Volvo announces 3,000 job cuts as EV sales drop and projects react
Volvo Cars is reducing its workforce by 3,000, primarily in Sweden, as part of a $1.9 billion cost-cutting plan. The move follows a significant decline in electric vehicle sales and a strategic shift in the company’s electrification goals.
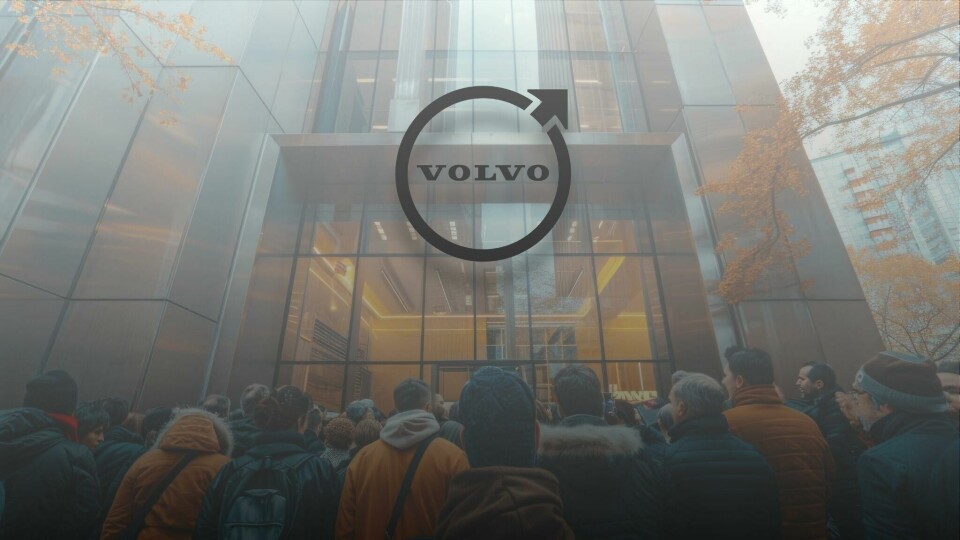
The outlook is not cloudless. Volvo Cars is undertaking a significant ‘restructuring’, after announcing the elimination of approximately 3,000 positions, predominantly affecting office-based roles in Sweden; another carmaker following an emerging trend.
This particular decision is part of an 18 billion Swedish kronor ($1.9 billion; £1.4 billion) cost-cutting initiative aimed at addressing declining electric vehicle (EV) sales and adjusting to uncertain and evolving - and clearly contracting - market conditions.
”In light of these difficulties, Volvo too, has now announced a revision of its electrification strategy”
The layoffs represent about 15% of Volvo’s white-collar workforce, with 1,200 employees and around 1,000 consultants in Sweden being affected. The remaining reductions will now occur across other global markets.
The decision comes in response to a 32% drop in pure EV sales in April compared to the same period last year, contributing to an overall 11% decline in global sales for the month.
In light of these difficulties, Volvo too, has now announced a revision of its electrification strategy. While the carmaker initially aimed to become fully electric by 2030, it now targets 90% to 100% of its global sales to consist of electrified vehicles, including - and this is significant - both fully electric and plug-in hybrid models. The adjustment demonstrates the OEM’s response to market uncertainties, and the need for flexibility in its product offerings.
Building ‘resilience’ through ‘restructuring’?
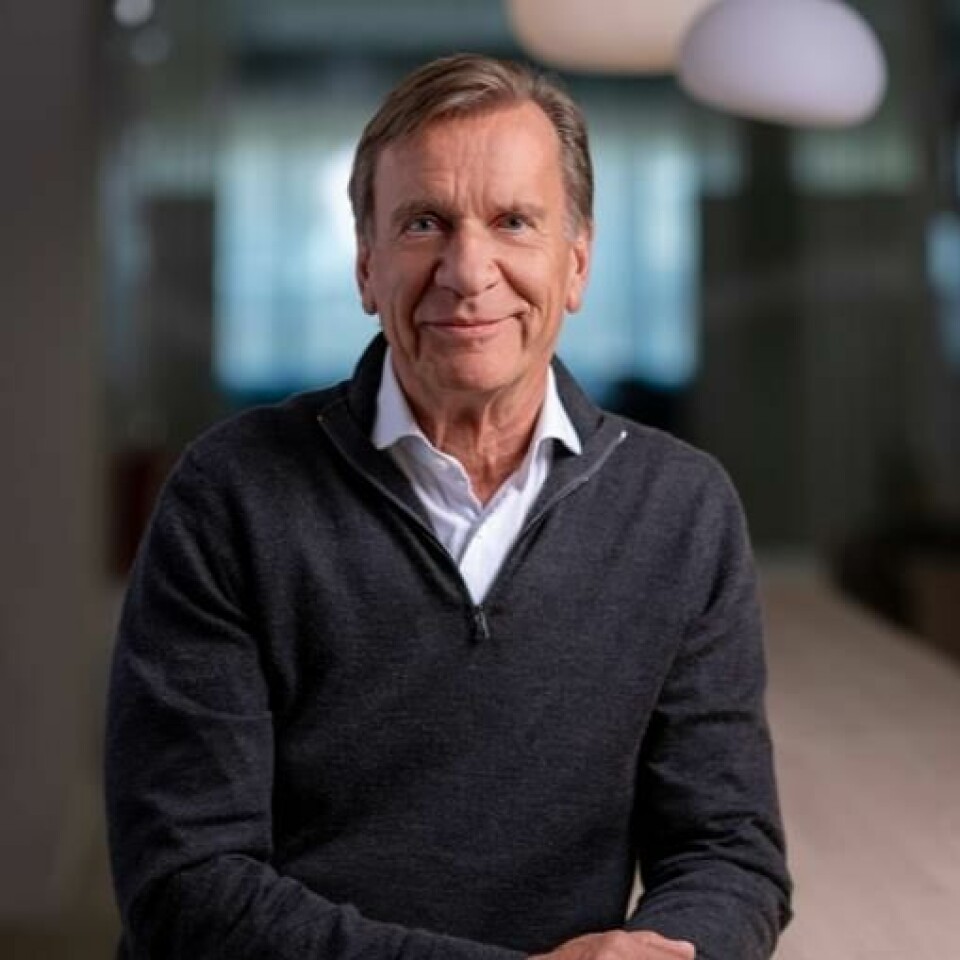
Håkan Samuelsson, who has returned as CEO following Jim Rowan’s departure, emphasised the necessity of these measures:
“The actions announced today have been difficult decisions, but they are important steps as we build a stronger and even more resilient Volvo Cars.”
This major cutback is expected to incur a one-time cost of 1.5 billion Swedish kronor ($156 million; £115 million), with the plan set to be finalised by autumn.
Volvo’s shares experienced a slight uptick following the announcement, though they remain down for the year.
These cutbacks highlight the broader challenges faced by the automotive industry as it tries to navigate the transition to electrification amid fluctuating demand and geopolitical uncertainties.
Analysis: the cuts just keep on coming and a contagion of caution
Volvo’s ‘pivot’, however, is not isolated. In fact, it is comparatively modest. Nissan, reeling from its own missteps, is cutting more than 20,000 jobs globally, closing plants and cancelling a $1.1 billion EV battery facility in Kyushu. The Japanese carmaker has scaled back production capacity by 20%, abandoned targets from its ‘Arc’ strategy, and warned of a net loss as high as $5 billion - the largest in its history. Its retreat from aggressive electrification plans coincides with its withdrawal from unprofitable markets and failed alliance talks, including a collapsed merger with Honda.
Read more about how carmakers are pivoting as electrification bites
- Nissan to axe 20,000 global jobs as EV production losses bite
- European auto suppliers keep slashing jobs amid EV slump
- VW’s plant closures illustrate industry’s existential crisis
- The urgency for enhanced Design For Manufacture (DFM) in vehicle production
“Decades of structural problems”
Volkswagen CEO Oliver Blume
Honda, for its part, has reduced internal combustion engine (ICE) production in China and shut down assembly lines after its China sales dropped below one million units for the first time in a decade. The carmaker is banking on the Honda S7, a new EV, to claw back relevance in a market now dominated by BYD, and not Toyota or Volkswagen.
If Japanese OEMs are trimming and regrouping, German giants are entering an open crisis. Volkswagen is planning to cut 35,000 jobs, relocate Golf production to Mexico, and close its iconic Transparent Factory in Dresden. The OEM’s recent 64% drop in profits has prompted CEO Oliver Blume to acknowledge “decades of structural problems”, including high labour costs and slow software development. In the words of one analyst, “Volkswagen is the archetypal legacy automaker: flabby, slow-moving and valued as if it was going out of business.”
What began as a green industrial revolution is becoming an employment reckoning. In 2024 alone, major European suppliers including Bosch, ZF, Continental and Schaeffler announced 54,000 job cuts. According to CLEPA, Europe’s supplier association, 65% of suppliers are now operating below the critical 5% profitability threshold needed to fund innovation and investment.
From electric optimism to overreaching oversupply
Just two years ago, the mood was very different. Policymakers funnelled billions into EV infrastructure and gigafactories. Manufacturers followed suit, investing heavily in battery plants, software, and new EV models. But forecasts were overconfident. While global EV sales reached record levels in 2024, growth has slowed markedly in Europe and North America. The demand needed to justify capital outlays has not materialised - at least not fast enough.
At the root of the issue is a mismatch between industrial timelines and consumer appetite. Chinese manufacturers, led by BYD and SAIC, have stormed the market with cheaper, simpler EVs - many powered by LFP battery chemistry and built in high-volume plants with localised supply chains. Western OEMs, by contrast, have bet heavily on high-spec, high-cost electric platforms that remain expensive to produce and difficult to scale.
“We have been spending more money than we earn. That doesn’t go well in the long term”
Arno Antlitz, CFO and COO, Volkswagen
The result: price wars. Tesla cut EV prices aggressively throughout 2024, followed by Ford, Volkswagen, and Hyundai. Yet even with discounting, profit margins on many EVs remain wafer-thin or negative.
Ford has admitted to losing as much as $50,000 per electric vehicle on some models. Volkswagen’s EV software division, Cariad, has been widely criticised as underperforming, prompting a $5 billion partnership with Rivian in an attempt to catch up.
A problem of structure, not just sentiment
These crises are not simply the result of softening demand or policy reversals. They are structural. Europe’s automotive manufacturing base is saddled with high energy costs, complex labour agreements, and fragmented production. As Volkswagen CFO Arno Antlitz put it bluntly: “We have been spending more money than we earn. That doesn’t go well in the long term.”
Even where EV investment continues, it is increasingly cautious. Volkswagen has pushed back the timeline for its €25,000 ‘affordable EV’, once seen as a potential Tesla rival for the mass market.
And it doesn’t stop there. Stellantis and Renault have scaled back battery investment, Ford has prioritised hybrids, Nissan has slowed its electrification targets in China and delayed next-generation EV launches, and Volvo’s walk-back from its 2030 target now looks less like a deviation and more like the emerging norm.
Governments, too, are growing wary. In Germany, EV purchase subsidies were pulled earlier than expected, leading to a sharp decline in sales. In the UK, Nissan has publicly warned that the country is “not a competitive place to build cars”, despite its £2 billion Sunderland investments. The EU’s proposed tariffs on Chinese EVs may slow imports but are unlikely to reverse underlying cost disadvantages.
An inflection point, not a collapse - we hope
But despite the seemingly dreary trend, none of this in principle, spells the end of electrification. On the contrary, plug-in hybrids and battery-electric vehicles will account for an estimated 27% of global production in 2025, according to CLEPA - up from 20% in 2024.
But one thing’s for certain; the transition will be slower, messier, and more selective than previously assumed.
For legacy OEMs, the challenge now is not, whether to electrify, but how to do so profitably and competitively. That means fewer megaprojects and more modular platforms. Fewer grand pronouncements, more realism. As Volvo’s Samuelsson put it, “resilience” is now the watchword.
What is unfolding is a recalibration. For those already overcommitted, the EV transition is becoming a costly exercise in backtracking. For others, it is a second chance to build leaner, smarter, and more responsive manufacturing models.
In this context, Volvo’s job cuts are neither surprising nor singular. They are the latest entry in an industry ledger that is shifting from bold bets to strategic retreats - or to be magnanimous - restructurings.