Flexible Production
Honda’s Ohio Anna engine plant turns 40 with EV ambitions
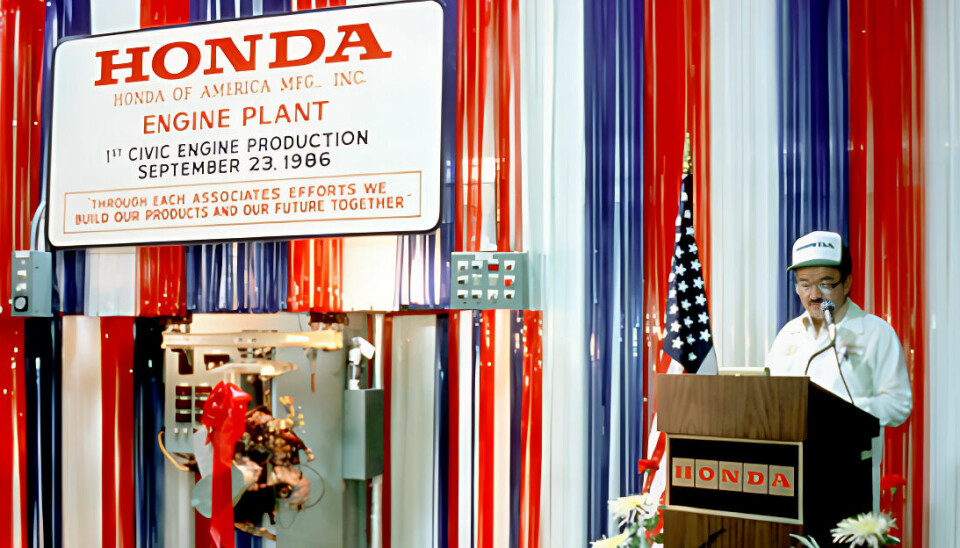
Honda celebrates 40 years at its Ohio engine plant as it scales flexible manufacturing, invests in megacasting and prepares for EV battery case production from 2026.
Honda’s Anna Engine Plant (AEP) in Ohio, the largest auto engine facility in the company’s global network, is celebrating its 40th anniversary this July. Since its first motorcycle engine rolled off the line on 22 July 1985, the plant has transformed from a 200,000-square-foot operation employing fewer than 100 associates into a 2.8m-square-foot manufacturing hub with a 2,900-strong workforce.
In four decades, AEP has built more than 32.5m engines for automobiles and powersports products, as well as powertrain components including cylinder sleeves, camshafts and crankshafts. It has earned a reputation as one of the most comprehensive powertrain plants in the industry, incorporating ferrous casting, high-pressure die-casting, machining, heat treatment and assembly within a single facility.
“Everything that Honda has accomplished at the Anna Engine Plant during the past 40 years has been achieved through the skills and commitment of our associates and this will continue as we pursue an expanded form of flexible manufacturing in the future”
Michael Tinch, plant lead at AEP
AEP's cumulative $2.9 billion (£2.24bn) investment reflects Honda’s long-term strategy to maintain advanced production capabilities in the US. Today, the plant is at the centre of the company’s shift to flexible manufacturing, producing internal combustion engines (ICE), hybrid systems and components for electric vehicles on shared lines using domestic and globally sourced parts.
“Everything that Honda has accomplished at the Anna Engine Plant during the past 40 years has been achieved through the skills and commitment of our associates and this will continue as we pursue an expanded form of flexible manufacturing in the future,” said Michael Tinch, lead, at Anna Engine Plant. “As we maximise production of ICE and hybrid models, even while preparing for the future of EV production, I know our associates will continue to produce high quality products that meet the needs of our customers.”
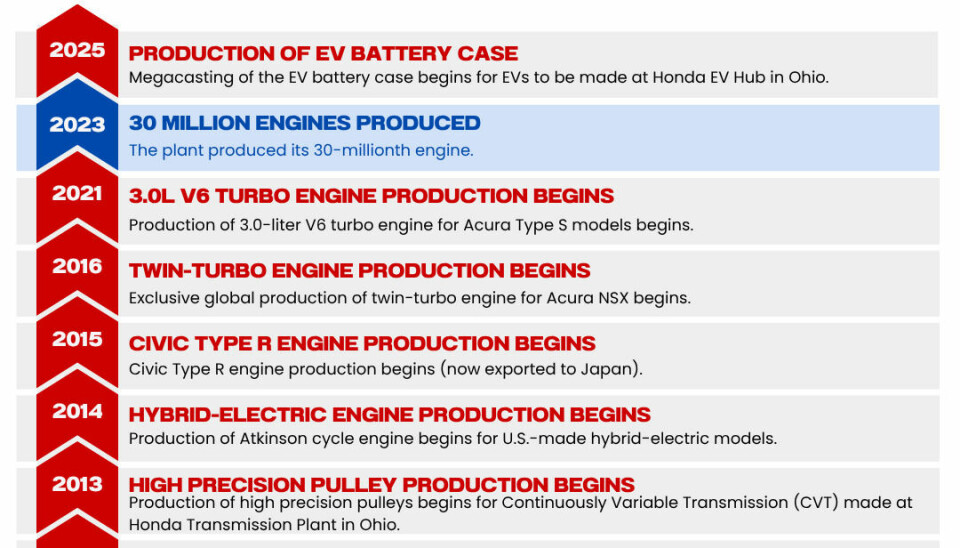
Flexible manufacturing at scale for ICE and hybrid engines
AEP began as a motorcycle engine plant before moving into automotive production in 1986 with a four-cylinder engine for the Honda Civic. It now produces a range of V6 and inline four-cylinder engines, including 1.5-, 2.0- and 3.0-litre turbocharged units. Its line-up includes highly fuel-efficient hybrid engines and performance powertrains for Acura and Honda models.
EV battery case production and advanced processes
Honda’s electrification strategy is bringing a new chapter for AEP. The plant has introduced three new processes to manufacture aluminium battery cases for EVs: megacasting, friction stir welding and minimum quantity lubrication machining. These techniques represent Honda’s first use of such processes globally.
When EV production begins in 2026, battery cases megacast at AEP will be sent to the Marysville Auto Plant to be integrated with modules into complete EV battery packs. These packs will power Honda and Acura electric vehicles built at Marysville and East Liberty. By developing these capabilities within its existing powertrain network, Honda is signalling that ICE and EV manufacturing will co-exist for the foreseeable future, leveraging shared expertise and scale.
Honda’s manufacturing footprint in Ohio
Honda’s Ohio operations date back to 1979, when motorcycle production began in Marysville. Automobile production followed in 1982.
Today, Honda employs more than 12,000 associates across five Ohio facilities with an annual capacity of 460,000 vehicles, 1.18m engines and over 1m transmissions and hybrid systems.
Over the past six years, Honda has invested $1.4 billion (£1.08bn) to modernise these facilities. Now, as part of its EV Hub strategy, Honda is committing more than $1 billion (£772m) to retool Ohio plants for EV production, alongside a $3.5 billion (£2.7bn) joint venture with LG Energy Solution to establish an EV battery plant in Fayette County.
The balancing act between ICE and EV
The Anna Engine Plant illustrates the tightrope manufacturers must walk during the industry’s transition to electrification. ICE engines remain profitable and in demand, even as EV volumes rise. By introducing megacasting and battery case production without shutting down its core ICE and hybrid lines, Honda is maintaining flexibility while hedging against market uncertainty.
For now, the plant’s next challenge is clear: mastering dual production systems while preserving the quality and efficiency that defined its first 40 years.
It is a challenge shared across the industry, as manufacturers weigh legacy processes against the demands of electrification. Those shaping this transition will converge in Detroit...