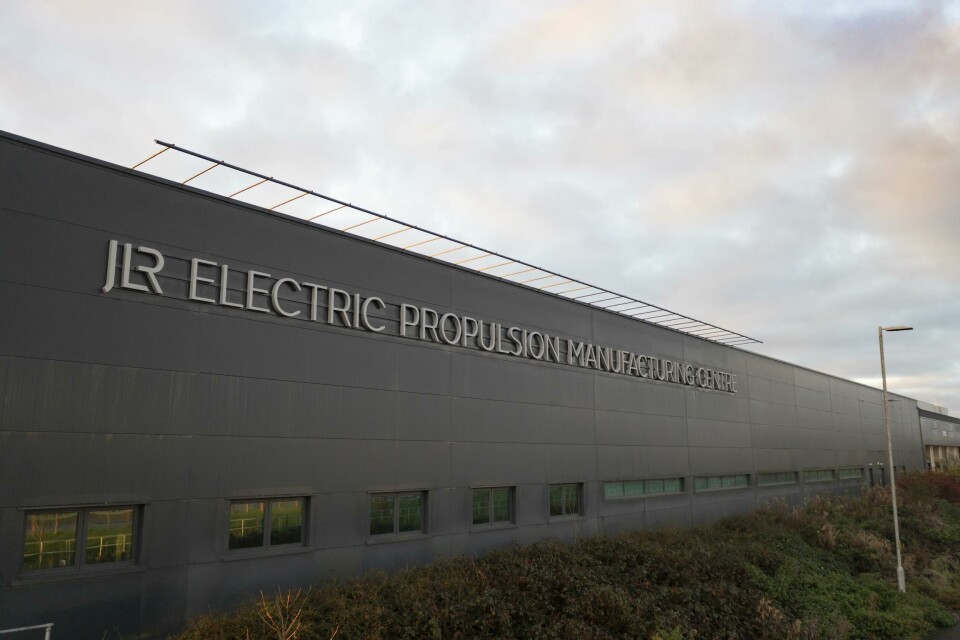
Powertrain – Reducing waste in machining fluids
Sustainability projects at plant and team levels are vital to reducing the operational carbon footprint in manufacturing operations. These range from simple energy management protocols to more involved process improvement related projects. JLR offers a very interesting case study on the latter at its Electric Propulsion Manufacturing Centre.
JLR’s sustainability programme encompasses every aspect for the company’s operations with projects ranging from high capex investments in infrastructure and renewables, to more localised, plant-focused projects. The latter play an important role in the overall reduction of the OEM’s carbon footprint, so while big steps are made through the shift to an electric vehicle product line up, the remaining gains are perhaps harder won, since the areas of operations that can make these improvements are diverse and complex to manage.
Speaking to AMS recently, JLR’s manufacturing sustainability transformation lead, Garrett Bell, noted that an important part of this process, particularly at the plant operational level, was creating a culture where sustainability is embedded in every process and operation, actively engaging the respective teams in identifying areas where improvements could be made and developing the solutions to achieve these.
This approach is seeing the OEM’s sustainability drive gathering momentum with a number of successes. One project at the company’s Electric Propulsion Manufacturing Centre (EPMC) at Wolverhampton in the UK, offers a good case study of the type of solutions coming from the operational teams.
The EPMC is currenting undergoing a reconfiguration of its operations in preparation to produce electric drive units and battery packs. The petrol and diesel ICE production operations are being consolidated into a single area, but the machining tasks and equipment will also serve the EV component production.
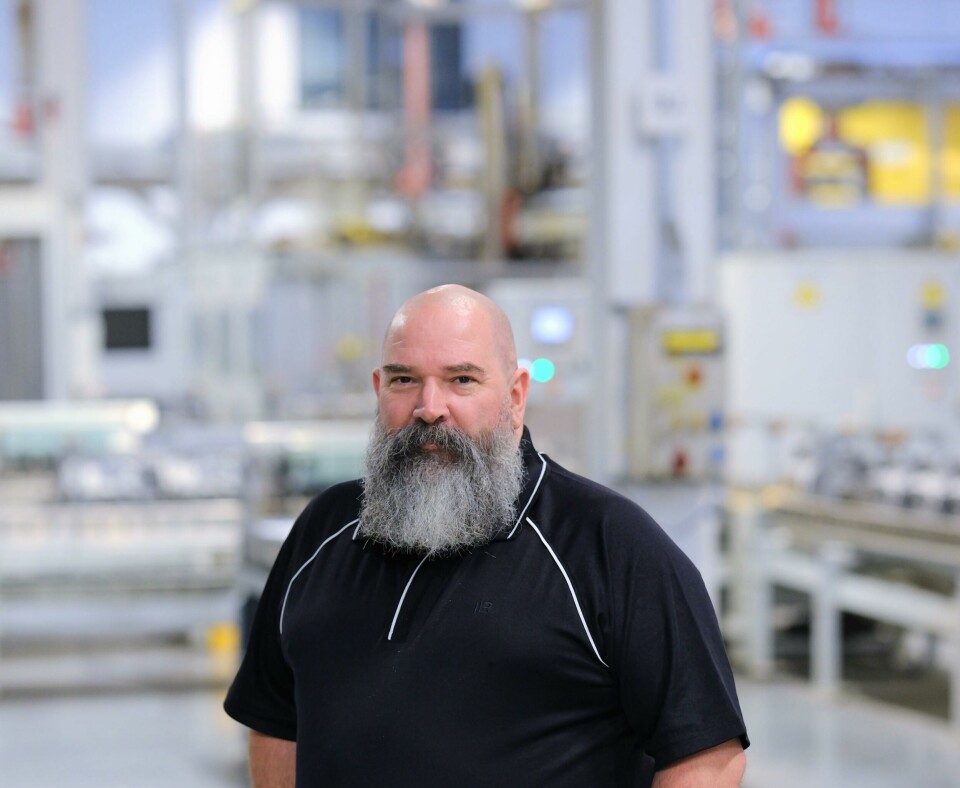
Improving waste management
Stuart Summers, maintenance and technical services manager at the EPMC explains some of the areas that the teams have been working on to improve the sustainability of operations.
“As part of my role, I look after the entire waste stream out of this facility, and we were looking at how we can reduce our waste to make us more sustainable in the long term. Our largest waste stream is metals, the waste steel and aluminium from machining operations, these are collected and sent for recycling. Our second biggest waste stream is fluids that go off site to be disposed of.”
The fluid disposal was an area that Summers and his team wanted to address but it was a challenge due to the process requirements.
Powertrains are highly engineered and complex, requiring a number of tightly controlled heating, cooling, machining and cleaning processes, all of which consume high levels of energy and fluids. Given the need for rigorous quality standards, these are difficult process steps to adjust or change without an extensive validation programme, but the team at EPMC, working closely with a technical supplier, have developed a solution which dramatically reduces waste in the machining and washing stages. Summers explains.
“Following the machining processes there are intermediate and final wash stages to thoroughly clean the components before they go to assembly. Each wash booth has a heavy-duty robot that picks up the component and moves it through high pressure jets, and underneath the robot is a tank containing approximately 3,000 litres of the cleaning media.
“After about seven or eight weeks, we start to see a deterioration in the quality of the cleanliness in the components. So, we perform a deep clean of each wash unit, pumping out all the used cleaning media and then refilling with new media. The old media is then pumped into a tanker for disposal off-site.
“So, we have 37 washes averaging 3,000 litres and we’re doing a system cleaning process and replacement of the wash media every seven to eight weeks, which amounts to 777 tons of fluids a year being disposed of.”
Complimentary formulations
Industrial lubricants supplier Castrol had approached the EPMC team with new formulations of both the machining coolant and wash media, which it claimed were complimentary and could be mixed, so the used wash media could be used to top up the machining coolant removing the need for large scale disposal. Given the performance requirements of both fluids, before they could be introduced into production processes, each would need rigorous testing and validation individually and then combined, and this would require a test rig separate to the main production lines.
Having set up a separate machining station, isolated from the main production flow, the coolant underwent a period of testing and was found to perform to the required standards. Similarly, the wash media was also tested with satisfactory results. Summers admits he was initially sceptical about mixing the used wash media with the coolant, but after extensive testing the performance of the coolant was found to be unaffected by the wash media.
“We were testing for 11 months. So, we picked our hardest machining task and ran a single CNC machine for cylinder heads. This is where we would expect to see the most problems with a coolant around the valve seats, as you get a lot of ‘chatter’ on the valve seat if the coolant is wrong.
“To start with we ran this machine for four months just with the coolant. After four months, we swapped a wash over, we checked the wash media, and then we started adding that wash fluid into the coolant system as well, just to check that the mix wasn’t going to damage it, and proved it worked.”
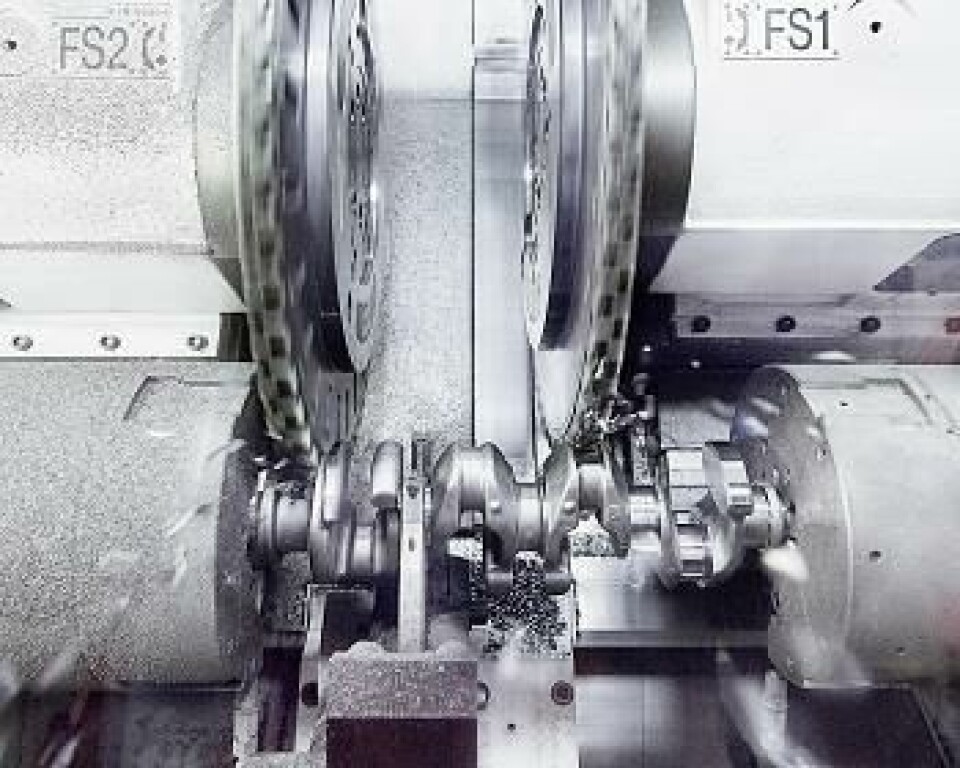
The testing and validation process was a joint effort across teams at the EPMC. Summers team, responsible for the coolant, worked with the continuous manufacturing engineering (CME) team, who monitored the quality of the product.
“They were tracking the data back from all the components that were being measured and we initially increased the frequency of checks running with the new coolant until we had confidence that it was okay. And again, once we started adding the wash media, we upped the frequency of the checks. We typically do a 30-part capability run and then we stop the machine while we get everything measured and checked. And once we know that’s okay, we then run it, but with an increased check frequency.”
Now the used wash media is carefully filtered and used in different concentrations, depending on the machining application, with the coolant. Summers notes that there are now 21,000 litres of the wash media saved, stored and ready to use.
In terms of the next steps, Summers says the wash process is also seeing further development to reduce energy consumption.
“What we’re working on now is reducing the temperature of the wash. When we first started with this wash process, we were running them at 65°C, but we’ve now got this down to 55°C. The main challenge with reducing the temperature is not cleanliness, it’s drying the component. We need to dry a component very quickly because we have a fixed 40 second cycle time. To make this work, when the part come out of the wash process it’s placed into a vacuum chamber, which then boils the media off.”
Summers notes that the vacuum chamber process was made more efficient by the production teams as part of their ongoing improvement activities.
“They put polystyrene fillers into the vacuum boxes so that there’s less volume. This means you can pull a vacuum quicker, using less energy”
Culture of continuous improvement
As well as big, longer-term projects like fluid waste management, Summers notes that the teams are actively encouraged to look for improvements across operations, even those on a smaller scale.
“We run a kaizen of the month, so we celebrate the top three kaizens that come from the plant. But every little thing that everybody does - it all helps. It can be the basic things such as turning lights and equipment off when not in use. So, we manage the baseline electricity usage at each of the plants and we’ve got improvement targets around that.”
Summers says that there’s always been a strong ethos around continuous improvement since the EPMC (formerly EMC) was opened, but feels the Reimagine programme has boosted the emphasis on sustainability.