Aluminium applications
Electric vehicles battery enclosures are increasing overall vehicle weight, with lightweight materials for structural components, such as castings, can offset the rise. Rio Tinto’s Jerome Fourmann tells Nick Holt about new opportunities and production innovations
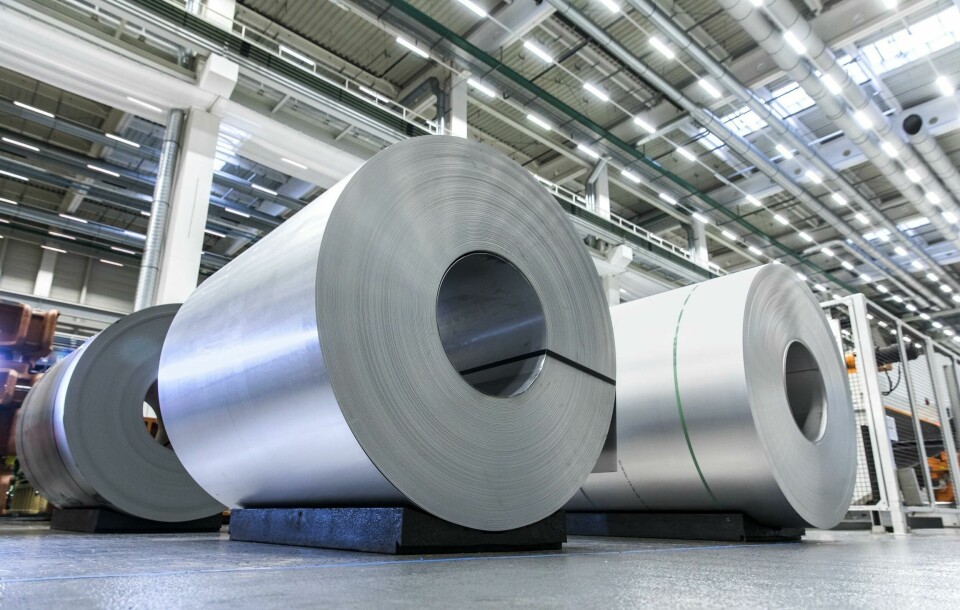
Jerome Fourmann is director of technical marketing – global customer support and product development for the mining and materials giant Rio Tinto. He is also an active member of the Aluminium Association Transportation Group (ATG), an association dedicated to increasing the use of aluminium in light weight vehicles. Along with Rio Tinto, members include Commonwealth Rolled Products, Constellium, Hydro, Kaiser Aluminum and Novelis.
Have new battery electric vehicle (BEV) architectures provided more opportunities for the application of aluminium cast parts?
Yes, absolutely, but it is helpful to put this into some context. The DuckerFrontier Study that was published last year reported that the aluminium content per vehicle continues to grow, and the forecast for the foreseeable future is the same. Taking North America as an example, since 2016 there has been an increase in terms of aluminium content of 62lbs (28kg) per vehicle, with 2020 reaching a total vehicle content figure of 459lbs (208kg), and that is primarily driven by the shift toward the light truck and battery electric vehicles. The expectation by 2026 is for 550lbs (250kg) of aluminium content per vehicle in light duty trucks.
This increase is seen primarily in three main areas of material usage: aluminium auto body sheet, castings and extrusions. A good example of this Tesla’s Model-S BEV, which uses over 800lbs (360kg) of aluminium for structural components, castings, extrusions, and the whole body of the vehicle.
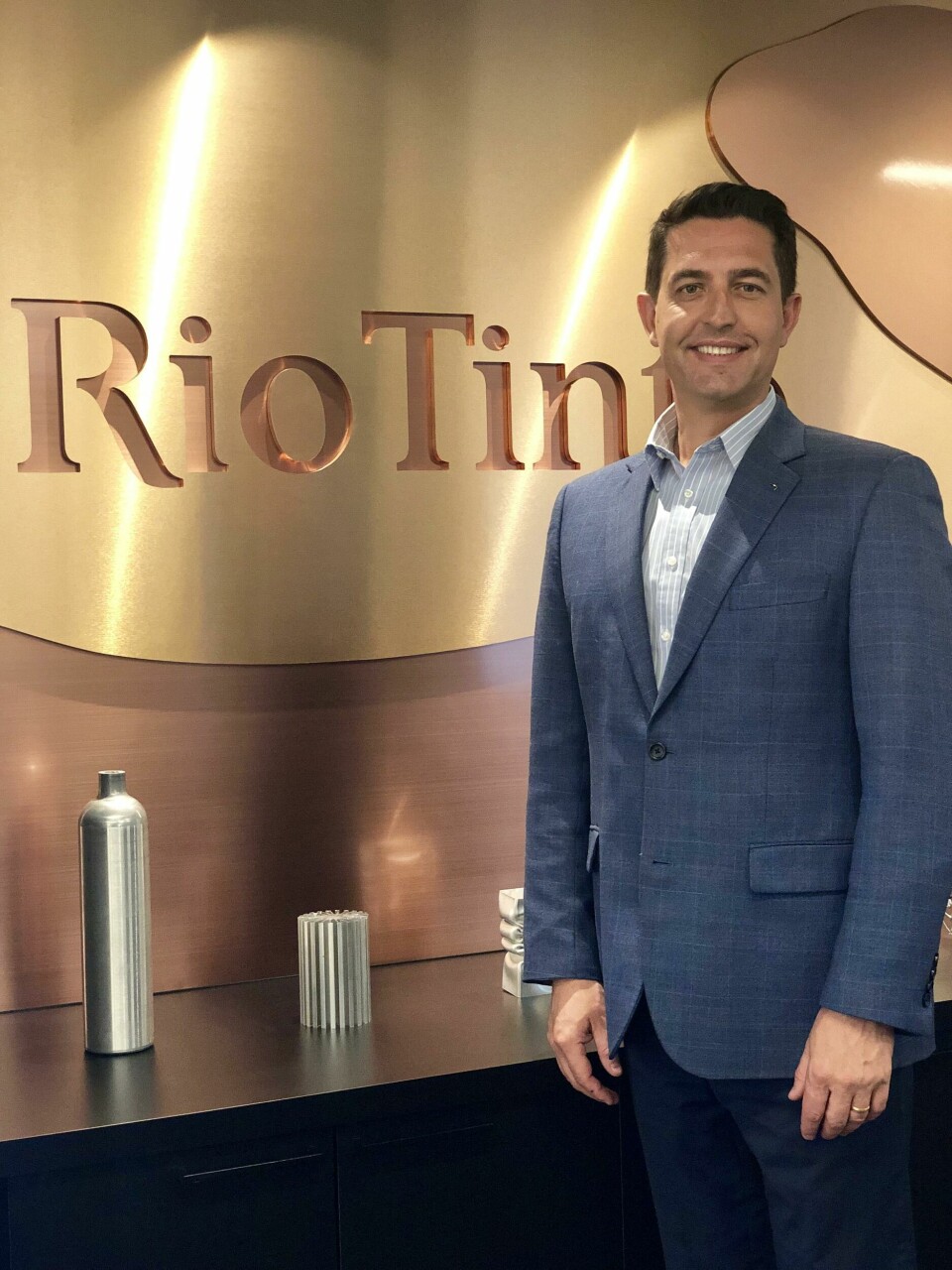
If we look specifically into castings, starting with the powertrain, there is a decline here in terms of weight of castings per vehicle, mostly due to downsizing in terms of engine size. However, if you look at the overall casting content per vehicle, including structural castings, in 2016 we had about 287lbs. By 2026 this is predicted to increase by about 10%. So, you’ve got more usage of castings per vehicle and those castings are mostly the structural die-castings that offer a lot of benefits.
There has been a lot of development around offsetting the weight of EV batteries and creating lightweight, functional enclosures. What part has aluminium played in this area of the vehicle structure?
Very simply, the battery adds weight, typically in the range of about 800lbs to about 1,300lbs. So, the use of aluminium castings, particularly here, is a key enabler to offset that extra weight.
A good example of the use of castings in a BEV is the Audi e-tron. Here you have a very strong enclosure frame, which integrates a sophisticated crash structure.
Taking the aluminium featured on this vehicle as an example, 47% is extrusions, 36% auto body sheet and 17% die-cast parts. These cast parts or nodes, connect the battery pack to the vehicle structure on each corner and these are specifically designed through development of the alloy and the casting process, to absorb energy in case of a crash.
“If you look at the overall casting content per vehicle, including structural castings, in 2016 we had about 287lbs. By 2026 this is predicted to increase by about 10%.” Jerome Fourmann, Rio Tinto
We see aluminium castings being used in smaller sub-frame areas and suspension parts, but Tesla is developing the use of much larger cast components to reduce the parts content and cost. Can you talk a bit about those enablers that have brought this technology around?
Aluminium castings produced using high integrity die-casting process have been around since the early 2000s. They are thin walled (about 1.8-2.5mm in thickness) and offer excellent mechanical properties combining ductility, strength and are well suited for various joining techniques (welding, adhesive, riveting). One of the benefits of die-casting is the ability to combine a specific alloy aiming a certain range of mechanical properties reach with or without heat treatments allowing the part to be geared for strength or more towards ductility, or a combination of both as required by the performance characteristics of the part.
If you look at the large cast parts Tesla is using, you have one single large aluminium part – I’ve heard the ratio is 70:1 – so you have one part, one casting, that can replace up to about 70 components. That saves weight, assembly time and cost. That translates a lot into reducing the factory footprint since you do not need the same number of robots to assemble 70 components together – you have one part and fewer processes.
This is the future for the use of aluminium castings; large ones that allow us to reduce the number of components and increase the integrity of different features.
A key enabler has been the development of high-integrity die-casting in the early 2000s. Before this, traditional die-castings were not typically used for structural components because they were more porous and didn’t offer high ductility for crash management.
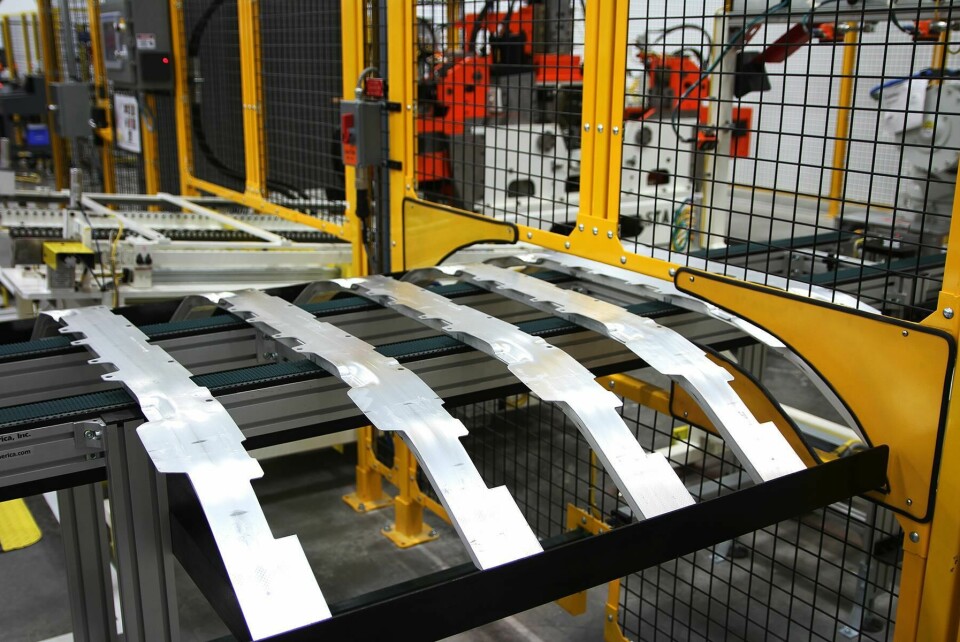
High-pressure vacuum die-casting is the technology that is now used to produce structural, high integrity die-cast parts. The three key enablers were the development of specific alloys that offer the castability, mechanical properties and ductility, the development of the vacuum process itself and the heat treatment of those castings. To reach high strength or high ductility characteristics, there are specific heat treatments that must be applied.
Once the alloys were developed, the vacuum was fully controlled and the heat treatments well understood, there was then an increase in use of aluminium high integrity castings in vehicle assemblies.
Another important factor in the use of these structural castings has been lowering costs. With modern industrial processes, there is no place for trial and error, and looking at castings in particular, the industry has drastically optimised its processes. Some material suppliers are offering material cards, let’s say for a specific alloy of a specific thickness. These are used to simulate production processes with the chosen alloy, for example joining using self-piercing rivets (SPRs). You’ve got thousands of possible options between the rivet itself and the die underneath. There are thousands of combinations. So, structural engineers can use those cards in order to simulate the die and rivet selection.
Data gathering, and the use of AI has enabled more accurate simulation of production processes and material performance. Has this been a factor in the wider use of structural castings?
Yes, artificial intelligence is supporting the casting industry. Why is it suitable? Because it is a repeatable process. High-pressure vacuum die-casting is a very consistent process – it is very controlled and closely monitored, from temperature to injection speed to mould temperatures, so the use of modern technology like artificial intelligence is very well suited in that aspect.
Aluminium alloy suppliers provide a very tight range of chemical compositions to foundries making those kinds of parts, because they need to have as few variations as possible. So, the alloy composition must be consistent and repeatable in order to reach the properties target for the components.
It is also the same with alloy development. If you look at structural castings, for example, the alloys that have been developed in the early 2000s are still in use today. They’ve been of course enhanced since, many variants have been developed and the characterisation of the material has been improved over the years. I am talking about the material cards, the optimisation of heat treatments when required. Things of that nature.
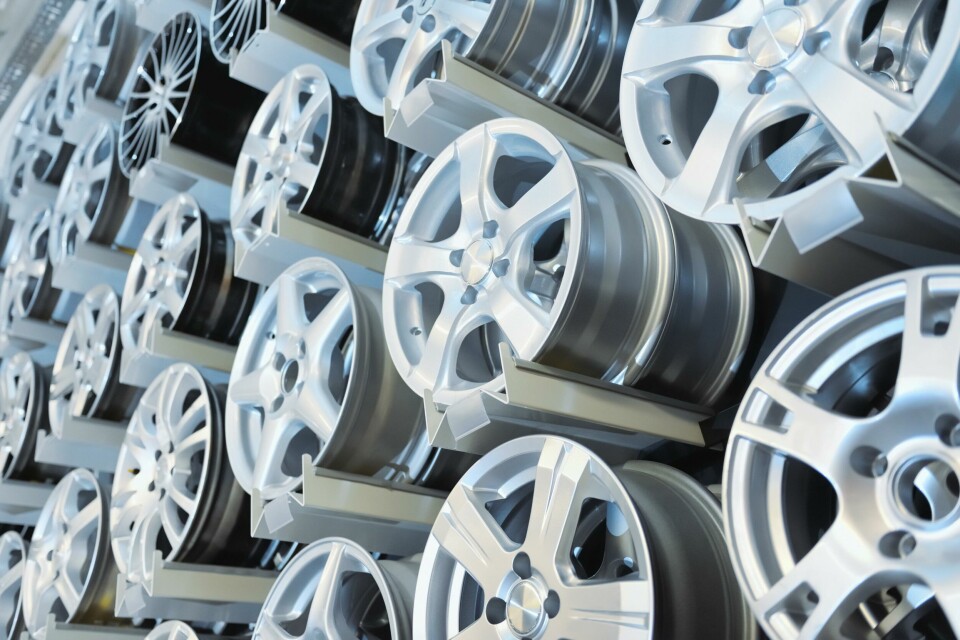
An example of this development can be seen in EV motors. For the rotor in this application, the OEMs are looking for an alloy with high electrical connectivity combined with high strength so they can enhance the torque of the vehicle. This is one of the most recent alloy developments. Alloys that offer about 50% IACS [international annealed copper standard] – that is the electrical conductivity – and more than 180MPa [megapascals] yield strength.
Also in very high demand from OEMs is the need to avoid heat treating the castings. Again, there have been a lot of improvements of the casting process combined with alloys developments and there are some existing solutions today that eliminate the need to do the full heat treatment of castings. This is important for two reasons: to reduce cost and to maintain high dimensional tolerances of the castings, which is a must for vehicle assembly.
Another recent technology development is the semi-solid casting process that is typically called rheocasting. It allows the production of low-cost aluminium components with high strength, very low porosity and it allows a broad range of non-conventional alloys to be used. Exceptionally thin wall part and giant castings can be made using this process.
With this process the viscous aluminium is introduced into the mould at a very specific temperature and high pressure, which allows the injection pressure to decrease. Once the slurry of metal is made, it is injected into the mould and there is no need to change the equipment and larger casting can be made using existing casting equipment.
High-pressure vacuum die-casting is very controlled and closely monitored, from temperature to injection speed to mould temperatures, so the use of modern technology like artificial intelligence is very well suited -Jerome Fourmann, Rio Tinto
Sustainability is an important factor in the choice of materials for carmakers. How does this feature in the development of aluminium alloys and production processes?
It is a priority to achieve the carbon footprint target committed by most carmakers. When we talk about new alloys, it includes the development of alloys containing recycled content or that allows recycled content. So, within the next five years there will be an increase of scrap aluminium recovered from existing vehicles. The challenge is how to reuse those different alloys used on the vehicle when it is all crushed together. What are the alloys that are going to be developed using end-of-life scrap?
In the foundries, waste aluminium is continuously recycled. If you look at a structural casting, to make one finished part it takes double the amount of metal, but the leftover materials (the flashings, etc.) all go back into the foundry process in a closed-loop recycling system. A primary focus for our industry is to really look at providing low carbon footprint aluminium. A lot of effort is put into the use of 100% renewable hydropower, for instance, to make primary aluminium.