Making the digital a reality: how AI and virtual reality are adapting automotive manufacturing to a changing world
Automotive manufacturers are facing the challenge of constantly changing vehicles, technologies and parts. However, stakeholders can increasingly plan and implement systems faster using real-time manufacturing data, digital twin simulation and training through augmented and virtual reality (AR/VR).
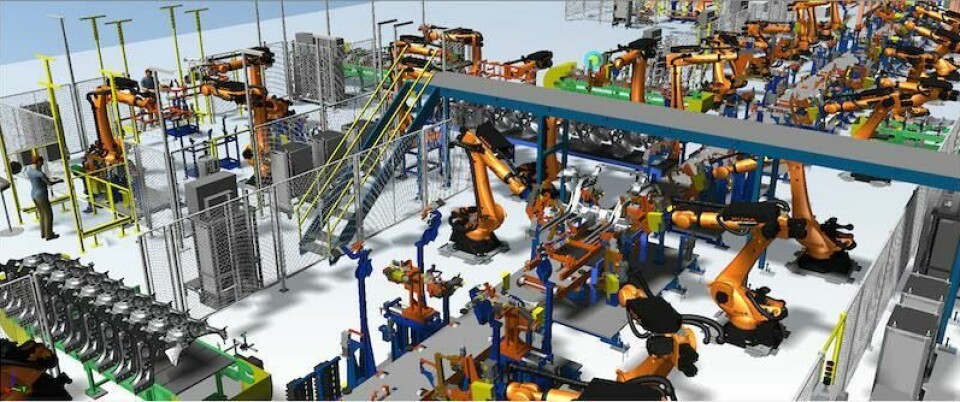
Virtual reality and AI allow companies to design, develop and improve their factories through simulation
Three top industry insiders spoke to the AMS Evolution Summit to discuss how manufacturers and systems suppliers use virtual planning tools to prepare for ongoing global changes, train employees and implement AI solutions in manufacturing.
Digital twins work as real-time models serving as the digital counterpart of a physical object or, in this case, the production process. In a world where visibility and quality testing are paramount, manufacturers are seeing these tools as increasingly necessary.
Digital possibilities
Arik Lämmle, IPA project leader at Fraunhofer IPA outlined how each tool that helps collect data, from artificial intelligence systems to machine learning, all aid in building a robust digital model.
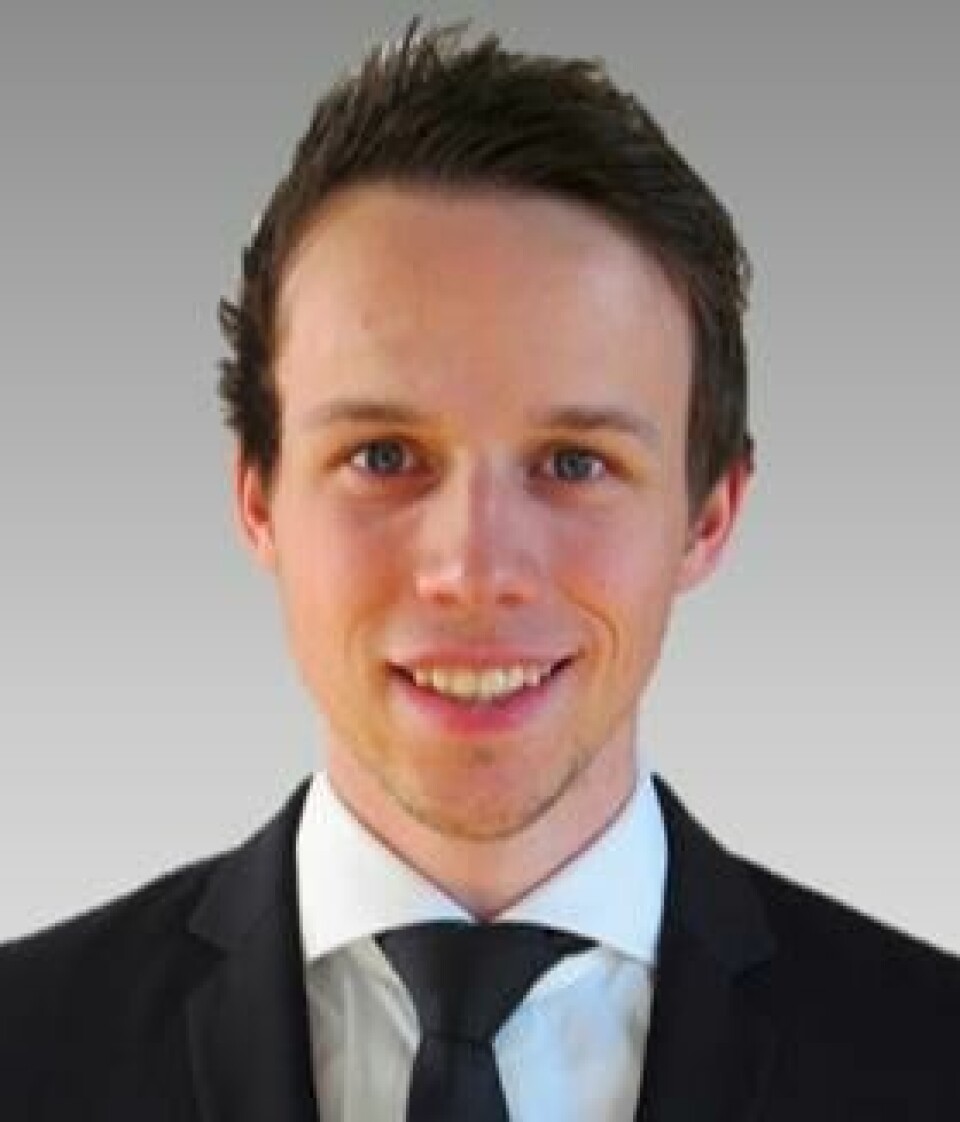
“Artificial Intelligence, simulation and robotics are the same things but different sides of the coin,” Lämmle said.
Digital twins and simulations represent the future of automotive manufacturing and applying these tools, not just at the factory level but across supply chains, is the next logical step to take.
Lämmle added the caveat that while working with simple components in manufacturing may not initially sound complicated, applications on the shop floor are a means of constantly dealing with uncertainties. Robots are confronted with uncertainties and tolerances, and the machine can then learn to deal with any problems identified through “trial and error”, according to Lämmle.
Dr Balakrishnan AS, vice president for MP&L Plant Group and material flow and packaging engineer at Ford Motor, added that the adoption of data in making decisions “has grown significantly in recent years.”
He explained that visualisations and digital twins help simulate processes and, therefore, help shorten time to market.
As digital twins become increasingly essential to manufacturing, customers are changing their perspective on what they want when purchasing a manufacturing tool for developing a digital system.
Raman Mehta, chief information officer and senior vice president at Johnson Electric, said that customer requirements are changing, and therefore “the discipline in engineering and design” has been forced to shift. As executive decisions gear towards a data focus, manufacturing providers are interested in selling a product and selling a service surrounding a product.
Systems providers are now having to “ensure that our engineers can not only simulate a product with its characteristics but how it’s going to be operated and manufactured in the factory environments.”
“It is becoming necessary to be able to simulate how products will act in real-life situations where conditions are not ideal, and environments are often unpredictable,” Raman said.
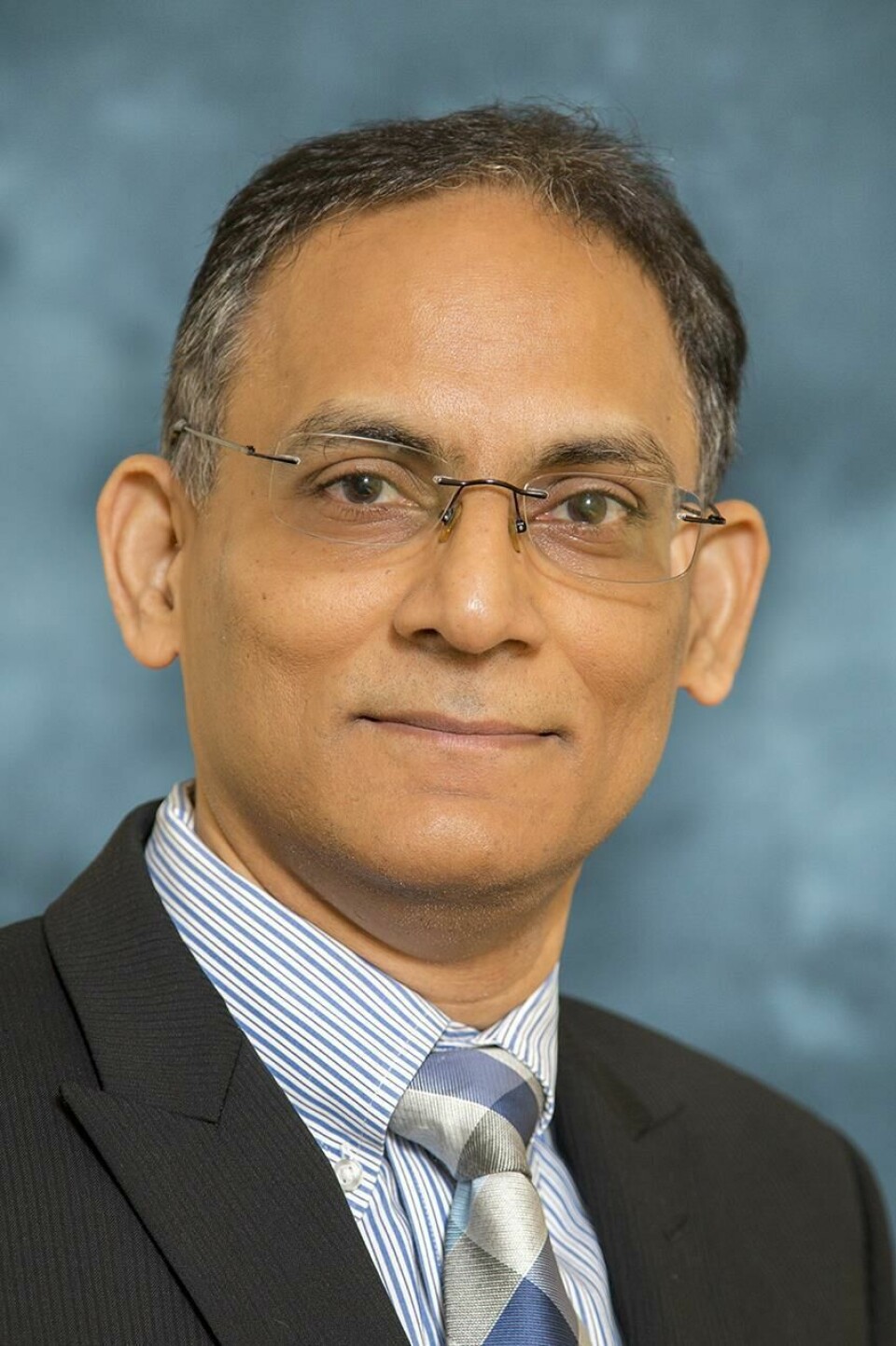
For a digital twin to work, data on production must be fed back to the engineering lifecycle to ensure accurate visualisation of the process is available across the manufacturing stages.
Bridging the gap
The effectiveness of a digital tool also depends on how well it can transfer quality data from the simulation into reality.
Lämmle said that the digital twin could be used to help robots generate knowledge in real-world applications. While decisions need to be based on data from digital twins and simulation tools, data also must be used efficiently to solve identifiable problems.
“Robots can train inside the safe simulation environment to deal with uncertainties,” he said.
The digital twin is a virtual representation of input information; size and shape of the factory, how many units are produced at what time and in what environment.
Romain Ropitault, senior product manager at Cosmo Tech, gave his insight into how the technology has changed. He explained that speed is critical to react to the new world with rapidly emerging new technologies. Agility and flexibility are now the key components demanded by companies.
“The digital twin is not new technology,” he said. “What is new is the scale; we model an entire company and model a single system and environment and supply chain, as opposed to a single product.”
This reality has defined the conversation over digital twins and AI tools. The question has increasingly become utilising simulations at a practical scale rather than just the newest technology. However, new technologies play a role in how fast data can be acquired.
“In real life, the digital twin is a virtual representation, and it comes alive by the census data,” said Raman Mehta.
“You do not want new technologies to disrupt cycle time. So how do you create an architecture that can move quickly that can accumulate all data in real-time from temperature to testing?”
Mehta highlighted that a way of solving this contradiction is to stream data on a cloud network.
“How do you create an architecture which can move quickly and collect all this PLC data, that is, getting all these product and machine characteristics in real-time?”
He said that collecting all the data, detaching it from the real flow, and streaming it on the cloud means developing simulations from accurate data. Collecting this data is what makes your digital twin more “potent”, according to Mehta.
Quality vs quantity
The overall drive towards digital systems is all-encompassing and increasingly essential to maintaining quick production and reaching the market in time. However, no one model is built the same, and the standard of data used is just as important as having the initial system.
“Data quality is definitely one of the very key aspects, you could have the most efficient algorithm and PCs, but if ground data is not representing the underlying processes accurately… your data will not be transferable to the real-world system,” Lämmle explained.
Therefore, the challenge for manufacturers has become how to ensure that tools are acquiring valuable and essential data.
“We are trying new technology to create synth data using generative adversarial networks that can respect the physics behind the model and still give you enough quality data you can’t get from real life,” Raman Mehta said.
Conversely, Balakrishnan highlighted that the global nature of automotive manufacturing might not be sufficient to accentuate individual problems as they can result from obstacles that span the entire value chain. This is often the result of complications that emerge with insufficient or poor-quality data.
“You can fix the problem at one specific station, but the variables may be different elsewhere,” he said.
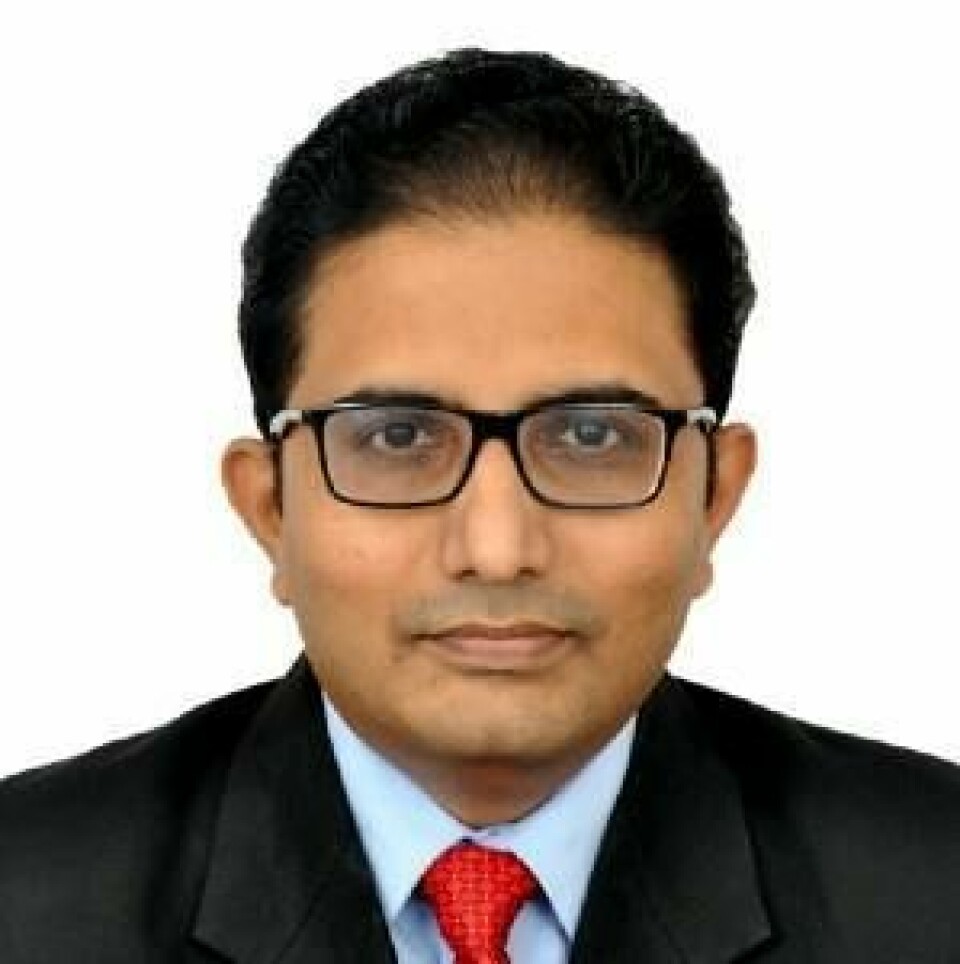
Perfect as the enemy of the good
Romain Ropitault, senior product manager at Cosmo Tech, cautioned against perfectionist attitudes in creating digital systems and said that focusing on isolated issues within the manufacturing process can often be more effective in extrapolating accurate data.
“Do not try to start with fully complete digital twins as it does not exist,” he said.
Ropitault stressed that simply accumulating data on individual parts of a supply chain and problems within it, such as bottlenecks between factories, can give sufficient “representative insight” and can be assimilated into a digital twin simulation.
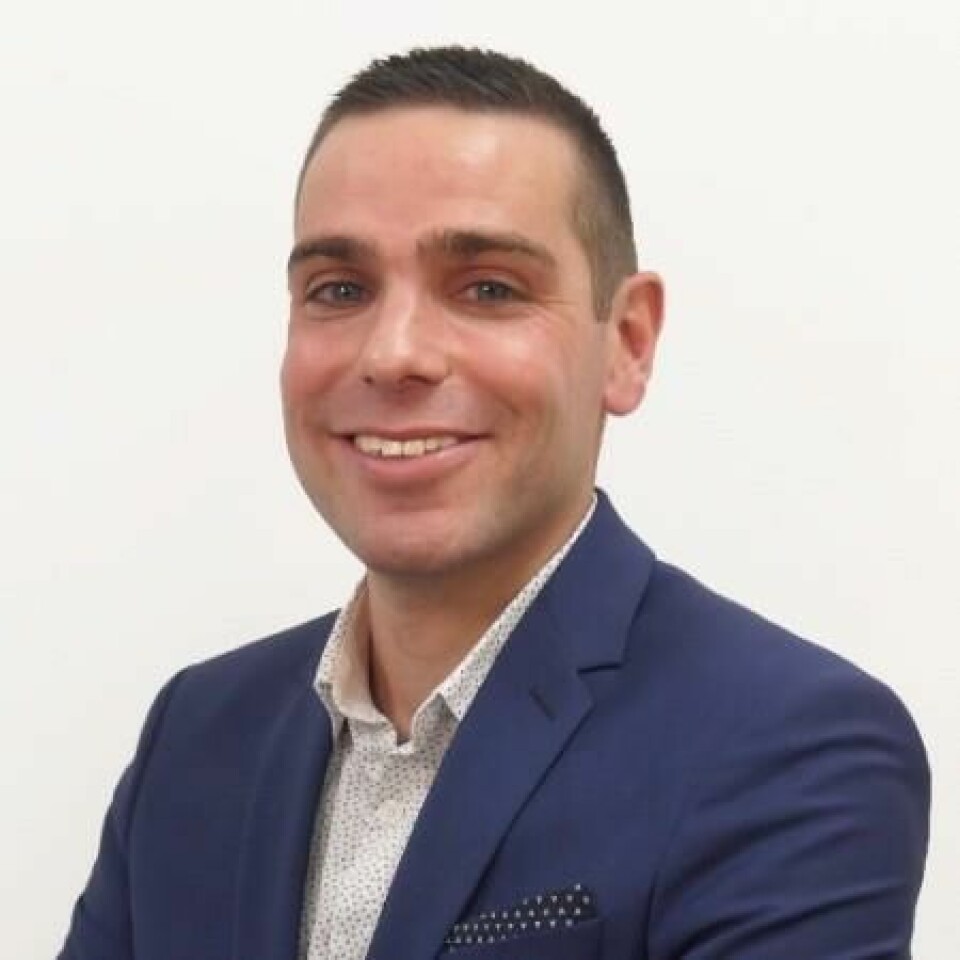
Data quality is a prerequisite for effective management in manufacturing, Ropitault added. However, he warned that overly ambitious targets can lead to a “data project with no end.”
Lämmle echoed this sentiment, saying that a digital twin does not have to be a perfect simulation, but “feedback must be high quality that can be used later.”
The visibility challenge
The ongoing challenges facing manufacturing mean making use of these new technologies for data collection, Balakrishnan said. He continued, adding that tracking assets is another task that is essential to improving visibility within end-to-end processes.
Citing “volatility in demand”, Balakrishnan stressed that the task of providers is to ensure that whatever service a customer is investing in should be what they receive.
“Making tiers more transparent, that’s a challenge. This is where trust and transparency become important and new technology is an enabler,” he said.
Lämmle added that it is vital that manufacturers and providers do not try to “reinvent the wheel over and over again” and focus on ensuring that transferring knowledge is possible from one assembly process to another platform.
Democratising digitisation
Raman Mehta explained that smaller, more defined applications are helpful in global networks to improve the visibility of the whole end-to-end manufacturing process. From data analysts to staff working on the shop floor, the ability for a digital network to be valuable and accessible to everyone involved ensures transparency.
“My CEO in Hong Kong should be able to see something taking place on a line in the last 5 minutes,” he said. “It is absolutely important that as IT and business, we should work together to clean up and harmonise data points.”
Information should be made available to people without any friction, Mehta said, such as through using phones and discovering information rather than hunting for it.
Romain Ropitault added that predictions can be made by accumulating a combination of uncertainties. Simulations can create data that can be used to compile a robust design of the manufacturing situation.
“We rapidly built a web application on top of the digital twin to give the key for an end-user to interact with the digital twin to run an experiment that could be very complex,” Ropitault said.
Therefore, end-users can use the accumulative data of minor performance analysis from independent information collected by digital twins and ascertain the final impact of a decision, he explained.
One road ahead
Balakrishnan concluded that despite all the ultimate goals of digitisation still must be ambitious if manufacturers and providers traverse the rocky future plagued with uncertainties such as economic instability, labour shortages and supply chain disruption.
Romain stressed that despite diverging approaches to the utility of digital twins, all developments are still heading in the direction of digitisation.
Whether it be minimising the environmental impact of entire supply chains or improving transparency, it remains important that these key figures are involved in the digital twin.
“All objectives are driving manufacturing in the same way, towards optimising digital twins. The capability to put different factors together simulate and optimise,” he said.
Romaine added that a free connected system to reality is the ultimate conclusion of introducing simulations that can rapidly adapt using feedback loops, stretching from the digital twin to operations within the context of an ever-changing world.
Click here to watch the full interview at the AMS Evolution summit