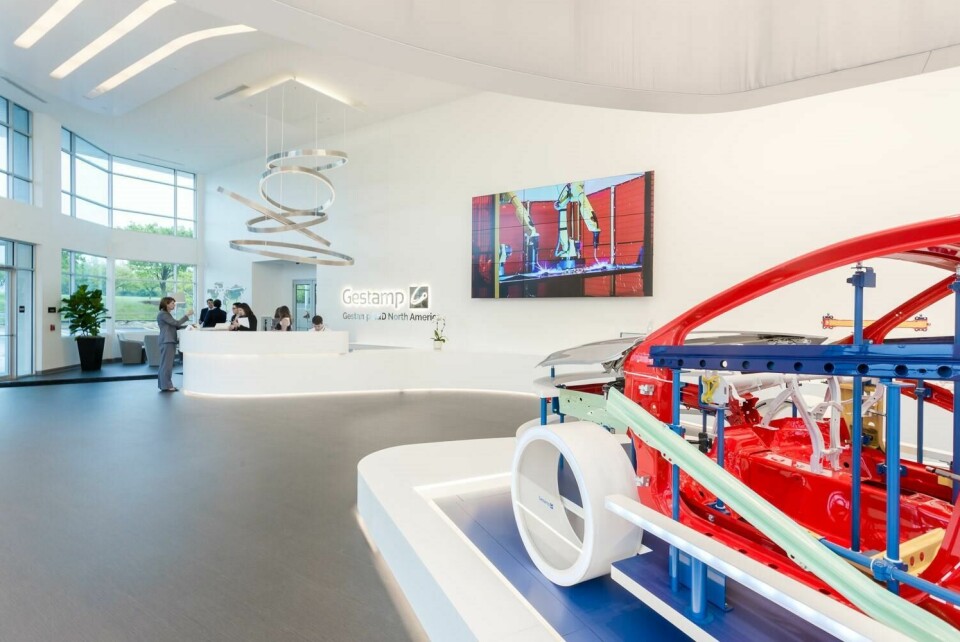
Form and function: Developing production processes and structures for electric vehicle architectures
As much as we read about battery cell development and production, in parallel the new electric vehicle architectures are also continuing to evolve as vehicle makers strive to find the optimum balance between platform flexibility to meet changing market demands for new models, while also being viable for high-volume production. To get some insights in to this ongoing process AMS spoke with Paul Belanger, Gestamp’s R&D Director for North America
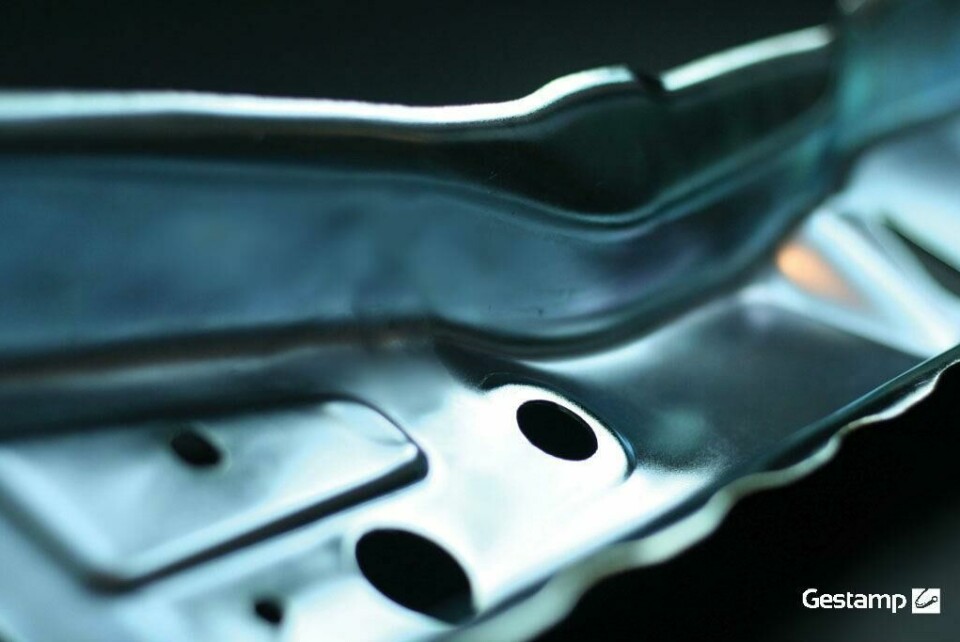
You have a lot of experience in vehicle architecture R&D. What do you find the most interesting and challenging parts of developing structures for electric vehicles (EVs)?
Paul Belanger (PB): I think it’s maybe two things. One is from the technical standpoint. For the longest time, ICE vehicles always had that engine in front. We really understood where the load paths were and how to best distribute the energy during various crash events. Of course, new crash events are always coming online that they have to be designed for, but the body stayed relatively the same as far as how you have to manage it.
But now you take away that engine and add a very heavy battery in the floor of the vehicle, the load paths become very different and how you handle that energy with those same, really challenging crash events. So that’s really interesting and dynamic on the technical side.
Then on the non-technical side you’ve got disruptors like Tesla that are coming in and taking so much time out of the vehicle development timeline, this is really interesting and of course everybody’s trying to follow that. So, speed to market is very different today than it was even just two or three years ago.
Have you seen a big push to compress that development time, and have you had to change your approach to that?
PB: We are definitely seeing it with all almost all our clients. But they’re all trying to adapt to the disruptors in the marketplace and those tighter schedules are requiring us to do a lot of things differently. We are doing more processes simultaneously. For example, where we usually might wait till design is frozen to start doing the die design, we’re doing those processes concurrently, and then adjusting later. So, we’re looking different ways of trying to shorten the timeline without adding risk.
Have digital tools played a big part in this?
PB: Yes, virtual modelling is a key enabler to reducing that time. We’re one of the largest hot stampers in the market and we need to understand what’s happening with the material at 700°C. We must ensure that our modelling cards are extremely accurate so that when we’re doing our formability simulations, that they are accurate when it comes to the first tool trials. So, that helps shortening those try-out stages.
We’re testing and characterising the materials to a much higher degree than we had before. In the past we’d do just tensile tests and get yield tensile elongation, but now we’re looking at multi-axial tensile tests, so we understand the effect of load paths and how the material deforms because that’s a critical factor. You need to understand how that material behaves in the crash so that you correctly model it. It’s important, especially so with some of the newest steels that we have. Even processes like paint baking can change things enough to where you must fully characterise it, test it so that you can model it accurately.
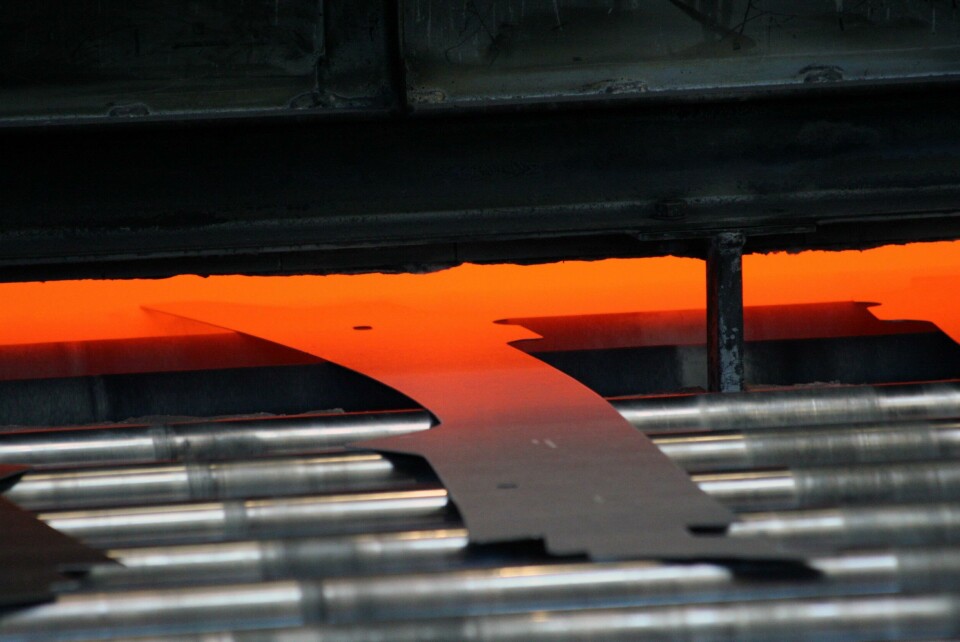
You mentioned earlier that Gestamp has decades of experience with ICE vehicle architectures, but is there a lot of new stuff that you’ve had to figure out for the for the EV platforms?
PB: Yes, absolutely, but our methodology hasn’t changed. At Gestamp we have our whole suite of lab vehicles, and these are fully validated. And we now have a suite of EV [lab] vehicles. Before we even get to the build phase, we have these vehicles that we can play with. We can change the load paths, change where the mass is. A good example is in chassis applications. Today because there’s no engine in the front, the chassis is taking on some of the crash management that the body used to do. And we’re able to use our lab vehicles to understand these requirements earlier in the process before you have a vehicle built and crashed tested.
With EVs are you dealing with a whole new paradigm in crash protection because it’s the passenger cell and the battery enclosure as well?
PB: That’s probably one of the biggest changes when it comes to EVs, especially for a side impact. You must absorb a lot of energy in a very short distance. The OEMs’ first solution was to put some very complex aluminium extrusions inside those stamped steel rocker panels. And that is a great way to absorb energy, but it’s an expensive solution. We have developed a hot stamped solution and a hydroformed solution. It’s almost like an egg carton design that fits right inside the rocker panel. And it absorbs a lot of energy in a very short distance. It’s doing what the aluminium extrusions are doing but at a much better price point.
Are the battery enclosures one of the most challenging, potentially complex parts of an EV structure to develop because of the performance requirements?
PB: At the high level, they’re extremely complicated. Much more so than the industry in the beginning thought that they would be. With the first generations of battery box the OEMs were perhaps uncertain of designing it and how it was going to perform. They used a lot of heavy extrusions, very complex manufacturing with different types of joining technologies that were involved. And we’re still in a very dynamic situation, it’s going to take two or three generations. The automotive industry does a really good job of benchmarking however, you need to have that first generation out there. Then you benchmark, then you have the second generation out there, then you benchmark again. And we’re right in that first-to-second generation phase. So, we still have some more work to do as an industry and right now they’re still very complex.
We think that in the long term they’re going to become simpler structures. The battery box themselves and the requirement for handling a crash is going to go to the body. So, it might make the body a little bit more complex but take out a lot of complexity in the battery boxes themselves, which should take out a lot of cost.
The battery, the cells (chemistries, formats, integration), is another area seeing rapid change. So, will this area of development affect the design of wider vehicle architectures?
PB: It’s very intertwined and it’s very dynamic. The battery chemistries, the energy density, that’s changing and that impacts on the need for space. It will be interesting to see where it goes. As energy density increases, once we hit a certain range, you can probably start downsizing those battery boxes and then they become less structural, less complex and that’s where we think it will go. But that’s still some years away.
Looking ahead, do you think that a multi-material structural package is going to be key to achieving all the goals that the carmakers want or need to meet for EVs?
PB: It’s going to really depend on the vehicle, the segment, the sensitivity to cost and the need for range and weight. It’s not a simple answer. I think the higher price point vehicles that can afford to pay for weight savings, they’ll undoubtedly have more lightweight materials in them, whether that’s aluminium, magnesium, carbon fibre, etc. So, we’re making sure that we’re researching all those material options. But the really cost sensitive segment vehicles would be really challenged to use more expensive lightweight materials. They’re probably going to stay with steel.
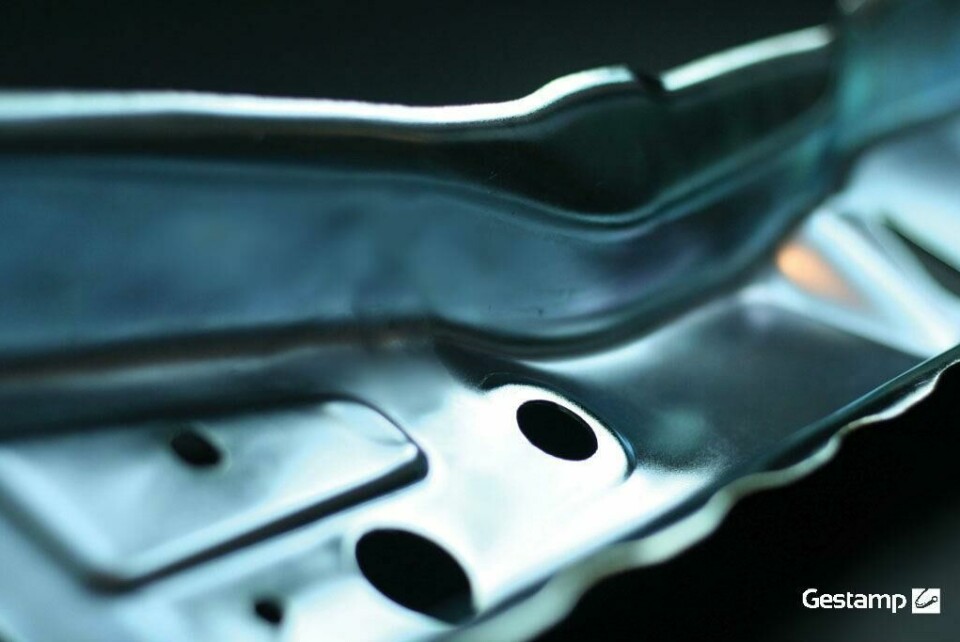
The Inflation Reduction Act in the US is driving a lot of investment in EV development and production. Is Gestamp starting to notice that pick up too, and what implications might it have for your teams, how you work with manufacturing to keep going at that pace and scale?
PB: We have definitely noticed it. The reduction act is really different and it’s definitely fuelling a lot of investment. Obviously, it’s focused a lot on batteries, but there’s a spill-over effect and it is affecting all areas of the automotive industry. We are looking to expand, for land and buildings as are many other companies, so that’s challenging and of course costs are going up. At the same time the OEMs are spending so much Capex transitioning to EVs and autonomous vehicles, so they are very sensitive to costs, and it is challenging to hit those cost points that we need to hit.
Some vehicle makers have been developing and producing large, single piece structures, using a giga-casting (aluminium) process to simplify their platform builds. Gestamp has developed a giga-stamping process. Could you explain this approach?
PB: The goal with giga-castings is part count reduction, and simplification of the bodyshop process, giga-stampings are following suit, but using steel and hot stamping as solutions. With the giga-stampings, we’re able to use our current assets to help contain those costs but come up with these new and innovative designs and processes. So, we can do a part consolidation by incorporating what would have been multiple pieces into a single, very large, hot stamping.
The ones that we’ve been working on so far, overlap patch door rings for example, and maybe in the future a rear section, that’s the one giant hot stamping. These are all in the right sizes that allow us to use our existing assets. We might have to make some modifications to it, but we’re not completely taking it out and putting in new equipment, and that helps to contain the costs.
Multi-step is another process for vehicle structural parts Gestamp has developed. Is this also a pressing operation?
PB: Yes, it’s new way of doing hot stamping. Conventional hot stamping operates at roughly four strokes a minute, and you get two or four parts depending on the size of the parts. With the multi-step we’re able to do it in a servo mechanical press at 10 to 15 strokes a minute. And this is the full operation, including in-press trimming, removing the need for post-forming laser trimming. It’s like a six-stage progressive press but in a transfer press and the parts are fully formed, trimmed and pierced. We can even have restrikes, so we can have negative angles which you can’t get in conventional hot stamping. So, it offers some product design features as well.
Watch: Structural change – Developing vehicle architectures optimised for EV manufacturing