Digital Transformation
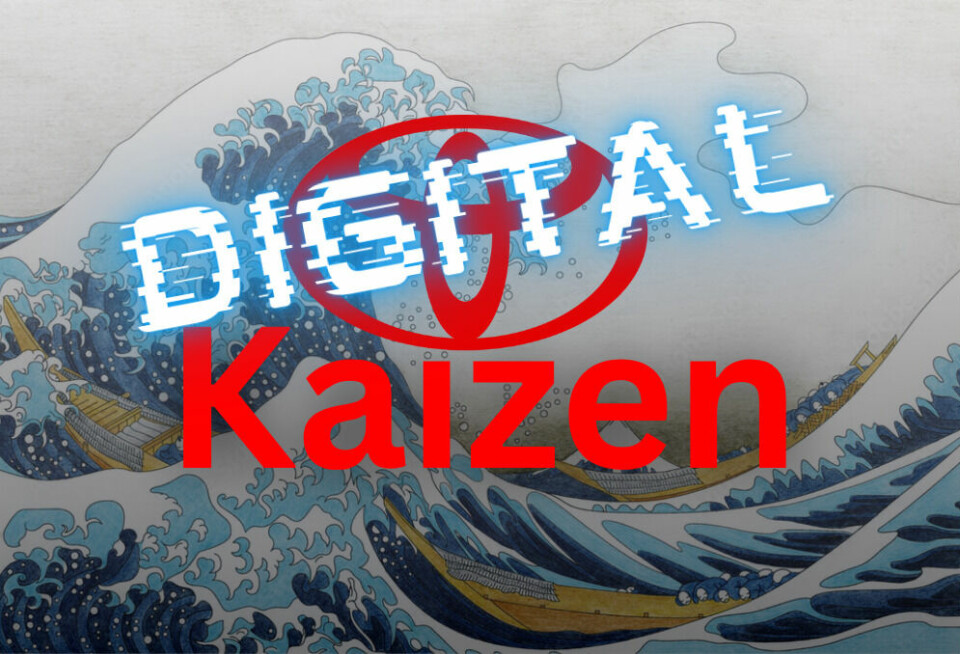
Inside Toyota’s 2025 Lean(er) Manufacturing System
Toyota’s lean production system enters a new phase in 2025. Combining its founding pillars of Jidoka and Just-in-Time with digital tools and tighter regional roles, the updated model aims to sharpen EV readiness and operational agility.
Toyota’s venerated production system, long the global gold standard for manufacturing efficiency, is embarking on its most significant transformation since its inception. This year, the Toyota Production System (TPS) will fuse its foundational principles of Jidoka (automation with a human touch) and Just-in-Time production (JIT), with a new level of advanced digital tools and a newly empowered regional structure. This evolution aims to sharpen the company's electric vehicle (EV) readiness and enhance operational agility amidst a turbulent global landscape.
The core tenets of TPS - eliminating waste (muda, mura, muri) and fostering continuous improvement (Kaizen) - remain sacrosanct. However, Toyota acknowledges that even a highly adaptable system must evolve. This holistic recalibration, initiated in 2025, reinterprets TPS for an era defined by rapid electrification, digital disruption, and geopolitical complexity.
Rather than abandoning its principles, Toyota is elevating them, embracing digital tools as catalysts for an intrinsic operational metabolism that enables self-optimisation and responsiveness.
Strategic decentralisation: why is Toyota empowering regional hubs?
A cornerstone of this adaptation is strategic decentralisation. In May 2025, Toyota Motor North America (TMNA) spearheaded a fundamental restructuring, creating three pillars - Manufacturing Business Operations, Manufacturing Operations, and Production Engineering - that coordinate across seven distinct regional groupings.
This reorganisation, effective May 19, 2025, delegates substantial authority to regional leaders, reducing hierarchical layers and allowing for localised decision-making based on specific market complexities.
This shift empowers regional vice-presidents, such as Kerry Creech (Georgetown, Kentucky), Jason Puckett (Indiana), and Frank Voss (Texas), to manage staffing, supplier coordination, and digital tool deployment. Stephen Brennan, Senior Vice-President of Manufacturing Business Operations, now oversees manufacturing strategy and EV supply coordination, while Susann Kazunas, Group Vice-President of Production Engineering, ensures consistent digital platform deployment for new product launches.
This institutionalises a more agile, localised Kaizen, fostering iterative improvements tailored to regional conditions and enhancing supply chain resilience against volatility and geopolitical risks.
TMNA 2025 Manufacturing Reorganisation
Pillar / Region | Key Responsibilities / Focus | Key Leader |
Manufacturing Business Operations | Manufacturing strategy, EV supply, project management, advanced planning, digital technology, production efficiency, safety, environmental, facilities operations | Stephen Brennan, SVP |
Manufacturing Operations | Oversees overall plant operations across regions | Kevin Voelkel, SVP |
Production Engineering | Leads new product launches, ensures standardised digital platforms across regions, compresses timelines for start-of-production | Susann Kazunas, GVP & Executive Engineering Officer |
Region 1 | Georgetown, Kentucky plant operations | Kerry Creech, GVP & President |
Region 2 | Indiana plant operations | Jason Puckett, GVP & President |
Region 3 | Toyota Motor Manufacturing Canada operations | Tim Hollander, GVP & President |
Region 4 | Toyota Motor Manufacturing Texas operations (truck & hybrid assembly) | Frank Voss, GVP & President |
Region 5 | Toyota Motor Manufacturing West Virginia, Alabama, Mississippi operations (includes TBMNC) | David Rosier, GVP & President |
Region 6 | Mazda Toyota Manufacturing (JV) operations | David Fernandes, GVP & SVP |
Region 7 | Toyota Battery Manufacturing North Carolina (TBMNC) operations | Don Stewart, GVP & President |
Digital reinforcement: the metabolism of modern lean manufacturing
Toyota’s digital strategy positions technology as an enabler for lean thinking - a pragmatic approach to "Lean 4.0"; a methodology that merges the principles of Lean manufacturing with Industry 4.0 technologies to optimise processes and boost efficiency.
Real-time analytics are now deeply embedded at the plant level, leveraging vast data to inform decision-making and accelerate Kaizen. Digital twins, such as those used by Toyota Europe via NavVis 360 mapping, simulate production flows, pre-empt bottlenecks, and optimise layouts, even reducing the company's carbon footprint by minimising travel for planning.
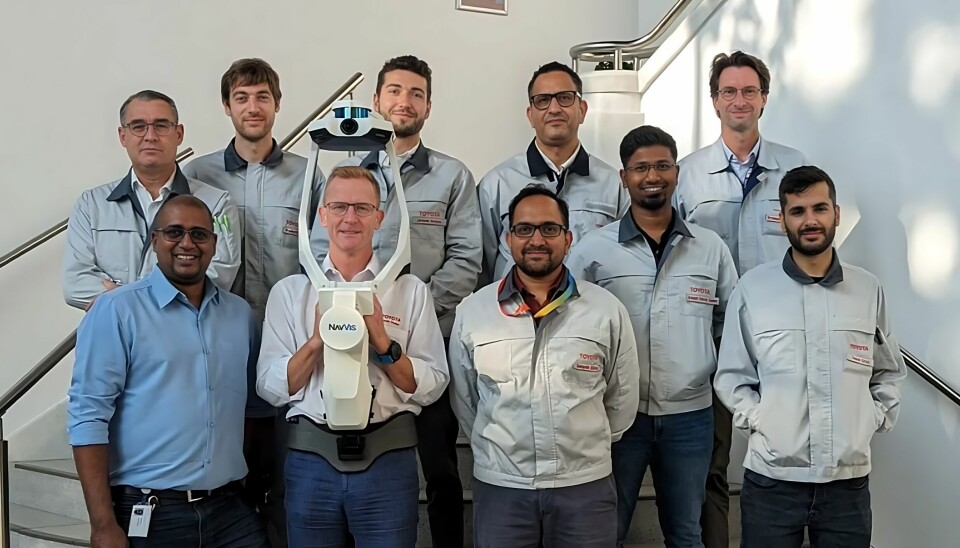
Toyota Senior Manager, Production Engineering, Kevin Anderson said, “embedded in the Production Engineering culture is the will to challenge and improve our processes. The introduction of Digital Twin technology enabled us to accelerate our shared understanding of each production site and the dynamics we need to consider from early design right through to final vehicle production.
“Instant access to the virtual environment has enhanced our ability to share data, brainstorm towards new innovations, predict technical challenges and so much more.”
Augmenting manual visual inspection, AI-driven image recognition, expanded through deep learning, automates vehicle quality checks. These systems, deployed at Toyota's headquarters plant since December 2020 for transmission gears, detect microscopic defects often imperceptible to the human eye, easing human burden and significantly improving inspection performance.
Predictive maintenance, powered by IoT sensors and machine learning, anticipates equipment malfunctions, sharply reducing unplanned downtime and maintenance costs. Toyota's in-house AI Platform is projected to save 10,000 hours of manual work annually, accelerating the Plan-Do-Check-Act (PDCA) cycle central to Kaizen. This digital integration exemplifies Jidoka for Industry 4.0, freeing human ingenuity for higher-value problem-solving.
Digital Technologies Enhancing Toyota's Lean Manufacturing (2025)
Technology | Specific Application in Toyota | Quantifiable/Qualitative Benefits |
Real-time Analytics & Dashboards | Integrated into plant systems, sifting vast data on production processes; used for KPIs like machine utilisation, downtime. | Faster decision-making, proactive maintenance, fuels continuous Kaizen, 97% operational efficiency rates observed in companies using similar systems. |
Digital Twins | Virtual replicas of European manufacturing plants (EMCs) using 360 mapping for planning changes, simulating production flow, pre-empting bottlenecks. | Optimise production workflows, reduce costs (e.g., CO2 footprint by reducing travel), identify safety/ergonomic improvements, mitigate risks via 'What-if' scenarios. |
AI-driven Visual Inspection | Supplementing manual checks for quality control (e.g., paint scratches, orange peel texture, transmission gears, general vehicle checks). | Automates vehicle checks, significant reductions in inspection times, eases human burden, detects microscopic defects, 16% increase in defect detection, 73% reduction in inspection time per vehicle. |
Predictive Maintenance (AI/IoT) | Sensors monitor equipment (vibration, temp, speed); ML algorithms anticipate malfunctions. | Decreases downtime, cuts maintenance expenses, 47% reduction in unplanned downtime, 32% decrease in maintenance costs, improved safety, enhanced product quality. |
Cloud-based Forecasting Tools | Replaced 75 spreadsheets with consolidated, cloud-based tools for 52-week forecasts. | Greater accuracy and efficiency, unprecedented visibility for suppliers, potential 10-40% cost reduction for companies with advanced supply chain visibility. |
In-house AI Platform | Empowers factory workers to develop and deploy ML models for tasks like inspecting finished parts, adhesive application, injection moulding abnormalities. | Automates mundane tasks, frees humans for higher-value activities, projected to save 10,000 hours annually, 20% reduction in learning model creation time. |
Electrification readiness: scaling for increasing EV demand
Accelerating its EV push, Toyota aims to offer an electrified version of every model by 2025. By mid-2027, seven new US-made EV models are planned for American showrooms, including two from Georgetown, Kentucky, and Princeton, Indiana. Production targets for EVs are set at 600,000 units in 2025 - a threefold increase from 2024’s 190,000.
Despite modest pure EV sales in the US in 2024, Toyota's overall electrified vehicle sales (HEVs and PHEVs) surged by 53%, surpassing one million units and comprising over 43% of total sales. The company aims for electrified vehicles to represent 50% of its US sales by 2025, pursuing a pragmatic multi-pathway strategy that leverages its hybrid strengths.
Snapshot: Toyota’s Electrification Breakdown
Powertrain Type | Status |
HEV (Hybrid) | Standard or available on nearly every new Toyota |
PHEV | Expanding - e.g. RAV4 PHEV, Prius PHEV |
BEV | Introduced mid-decade, with growing model offerings |
Fuel Cell / Hydrogen | Niche, mostly experimental or luxury (e.g., Mirai) |
Toyota Battery Manufacturing North Carolina: a blueprint for electrification
A linchpin of this strategy is the Toyota Battery Manufacturing North Carolina (TBMNC) plant. With a $13.9bn investment and plans to employ 5,100, the facility will commence production in 2025 with 14 lines (four for HEVs, ten for BEVs/PHEVs). At full capacity, it will support 30 gigawatt-hours annually, enabling 300,000 BEVs, 150,000 PHEVs, and 800,000 HEVs.
This substantial investment signifies a strategic move towards vertical integration for critical EV components, reducing reliance on external suppliers and mitigating future tariff impacts. Toyota's commitment to carbon neutrality by 2035 also embraces a "multi-pathway approach," including hydrogen fuel cell technology.
Achieving operational resilience in the face of global uncertain
Toyota's emphasis on regional autonomy is a direct response to evolving geopolitical realities, including localisation mandates and varying regional costs. The TBMNC plant epitomises this localised strategy, with meticulously configured battery cell supply chains and advanced planning tools optimising inbound logistics based on local conditions. Initial battery shipments from TBMNC to US assembly plants like Mazda Toyota Manufacturing and Toyota Kentucky further solidify this commitment.
Read more Smart Factory stories
-
Key insights from Daimler Truck’s Twin4Trucks project
-
Benteler starts work on advanced manufacturing plant in Morocco, boosting job creation and integrating Industry 4.0 technologies
-
How flexibility, digitalisation and workforce agility are reshaping auto manufacturing
-
Key steps to building flexibility into production operations
Empowering regional leaders to interface directly with local governments expedites investment approvals and tailors workforce development initiatives. The TBMNC project, for instance, benefited from a Transitional Job Development Investment Grant (JDIG) from North Carolina, committing Toyota to create 1,750 jobs and power the plant with 100% renewable energy.
While fostering decentralised "living laboratories" for innovation, the carmaker maintains global consistency through standardised KPIs and shared operational dashboards. This distributed yet coordinated model enhances resilience and allows for local adaptations within a globally consistent framework.
Regionalisation and building where it sells
Regionalisation and localisation are crucial for mitigating tariff impacts. With US Section 232 tariffs on Japanese automobiles (25% since April 2025), Toyota is accelerating US assembly of models like the Tundra, Camry, and RAV4 to reduce tariff liabilities, and beyond production, cloud-based supply chain tools further enhance this strategy, offering significant cost reduction potential.
Toyota's "building where it sells" principle now encompasses deeper operational synchronisation within regional ecosystems, localising critical components and aligning processes, supply chains, and digital platforms.
Conclusion: iteration, adaptability, and enduring lean principles
Toyota’s 2025 lean manufacturing system is a remarkable paradox: its core principles are steadfast, yet its structure and execution are radically updated. The company has meticulously retooled its organisation to thrive in an increasingly electric, digital, and decentralised world, retaining the foundational elements that made it efficient.
The long-term success of this sophisticated ‘hybrid model’ hinges on balancing continuous experimentation with unwavering consistency, and local agility with global discipline. Standardised KPIs and shared operational dashboards across regional sites are crucial for integrating localised innovations into a cohesive global strategy.
Toyota's adaptive approach may again serve as a blueprint for the automotive industry, not by chasing trends, but by masterfully integrating new tools and structural changes into the proven framework of the Toyota Production System.
Its core philosophy, the "Toyota Way," acts as a meta-framework, ensuring adaptations align rigorously with long-term objectives of efficiency, quality, and value creation.
Toyota's demonstrated ability to iterate within its deep-rooted philosophy, coupled with consistent investments in critical areas like battery manufacturing (nearly $21 billion committed to US manufacturing since 2020 for electrification), proves more durable than any fleeting technology or market trend.
This sustained capital investment in its operational foundation, even amidst short-term profitability pressures, underscores the strategic importance of foundational investment for sustainable operational excellence, making Toyota’s 2025 journey a compelling case study for professionals in automotive manufacturing.