Audi’s Brussels revolutionises sustainability with freshwater reduction initiative
To reduce waste and energy consumption paintshops are deploying a range of strategies, innovative processes and materials to meet new sustainability targets. Report by Mike Farish
In March this year the Audi manufacturing site in Brussels initiated a project that aims to reduce the use of freshwater at the plant including all that used in its paintshop operations by as much as 100,000m3 per year. That was when the plant started reusing water in a continuous closed loop cycle, in which it is repeatedly treated off-site and then returned to be used again.
The project is a public-private cooperative venture with the Brussels-Capital Region and Belgian company Hydria, which manages the Brussels South wastewater treatment plant that is located close by the Audi site.
Getting serious about wastewater
The venture is more extensive than just paintshop operations. An Audi spokesman confirms that “the re-use water is used in all production processes in the whole factory including not just the paint shop, but also the bodyshop, assembly line and battery assembly operations.”
The re-use water is known more generically as ‘grey water’, but the company says that the term denotes no more than that it has been through the recycling process and that it is no less fit-for-purpose in factory floor operations than fresh water of drinking quality. “For ‘grey water’ we use the term ‘re-use’ water, which simply means that we do not use drinking water but recycled water,” the company states.
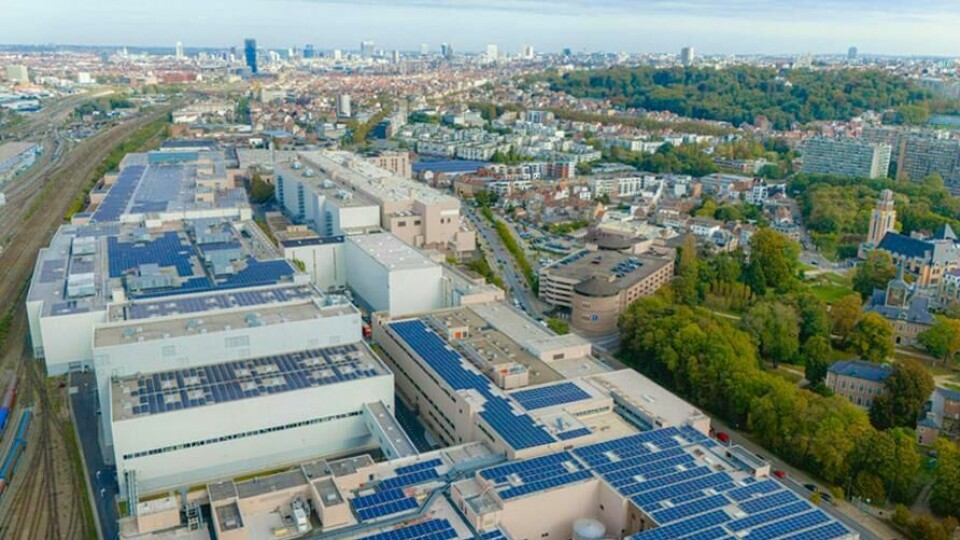
But the company is clear that the water returned to the plant from the Hydria site in no way compromises the efficiency or quality of any of the processes in which it is used.
The Audi Brussels plant is not, however, the first of the company’s manufacturing sites to initiate a closed cycle water re-use project. “The plant in Brussels is one of several plants to have such an operation, but not the only one,” the company states. “Water is also reused at Ingolstadt, and Neckarsulm will introduce a closed water cycle before the end 2024.”
Audi notes, that the Brussels plant is one of its own leaders in terms of sustainability. “The plant in Brussels has been using renewable energy since 2018, making it the world’s first certified carbon-neutral large-scale production facility in the premium segment,” the company states.
Moreover, a further implementation of the approach can be found on the other side of the Atlantic. “Another example of closed water cycles can be found in Mexico, where well water is treated using ultrafiltration and reverse osmosis systems to produce both process (re-use water) and drinking water,” the company confirms.
In the case of the Brussels plant, Audi indicates that the operating cycle involves the removal of several contaminants from the water before it is returned to the plant for re-use. “Operations at Hydria are basically designed to remove organic matters, suspended solids, nitrogen and phosphorus,” the company states.
But the company adds that the water also undergoes a slightly more extensive treatment process than might otherwise be the case to make it suitable for use inside the car plant. “For Audi re-use water the treatment has been reinforced with reverse osmosis in order to be able to have a purer water required for Audi processes,” it explains.
Once they have been removed from the water at the treatment plant the contaminants involved take one or other of two forms. “It depends on the type of compounds, but the main part of pollution is removed in the form of sludge,” the company says adding that waste in that form would in any case be the main output of the wastewater treatment plant. But it adds that a part is removed as a gas like ammonia and that some organic matters are transformed into biogas.
Nevertheless, the overall cycle time from when the water leaves the Audi plant to when it is returned for further use is less than a day. “The retention time of the water in the wastewater treatment plant is approximately 18 hours,” the company states. “But the water is continuously available.”
The actual amount of water involved in the process seems surprisingly small. The company state that the total volume is “approximately 1,000m³ including all water in the tank and pipelines”. But as it further elaborates on the figures it becomes evident that the overall process is highly efficient and that the scale of re-use is extremely intensive. “The process is technically ‘unlimited’, but there will always be a little evaporation,” the company states. “This means that while the cycle is not 100 percent closed, it nevertheless is to a very large extent.”
As such the actual amount fresh water that is saved over the course of a year is many times the amount of water in the system. “The figure is approximately 100,000m³ of drinking water,” the company confirms.
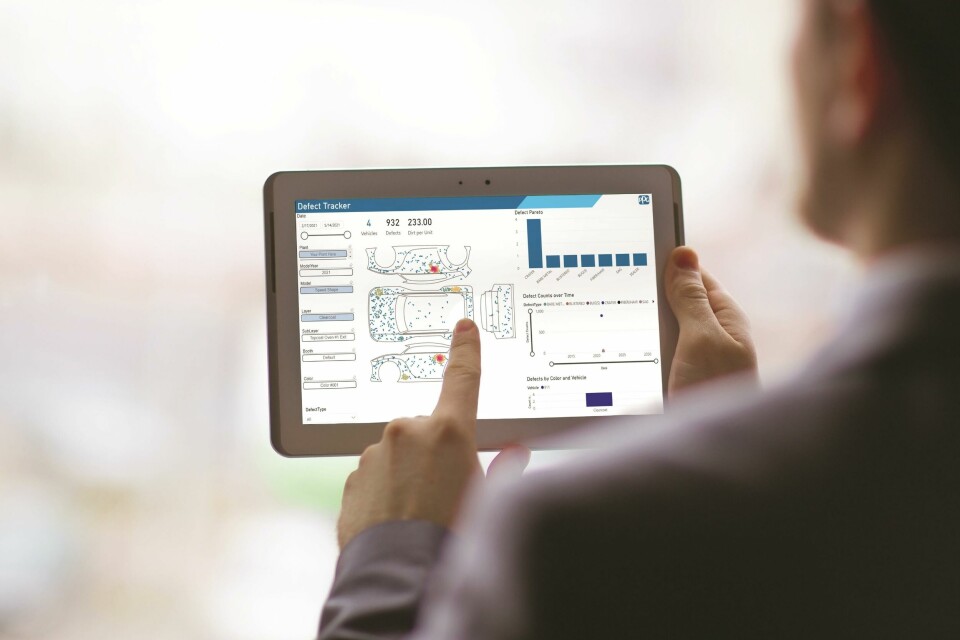
Managing data to reduce waste and energy consumption
While the physical aspects of automotive paintshops – energy intensity and use of multiple types of coating materials – are self-evident a less immediately visible factor is also vital. As Anne Sybil Bragadir points out, “the ability to capture and rapidly analyse data is the foundation for all sound decision making in manufacturing, and paintshops are no different to any other type of operation in that respect.”
Bragadir is Optima Solutions global business development director with US-based automotive painting systems supplier PPG. She notes that paintshops tend to be different from each other. “Every paintshop is different in practice with the variables including age, equipment and processes,” she states.
PPG has developed a digital toolset to support paintshop-related quality and decision-making consisting of cloud-based software packaged as a series of modules including Defect, Color+, Electrocoat and Mix Room Management. Bragadir note these modules aim “to draw correlations between different areas of the paint shop and between OEMs and their tier suppliers.”
A complicating factor is that even where the energy intensity of a process can be mitigated there may be repercussion elsewhere. Bragadir’s colleague Steven Phillips, global digital application manager at PPG, offers the example of turning down the temperature in bake ovens in between shifts, something he notes that can have implications for product quality if correct temperatures are not restored on time.
“Finding the balance between quality and sustainability is where one of the challenges is,” Phillips states.
“Very often if companies don’t do something that seems self-evidently sensible it may be because in the past, they have had an issue with it. Quite simply if you turn something down you might have a hard time turning it back up.”
A key enabler is therefore going to be the availability of data that is accurate immediately and continuously. Bragadir confirms that the company is now completing the final testing and will shortly be launching AiM Automate, a system which automates electrocoat bath controls by continuously measuring and collecting key data readings using sensors and converting these readings through proprietary algorithms to key measures used every day thereby limiting the need for manual testing.
Biomass balancing to manage materials usage
Meanwhile paint supplier BASF has been promoting a concept it terms the ‘biomass balance’ approach for the last two years. As Dr. Markus Piepenbrink, head of global sustainability, BASF Coatings, explains, it prioritises the use of “recycled or renewable raw materials as alternatives to fossil resources at the beginning of its value chain”. He stresses, though, that “while mass-balanced products keep all product properties unchanged compared to their conventional equivalents, they contribute to the substitution of fossil resources in our production process and may have a smaller product carbon footprint than their conventional equivalent.”
The core elements of that production process are, Dr Piepenbrink explains, “two steam crackers plus synthesis gas and the acrylic acid plants”. He explains that in the steam cracker, steam is used to split or ‘crack’ naphtha, a long-chain hydrocarbon, into smaller molecules, which then serve as the building blocks for downstream production. These include, for example, hydrogen, methane, ethylene and propylene, which are processed into various products including not just coatings, but also plastic and solvents.
Dr Piepenbrink says that renewable raw materials like bio-based naphtha and biomethane from organic waste are used when manufacturing primary chemical products. “By feeding alternative raw materials into the production chain alongside fossil raw materials at an early stage, the end products remain chemically unchanged,” he confirms. “As such products that are certified as biomass-balanced offer the same performance and quality as conventional products, with the added benefit of a lower carbon footprint and a contribution to waste recycling.”
The approach is now in the mainstream of BASF’s portfolio with the company offering some 1,500 relevantly certified products according to global sustainability manager Dennis Dropmann. “In the automotive OEM coatings sector, we provide a certified version of our e-coat technology CathoGuard 800 ReSource, our scratch resistant clearcoat iGloss matt ReSource as well as several basecoats in close collaboration with our customers,” he confirms. “Using more sustainable product versions for automotive coatings enables CO2 avoidance of around 40% per coating layer.”
The automotive launch customer for BASF biomass balance products was BMW Group, which chose to use BASF Coatings’ CathoGuard 800 ReSource e-coat at its plants in Leipzig, Germany, and Rosslyn, South Africa, and the iGloss matt ReSource clearcoat throughout Europe. The car maker is targeting a reduction in the amount of CO2 emitted in the plants by more than 15,000 metric tons by 2030 as a result of the move.
BMW using biomass paints
At the time BMW made a point of stressing that it would be the “first automotive manufacturer worldwide to use matt paints made from biomass instead of crude oil.” In addition, the car maker stated that the Leipzig and Rosslyn plants were also using sustainably produced corrosion protection.
Since then, BMW has not divulged any further detailed information about its use of this type of material. Right now, though, it will state that: “Biomass Balance paint is currently available in our European paint shops and only for matt paint. In addition, electrodeposition paint (KTL) was converted to the process at the Leipzig and Rosslyn plants. We are testing the use in other BMW Group plants.”
Elsewhere BASF says that an automotive customer in China has started to use the ColorBrite Airspace Blue ReSource basecoat which it claims enables reduction of around 20% in product carbon footprint. Furthermore, relevant product manufacture is also now taking place there with BASF having received biomass certification for its resins plant in Caojing, as well as its paint manufacturing sites in Minhang and Caojing operated by BASF Shanghai Coatings.
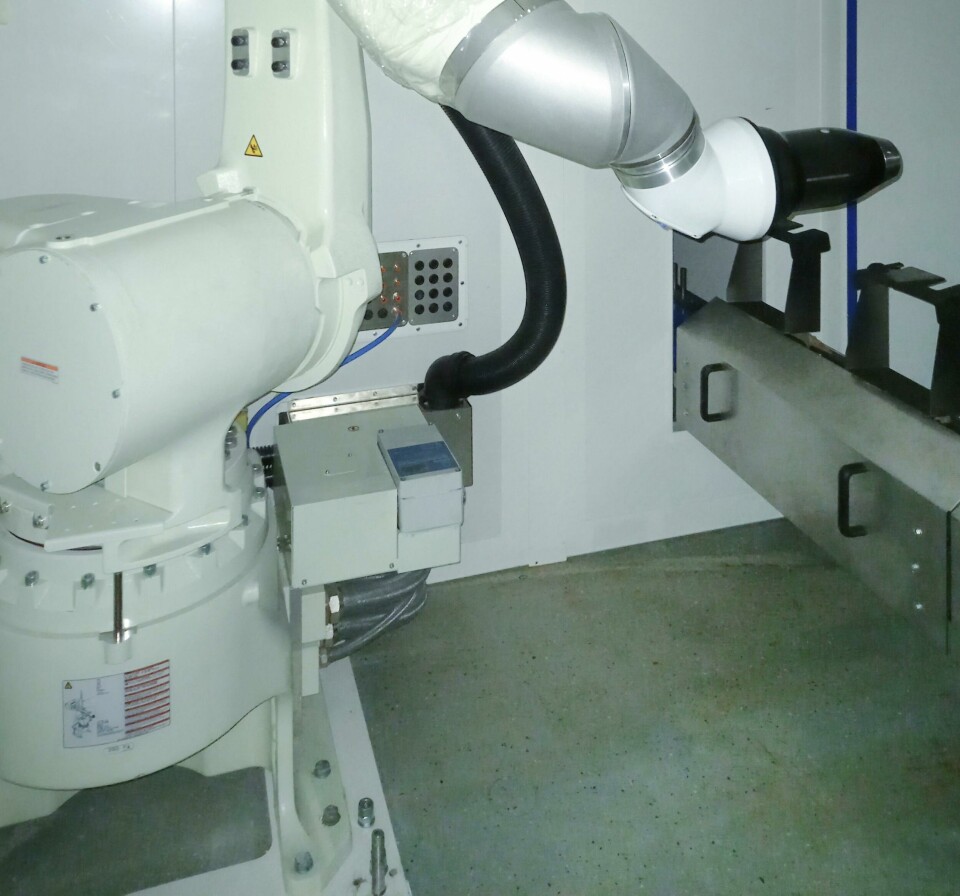
Improving paint transfer efficiency
Application hardware rather than chemical composition is the key to a sustainability-related initiative on the part of automotive component supplier Valeo, which has adopted the use of high-speed rotary atomiser spray gun technology for the first time at its plant in Hungary. Specifically, it is using Dürr’s Ecobell devices mounted on a Kawasaki robot to paint plastic interiors for electric vehicles in a move whose benefits are expected to include a significant reduction in paint loss and rinsing agent consumption compared with conventional spray gun counterpart technology.
The advantages of rotary atomiser technology are explained by Sebastien Pellissier, sales manager industrial products with Dürr Systems France. “Rotary atomisers offer better transfer efficiency with the rotation enabling more targeted application of the paint to the workpiece,” he states. “This reduces overspray and therefore paint consumption. At the same time, energy can be saved in the paint booth, because the air flowrate in the paint booth is reduced to 0.30m/s instead of 0.50m/s with conventional spray guns.”
Pellissier adds that the spray cone generated by a rotary atomiser leads to a higher area performance, as fewer coating paths are required to paint the workpiece. “This results in higher productivity, while the diminished overspray makes it possible to reduce the air sink rate which saves energy costs,” he states.
The specific configuration at Valeo is reported by Pellissier to be “an EcoPump AD package, a fluid board, a two-component mixing and dosing system and the EcoBell high-speed rotary atomiser without high tension”. He says that specific features of this set-up that enhance both efficiency and sustainability include reduction of the paint mix volume due to the location of the mixer in the robot arm and the fact that only one control is required for both mixing and application. “It is important to understand that we can also use the bell with a non-conductive substrate,” he adds”. “Another advantage of painting plastic parts without high tension is that the parts do not have to be specially grounded or previously coated with a conductive primer.”