TRADE POLICY SHIFTS
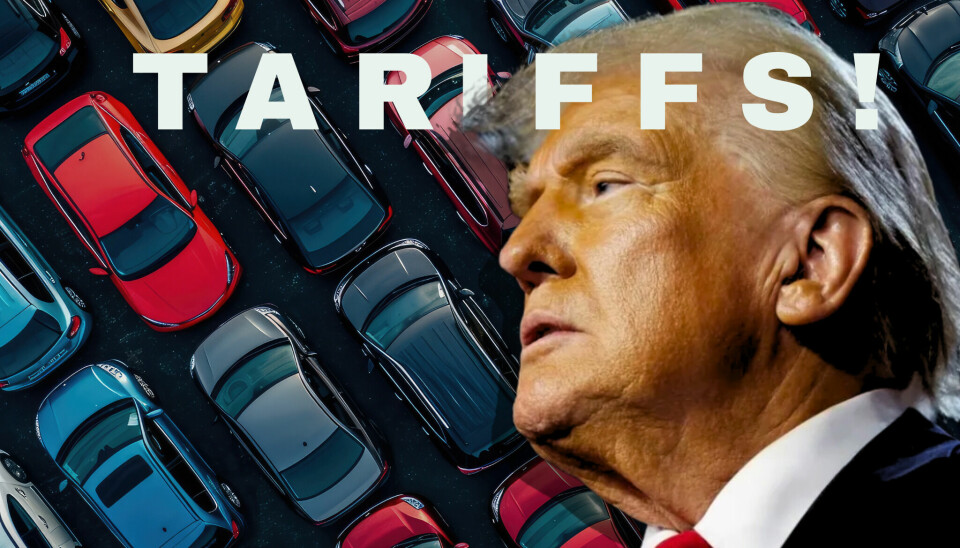
Washington’s tariff gambit upends vehicle production map
Fresh US tariffs are upending EV strategies, accelerating reshoring, stalling imports and forcing automakers to overhaul production footprints and future investment plans.
On July 10, 2025, President Donald Trump threatened to ratchet up the US’ already formidable tariff regime, signalling a rise in baseline reciprocal duties to 15–20% and hinting at a “fentanyl tariff” of 35% by August. No executive order has yet followed, but the message was clear: trade protectionism is not a negotiating tactic, but now, a governing doctrine. Automakers were already reeling from months of policy shocks. Now they face the prospect of yet another blow to their cost base and investment strategies.
The European Union may be gearing up to reply with its own salvo in response, in the form of “Anti-Coercion Instrument” (created in 2023) with a potential 30% reciprocal tariffs on American goods which could take effect on August 1 after a consultation that began in May. Canada had acted earlier, applying 25% duties on non-USMCA-compliant vehicles in April. Retaliation is becoming as structured as the original tariffs themselves, creating a patchwork of barriers that disrupts the very foundations of automotive integration.
July: A New Round of Deals
Just as the industry braced for further escalation in July, a series of new trade deals emerged. On July 23, the US announced a "massive" agreement with Japan. This deal sets a 15% tariff on Japanese goods, including vehicles and automotive parts. While a welcome reduction from the 25% President Trump had explicitly threatened just weeks earlier, it remains notably higher than the previous 2.5% base duty and the 10% interim rate applied during negotiations. Crucially, unlike the British deal, this Japanese agreement appears to include no quota on vehicle imports, a significant distinction for a major automotive exporter.
Japan, in turn, has pledged a formidable $550 billion in investments into the US, though specific details and timelines remain elusive. For Japanese automakers, this creates a new calculus: a better deal for cars imported directly from Japan than for those produced in their significant facilities in Mexico or Canada, which are still subject to the full 25% tariffs. In tandem, the US also announced trade agreements with the Philippines and Indonesia, with US imports from the Philippines to be taxed at 19% and Indonesia at 19% (down from a threatened 32%).
June: Tariff pressure meets regulatory retreat
The threat of escalation came weeks after Trump vowed on June 12 to “go higher than 25%” if that is what it takes to “bring back American car production.” That same month, the administration scrapped California’s Advanced Clean Cars II regulation, which aimed to ban new petrol-powered vehicles by 2035, along with similar rules in a dozen states.
For carmakers, this marked a pivot as dramatic as the tariffs themselves. One-third of the US market is now open to combustion engines for decades longer than planned. It is a gift to manufacturers struggling to meet zero-emission mandates. Yet the broader environment of volatility makes long-term planning no easier.
May: Trade deals and strategic pivots
A partial reprieve came on May 8, when Washington struck a deal with London to soften the tariff shock for British-made cars. Imports from Britain, previously facing a combined 27.5% duty (2.5% base plus 25% additional), were cut to 10% up to an annual quota of 100,000 vehicles. Components named in the pact enjoy the same rate. For a handful of premium brands, this is a lifeline. For mass-market models, it is barely a sticking plaster.
China’s EV champions were not so lucky. They remain excluded by a 100% tariff that effectively doubles sticker prices. For BYD and its peers, the dream of cracking the American market is dead for now. Instead, they are chasing growth in Latin America and Africa, where tariff barriers are lower and consumer appetite is rising.
Meanwhile, the industry’s production map is redrawn in real time. Honda is shifting Civic Hybrid assembly from Japan to America and planning to relocate CR-V production from Canada. Hyundai has started moving Tucson crossover production north of the Rio Grande.
Polestar, once reliant on China for its Polestar 2, halted orders from those factories and is banking on South Korea as a stopgap before expanding in America. Subaru will start building the Forester in Indiana later this year rather than importing from Asia.
April: The shockwave begins
The first tremor came on April 3, when the 25% tariff on imported vehicles took effect, a week after Trump signed his March 26 proclamation restoring Section 232 duties under the Trade Expansion Act.
Parts followed on May 3, ensnaring engines, transmissions and electrical components. Automakers had days, not months, to react. By April 29, the White House unveiled a sop to manufacturers: an “Import Adjustment Offset,” granting credits of 3.75% of MSRP on US-assembled vehicles until April 2026, falling to 2.5% the following year. But this incentive is contingent on 85% domestic content, a high bar for an industry that has built its fortunes on cross-border integration.
Disruption on the factory floor
The effect on production was immediate and brutal. Just-in-time manufacturing, the system that keeps inventories lean and costs low, buckled under the strain of new customs checks and tariff paperwork. Components that once breezed across the Rio Grande or the St Lawrence now crawled through a thicket of compliance. Within a week, S&P Global estimated that a third of North American vehicle output faced disruption, with daily losses of 20,000 units. Some assembly lines fell silent for lack of wiring harnesses or drivetrain modules.
Costs soared. Analysts calculate the 25% duty adds at least $2,000 to the average car, and as much as $10,000 for premium imports. Even US-built models, whose supply chains are global, absorbed roughly $3,000 in extra costs. Stellantis offered a grim case study: a €300m ($350m) tariff hit helped drive a €2.3bn ($2.7bn) net loss in the first half of 2025, while North American shipments of imported models plunged by 25%.
General Motors also reported a significant impact, revealing a $1.1bn hit from tariffs in its second-quarter profits, contributing to a 35% overall drop. Despite beating analyst estimates, GM cautioned that the second half of 2025 would see lower profits due to the ongoing tariff impact, which it estimates could reach $4-5 billion for the full year. The automaker aims to mitigate at least 30% of this through manufacturing adjustments and cost initiatives, and has already pledged $4bn to expand US plant production, shifting some Chevrolet Equinox and Blazer assembly from Mexico.
From just-in-time to just-in-case
Years of efficiency gains are being sacrificed on the altar of resilience. Carmakers are stockpiling parts and bulking up inventories - an expensive reversal of decades of lean practice. “Just-in-case” is the new mantra. It brings security but also higher capital costs and more waste.
For suppliers, the pain is sharper. Operating on thin margins, they face rising input prices and delayed payments from OEMs squeezed by tariff shocks. Bankruptcies in the supply base would ripple through the industry, adding another layer of fragility.
Table 1: Key US Automotive Tariff Updates (March-July 2025)
Proclamation/Agreement Name | Date of Announcement/Effectiveness | Tariff Rate (New/Total) | Affected Products/Categories | Key Provisions/Exemptions | Primary Rationale/Context | Countries/Regions Targeted/Benefiting |
Section 232 Proclamation | March 26, 2025 (Announced) April 3, 2025 (Vehicles Effective) May 3, 2025 (Parts Effective) | 25% (Additional) | Imported Passenger Vehicles, Light Trucks, Key Auto Parts (engines, transmissions, powertrain, electrical components) | Applies to non-US content for USMCA-compliant vehicles/parts (mechanism by May 3) | National Security (strengthening domestic industrial base) | Global, with USMCA content exemption for Canada/Mexico |
Import Adjustment Offset | April 29, 2025 (Announced) Retroactive to April 3, 2025 | 3.75% of MSRP (Year 1) 2.5% of MSRP (Year 2) | Parts used in US-assembled vehicles | Offset for US-assembled vehicles (85% domestic content goal for Year 1 tariff-free) | Temporary relief for US manufacturers from parts tariffs | US-assembled vehicle manufacturers |
US-UK Bilateral Agreement | May 8, 2025 (Announced) June 16, 2025 (Effective) | 10% (Total) | British-made Vehicles (up to 100k quota), British Auto Parts | Quota of 100,000 vehicles/year at reduced rate | Bilateral trade agreement, addressing Section 232 concerns | United Kingdom (benefiting) |
Chinese EV Tariffs | Ongoing (pre-existing) | 100% (Total) | Chinese-made Electric Vehicles (EVs) | Effectively locks out Chinese EVs from US market | Trade policy to limit Chinese EV presence | China (targeted) |
US Escalation Threats | June 12, 2025 (Signalled) July 10, 2025 (Threatened) | >25% (Automotive) 15-20% (Baseline Reciprocal) 35% ("Fentanyl" Tariff) | Automotive, All Products | No legal documentation yet for July 10 threats | Accelerate domestic manufacturing, broader trade policy | Global |
Canadian Retaliatory Tariffs | April 9, 2025 (Vehicles Effective) March 13, 2025 (Goods Effective) June 27, 2025 (Trade Talks Terminated) | 25% (Ad Valorem) | Non-USMCA compliant vehicles/content, CAD $29.8B US-origin goods | Response to US tariffs, digital services tax dispute | Reciprocal action, trade dispute over digital services tax | United States (targeted) |
EU Reciprocal Tariffs | July 7, 2025 (Effective) Delayed to Aug 1, 2025 | 30% (Reciprocal) | All products (with exceptions) | Public consultation on countermeasures (May 8, 2025) | Reciprocal action, response to US tariffs | United States (targeted) |
Indian Retaliatory Tariffs | May 3, 2025 (US Tariffs Effective) | 25% (US Tariff) | Passenger vehicles, light trucks, auto components from India | India disputes legal basis at WTO | US tariff on Indian autos, India's response | India (targeted by US, threatening retaliation) |
Investment flows reverse - slowly
The tariffs are meant to force factories home. They are succeeding, up to a point. GM has pledged $4bn across three American plants and plans to lift annual assembly capacity to 2m units by 2027. Hyundai’s $21bn investment package includes a new US steel plant. Mercedes-Benz will add GLC SUV output in Alabama. Yet full reshoring is rare. More often, manufacturers are hedging with regionalisation: keeping production inside tariff-free zones such as the USMCA bloc, or shifting to politically stable low-cost hubs in Southeast Asia and India. For global brands, diversification trumps dogma.
Read Digitalisation stories
-
Volkswagen accelerates AI-powered production with 5-year AWS extension
-
Automotive industry faces workforce upheaval in 2025, reshapes jobs amid shifting tech
-
Modular manufacturing moves automotive production into the future
-
Boosting automotive production efficiency with AI-powered predictive maintenance
EV ambitions collide with policy reality
Electric vehicles face unique pressures. Tariffs add roughly $10,000 to a $40,000 imported EV, even before the threatened removal of the $7,500 federal tax credit. That double blow could choke demand for mid-priced EVs - the very segment needed for mass adoption. Tesla, with its Fremont and Austin plants, enjoys a “home-court” edge, as do Rivian and Lucid.
Volkswagen and Toyota are less fortunate; their ID.4 and bZ4X rely on imported parts. Chinese firms, already shut out by a 100% tariff, are pivoting elsewhere. Meanwhile, US EV makers still depend on foreign battery cells and critical minerals. Building that capacity at home will take years.
Trade policy risk, once a peripheral concern, now sits at the heart of manufacturing strategy.
Table 2: Illustrative OEM Responses to Tariffs (Production & Pricing Adjustments)
OEM Name | Key Strategic Actions (Production/Pricing) | Affected Models/Regions | Date of Action/Announcement |
Audi | Halted all imports to the US; holding incoming inventory at port. | All imports to US | April 2025 |
Chevrolet | Relocating Equinox and Blazer SUV production from Mexico to the US. | Equinox, Blazer SUV | Ongoing |
Ferrari | Raising prices by 10% for vehicles imported after April 2nd. | Most models (296, SF90, Roma exempted) | April 2025 |
Honda | Shifting Civic Hybrid production from Japan to the US; plans to relocate CR-V SUV production from Ontario, Canada, to the US. | Civic Hybrid, CR-V SUV | Ongoing |
Hyundai | Relocated some Tucson crossover production from Mexico to the US; will not raise MSRP of Hyundai and Genesis vehicles until June 2, 2025. | Tucson crossover, Hyundai & Genesis vehicles | Ongoing, May 2025 |
Mercedes-Benz | Plans to begin production of GLC SUV at its Tuscaloosa, Alabama facility. | GLC SUV | Ongoing |
Polestar | Moved some manufacturing footprint to US; stopped accepting orders for China-produced Polestar 2; producing Polestar 4 in South Korea to avoid tariffs on China-produced vehciles in US. | Polestar 2, Polestar 3, Polestar 4 | Ongoing |
Stellantis (various brands) | Offering employee pricing to offset tariff pressure; temporarily pausing production of some models in Canada/Mexico. Reported €300M ($350m) tariff hit and 25% drop in Q2 North American shipments. | Pacifica, Voyager, Charger EV, Jeep Compass, Wagoneer S; North American imported models | June 2025, H1 2025 |
Subaru | Lafayette, Indiana facility will begin assembling the Forester later this year to avoid importing from Japan and Mexico. | Forester | Ongoing |
Digitalisation as a defensive weapon
As tariff costs bite, automation and software become defensive tools. Robotics, 3D printing and modular product design promise to cut labour costs and sidestep supply shocks. Digital twins, Human-Machine Interfaces, and AI-driven analytics are migrating from pilot projects to production floors, helping managers reroute components and model tariff scenarios in real time. Software-defined vehicles offer another hedge, reducing the need for bespoke hardware that can be tariffed. The smart factory is no longer a buzzword; but an insurance policy.
The new normal: geopolitics on the line
The broader picture is bleak for global integration. Trade policy risk, once a peripheral concern, now sits at the heart of manufacturing strategy. Tariffs are wielded not just to protect industry but to punish digital taxes, sway labour rules and project foreign policy. For carmakers, that means living in a world where political volatility is as disruptive as a chip shortage. The response - localisation, automation and digitalisation - is costly, but the alternative is worse: paralysis in a balkanised market.
The tariff war of 2025 is more than a skirmish. It is a structural shift that will shape where cars are built, how factories operate and which firms survive. For an industry that mastered efficiency, the challenge now is a higher level of resilience. And resilience does not come cheap.