The automotive value-add of additive manufacturing and simulation technologies: an agile and resilient powerhouse in engine development
Markforged’s additive manufacturing solves Punch Torino’s automotive challenges with robust camshaft tools. Simulation technology streamlines design, reducing iterations with a future focus on sustainable internal combustion engines and alternative fuels.
At its most basic level, automotive production is about optimising for internal, and external complexities. Punch Torino, (part of Dumarey Group NV) specialises in the design and development of innovative propulsion systems and is recognised for its ability to produce a wide range of prototype combustion engines and conduct the comprehensive development and testing of new components for existing engine designs.
A critical challenge in the engine build process is the installation of a timing chain which links the engine’s crankshaft to a pair of camshafts. These need to be locked in place to ensure precise alignment to ensure that valves open and close at the correct intervals to prevent engine damage.
To address this challenge, Punch Torino’s engineers have constructed fork-like camshaft locking tools, but as the automotive industry knows, even solutions can bring with them their own sets of challenges. Due to their critical role in engine operations and safety, the camshaft locking tool requires a high level of structural integrity, as well as ease and efficiency of production - an issue precipitated by the lack of available automotive components brought about by disruptions. This is the point at which the importance of partnerships shines through for Punch Torino.
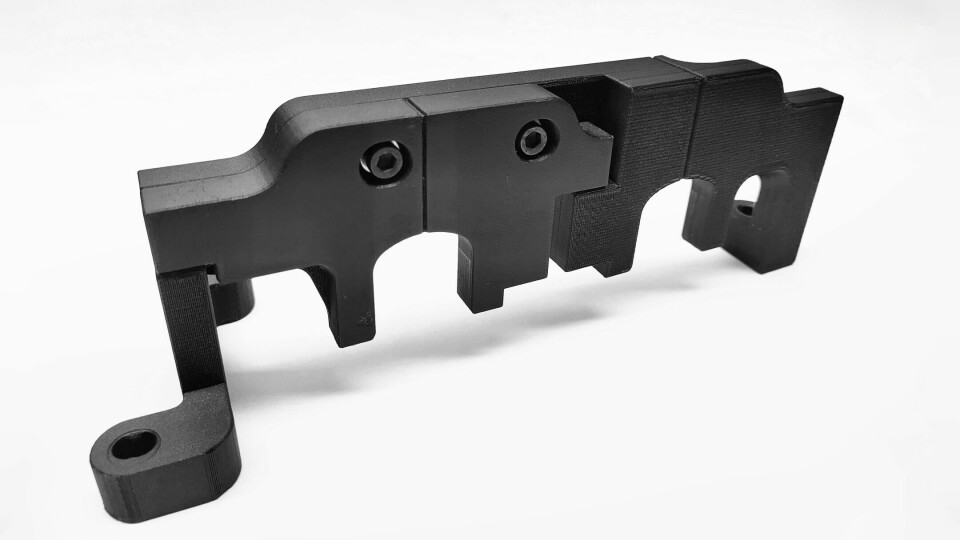
American additive manufacturing company, Markforged, has the expertise and technology perfectly fitted to solve Punch Torino’s auto production challenges.
The company designs, develops and produces an industrial platform of 3D printers, software and materials that enable manufacturers to print highly specific, intricate parts at the point-of-need.
The inarguable benefits of additive manufacturing
Markforged’s additive manufacturing holds the keys for Punch Torino’s challenges, but the technology has a wide array of potential solutions for automotive production. “At a high level, there is the fundamental benefit of the ability to manufacture complex geometries with ease,” says Rick Dalgarno, product marketing manager at Markforged. “But another key benefit is the ability to manufacture parts at the point of need, which allows for assembly lines to keep up and running; an example we’ve recently seen from a well-known automotive OEM customer of ours.”
Other customers saw measurable benefits from producing components in the thousands when traditional parts weren’t available due to disruptions, according to Dalgarno. The technology allowed them to immediately begin printing missing components and keep production lines operative, preventing costly and time-consuming rework at the end of the line.
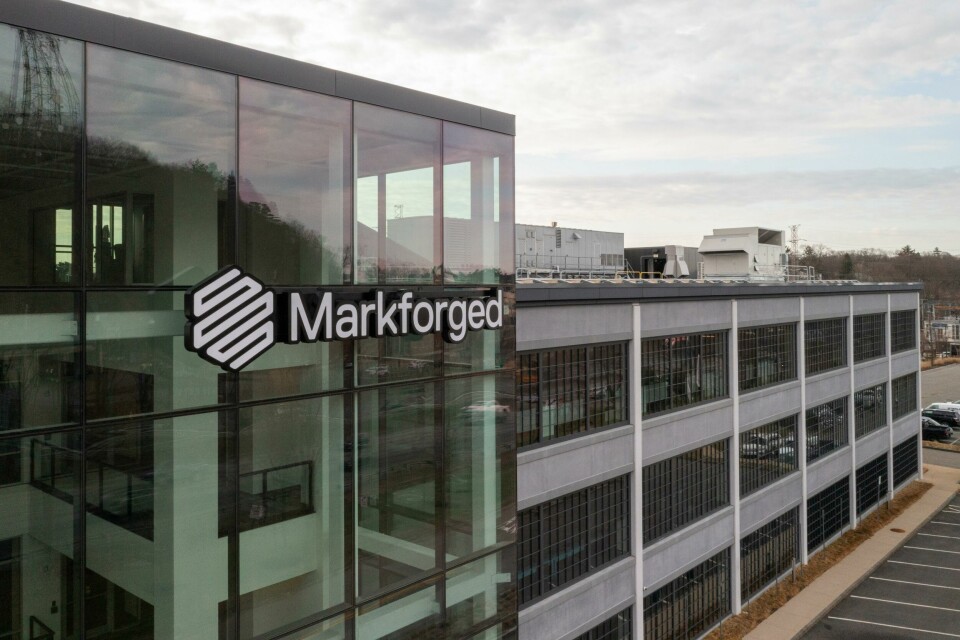
“If they weren’t able to produce these parts, they would have kept building the vehicles while still needing to set them aside and store them in a parking lot until the parts became available again, weeks or months later - clearly an incredibly costly option,” he says.
As a technological solution, additive manufacturing is flexible in producing components for numerous automotive specifications, but Punch Torino had very particular requirements for its camshaft locking tool. These related specifically to robustness, structural integrity and durability. “The tool needed to be really stiff, and it needed to be really strong,” says Dalgarno. “You don’t want that particular component breaking in service. In terms of structure, the benefit came from what we call continuous fibre reinforcement (CFR), and that’s our ability to put continuous strands of carbon fibre inside the component, making it an order of magnitude stiffer and stronger than a part that’s printed simply using plastic.” CFR was achieved using Markforged’s X7 additive manufacturing printer, with each camshaft locking tool requiring approximately 18 hours for the entire printing process.
Enhancing optimisation by digitising additive production: simulation technology
But this process was even further optimised through the introduction of a second technology - Markforged’s simulation tool, which provided clear enhancements to Punch Torino’s workflow. Dalgarno says, “without a simulation tool, you’re asking questions like, ‘how much fibre do I need?’, ‘where do I put it?’, ‘what will be the effect of adding fibre?’, ‘how much stronger, or stiffer is it actually going to be?’”
The power of simulation technologies lies in their ability to allow for design and structural tests without the costly occupation of manufacturing space, the expenditure of time or the resource-intensive activity of physical printing.
Valerio Ametrano, senior pre-production engineer and additive manufacturing lab coordinator at Punch Torino, adds, “simulation is in fact a very easy tool to use. And importantly, it allows the end users directly on operation to validate and test the properties and behaviours of the part before printing it. What this means is that even a non-specialist engineer is able to use it and extract all the advantages of structural analysis. This has significant benefits for automotive production.”
![“[Simulation] allows the end users directly on operation to validate and test the properties and behaviours of the part before printing it” - Valerio Ametrano, senior pre-production engineer and additive manufacturing lab coordinator at Punch Torino “[Simulation] allows the end users directly on operation to validate and test the properties and behaviours of the part before printing it” - Valerio Ametrano, senior pre-production engineer and additive manufacturing lab coordinator at Punch Torino](https://image.automotivemanufacturingsolutions.com/541091.webp?imageId=541091&width=960&height=720&format=jpg)
Markforged’s simulation technology essentially allows for virtual production experiments. With it, Punch Torino’s engineers are able to set up their parts in digital space, place fibres where they think they may need it, and run virtual tests in a matter of minutes - gaining quick feedback on how the component is going to perform in the real world.
Previously, the development of a new camshaft configuration necessitated the printing and testing of up to eight jig designs, a process often involving multiple iterations until the optimal configuration was achieved.
“Without simulation,” says Dalgarno, “they were doing these print-test-iterate cycles. And Punch Torino confirmed that in some cases, it took up to eight iterations to get the locking tool dialled in, and with each of those parts taking about eighteen hours to print - this translated into a lot of print time and related material costs.” Simulation also has the added benefit of allowing additive printers to be freed up for production while eliminating multiple prototype prints.
With the adoption of simulation from Markforged, the average number of locking tool design iterations has been drastically reduced from eight to three. This approach enables the team to simulate and print a typical locking tool in a single iteration, translating to a significant leap in efficiency.
According to estimations of the Punch Torino team, the use of Markforged’s simulation tech not only saves an average of eighteen hours per jig, but also streamlines the engineering time required for part design modifications, now managed entirely within the software.
Industry trends in engine development: ICE as indispensable to sustainability
It has become almost reflexive to reply, ‘electrification’ to the question, ‘what does the future of sustainable engine production entail?’ But Punch Torino has a different answer. Antonio Giulio Marino, engineering project leader at the company says, “when it comes to the future of engine development, the focus will undoubtedly be on sustainability. Our motto is that we want a future with sustainable mobility for all.
“But with this, we strongly believe that internal combustion engines (ICE) will play a critical role in realising this vision, and even more so in some market segments and countries. In Europe the push for electrification is more upfront, but we still see a big gap in terms of infrastructures to achieve this on a very large scale.”
Marino emphasises that countries like China and the United States have not announced any clear path concerning the role of ICE in their journeys towards electrification. China in particular, he points out, is investing in the acquisition of assets and technologies to improve their ICE capabilities.
Punch Torino strongly believes that there is a future for ICE in automotive, especially in regions outside Europe. Marino says the European ICE footprint will certainly shrink, “but there are still opportunities, and our approach is to exploit these opportunities by aggregating knowledge, technologies and component manufacturing capabilities to optimise costs while providing continued supply to the major car makers.”
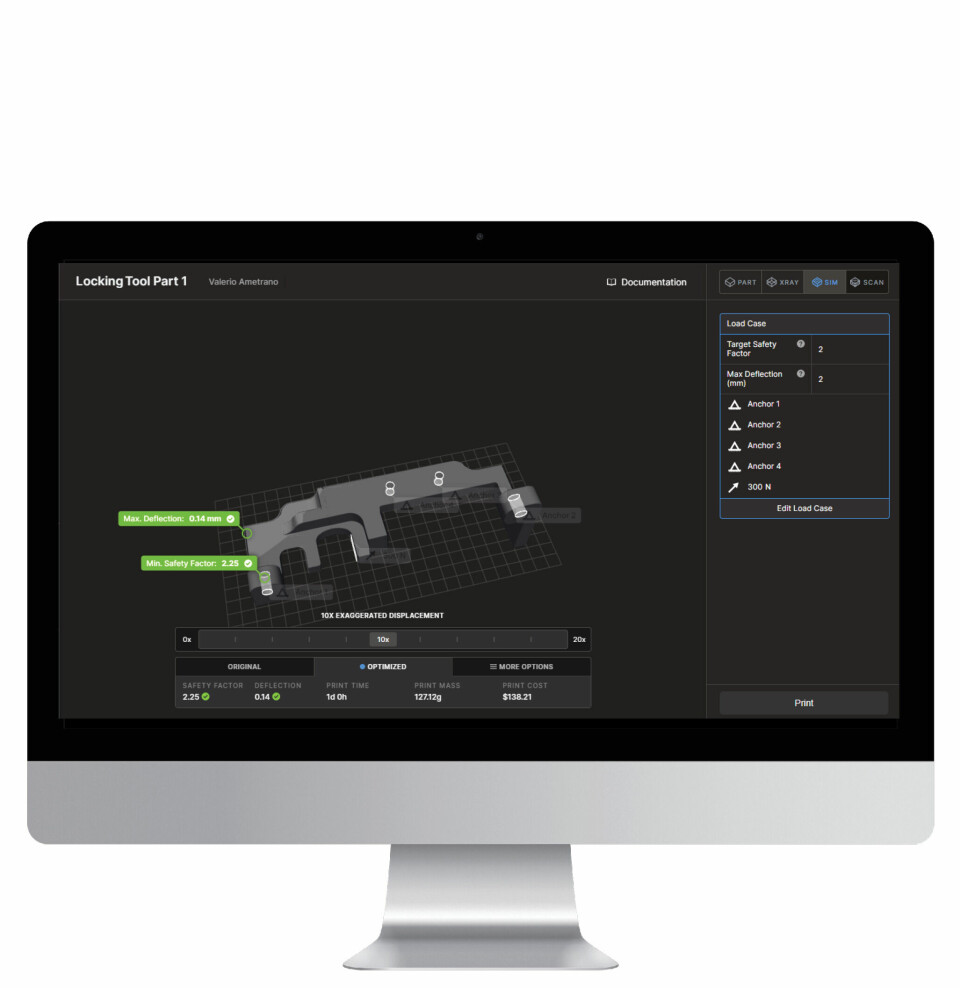
Approaching sustainability from an ICE perspective, “there will be different steps involved,” he says, “beginning with a focus on different levels of urbanisation,” but more importantly, “sustainability can only be achieved through the use of certain alternative fuel types such as eFuels, (produced with electricity from renewable sources, water and CO2), and Hydrogen - which will play a major role towards the final goal of carbon footprint reductions.”
Major ongoing developments at Punch Torino are mostly focused on making the best use of these alternative fuels and making them affordable on the path to zero carbon emissions.
The challenges and opportunities of additive manufacturing in engine development
Dalgarno thinks that one of the major challenges for additive manufacturing in automotive and engine development concerns getting more people to lean into the technology, take the time to learn about it and understand its value.
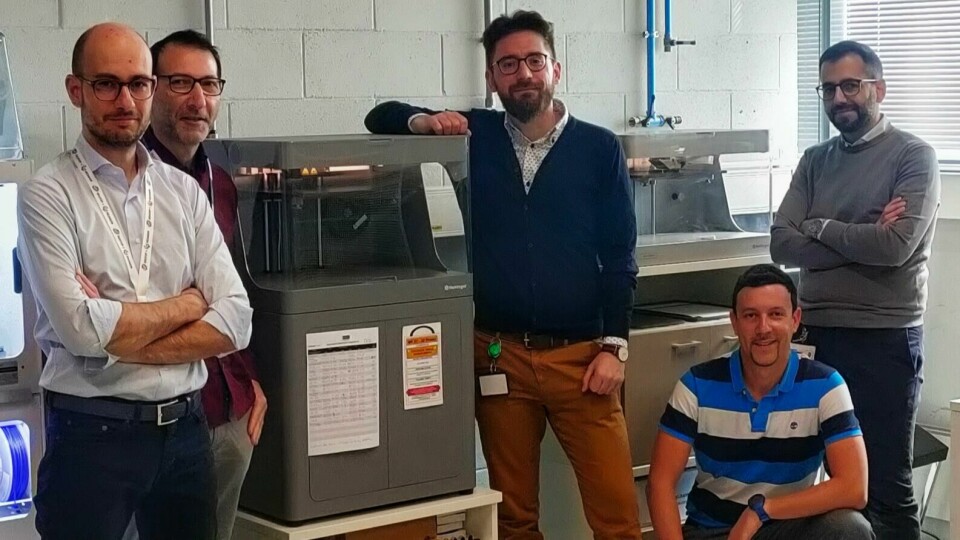
“There are so many applications for automotive where additive manufacturing is really the best choice. I think education is an important area where we need to see serious improvement. Getting people educated on when, and when not to use additive manufacturing, what materials to use and how to design is key.”
“I completely agree,” says Ametrano. “Education is very important because sometimes additive manufacturing is seen as the fast and easy method for everything - but not always as the best way. But you have to study and develop solutions to be effective with additive manufacturing technologies and methods.”
Dalgarno adds, “additive manufacturing is often perceived as just a tool for prototyping, but it has now become so much more than that. And in fact, many printers today are designed for industrial applications and use, with 24/7 operations to solve real-world problems and not only on the R&D side of things, but on factory floors. So, simply put, modern additive manufacturing platforms now make it simple to print reliable, functional parts for industrial use, right where they’re needed.”
“Yes,” says Marino. “We believe that in a period of uncertainty like this, with its swiftly mutating technological environment, it’s really important to explore new technologies and solutions to gain a competitive advantage, and we at Punch Torino are really committed to that in achieving our vision of sustainable mobility for all.”