Continental digitises European automotive manufacturing plant with a private 5G Network
Continental’s innovative private 5G network accelerates production, enhances efficiency, and transforms the digital factory landscape, addressing automotive industry challenges.
Continental has unveiled its first private 5G network at its display solutions plant in Brandýs nad Labem, Czechia. The move marks an important step towards a fully-realised digital smart factory and efficient, integrated production processes.
The private 5G network is powered by T-Mobile in Czechia. With plans to integrate over 1,000 devices and sensors within the plant’s expansive 5,000 sq.m, the company’s smart network promises to create an interconnected ecosystem that enables seamless communication between employees, machinery and devices such as sensors, production robots and autonomous transport vehicles.
The ecosystem is poised to enhance manufacturing processes; boosting efficiency and minimising downtime.
“With the introduction of a private 5G network at our location in Brandýs nad Labem in Czechia, we have now reached a significant milestone on the road to the digital factory.”
Thomas Ebenhöch, head of Operations in the User Experience business area at Continental Automotive, emphasised the importance of this milestone, saying: “The production of complex display solutions for vehicle cockpits requires innovative technologies already today. The challenges of manufacturing high-tech products of the highest quality and in large quantities will continue to grow in the future.
“In line with our megafactory strategy, we are therefore systematically focusing on state-of-the-art production. With the introduction of a private 5G network at our location in Brandýs nad Labem in Czechia, we have now reached a significant milestone on the road to the digital factory.”
5G production ecosystems: efficiencies across the board?
Continental’s private 5G network holds a wide array of potential benefits for automotive manufacturing. Enhanced connectivity results in speedy communication, facilitating real-time interactions between various production systems and giving employees greater flexibility. It also potentially enables remote collaboration and maintenance work with augmented reality (AR) capabilities. Such systems also open the doors for cross-plant collaboration, extending derived efficiencies beyond a single facility and eliminating manufacturing silos.
”As opportunities for integrations and enhancements grow, so does the threat potential.”
Automotive manufacturing has been marked by systems-integrations since Ford was established in the early 20th century; integrations which necessarily rely on data and information in optimising processes. The 5G network’s integration of over 1,000 sensors and devices has the added implication of generating a vast repository of data.
Continental plans to harness this data to further improve production processes as well as predict maintenance requirements to reduce downtime for production robots and production lines. Continental’s private 5G network represents an important step towards the realisation of the digital factory where innovation and connectivity converge to address the potential challenges of automotive manufacturing.
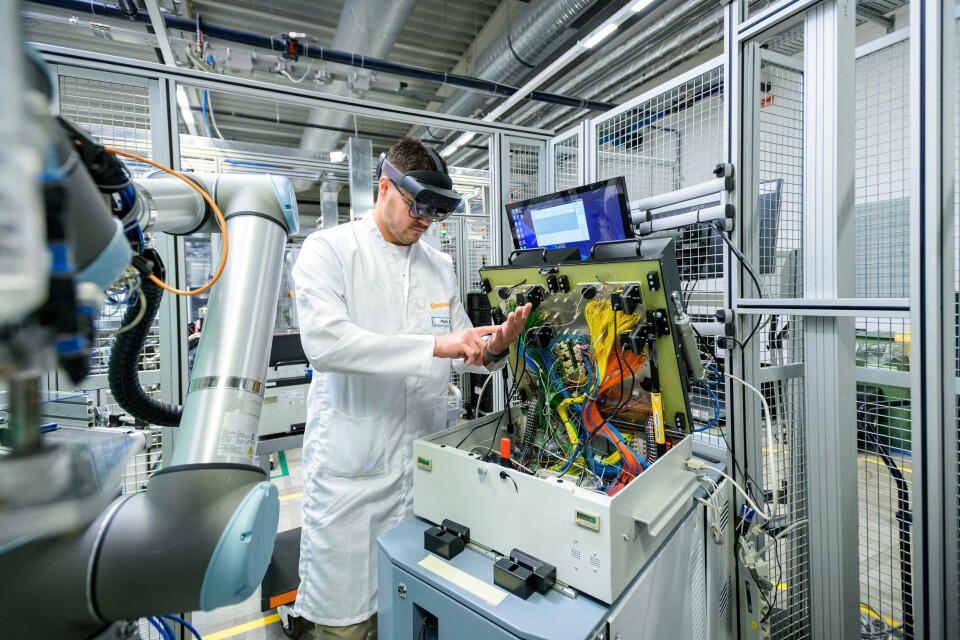
Opportunities and threats of 5G production plants
5G technologies are quickly taking hold of automotive manufacturing across diverse regions. Zeekr, for example, has an intelligent factory in Ningbo, China. Zhao Chunlin, vice president of Zeekr and plant manager at Ningbo, recently told AMS that as a factory exclusively manufacturing high-end pure electric intelligent vehicles, the Ningbo facility adopts digital design, digital process simulation and digital operations, and is a 5G fully connected factory that has been honoured as one of the first “Future Factories” in Zhejiang. So the development is not confined to the west.
But as opportunities for integrations and enhancements grow, so does the threat potential. Recently, Toyota’s production ground to a halt in Japan following a digital system failure. The issue was reported to be due to breakdown in a computer processing orders for vehicle parts and resulted in production at all 14 of the OEM’s Japanese assembly plants shutting down. The extent of production losses was not insignificant, with the affected plants collectively contributing to approximately one-third of Toyota’s global output.
Until now ‘disruptions’ have been associated with pandemic lockdowns and related supply chain interruptions, but as 5G technologies and digitisation permeates deeper into automotive production processes, the potential impediments are expanding the definition to encompass internal systems and technologies; and comprehensive solutions are still wanting.