New materials drive electric motor development
Original equipment manufacturers need electric motors that are more energy-efficient and power-dense than those currently available. How composites and resin materials could support developments on this area was discussed by industry experts at a recent conference organised by Sumitomo Bakelite Europe (Ghent) NV (Sumitomo Bakelite Ghent).
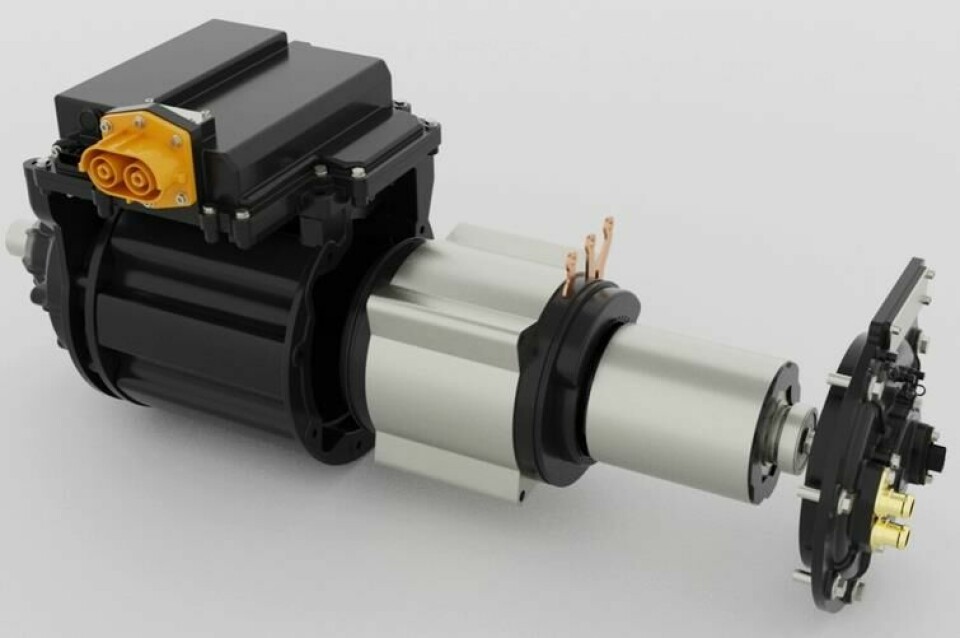
The automotive industry is rapidly changing. The production and sale of electric vehicles (EVs) have grown significantly over the last five years, driven principally by the introduction of more stringent targets for greenhouse-gas emissions by regulators worldwide.
This rapid electrification of automotive powertrains will create numerous opportunities for suppliers of composites and resins based on phenolics and epoxies. Original equipment manufacturers (OEMs) need electric motors (e-motors) that are more energy-efficient and power-dense than current motors, and such materials could be key enablers for them to achieve these aims. These were the key messages delivered at the Composites for Future Mobility Conference held in Ghent, Belgium and organised by thermoset plastics specialist Sumitomo Bakelite Ghent.
The conference attracted over 50 experts from OEMs, suppliers and research institutes working in the automotive industry, including Ford, Volkswagen (VW), Mahle, GKN, Denso Automotive, Robert Bosch, Infineon Technologies, Vitesco Technologies and the Fraunhofer Institute for Chemical Technology (ICT).
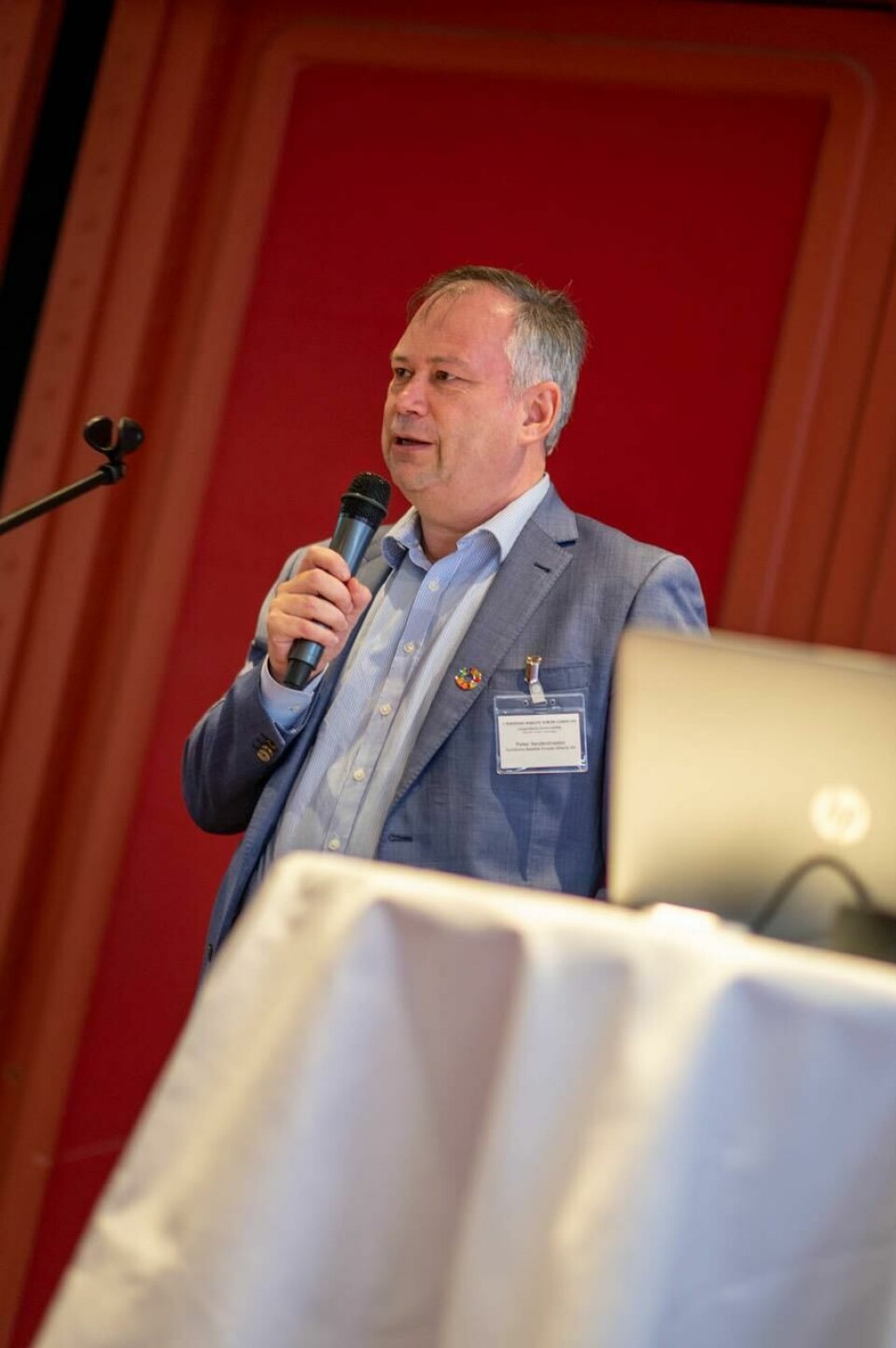
The managing director of Sumitomo Bakelite Ghent, Pieter Vanderstraeten, told the conference delegates: “Five years ago, we were asking ourselves whether plug-in hybrid powertrains or full-electric powertrains would become dominant in future. Today, we must ask ourselves if there is even a future for conventional powertrain technologies. The human coronavirus pandemic and the current geopolitical situation have also created a need for strong local supply chains, rather than global ones.” These trends were reflected in the presentations from OEMs at the conference.
OEM’s develop in-house EV technologies
VW’s team leader for process development and power electronics, Jan Winter, told the conference that the carmakers’ sales of EVs will surpass those of cars with internal combustion engines by 2030. By the same date, VW expects what it describes as “software-enabled revenues”, those related to autonomous driving technologies, to account for one third of its turnover. VW is creating an entirely new platform, the Scalable Systems Platform (SSP), for all the EVs it produces across its numerous brands, including Porsche and Audi. To meet the demands of all these vehicles, from the relatively low powered family cars to the high-end sports cars, VW plans to introduce a modular electric powertrain, and is developing much of the necessary technology in-house.
VW is using composites and resins in the production of its e-motors. For permanent magnet synchronous motors (PMSM), it is using moulding compounds to fix the magnets in the rotor, owing to their advantageous thermal management properties and the stability of the process used for their application. As it manufactures more electrically excited synchronous motors (EESMs), which – as they do not rely on rare-earth metal magnets – are more environmentally friendly, composites will be needed. Furthermore, Winter sees opportunities for composites in the production of lightweight, transfer-moulded encapsulation for power modules.
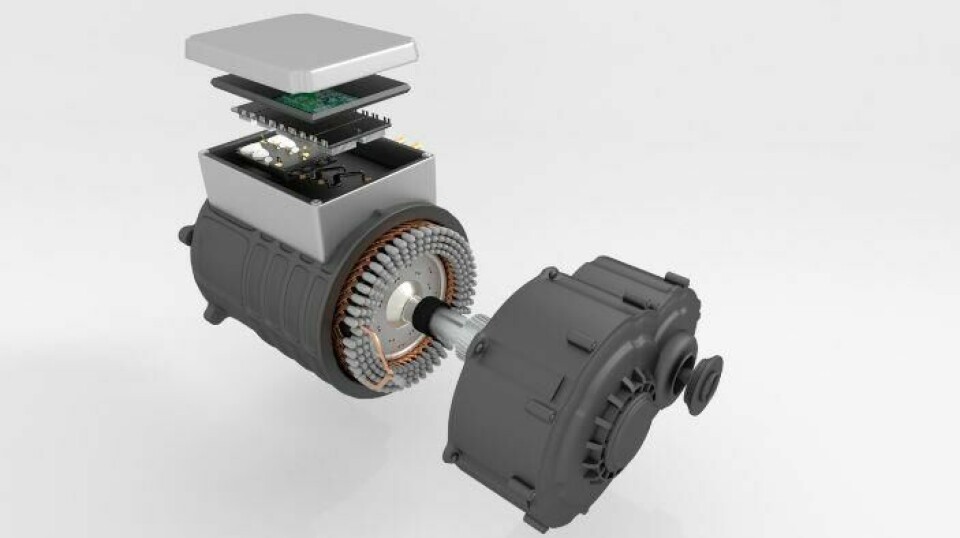
VW is also developing the inverters used to convert power from the battery so that it can be used by the e-motor. Again, this work is being done in-house, said Winter, to ensure security of supply, and to reduce costs and time to market. Here transfer-moulded composites can be used to encapsulate power modules.
Similarly, Ford’s technical leader for E-machines, Franco Leonardi, told delegates that Ford is making huge investments in EVs. F-150 Lightning was MotorTrend’s Truck of the Year for 2023, E-Transit has an 80% share of the US market for EV commercial vans and Mustang Mach-Es is now sold in more than 40 countries worldwide.
Improving insulation and thermal management
To produce the e-motors for its F-150 Lightning EV pick-up truck, Ford uses resin to fix the magnets in the rotor. The magnets are inserted in precisely shaped pockets in the rotor, which is then preheated before a resin is transfer-molded into the pockets to fill any remaining space and then cured. The cycle time for this process is less than 3 minutes. The resin transfers heat and allows the component to operate at higher rotational speeds than would otherwise be possible.
Ford Research and Advanced Engineering is investigating a process that would enable it to replace the paper typically used to insulate the wire coils from the stator with over-molded resin. This over-molding process yields more robust insulation and superior heat rejection.
The potential of resins and composites to produce components for electrified powertrains was illustrated by two demonstrators developed by Sumitomo Bakelite Ghent and shown during the event. The first one was co-developed with Fraunhofer ICT and was a high-energy-density battery module with a strong, durable, housing made from flame-resistant and thermal runaway-delaying phenolic moulding compounds. The developers say this housing maintains its structural integrity in the event of a crash and is 40% lighter in weight than conventional alternatives.
The second demonstrator was a lightweight, compact, and cost-effective e-motor with a phenolic compound housing that demonstrates excellent noise, vibration, and harshness (NVH) behaviour. A moulding compound is used to fix the magnets in place in the rotor, which reduces the number of parts required and the time needed for the fixation process in comparison with adhesive-based or mechanical methods. A hairpin-style stator is insulated using an over-moulding process that allows for the integration of channels through which water glycol can be passed, which is a more efficient cooling medium than the oil currently used.
Sumitomo Bakelite Ghent has joined a €4m research and development project established by Mondragon University, of Gipuzkoa, Spain, to develop cheap, efficient and power-dense permanent-magnet e-motors for mass-produced EVs. The partners on the European Union (EU)-funded project – which is called HEFT, started in December 2022 and will conclude in May 2026 – plan to exploit a variety of technologies to reduce the size of magnets used in e-motors, so that less rare-earth material (neodymium and dysprosium) is needed for their production, and to enable their re-use and/or recycling.
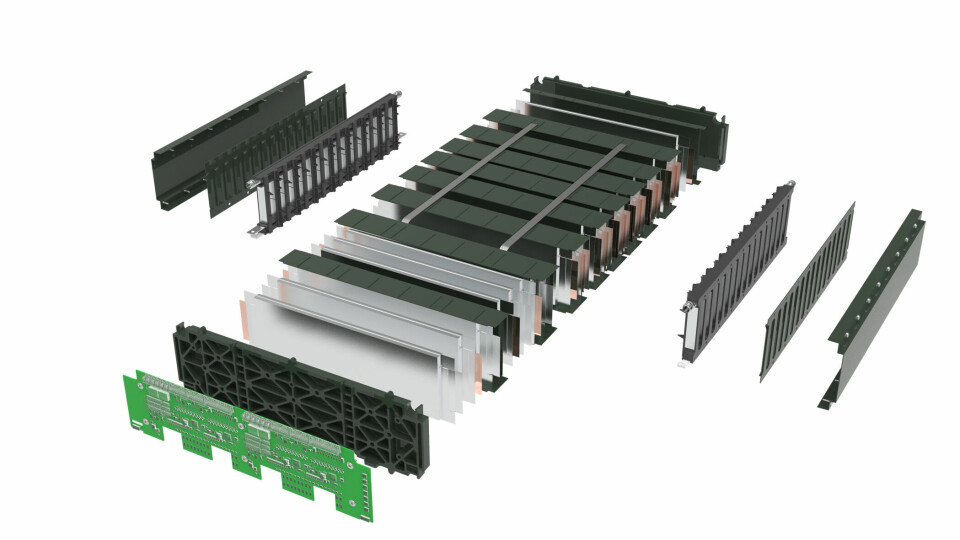
Increasing efficiency and reducing cost
Compared with two reference e-motors currently on the market, the HEFT partners hope to create a motor that will demonstrate up to a 20% reduction in power losses, will be up 28% cheaper to produce, and will consume up to 66% less material.
Another partner on the project is GKN Automotive, which delivered more than two million e-drive systems to its customers in 2022. At the conference, the company’s Head of Electromagnetic e-motor Development, Iago Martinez, outlined some of the technologies that the partners on HEFT will use to realise their aims.
The compact motor will, for instance, feature a multi-stack rotor with over-moulded magnets, which will be stable and robust, and will enable a 14-20% increase in peak torque and power. In the stator, oil, rather than water, will be used to cool the end-windings, which serves to increase torque by 5%, but reduces the weight of the motor by 30% by eliminating the need for a water jacket. The motor will also feature a fibre-reinforced plastic (FRP) housing, which enables a weight reduction of 15-30% compared with aluminium and, according to Martinez, has a smaller carbon footprint. Further, cooling features can be integrated directly into the FRP housing.
In B- and C-segment vehicles, these technologies could reduce the weight of e-motors by 40% and 30%, respectively, compared with incumbent versions, while generating the same levels of continuous torque and power.
Materials may be considered by some to be legacy technology, but they will be key enablers as the world transitions to a zero-emissions economy.