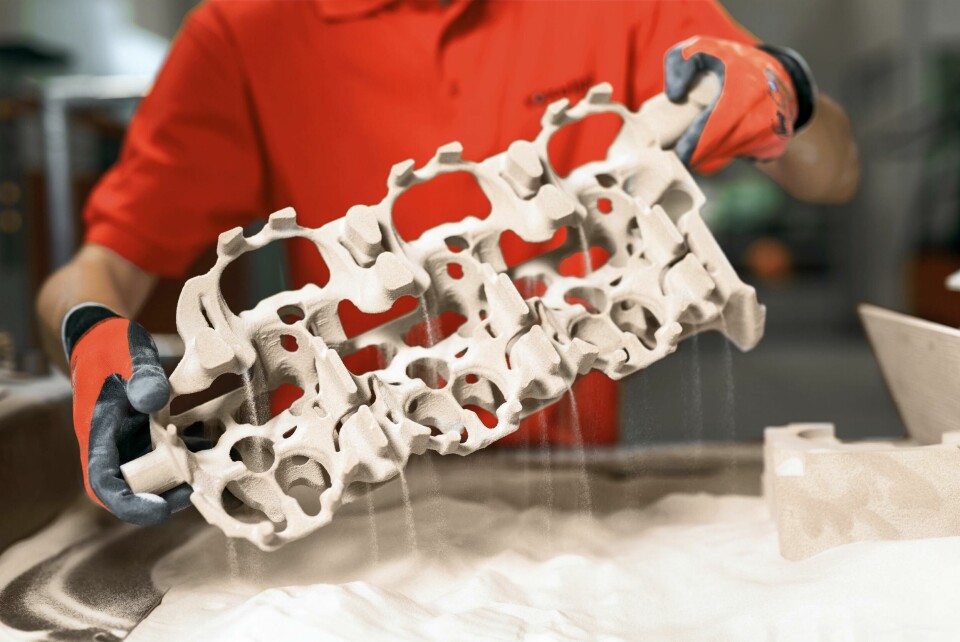
Additive manufacturing: Supporting sustainable production
3D printing is advancing, and while new materials and processes could make it more eco-friendly, experts think that component elimination may be the way forward.
Additive manufacturing (AM) is evolving, and fast. Technologies and tools used in the processes are advancing, resulting in increased efficiency, scalability, and cost effectiveness. AI is being leveraged with dramatic effect, with some adopters reporting massive reductions in printing and engineering costs. New materials are being trialled, offering avenues of exploration for both design and production, and allowing for improvements in both manufacturing and the end product.
This process is also an avenue for companies looking to reduce their environmental impact and transition to circular economy principles. According to Sherri Monroe, executive director of Additive Manufacturer Green Trade Association (AMGTA), AM can help support the circular economy in multiple ways and will become a crucial technology as carmakers aim to improve their eco credentials.
Designing parts, components, and systems without the constraints of traditional manufacturing has the immediate benefits of resource efficiency…”
Sherri Monroe, AMGTA
Additive Manufacturing beyond parts
“The transformational potential of AM really refers to much more than the printing of components,” Monroe explains to AMS. “Designing parts, components, and systems without the constraints of traditional manufacturing has the immediate benefits of resource efficiency, with reduced power consumption and raw materials, as well as producing less waste in the production phase. But the full potential for AM is realised in a strategy that begins well before anything is printed.”
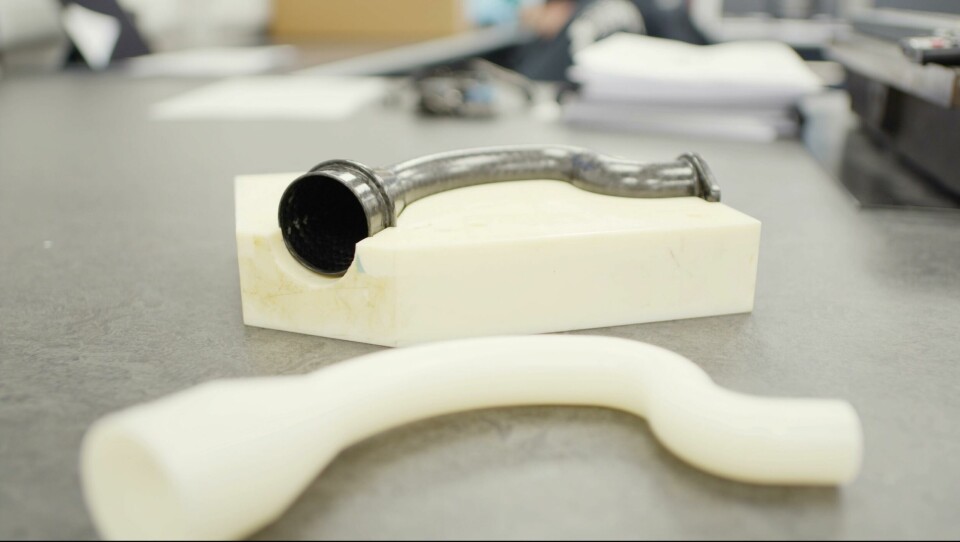
Monroe thinks that industries like automotive can change drastically by including additive as a cornerstone of operations. It could, she suggests, potentially impact every aspect of how businesses work, from manufacturing and to logistics, distribution, inventory and even finance. Weighing in on the topic, Fadi Abro, global automotive director at Stratasys, encourages the idea of including AM as a cornerstone of car making operations, and suggests that it can revolutionise the design of vehicle components.
By using software-driven 3D printing tools, Abro says that designers can produce high quality and reliable parts. These parts can then be shared digitally, allowing colleagues to create exact replicas regardless of where in the world they are based, avoiding the transportation of parts and tools across the globe. He also thinks that additive-driven design could offer various benefits that help with circular economy principles, like enabling the creation of components with less parts, or providing opportunities for the use of bio-based materials.
AM is far more sustainable because production occurs layer by layer, resulting in more efficient use of materials. The next sustainability step involves using more recycled materials and biodegradable components”
Fadi Abro, Stratasys
From plant to polymer
“The past five to ten years have seen advancements in AM, mostly centring around materials, material properties, material development,” Abro recalls. “In terms of pricing and performance, a lot of the focus has been around material development. This shift is significant, as it marks a departure from the early days of the AM industry when 3D printing was primarily focused on appearances. Improving the materials repertoire enables 3D printing of fully functional end-use pieces.”
He highlights the use of bio-based polymers and recycled composites, as well as natural materials like wood fibres. These have been used by various companies to produce components through AM, and work is on-going with many other materials.
Chalmers University of Technology and the Wallenberg Wood Science Centre in Sweden recently published a paper showing how a hydrogel material made of nanocellulose and algae can be used in 3D printing to create a building material for architectural purposes. The materials used are abundant, found in plants, and could therefore be harvested sustainably while also generating zero waste.
Ingo Ederer, CEO of Voxeljet, tells AMS that there have been some significant developments when it comes to materials used in AM, and several improvements could allow adoptees to enhance their position in the circular economy. “The ability to 3D print materials depends on the AM technology used,” he explains. “With the binder jetting technology that Voxeljet uses, any powder material can be 3D printed as long as a suitable binder is available. Obviously, there are some criteria that need to be fulfilled, like flowability and recoatability of powders, printability and print head compatibility of fluids, but everything could be printed in theory. Many advanced materials are already available for 3D printing today, such as PA11 which is derived from castor beans and is therefore a bio-based polymer.”
Voxeljet also recently studied 3D printing of recycled construction waste, testing biogenic and mineral particle materials. Ederer states that it is important to carefully examine whether any of these materials can be used for end-use or safety-relevant applications in the automotive industry but thinks that they can play a big role in terms of the circular economy when it comes to producing tooling for end-use parts.
While Voxeljet pushes the boundaries on material development and application, Stratasys is busy trying to reduce the time it takes from when a customer orders a part to when it is produced. “Material developments pave the way for optimising manufacturing methods, particularly addressing throughput challenges,” Abro continues. “How do we get more out of a single system, or bank of systems? Can we create a print farm? While current equipment boasts impressive throughput, there’s still potential for improvement, and that is where our focus is.”
“AM also allows for consolidation of parts, meaning that parts that used to be assembled from multiple components can now be printed as one single part…”
Ingo Ederer, Voxeljet
Advancing eco-friendly automotive production
Moving on from progression in materials, Abro returns to the basic principles of AM and how they differ from other production methods. Additive, he states, is fundamentally more sustainable when compared to other manufacturing methods that have been used in the automotive space for many years. “Take CNC machining for example,” he notes. “A block of material is produced, and then the machines are used to whittle away everything that is not the part. It is a wasteful process, and by its very nature, additive is far more sustainable because production occurs layer by layer, resulting in more efficient use of materials. The next sustainability step involves using more recycled materials and biodegradable components.”
Ederer agrees, suggesting that at its core, AM is a more eco-friendlier manufacturing method than most others. “It can definitely help support a circular economy,” he clarifies. “It starts by reducing the amount of material used, and then there are the materials themselves. There are technologies available to reclaim the original printing materials, such as sand, plastics, or metals, and feed them back into the cycle. AM also allows for consolidation of parts, meaning that parts that used to be assembled from multiple components can now be printed as one single part. This, in turn, means fewer connecting elements are used, making recycling much easier.”
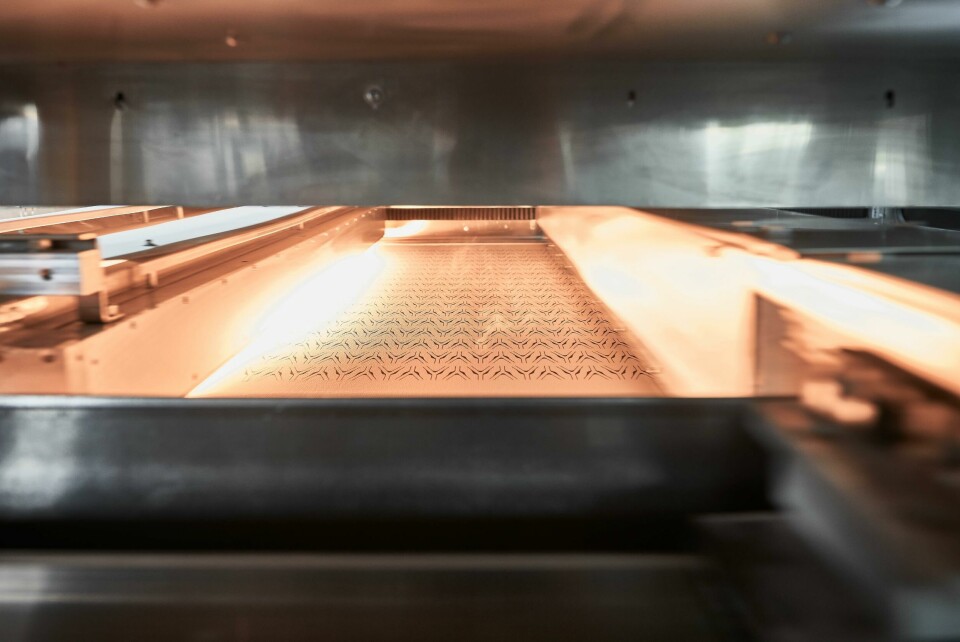
This brings us to end of life use and reuse. Depending on the material used, Ederer says there may be some difficulties in ensuring a 3D printed part could be reused and have a second life in automotive, but they could be used elsewhere. “In binder jetting, for example, unprinted powder can be recycled but should always be mixed with fresh powder to ensure specified material properties and quality. Our sand parts are predominantly used in the foundry industry, where recycling rates are already very high. On the other hand, our high-speed sintering (HSS) technology uses ink to colour white polymer powders resulting in black or grey dyed printed parts that cannot be recycled for use with HSS again because the technology requires the differentiation between black and white. However, the printed parts can be recycled and turned into pellets for injection moulding or filament for fused filament fabrication (FFF).”
Avoiding the circle
Recycling parts that have been made using AM will be an integral area of development for many companies in the field. But for Monroe, the ultimate goal for AM is perhaps to avoid the circular economy altogether. This, she explains, is because additive can help reduce overproduction and lower the number of parts being made in the first place by providing high quality, robust and reliable production. With fewer defects, the use of advanced materials that provide stronger and more efficient parts, and the inclusion of monolithic structures, Monroe thinks that a lower number of components will need to be made as AM becomes more commonplace and the technology continues to advance.
“AM practices certainly can lead to a more circular economy for resources,” she observes. “But AM can also help avoid the circle altogether for many currently overproduced products.”
Ederer also envisages a future where AM prevents parts from being made unnecessarily but decides to be cautious with his predictions for additive in automotive. Although he clarifies that 3D printed parts are still predominantly found in low volume cars, he is confident that they will become more widely used in mass produced models very soon.
“The advantages are so tangible and intrinsic: practically no tooling or retooling costs, almost no design restriction, high local flexibility of production, reduced assembly effort, more resource-efficient handling, lightweight construction and so on. Many associated problems are already solved today, but customers need to have the courage to break new ground in production. The automotive industry is sometimes rather hesitant when it comes to changing production methods, so with this in mind, AM will have to feel its way forward step by step. But it will happen, it’s simply a matter of time.”