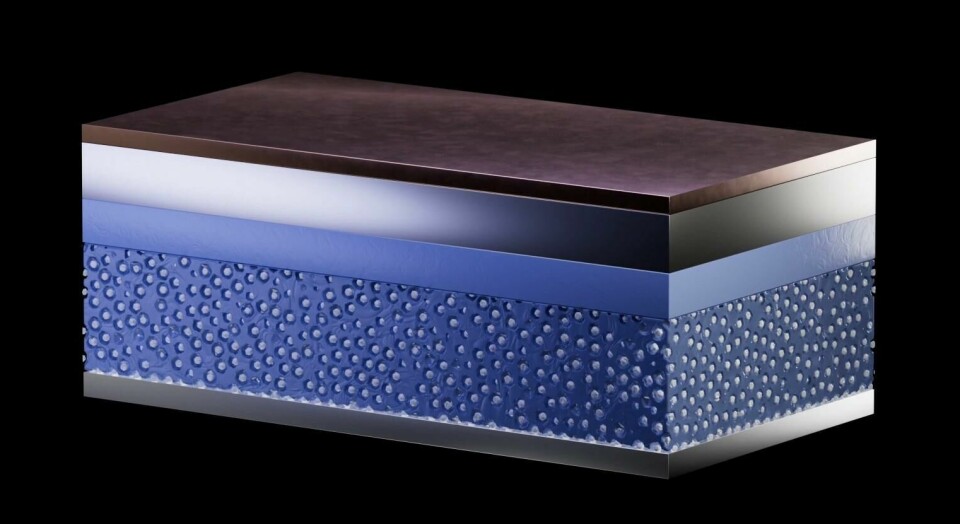
Next steps towards solid-state
Solid-state batteries are seen as the next big technology step for electric vehicles, potentially reducing battery pack weight and offering improved energy density and range. AMS reports on progress at Solid Power.
The core technology for BMW’s projected use of solid-state batteries to power new generations of electric vehicles (EVs) is provided by US company Solid Power based in Louisville just outside Boulder, Colorado, which was spun out from the University of Colorado Boulder back in 2011.
The company describes its all-solid-state battery (ASSB) technology as combining a mix of innovative chemistry with established manufacturing procedures to help produce benefits that include permitting the use of higher capacity electrodes and pack level cost-savings of 15-35% compared with existing lithium-ion counterparts.
The first of those factors is represented by its implementation of sulphide-based solid electrolytes that obviate the requirement for a flammable liquid electrolyte and polymer separator layer. This single layer then acts as both a barrier between the anode and cathode and as a conductive electrolyte. The second is that the cell manufacturing processes it has developed are based on those that are already well-established for existing high-volume lithium-ion battery cell production.

Using sulphide materials
Details of the company’s exploitation of sulphide materials are confirmed by CEO John Van Scoter. “We chose sulphides as opposed to oxides or polymers for our electrolyte because they have a superior combination of ionic conductivity and manufacturability, which should allow us to develop technologies that will increase driving range and battery life at lower production costs than conventional lithium-ion,” he states. “There are many proprietary inputs and unique processes which go into the production of our electrolytes,” he continues. “To our knowledge, we are the only publicly traded company developing true solid-state batteries in which 100% of liquids and gels are removed from the cells.”
Van Scoter also stresses that this innovative chemistry is achieved by means of commonplace materials. “Our electrolyte is made from abundant materials produced at industrial scale in multiple geographic locations, except for the lithium sulphide (Li2S) precursor material,” he states. “We currently source Li2S from leading lithium and chemical companies globally and are also developing our own Li2S production method to further hedge supply risk.”
In fact, Van Scoter further confirms the company has been engaged in exploratory manufacturing operations for some time. “We have been producing both electrolyte and prototype battery cells for several years,” he says. “Furthermore, over the past 18 months we have made large operational investments that are now enabling us to produce our electrolyte at higher volumes as well as larger, more complex EV cells.”
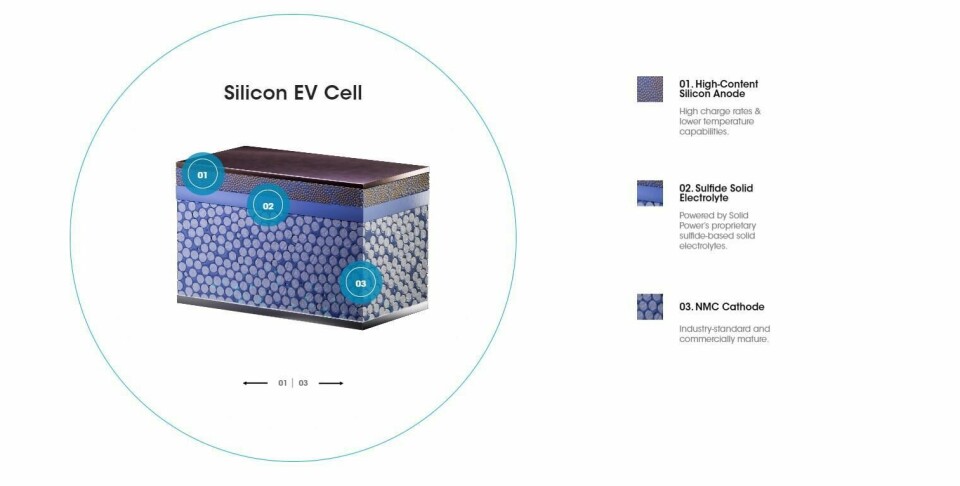
Developing production for commercialisation
Van Scoter provides more relevant details. “Our new SP2 electrolyte production facility, which is in Louisville, started production in April 2023 and is designed to produce up to 30 metric tons of electrolyte per year, a production level that will meet both our needs and the needs of our customers until we get to larger scale commercialisation,” he says. “We also have two working cell manufacturing lines at our SP1 facility in Thornton, north of Denver: a prototype line for up to 20Ah cells and our EV line, which allows us to produce larger cells between 60 and 100Ah. The EV line is designed to produce cells for automotive qualification and is currently producing cells to be delivered before the end of this year for BMW’s demo car.”
But Solid Power does not design or assemble the battery packs and modules – that is up to its automotive partners. Instead, the company aims to work closely with them on pack level requirements and vehicle integration to ensure cell operation accords with specifications. Apart from BMW, one automotive manufacturer the company acknowledges working with is Ford.
Solid Power’s relationship with BMW dates to 2016 and initially, says Van Scoter, the relationship was focussed on cell R&D. But in December 2022 the relationship was expanded to facilitate technology sharing and even closer collaboration. “Currently the Solid Power and BMW teams are engaging in development and manufacturing activities at Solid Power’s Colorado facilities,” he states. “The work has been aimed at improving manufacturing techniques and at incorporating and utilising new quality control and inspection equipment.”
Furthermore, the agreement will also allow BMW to install its own solid-state prototype cell manufacturing line. That projected facility will be a duplicate of Solid Power’s pilot line and will allow BMW to begin parallel development in Germany, though the timescale for that is entirely a matter for the car maker.
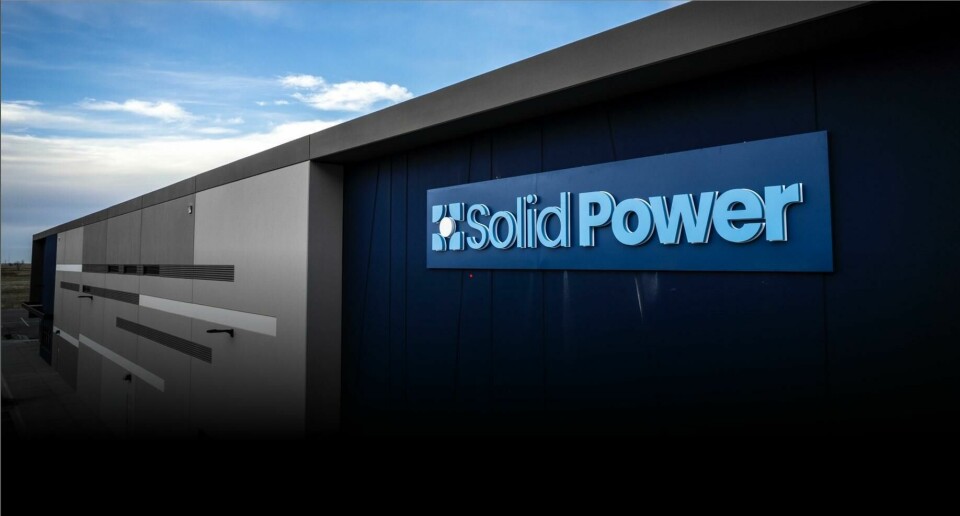
This expanded relationship is already producing positive results. “On our second quarter earnings call, we announced that our 20 Ah cell builds have yielded performance at a level where we shifted our focus to our larger EV cells,” Van Scoter says. “We plan to deliver those cells in 2023 for BMW to use in their demo car.”
Van Scoter says that manufacturability has been fundamental to Solid Power’s strategy since its inception. “Our business model focuses on being an electrolyte materials supplier and licensing our cell designs to third party manufacturers instead of manufacturing the cells ourselves,” he states. “This allows us to be ‘capital light’, which means keeping our capital outlays low while expanding our addressable market by partnering, rather than competing with, existing cell manufacturers. Cell manufacturability is key to that strategy.”
Working in partnership not competition
From Solid Power’s perspective this approach has two major benefits. Firstly, is avoids incurring the massive capital outlays that can be involved in battery manufacture. Secondly existing cell manufacturers should be able to use Solid Power’s designs and electrolyte on their existing lithium-ion battery manufacturing infrastructure, which lowers commercialisation risks.
“Our business model is unique amongst next generation battery companies in that we seek to partner, rather than compete, with incumbent battery manufacturers,” Van Scoter states. “Ultimately, our goal is to be a leading producer and distributor of sulphide-based solid electrolyte material for powering EVs and other applications.”