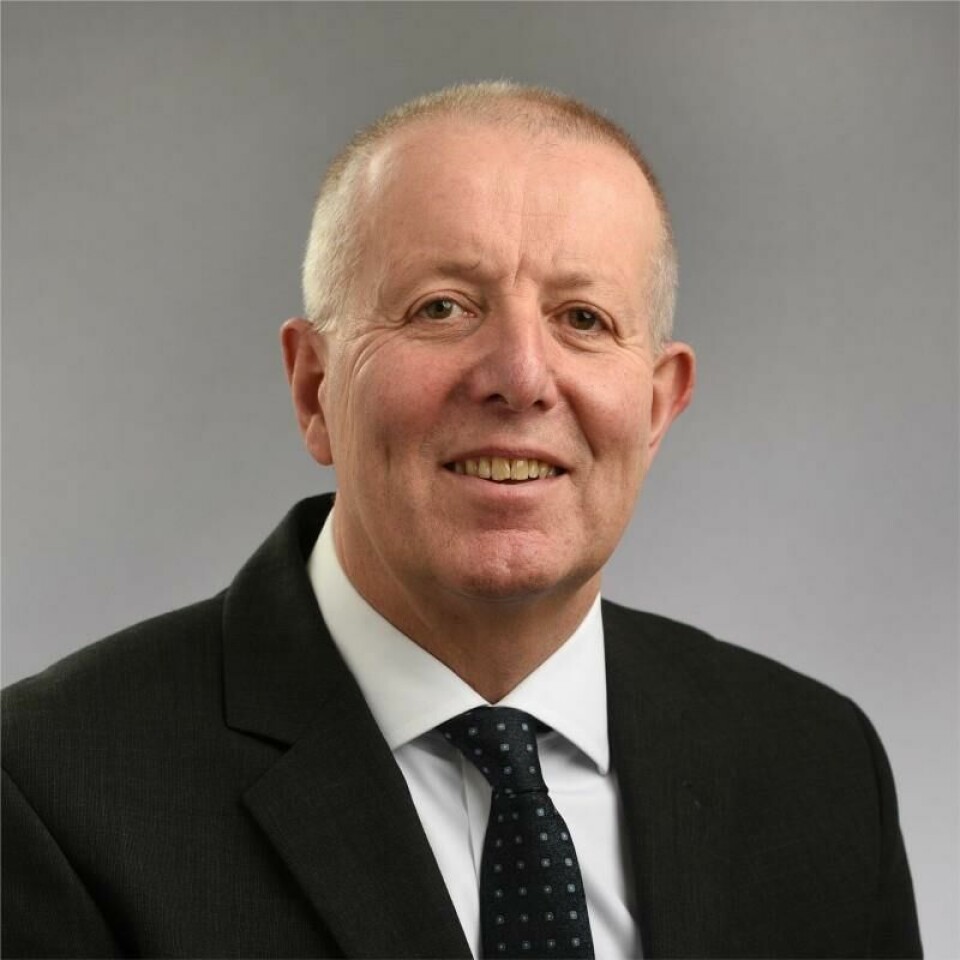
“Battery cell production is an energy intensive process. So, the use of renewable energy is fundamental to the sustainability of the process”
Getting started
A lot of the news around electric vehicle (EV) battery production has focussed on the current levels of regional sourcing, with most cells being produced in Asia, particularly China and Korea. And although there are numerous projects to build Gigafactories in Europe and the US, both under construction and in the pipeline, vehicle makers in the West are seen to be lagging behind in establishing the necessary localised supply chains for these essential components.
Offering some context for the challenges involved in establishing a new battery production operation was Alan Hollis, CEO at AMTE Power. The company is in the process of both expanding production at its existing site in Thurso, Scotland and establishing a new, much larger production operation at a proposed site in Dundee. Hollis noted that several key external resources are needed to support expansion of production operations: “There are many different considerations when setting up a Giga-factory and all are equally important. Location and proximity to your customers is always a consideration but especially with battery cells as they are heavy and require specialist handling during transportation, and we are planning to produce around 8 to 10m cells per year, so the volumes are high.
“Investment incentives are also important. Gigafactories are expensive to set up, and our planned facility is not large compared to some projects, we are looking at 1GWH output per year, but will cost in the region of £250m to set up. If you look at the Inflation Reduction Act in the US and a similar incentive package being developed by the EU, these are very important to support future development of battery production.”
As well as bureaucratic requirements around planning and permitting, Hollis highlighted the need for access to affordable renewable energy. “Battery cell production is an energy intensive process. Typically, every KWH of battery power produced, requires 25KW of energy in the process. So, the use of renewable energy is fundamental to the sustainability of the process.” Logistics and the availability of a skilled workforce were also noted as key requirements.
Ramping-up volumes
Delving more deeply into the manufacturing processes the panel examined the steps needed in the assembly of the battery pack and how to affect the volume ramp-up to meet growing demand. The automotive industry’s shift to producing electric vehicles and components has been uncharacteristically rapid with pressure on shortening development cycles and time to market for new products. Offering a supplier’s perspective, Henkel’s Global Senior Manager for Thermal Technologies, Holger Schuh commented on some of the key parts of the integration and thermal management of the cells in the pack assembly. “Coming from a chemical company perspective, this is quite a challenging aspect in that the pack designs are quite fragmented, and we see the need for different types of materials mostly in thermal conductive gap fillers. And the increased demand for these materials has required us to ramp-up production from initially just two plants producing these materials, to 10 plants, to supply our customers globally.
“And, as Alan said, this also ensures the supply of materials is closer to our customers, reducing the shipping requirements. We are delivering much higher volumes of these materials. In the past an electronic control unit might require 1 to 5ccs of material per unit, now each EV battery requires up to 2-litres of gap filler.”
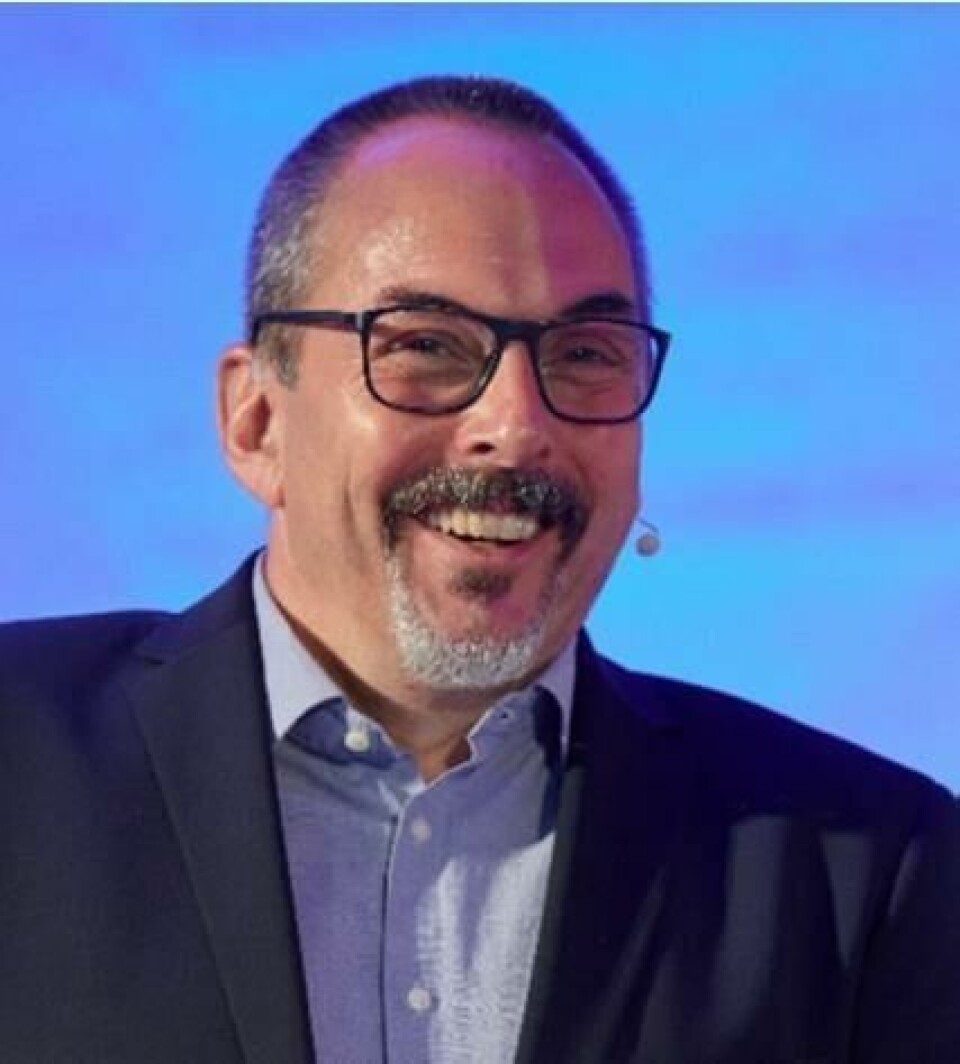
“We need to deliver high volumes of materials, be flexible in the chemistries we produce and fast in the development of these materials because the design of component changes much faster now”
Schuh also noted the need for flexibility in production, a consideration that has become a key element of modern automotive production. “Beyond our current gap fillers and thermal conductive materials, we also need to work with different chemistries. Some OEMs prefer polyurethane based products others favour epoxy-based materials. There are also restrictions on European based OEM on using silicone-based materials.
“So, we need to deliver high volumes of materials, be flexible in the chemistries we produce and fast in the development of these materials because the design of component changes much faster now. In the past a gap filler for a control unit might have a five or even 10-year production life cycle, and that could be used across multiple components. Now in an EV battery that life cycle is perhaps two years and then you are developing the next generation of materials to meet the requirement of new batteries.
“We don’t have a standardised portfolio for these applications, and this has an impact on our production in terms of processes and equipment choices. We have developed smart and sustainable manufacturing operations and looked at how we manage our supply chains to meet the higher volumes.”
Battery pack assembly
These challenges are much the same for the carmakers as they look to balance ongoing ICE production with the integration of EV products. Aygen Ahsen Yildirim, 1T Battery Pack Manufacturing Engineering Chapter Leader at Ford Otosan explained that, in addition to an existing 3P battery pack production line producing the packs for the e-Transit, the OEM is installing a new battery pack assembly line at the Koceali facility in Turkey, which will have a capacity of 120,000 units per year. Yildirim noted that this will produce BEV and PHEV batteries with different levels of complexity.
Yildirim also offered some insight into the company’s approach to integrating these new lines for electric vehicle components: “A key starting point with any new line is what the capacity will be, and then the number of working days, hours, shifts to produce this capacity and from this you get the required cycle time. This informs discissions around the number of workstations, automation levels and equipment such as robots, automated guided vehicles (AGVs) etc.
“Another important consideration is the flow of materials, both to the line for assembly and the handling of the battery packs to the vehicle assembly line. This influences the footprint of the line. There are also safety considerations with battery pack assembly, such as having suitable fire protection in place in case of thermal runaway.”
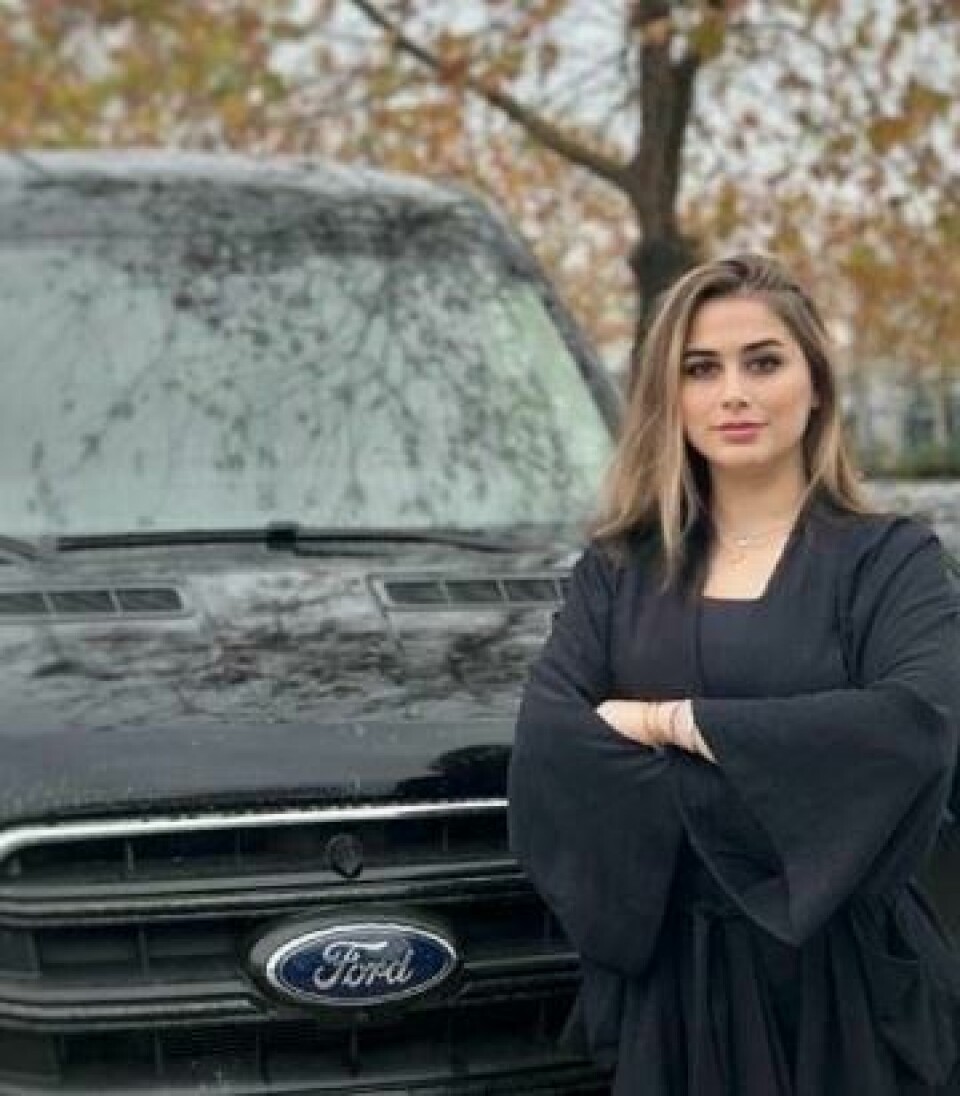
“A key starting point with any new line is what the capacity will be, and then the number of working days, hours, shifts to produce this capacity and from this you get the required cycle time”
Experience is important to the speed of integration of any new line and the facility’s existing battery assembly line offers the Ford team a lot of data at the start of the process, from which improvements and adaptations can be made. However, Yildirim noted that in this instance the project time to completion was longer than usual, more than a year, due to the impact of the semi-conductor shortage on the equipment suppliers for the line.
The cycle times for battery assembly are fast and this impacts on equipment choices and processes. Schuh noted that material dispensing cycles times for EV batteries were more demanding: “The gap filler for electronics we have been supplying for 20 years had a throughput of 1 to 5ccs per second, this is the material flow rate, but the OEM’s requirements for dispensing a similar material for the battery packs is now 80ccs per second.
“To meet this requirement we started from scratch in developing fillers and resins that had this flow rate and worked with our equipment partners on the dispensing process. This had been a challenge in the beginning, but we engaged with our OEM customers early in the development cycle. We see the cycle times getting shorter due to commercial requirements, even in cell-to-chassis applications where more filler might be required, but we have been developing the material flow rates and can now achieve 100ccs per second.”
Yildirim also saw cycles times falling as volumes increase: “We definitely see cycles times getting shorter to meet demand, and this will require more automation of the battery pack processes.”
Sustainable production
The process challenges include meeting sustainability targets. Discussing ways of doing this in production Hollis observed that improving productivity was an important factor: “You can reduce your carbon footprint with the assets and processes you already have by improving productivity and eliminating waste at all stages of the operation.”
Hollis explained that the development of AMTE’s Giga-factory also offers the opportunity to upgrade equipment and optimise processes to reduce the carbon footprint and to improve the flexibility of the manufacturing operations.
An important part of managing sustainability in the production/assembly process is to consider the entire life cycle of the product according to Schuh. “We look at how we develop the product, produce it and how is it used in the battery pack. Also considering the repair and recycling requirements. For our thermal products the development uses digital tools to advance the material formulation which reduces the physical process steps and saving energy in the mixing stages.”
The value of digital tools was supported by Hollis who pointed to the savings in energy, time and materials when developing cell formats and chemistries: “We can have multiple iterations of a cell design before we go to any physical prototype.” He noted this reduced the time to market and costs involved in development.
Continuing change
In the automotive sector there still a lot of ongoing development around battery chemistries, format and integration into the vehicle. The panel were asked if they saw this continuing in the mid-to long-term.
Hollis observed that the EV battery industry is still maturing: “In terms of electrifying the entire road transportation system we are certainly not at the end of the process, as such the cell and battery pack technology will continue to develop and evolve, and this will be driven by the economics of the process, critical materials availability, and other alternative technologies such as fuel cells will also play a part in this.
The continuing development in battery chemistries and pack integration would not slow down in the mid-to long term according to Schuh. “The EV market is being driven by innovations from the OEMs and also the battery suppliers, and the expansion of the electric vehicle market into more regions, India for example, will also influence the direction of cell/battery development.”
Yildirim agreed that battery pack and cell development would continue at pace but noted that tightening vehicle safety regulations would also influence this: “The developing electric vehicle safety regulations will influence the architecture design, which will in turn affect the battery integration and the pack designs. This will see the need for new components and in assembly change the materials handling requirements. So, the production processes and lines need to flexible to meet these changes.”
You can watch the full livestream on-demand here