BMW Landshut is now using new multi-plate die casting technology
The light metal foundry at the BMW components plant in Landshut is using multi-plate die casting technology, which offers function-optimised component design and design of the required sprue positions and flow paths
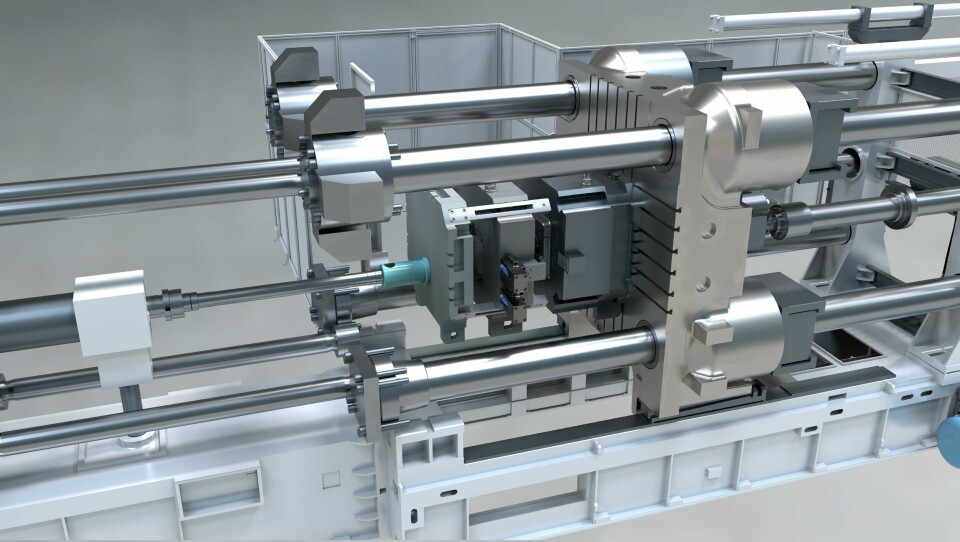
“With the development of new gating and demoulding systems using direct gating in multi-plate mould technology, component designs that are function-optimised instead of flow path-optimized can be realized in the die-casting process. In addition, the weight of the component can be reduced by up to 20% while still fulfilling the function,” explains Klaus Sammer, Head of Toolmaking, Maintenance and Advanced Development at the light metal foundry.
BMW notes that the CO2 emissions in the production and use phase of the body components are sustainably optimised. “The process improvement enables product designs with optimal use of materials and a weight-neutral switch to alloys with lower CO2 emissions. This, in turn, contributes to achieving our sustainability goals,” says Sammer. In future, the Landshut foundry specialists will also be able to use existing systems for casting structural components. The OEM says the new process also increases profitability and reduces energy consumption compared to large and more energy-intensive die casting systems.
With the use of the innovative multi-plate technology developed at the BMW Group plant in Landshut, multiple feed channels leading into the mould cavity can be implemented, as can improved, highly effective sprue separation and demoulding. “The variances in the component design that can be realised in the die-casting process enable the use of casting materials that meet the requirements, taking into account a more efficient and sustainable circular economy,” notes Sammer.
Landshut is the only production facility for light metal castings in the BMW Group in Europe. In 2021, the plant produced 3.1m cast components with a total weight of almost 67,000 tons. The scope of production includes engine components such as cylinder heads and crankcases, components for electric drives or large-scale structural components for vehicle bodies.
Five different casting processes are used for series production of the cast components. Depending on the respective component concept, the technological requirements and the production volume, the most suitable casting process is selected.
In 2019, the foundry at Landshut was certified for its sustainable use of aluminium. It meets the standards of the Aluminium Stewardship Initiative (ASI). BMW also notes that since the beginning of last year, the foundry has been purchasing aluminium, which is produced using electricity from solar energy.