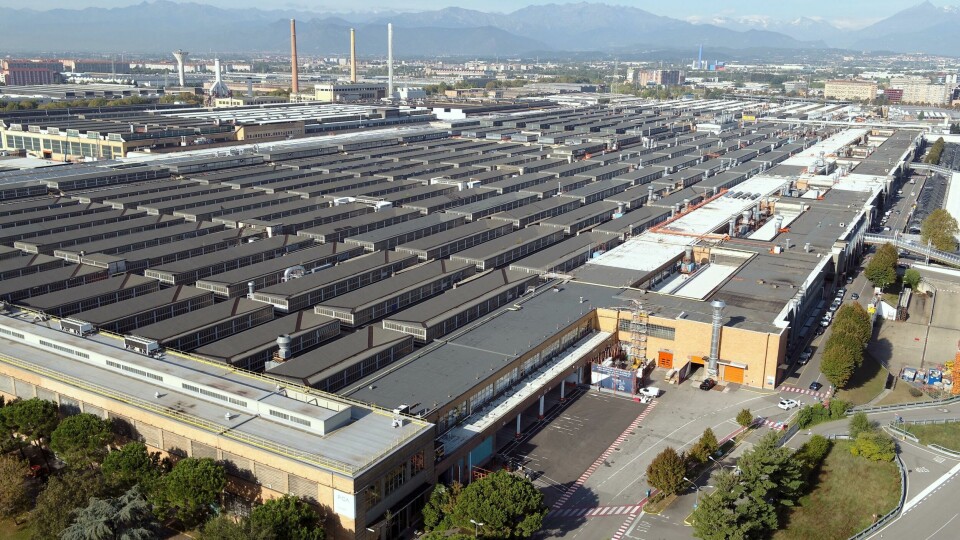
Adopting circular economy principles in car production
As the automotive industry looks at how to be more eco-friendly, car companies are taking various approaches to lower emissions across their manufacturing operations. Experts at Stellantis and Mazda speak about the implementation of circular economy principles in vehicle production
Decarbonising vehicles is one of the top priorities for countries looking to reach net-zero. EVs are widely considered as the best fix, but electrification alone and the elimination of tailpipe emissions may not necessarily result in an eco-friendly auto industry. According to figures from the International Energy Agency (IEA), the average CO2 emissions created during the production of battery electric vehicles is 5.4 tonnes.
Adoption of circular economy principles in manufacturing could help to lower this number significantly. “Electrification is not the sole answer to the decarbonisation challenge within the automotive sector,” confirms Natalia Dziergwa, circular cars initiative specialist at the World Economic Forum. “End-to-end value chain emissions need to be tackled and circularity is a key building block for a low-carbon mobility system. From a production perspective, material circularity and lifetime optimisation are important levers for this transition, from usage of low-carbon materials to product life extension through reuse, remanufacturing, and refurbishment.”

Design and remanufacturing
Car companies are taking various different approaches when it comes to lowering emissions across their manufacturing and production operations. Stellantis, for example, set up a new business unit in March 2022 that focuses entirely on circular economy principles with the goal of reducing the environmental impact of its factories around the world. This is part of the company’s plan to reach carbon net-zero by 2038.
“The principle of circular economy is to move from a ‘take-make-dispose’ approach with materials and products to a circular use of resources, extending their lifespan and making them last as long as possible, thereby reducing waste and the need for new raw materials. It changes our consumption model starting from the way we design our products,” explains Alison Jones, Stellantis senior vice president, Circular Economy Business Unit.
There are several ways of putting this into practice, Jones continues. Designing components using materials that are easy to disassemble, recover and recycle at the end of their first life in the vehicle is one example. Another is to recycle production scraps and return waste materials into the production loop. A third is the remanufacturing of defective parts.
Each of these approaches, says Jones, is critical to reduce the environmental impact of production. “Remanufactured parts have up to 80% less new material and up to 50% less CO2 emitted to produce, when compared to a new part, which is great for sustainability, affordability and customer choice,” she emphasises.
“Our remanufacturing activities are implemented in Europe as well as North and South America, and we will continue to expand them. We repair parts that have been removed from a customer’s vehicle, like electronics, gearboxes and traction batteries, and we recondition vehicles.
“We have various locations and partners that collect material for recycling, including scraps from our own factories and material from end-of-life vehicles. These vehicles are also a source of product for our reuse ecommerce platform, B-Parts, that enables parts still in good condition to be sold to customers directly and reused in their vehicles.”
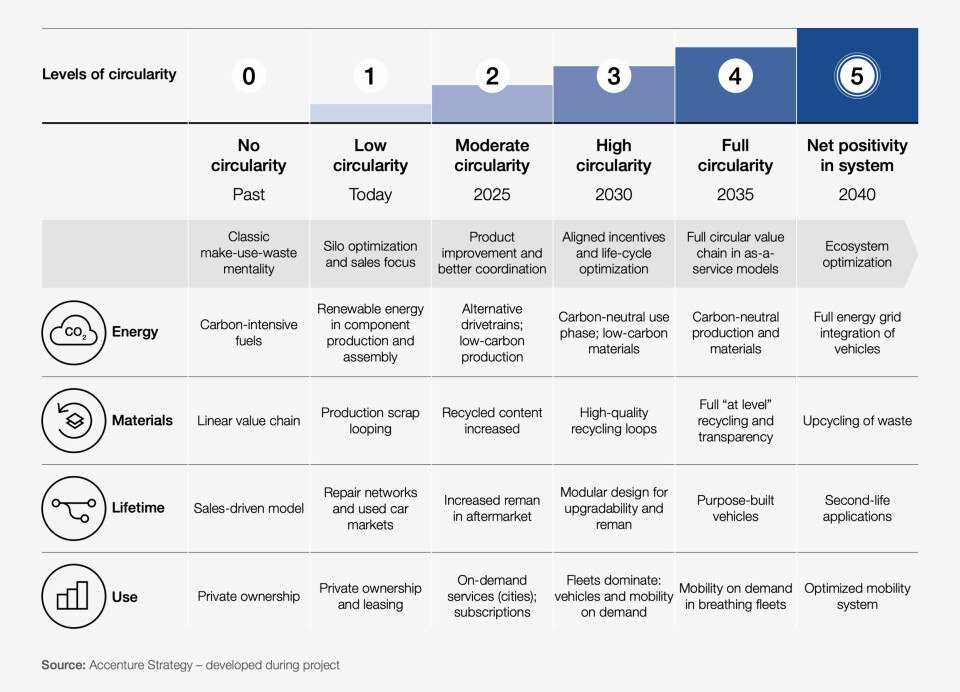
Achieving carbon neutrality
Mazda also has lofty plans to reduce its environmental footprint, albeit in a different time frame. The carmaker aims to ensure all its production facilities are carbon neutral by 2035, with the wider goal of achieving carbon neutrality across its entire business by 2050. It is initially targeting three areas: energy conservation, the shift to renewable energy, and the introduction of carbon-neutral fuels for in-house transportation.
The OEM is also examining the benefits of implementing circular economy principles within its production operations. “Mazda sees it as the core responsibility of all automotive manufacturers to do their part in curbing global warming and other issues related to climate change by reducing CO2 emissions in every step of vehicle production, including manufacturing, transport, vehicle usage and recycling,” a company spokesperson told AMS. “We promote initiatives for resource recycling based on the three Rs: reduce, reuse and recycle.”
Like Stellantis, Mazda sees design as one of the key focal points. “We are incorporating the three Rs into under development to increase their recyclability,” the spokesperson continues.
“This includes researching vehicle design and technologies that simplify dismantling and separation to make recyclable parts and materials easier to remove, and the use of easily recyclable plastics. It is also important to point out that Mazda has been proactively developing plant-derived biomaterials which have the potential to help reduce environmental impact by curbing the use of fossil fuels and CO2 emissions.”
Looping the EVs
Mazda is involved in the Carbon Circular Economy Promotion Council – an organisation that was established by Hiroshima Prefecture back in 2021 to promote CO2 reduction and recycling. Discussions within the council are currently centred upon addressing some of the issues and challenges that surround the adoption of circular economy principles in production.
One of the key challenges is the degradation of parts and materials, particularly when considering EVs. Estimates vary based on the materials and production methods used, but according to the Massachusetts Institute of Technology (MIT), emissions created during the production of the 80kWh lithium-ion battery found in a Tesla Model 3, for example, could range between 2400kg (almost two and a half metric tons) and 16,000kg (16 metric tons).
Furthermore, the rare earth metals used in batteries, like cobalt, are sourced in enormous mines that destroy local habitats and are often linked to child labour, inhumane working conditions and conflict.
Reusing batteries must be a top priority, but as capacity and efficiency worsens with age and use, second life batteries will not meet performance standards for cars and will instead be used in other applications like energy storage and power generation. This is not just a battery problem, and as Jones explains, the potential for material degradation means that circular economy production will require skilled labour forces.
“The automation for production of circular economy parts can be hard to achieve because the material we start with can come in various different states,” Jones admits. “It means the process of sorting and grading is a skill that relies heavily on expert team members. In vehicle production, the main challenge is sourcing the recycled materials in the quantities and ranges of material that are needed to run a production line, and so we work with our suppliers on their technical innovations to do this.”
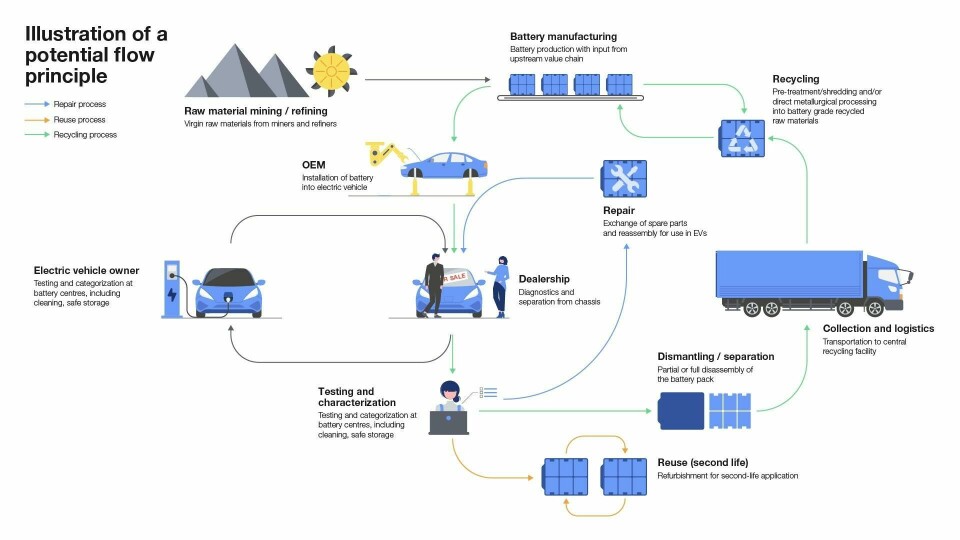
Covering every base
Stellantis has big plans for its circular economy business unit. The company recently announced that it will create a ‘Circular Economy Hub’ at the Mirafiori complex in Italy. As Jones explains, the hub will essentially house various activities under one roof to ensure consistency and clarification.
“It will have skilled team members who are driving towards the future, and will host parts remanufacturing, vehicle reconditioning, and vehicle dismantling activities to start,” she clarifies. “The idea is to further expand further in each field, and to roll out these ideas globally. The knowledge we develop here will support us as we design new vehicles for circular economy, always looking to extend the life of our vehicles and parts, and then when they get to the end of their life, making it easy to bring that material back into our material loop to be used on future vehicles and parts.”
But it’s not just the materials and parts of the vehicles that are being considered. Jones also argues that the tools and machines used to create the cars must also be part of the circular economy model. “We must apply the same principle of reuse to our process tools, with a shared database in which plants can manage transfers of tools or robots considering the availabilities and needs in the different sites,” she states. “Many of our plants have developed the skills to transform and adapt robots for reuse.”
At Mazda, examination of new technologies and measures to move its recycling programme forward are on the table. The company currently processes and recycles three items: automobile shredder residue (ASR), chlorofluorocarbons, and airbags, which require specialist knowledge for disposal. “In the case of ASR, Mazda is working through ART – a consortium of 13 key companies – to comply with Japanese law and achieve progress in the reuse of resources.
The company also appropriately executes recycling at dealerships, collecting vehicle recycling fees at the time of sale and receiving the end-of-life vehicles from their final owners in order to transfer them to the disposal processing companies. Mazda is committed to collecting lithium-ion batteries installed in vehicles launched in and after October 2012 through the LiB Joint Collection System of Japan Auto Recycling Partnership. Last but not least, useful metal is recycled in cooperation with metal recycling related companies such as dismantlers, crushing and shredding contractors, and steel manufacturers.”
A team sport
It is clear that a holistic approach must be considered to adopt circular economy principles. No stone must be left unturned, and as carmakers like Stellantis and Mazda look forward and attempt to cut carbon, circular economy principles will be crucial if they are to achieve their goals. Dziergwa agrees, and also points to the importance of collaboration.
“Circular economy is a team sport,” she suggests. “For a truly circular vehicle production, circularity principles need to not only be applied on the factory floor but also across the entire value chain all the way from sourcing through to parts and materials recollection. No single player can achieve that on their own, so strong industry-wide collaborative efforts will be required to win the game.”