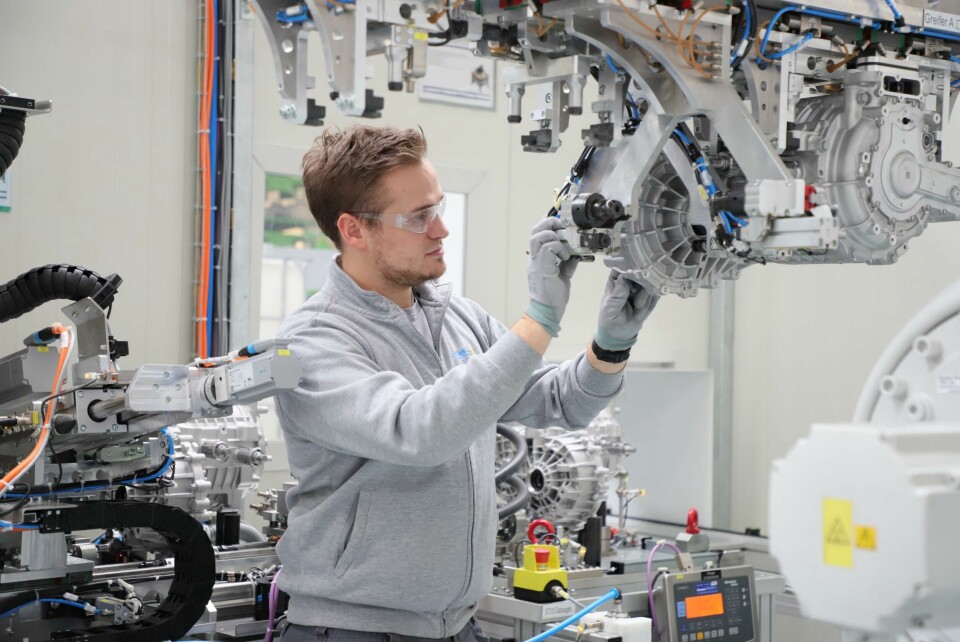
Shifting gears – Electrifying the driveline
GKN Automotive has a long history as a driveline component and system developer, and manufacturer. Like many of the leading tier suppliers in this segment, the company has now added a range of products for electric powertrains to its range. Jorge Beja, VP of Operations Systems shares some insights into production at the company’s centre for excellence for eDrive systems, at Bruneck, Italy.
Could you briefly describe some of the key investments in the production operations at Bruneck over recent years?
We have recently invested in a dedicated machining area with new machining and hardening equipment for the production of gears at Bruneck. This new area supports the business in manufacturing its own gears, which are a core component of our eDrive systems, rather than sourcing externally. Alongside this we have built multiple new assembly cells to meet the demands of our eDrive and all-wheel drive (AWD) customer programmes.
Do EV and non-EV component production operations share any processes?
Our equipment mostly consists of standard machines that can be used for EV and non-EV components. For example, the heat treatment shop floor and soft machining we use for eDrive production can also be used for AWD components. There are limited cases where specialist machining is required, for example in complex gear finishing processes. This enables us to maximise the usage of our equipment and its output.
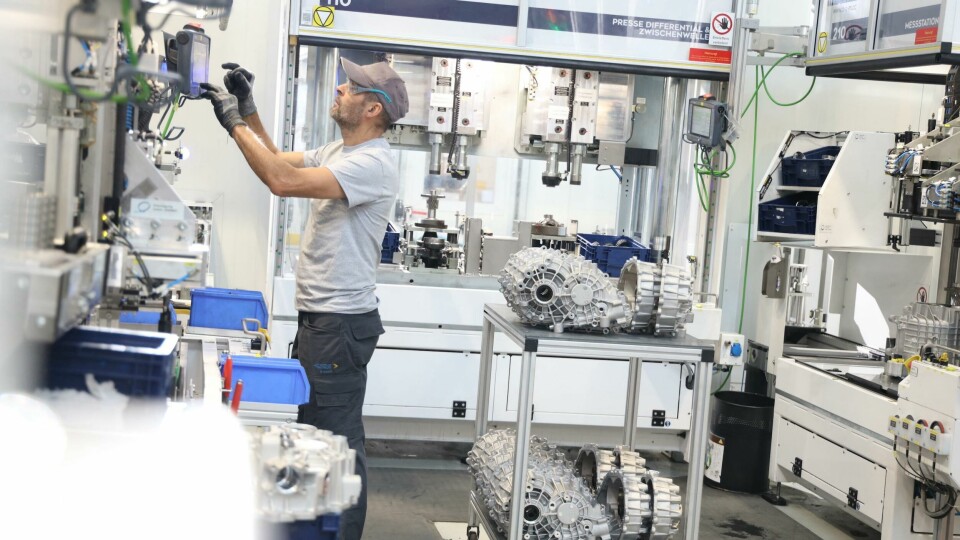
Flexibility in production has become increasingly important. Has this flexibility been built into operations at Bruneck?
We build in flexibility by carefully balancing the use of automation and human involvement. Where we need more flexibility, we take a more manual approach and where we need a more standardised approach, which is typically when we have a large volume demand, we make more use of automation.
The machinery we have is also flexible in its use since we have mostly the same machinery for both eDrive and AWD components. In addition, a batch-oriented machining strategy helps us to be more flexible, using machining cells per operation and not fully connected and highly automated machining lines.
Has the shift to producing eDrive components required higher levels of automation?
No, the level of automation is mainly driven by volume rather than the type of processes required to produce certain products. In fact, the shift to eDrive components has driven a demand for higher technical skills of our people.
How has GKN approached training/upskilling on eDrive production at Bruneck?
We’ve always had highly skilled technicians at Bruneck who have learnt new technologies and processes very quickly. Our local learning and development teams in Bruneck provide opportunities for continuous upskilling and our central teams share important know-how to ensure best practice is delivered across all sites. We also work closely with our machining suppliers and tooling partners to ensure new processes are implemented successfully and are being utilised to their full potential.
How big a role has digital tools played in developing and expanding production operations at Bruneck?
Bruneck has helped set the benchmark for us globally in the digitalisation of its shop floor. All its machines are connected to a central Manufacturing Execution System (MES) which allows us to have a full overview of the production, so we’re always aware which machines are running, what they’re producing, and if there are any issues. The site has also implemented tools to predict the quality of its products, which is particularly helpful when producing gears that are technically challenging to make. These tools have been important in supporting the transformation towards eDrive manufacturing and assembly at Bruneck.
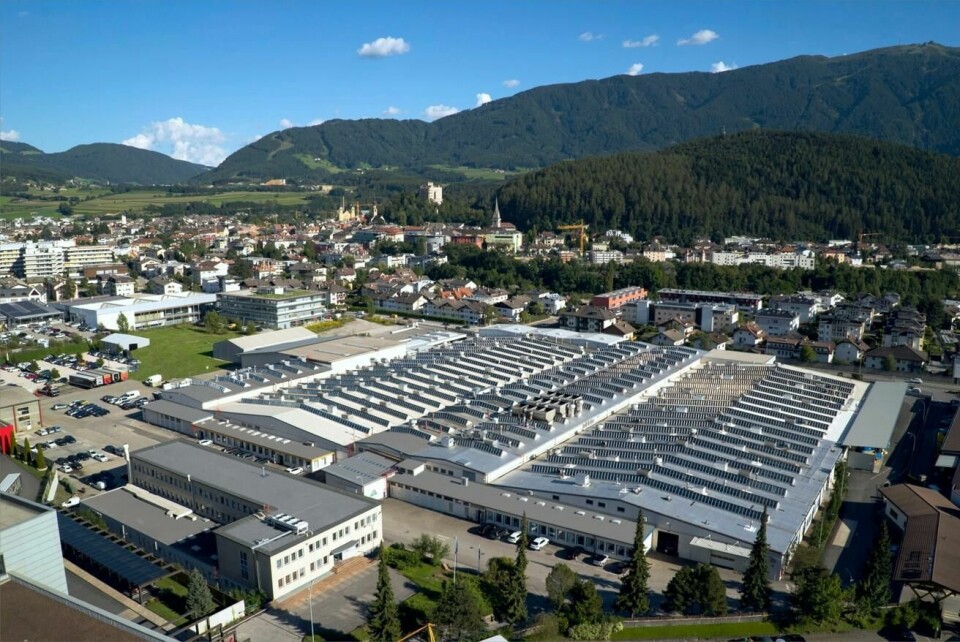
Has GKN had to introduce new competences/technologies to produce eDrive components?
We have introduced many new processes for eDrive components to Bruneck. For example, dedicated heat treatment processes, gear finishing and complex gear assembly processes have been newly implemented and we have a number of skilled technicians on the ground that have been trained on these new processes and machines.
Bruneck is a centre for excellence for eDrive. How does GKN’s production network share manufacturing innovations?
The Bruneck team works closely with our other sites to share tools, process standards, and on-site training and workshops as needed. We have a central manufacturing engineering team who develop process standards and know-how databases, which are shared across all our 47 manufacturing sites. This level of standardisation is crucial to ensure consistency across our sites and ensure that we’re delivering the best quality as efficiently as possible for our customers.