Next-gen transparency
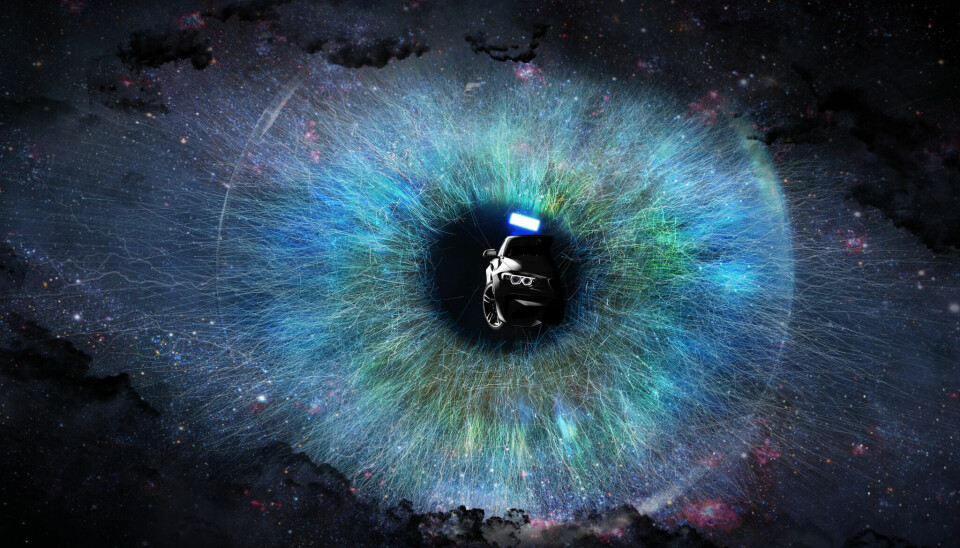
5G, AI, IIoT and the race for real-time visibility in auto manufacturing
As automotive plants grow more complex and dynamic, real-time visibility is becoming the foundation of smarter, more responsive manufacturing. From 5G networks and AI-powered inspections, to digital twins and predictive maintenance, leading OEMs are unlocking next-generation transparency and control on the factory floor.
Imagine an automotive factory where every robot, machine, and delivery cart communicate in real time. Thanks to 5G and IIoT, operations no longer rely on human checks or manual updates – as data flows seamlessly from the weld line to the warehouse. Equipment maintenance is predicted before failures, part delivery is perfectly timed, and quality inspections happen on the fly with AI-powered cameras.
This capability has never been more important. As automakers face narrower margins, growing consumer demand for customisation, and pressure to eliminate waste, visibility enables precision, efficiency and resilience.
The case of ZF: tier-suppliers and smart factories principles
At the Automotive Evolution North America conference last year, Fernando Bera, engineering supervisor and smart factory coordinator at ZF Transmissions described the company’s approach to visibility at their Gray Court factory. ZF has a strategy to connect all information from machines making it accessible, connected, traceable, and real-time through its Digital Manufacturing Platform (DMP).
“We have a lot of apps that are connected into these (DMP) machines, which deliver real results. Our future is no paper, and no wasting time in getting information from the production floor, so we can use this time to focus on the root-cause analysis and all the information comes directly from the machines,” said Bera.
How visibility is being implemented across the industry
Area of Impact | Description | Example |
Operational Efficiency | Improves material flow and reduces bottlenecks through real-time insights into shopfloor activity using IIoT sensors. | Ford’s Michigan Assembly Plant streams machine data to the cloud to detect delays and reroute work in real time. |
Quality & Compliance | Ensures part traceability through barcoding, RFID, and blockchain, helping meet regulatory standards and manage recalls. | Stellantis uses blockchain-backed traceability across North American sites for quality control and recall readiness. |
Downtime Reduction | Reduces unplanned outages using predictive maintenance powered by machine learning algorithms analysing equipment data. | Nissan’s Smyrna plant cut unplanned maintenance events by 30% using sensor-based condition monitoring. |
Supply Chain Resilience | Provides real-time insight into inbound logistics and supplier inventory to mitigate disruption risks and bottlenecks. | BMW’s Control Tower in Dingolfing monitors global parts flow and integrates supplier data to prevent disruptions. |
The 5G era: How connectivity is enhancing visibility across vehicle production
As automotive plants become more complex and digitally integrated, traditional connectivity methods are proving inadequate. Wi-Fi and Ethernet, once sufficient for connecting isolated machines or workstations, lack the speed, bandwidth, and reliability needed for real-time, plant-wide communication. This is where 5G steps in as a game-changer.
Private 5G networks offer ultra-low latency (as low as 1 millisecond), high bandwidth, and network slicing capabilities (splitting one big 5G network into smaller, separate “mini-networks” with each ‘sector’ assigned to different tasks); allowing manufacturers to prioritise critical data flows. This ensures seamless machine coordination and instant data exchange between equipment, robots, and digital systems. For automotive factories, managing high-mix, low-volume production scenarios, such responsiveness is vital. Such an approach further reduces the risk of signal congestion and enables device connectivity at scale.
Bosch, Siemens, and sea-change in digital production
Bosch and Siemens have been among the early adopters, leveraging 5G to enable digital twin visualisation and live monitoring of production environments. Bosch’s pilot plant in Stuttgart utilises 5G to connect hundreds of sensors and control systems, feeding real-time data into digital models that allow operators to detect inefficiencies and intervene remotely. The system supports AGV coordination and live condition monitoring across assembly cells.
With deterministic communication through 5G and Time-Sensitive Networking (TSN), production lines can orchestrate precise actions between robotic arms, AGVs, and quality stations.
Read the article:
This integration unlocks new levels of visibility – detecting anomalies, rerouting flows, or retooling lines without physical intervention. TSN ensures that time-critical control data is delivered with guaranteed latency, even in the most data-intensive settings.
Siemens, meanwhile, has integrated 5G and edge technologies across its showcase facility in Amberg, Germany, where smart sensors and AI-driven analytics work in tandem to monitor production quality and equipment health in real time. The plant uses digital twins to simulate and optimise workflows, while autonomous systems adjust processes on the fly.
Key enablers of visibility: Tech stack overview
True visibility in automotive manufacturing is powered by a layered technology stack that seamlessly connects physical assets with digital intelligence. At the foundational level, IIoT sensors and RFID tags embedded in machines, tools, and components capture real-time operational data – ranging from cycle time and machine vibration to part temperatures and usage frequency. This forms the foundation of live monitoring. These devices must be ruggedised, secure, and interoperable across multiple systems to support a broad range of use cases.
Edge computing devices sit near the production lines to process this data locally, enabling real-time decision-making. These devices use AI algorithms to detect anomalies – such as early signs of equipment wear or deviation in quality metrics – before they escalate into major issues. This level of responsiveness is critical for lean and just-in-time production systems. It also reduces the strain on central IT infrastructure and minimises latency compared to cloud-based analytics.
“By implementing the 3DEXPERIENCE platform fully on the cloud, Volkswagen, Audi and Porsche will harness the power of AI-driven virtual twins to accelerate innovation, streamline processes, and bring cutting-edge vehicles to life—before a single part is physically built.”
Sabine Scheunert, Managing Director, EUROCENTRAL, Dassault Systèmes
At the visualisation layer, digital twins and operational dashboards provide a dynamic, synchronised view of manufacturing systems. These digital representations allow plant managers and engineers to simulate process changes, test production scenarios, and predict downstream impacts without disrupting the physical environment.
Crucially, Manufacturing Execution Systems (MES) and Enterprise Resource Planning (ERP) platforms are being integrated to bridge the shopfloor and business systems. This ensures that production decisions are aligned with demand forecasts, inventory levels, and supply chain schedules.
Dassault Systèmes and Volkswagen: cost-savings and efficiency through digital integration
Dassault Systèmes has demonstrated in multiple automotive deployments how MES-ERP integration reduces inventory holding costs by 15% while enabling traceability and real-time synchronisation across production and business planning functions. This alignment supports accurate reporting, compliance, and improved cross-functional collaboration.
The approach to integration is now being scaled to an enterprise level, powerfully illustrated by the Volkswagen Group's new partnership with Dassault Systèmes. To advance its shift towards software-defined vehicles, Volkswagen Group is adopting the 3DEXPERIENCE platform as its core engineering and manufacturing system. The long-term partnership will bring Volkswagen, Audi, and Porsche onto a unified, AI-powered cloud-based environment to streamline operations and accelerate development.
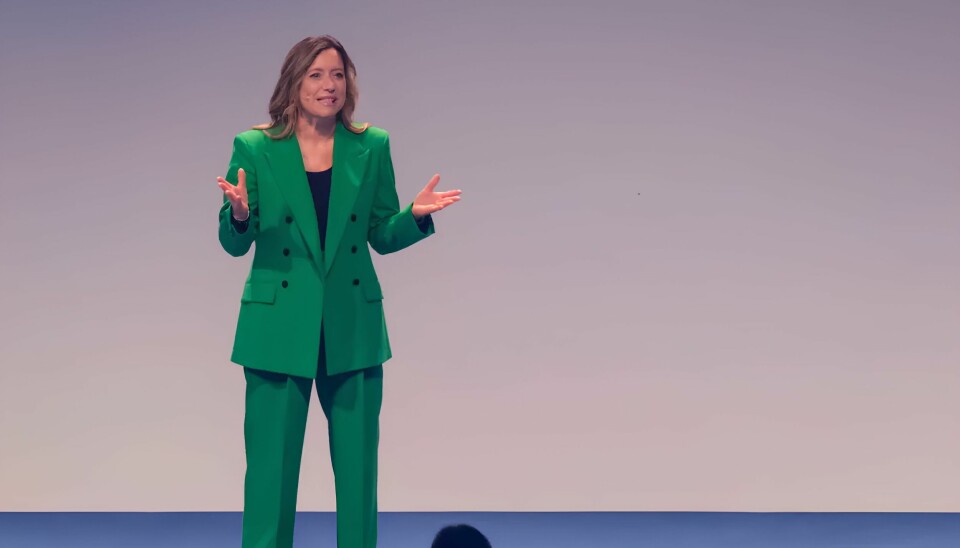
Sabine Scheunert, MD, EUROCENTRAL, Dassault Systèmes, Advisory Board Member at Volkswagen Group, (and ex-VP Digital & IT Sales/Marketing, Mercedes-Benz AG), highlighted the broader strategic implications of this partnership in a recent LinkedIn post: “By implementing the 3DEXPERIENCE platform fully on the cloud, Volkswagen, Audi and Porsche will harness the power of AI-driven virtual twins to accelerate innovation, streamline processes, and bring cutting-edge vehicles to life—before a single part is physically built.”
Volkswagen’s shift in this direction is another signal of the increased integration of AI and AI-driven digital twins into vehicle design and production. The 3D UNIV+RSES knowledge platform, an integral part of this collaboration, aims to enhance efficiency, regulatory compliance, and sustainability.
The shift to 5G is not just about faster data - it’s about transforming factories into responsive, intelligent ecosystems.
Top benefits in action
Benefit Area | Description | Example |
Real-Time Quality Control | AI-powered vision systems detect defects (micron-level precision), trigger real-time process adjustments. | Magna’s Ontario stamping facility uses AI cameras to reduce scrap and rework. |
Predictive Maintenance | AI analyses vibration, heat, pressure to predict breakdowns, schedule maintenance efficiently. | Toyota’s Georgetown plant cut unscheduled downtime by 60% using predictive maintenance. |
Flexible Production | Digital twins and smart config enable quick switching between models without halting production. | Volkswagen’s Wolfsburg plant shifts between ICE, hybrid & BEV on the same line. |
Supplier Integration | Real-time dashboards improve forecasting, reduce inventory waste, enhance delivery performance. | BMW’s Leipzig plant improved on-time delivery by 25% using connected logistics dashboards. |
Challenges and pitfalls to be cautious of
Despite the transformative potential of visibility technologies, automotive manufacturers face a series of complex challenges in deploying them effectively. Chief among these is the intricacy of integrating diverse technologies across operational (OT), information (IT), and telecommunications (telco) networks. Many plants operate with legacy control systems that were never designed for open connectivity or real-time data exchange. Retrofitting these environments to support IIoT devices, edge computing, and AI-based analytics can be technically demanding and costly, particularly without a clear roadmap for systems harmonisation.
Cybersecurity presents another critical hurdle. As manufacturers become more connected - from shopfloor sensors to cloud-based digital twins – their exposure to cyber threats expands significantly. Safeguarding production systems requires robust data governance, real-time threat detection, and layered access controls.
There’s also the human element. The transition to visibility-driven manufacturing demands new skill sets in data science, systems integration, and network management – skills that are often in short supply within traditional manufacturing workforces.
Finally, the cost of scaling visibility remains a barrier. While pilot projects can deliver clear value, expanding them across large, complex manufacturing environments requires significant investment. Many OEMs have adopted a phased approach – starting with critical production cells or high-value equipment – to demonstrate ROI before scaling plant-wide.
From 5G to 6G and smarter production
As automotive manufacturing continues its digital transformation, the next wave of innovation is already forming on the horizon. Technologies like 6G, advanced vehicle-to-everything (V2X) communication, and AI-led self-optimising systems promise to push visibility beyond the factory floor to encompass the entire value chain – from R&D to the end-user.
6G, still in early development stages, is expected to offer latency as low as 0.1ms and massive bandwidth, enabling hyper-real-time communication between vehicles, infrastructure, and manufacturing systems.
This will allow OEMs to build closed-loop ecosystems where data from vehicles on the road informs production processes in real time, creating a continuous feedback loop for quality, customisation, and demand planning. Ford’s CV2X pilots – first in China and now in the US – show how vehicles and infrastructure can communicate in near real-time.
Meanwhile, AI-led digital twins will become more autonomous. Instead of merely mirroring physical processes, future twins will anticipate changes, simulate multiple response scenarios, and adapt machine behaviours automatically.
BMW’s iFACTORY and the expanding digital ecosystem in vehicle production
BMW’s iFACTORY vision is already laying the groundwork for this future by deploying digital twins across more than 30 plants, enabling virtual planning, collision checks, and factory layout optimisation before physical build-out – slashing production planning costs by up to 30 %.
The shift towards ecosystem-wide visibility will also strengthen cross-plant collaboration and supplier integration. We’ll see more digitally federated networks where tier suppliers, logistics providers, and OEMs operate on shared platforms with real-time transparency - driving collective resilience and efficiency.
More Smart Factory stories
-
Automotive industry faces workforce upheaval in 2025, reshapes jobs amid shifting tech
-
Modular manufacturing moves automotive production into the future
-
Boosting automotive production efficiency with AI-powered predictive maintenance
-
Augmented Reality transforms automotive production quality control and efficiency