“Our future viability is not a given”: BMW Leipzig’s plant manager Petra Peterhänsel
Despite the crises, the BMW plant in Leipzig is optimistic about the future: in an interview, plant manager Petra Peterhänsel explains how investments in electrification and automation should contribute to a rosy future for the location
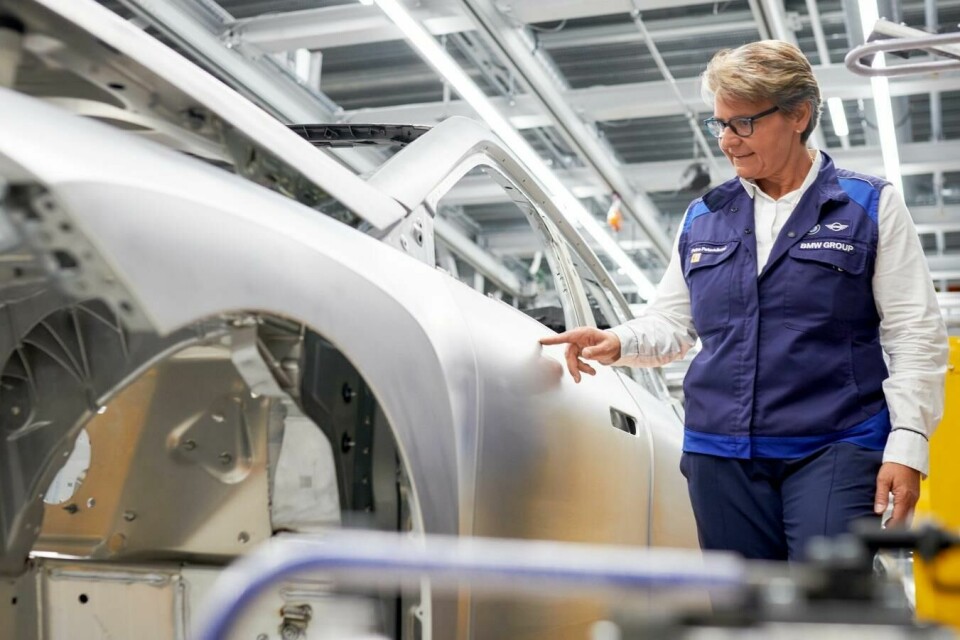
While other plants in the industry are suffering multiple shocks, people at BMW’s Leipzig plant in Saxony are looking ahead with a sense of optimism. This is due to an increase in the number of Mini models and a projected ramp-up of production. Plant Manager Petra Peterhänsel explains how the investment in electrification and automation is expected to help create a hopeful future for the location.
Ms. Peterhänsel, you have been the plant manager at BMW’s Leipzig plant, the newest production facility in the automaker’s German production network, for two years. Is the facility’s relative youth an advantage in dealing with the challenges arising from the industry’s transformation?
I have been in charge of the Leipzig plant for two years; since January 2022. It is definitely an advantage that sustainability was taken into account when it was built. And sustainability not only has an ecological dimension – it has economic and social aspects as well. It is extremely important to see the three topics in combination with one another, and we have done that here in Leipzig from the beginning.
During a transformation process, it is naturally a bit easier to have a relatively young plant as a site for new structures. That is what the BMW iFactory is getting. But the concept is not just intended for new factories. It is being implemented at all our locations – including our more-than-100-year-old main plant in Munich. When it comes to infrastructure, the options in Leipzig are entirely different from those at the Munich plant, for example. It is in the middle of the city with little space for development. The concepts were completely revamped here since Leipzig offered the option of building on a greenfield site.
What experiences were you able to draw on from your past management activities in the auto industry for the job of plant manager?
There were many of them. If you count my education, I have worked in the auto industry for 42 years. I can look back on my numerous experiences, I think you grow in any position that you are in. You learn new things, have new experiences, and take something with you from each job.
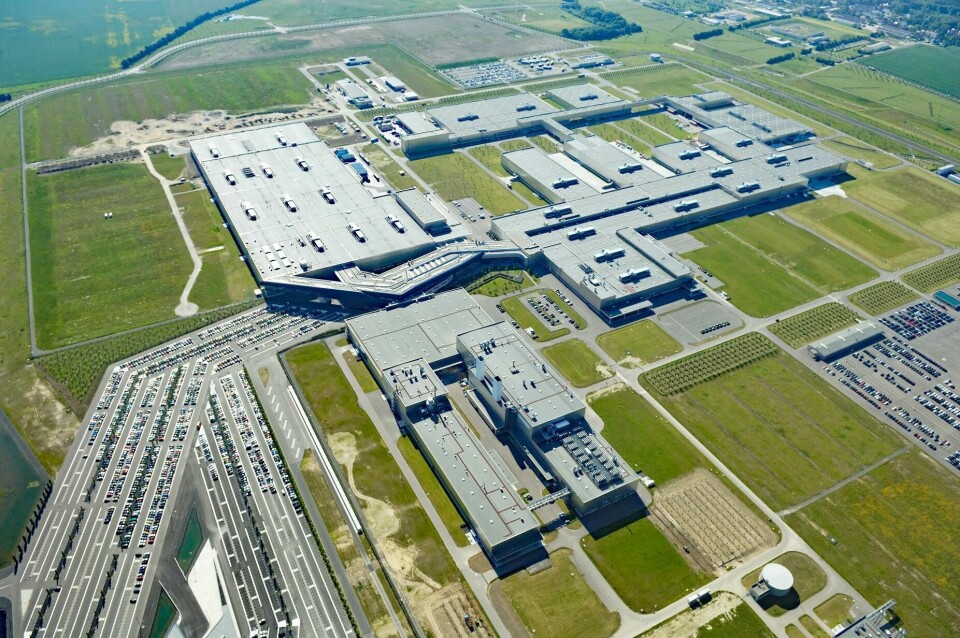
I took advantage of the opportunities that I was offered and dealt with many production technologies in the automotive area – whether they involved quality control, stamping or the technical analysis of noise or driving. I’ve always thought it was fun to learn. I draw on what I have learned to this day.
”The complete conversion to electric models is not under consideration in Leipzig”
My many assignments abroad – in Poland, Russia, Belgium and China – promoted my personal and professional growth. In some ways, they have very different cultures, mentalities and strategies.
As the sole female production manager in vehicle manufacturing in Germany, you have star power. To what extent do you find this special or unique?
I must say that I was often the first or the only woman in these positions in the past. Today, I take pride in being a female plant manager. But on the other hand, I wonder why I’m the only woman in this sort of job. The star power emerges from my ability to make things happen, personally and by virtue of my position. I regularly participate in discussions with politicians and people from industry, organisations, associations and universities. I am happy to talk about my role. Here, I try to inspire other women to follow a similar path. Again and again, the issue of the compatibility of career and family comes up, but today I think there are many opportunities to bring both aspects into harmony.
Sustainability seems to be a core project for you. What are you planning to help you move even closer to a sustainable factory?
We have had windmills at our facility since 2013. They provide up to 14 percent of our electricity supply. We also have a battery storage park to supplement them. Second-life batteries from the BMW i3 capture spikes in electrical production and store the excess power on an interim basis. We are also constantly working on the use of hydrogen in our paint department.
In 2022, we put our first bivalent burner into operation, which can switch flexibly between natural gas and hydrogen. We have now converted our first dryer line, and the work on converting a second line is already underway. Photovoltaic technology is another aspect. When it comes to sustainability, I believe diversification is important so we won’t be dependent on one or another energy source. By 2030, we want to reduce CO2-emissions from manufacturing by 80 percent compared to 2019.
Let’s look at production more specifically. With the production launch of the Mini Countryman, a model from BMW’s British subsidiary is being built in Germany for the first time – on the same line as the BMW 1 Series and 2 Series. How do you manage the challenges that emerge from the different requirements and powertrain variations?
We are proud of the fact that we are the first BMW plant where two brands – in this case, BMW and Mini – are being built on the same line. That gives us four models with three different types of powertrain from two brands on one line. The scenario definitely required good preparation and planning. We use specific modular systems to facilitate the integration. All in all, we were able to take full advantage of the considerable flexibility that our plant offers, and are able to cope with the complexity thanks to our highly skilled employees. We are now ramping up for the Mini Countryman and can handle future derivatives in a continuous production process.
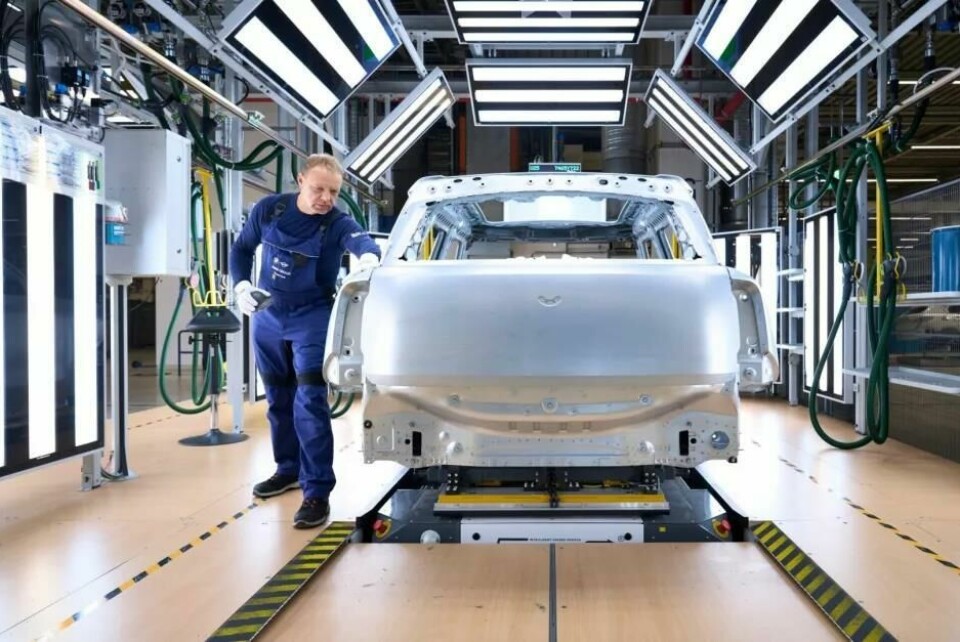
The BMW plant in Munich recently announced that it would no longer produce internal combustion engines as of 2027. Leipzig has just received major investments earmarked for electrification. Is your facility facing a purely electric future as well?
In fact, we have invested more than €800 million euros in e-component manufacturing since 2021, creating about 1,000 jobs at the site. For the production launch of the all-electric Mini Countryman, we reproduced the entire process of high-voltage battery production. The battery for the Countryman is manufactured in-house.
“Digital solutions are in use and have a real impact on our production processes”
The complete conversion to electric models is not under consideration in Leipzig. We are building three drivetrains – internal combustion, plug-in hybrids and all-electric vehicles – on one production line. In the future, we will be able to respond to customer desires flexibly, using the installation. For example, we can increase the share of all-electric vehicles on short notice.
Let’s take a moment to look at the numbers. In recent years, your production capacity has decreased slightly. Where should the production volume be in the medium-term?
As you look back, you can clearly see that the Covid years and the issue of semiconductor procurement had an impact on production volumes. But we had already started to gradually expand the plant’s capacity in 2018. This year, we plan to build more than 250,000 units.
As of 2025, our goal will be more than 300,000 units. We have almost completed an expansion to bring volumes as high as 350,000 units. And we have flexibility. With the Mini Countryman, we have a high-volume vehicle in our portfolio. Here is something that I can announce: We have two assembly shifts right now, but in the fall of this year, we will add a third shift. With an overnight shift, we will be building vehicles around the clock.
BMW’s iFactory production master plan is putting a particular focus on digitalisation in addition to sustainability and flexibility. What does the short-term roadmap for this field look like in Leipzig?
Aside from the cloud-based Factory Viewer that we used to scan the entire plant in 3D, one focus is on the use of autonomous driving systems. The technology has already been implemented in Dingolfing, and we are going to be the second plant to get it. We also have launched an app project here. Our innovation and digitalisation team is working with trainees to develop apps to deal with certain tasks and problems that occur on the shop floor.
The issue of artificial intelligence also comes into play, in combination with camera-based quality systems that perform automated surface inspections. We have also incorporated scanners into production systems, which makes manual scanning unnecessary. Individual parts or even entire cars are now captured automatically to support process optimisation. Except for the autonomous transport systems, which will be implemented in mid-year, all these solutions are in use and have a real impact on our production processes.
The wave of new, young competitors from China is putting enormous competitive pressures on some European automakers. Have these companies had an impact on your strategies?
Of course, we pay close attention to what Chinese competitors are doing and what we can learn from them. In China, they are basically doing the same thing we are here: building cars. But their speed of decision-making and execution is extremely fast, and they are very ambitious and determined. In the entire area of digitalisation, China is a step ahead – we still have a lot to learn. Still, it is important to note that, at the end of the day, we learn from each other on a daily basis throughout the entire BMW production network, and apply best practices across plants. We should keep in mind that the competition tends to be in the lower segment – and not at the premium level where we operate. In addition, we are well represented in the Chinese market. BMW has its own strategy for international markets. So that should be the focus instead of always looking to see what others are doing.
”We aren’t taking our future viability for granted”
On a different topic: BMW CEO Oliver Zipse sees the shortage of skilled workers as a risk to BMW’s growth. Yet you plan to add staff here in Leipzig. How are you tackling the problem?
Last year, we were unable to cover the increase in e-component output with company employees alone, and had to go outside for staff. Even though we are a well-known, attractive employer, we didn’t just have a problem of finding skilled staff – it was even hard to find new employees at all. Recruiting was quite difficult for a while. But we are now seeing a greater inflow. One reason is that we have been looking outside Saxony.
Working with staffing agencies, we are expanding our recruiting into eastern and southern Europe. We already have employees from 77 countries, including a high proportion from Syria, Poland and Spain. You would have to say we are in a comfortable position. We continue to manufacture products on a stable basis and our future is secure. As everyone knows, that may not be the case at every manufacturer.
Do you sense that employees have some concern for their jobs since automation is taking on more and more tasks, and the manufacturing of the future will get along with significantly fewer staff?
Over the last few years, we have gone through a number of unsettling situations. But despite Covid, the semiconductor crisis and other challenges, we have always believed in the future of the plant. The temporary end to electric mobility at the Leipzig plant due to the phaseout of the i3 and i8, initially raised questions. But as you see, we are now building an all-electric vehicle and investing in electrification, beyond our e-components.
This transformation process alone was a sign to all our employees that the plant is moving forward. We aren’t taking our future viability for granted. We continue to work on it. Sure, we are doing a good job, but that doesn’t mean we can stand still for long. We have to keep improving. But I would say no one here needs to worry about his or her job under these circumstances.
This Interview was translated from an article published in AMS’ sister publication, Automobil Produktion, and was carried out by Ronja Schmiedchen and Yannick Tiedemann.